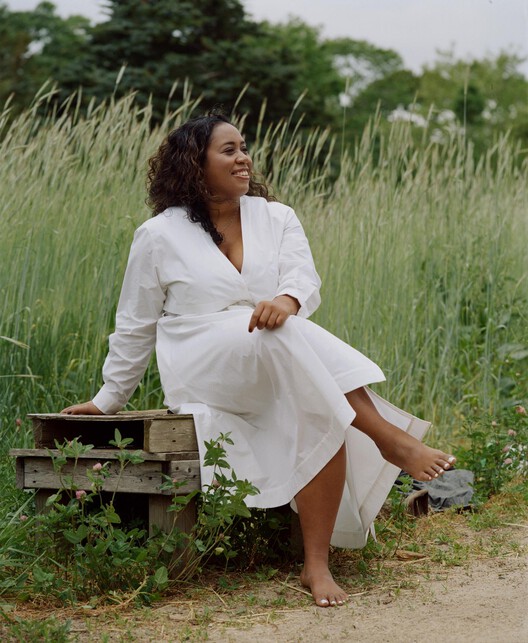
Agriculture and the food industry seem to have little in common with architecture, but it is precisely the overlap of these three areas that interests Ghanaian-Filipino scientist and architect Mae-ling Lokko, founder of Willow Technologies based in Accra, Ghana. Working with recycling agricultural waste and biopolymer materials, Lokko searches for ways to transform the so-called agrowaste into building materials.
Among her most comprehensive works, the research with the coconut industry in Ghana stands out. In it, Lokko investigates how the by-product of this production chain — the coconut husk —, associated with certain fungi and mycelia, serves as a substrate for the production of low-density panels that can supply alternatives for thermal insulation and acoustic to the architecture and construction industry.
Because of its transdisciplinary and innovative nature, Lokko's work has gained worldwide notoriety. In 2019, the architect was among the finalists for the Hublot Design Prize. Her research had already been nominated for the Visible Award in 2019 and the Royal Academy Dorfman Award in 2020. ArchDaily had the opportunity to talk to Lokko about recycling, waste, food, and how these areas relate to the architecture industry.
Romullo Baratto (ArchDaily): Could you start by sharing your personal experience in Ghana and the coconut farms, the waste they produce?
Mae-ling Lokko: Recently there was a coconut boom in Ghana. Advertised as both a healthy drink and base for cosmetic products, coconut is now a wave and in every neighborhood here you can find piles of it. In this context, I started to think about how the sellers could be empowered and get money from this market and the huge amount of waste it produces.
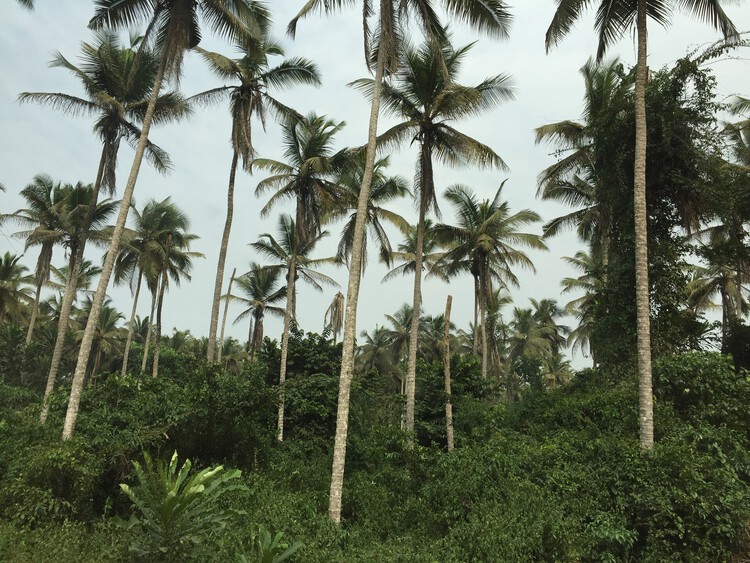
It all started with the coconut husk and traders, and as I got deeper in this investigation I became friends with a coconut seller that shared details of their operations. I went to visit his family and his farm in the Eastern region of the country — it was a small-scale production but with a strong network of people that took the coconut back to the city twice or three times per week. That was my first encounter with a coconut farm. But it’s not where most of the production is concentrated. It is in the Western region, closer to the Atlantic coast, where they grow coconut in large plantations. So there are two systems, one producing for exportation and the other one selling coconut water to the cities on a smaller scale.
But my first focus was on the small farmers and the waste — that is, the husk — produced by this industry, which is not centralized, it is everywhere in the country, making it interesting for the small biomaterial industry that can take advantage of this distributed availability to create more sustainable building materials.
RB: But could the reuse of the husk be implemented on a large scale as well?
ML: Oh yes. It is even easier to collect the husk and control its quality since it hasn’t been tainted, hasn’t been thrown on the road, or been exposed to the rain. You have more control when you work with large scale cooperatives of coconut farmers, and also a much more streamline collection of the waste.
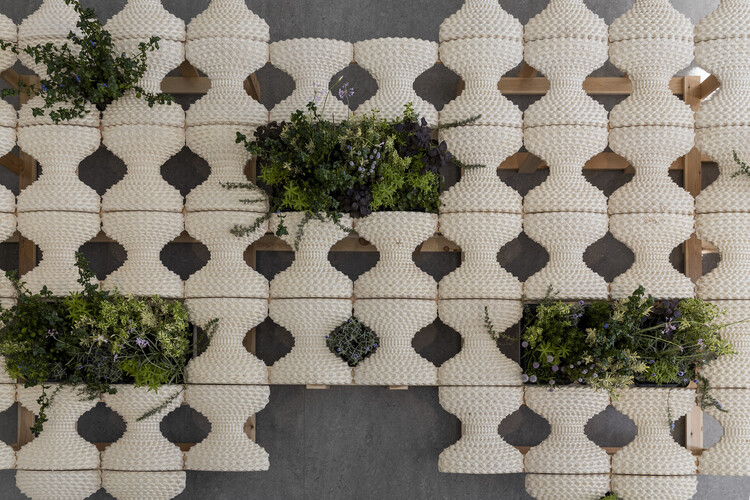
RB: The first thing that comes to my mind when I think about this process is how amazing it is to reuse the coconut husks. But questions arise, like what are the byproducts of this new industry or, what are the wastes left behind after the reuse of agrowaste? Does it pay off in terms of energetic consumption? Or is it still only a bet?
ML: From an energy standpoint, we know that fiberboards or particle boards made of bioadhesives and agrowaste — coconut husk, mycelium etc. — actually melt and basically disintegrate at lower temperatures and pressures than what you would see if you were pressing plywood or medium density fiberboard. But the embodied energy is much lower because of the glues we are using.
What is interesting about the coconut husk is that when you break it you get the fibers and this dust substance called pith widely used for hydroponics as a substitute for the soil. At half of the temperature and slightly lower pressure when compared to plywood, that melts into a very strong glue. In fact, bioglue can produce high-density fiberboards as close to oak. So embodied energy-wise, there’s a lot going for it in terms of the pressing process.

On the other hand, things can get difficult in terms of the life cycle, emissions from collecting the waste, and distribution. Having some control on where the waste is produced can cut down the energy costs in transportation. Besides that, if the waste is left out and gets wet, you need to spend energy dehydrating the husk. You can do that in open air, but with less control. That’s why the price tag is so shaded with the quality control of the waste. That’s where energy-wise and cost-wise it has always been quite expensive. It is a challenge.
In terms of byproducts, there aren’t many. In the coconut boards we are using the dust and the fibers, that’s all you need for the board. You get almost a binderless building material. When you start looking at other bioadhesives employed to protect it against rain or even fire, then you can have some sort of byproducts — but nothing to prevent you from using them.
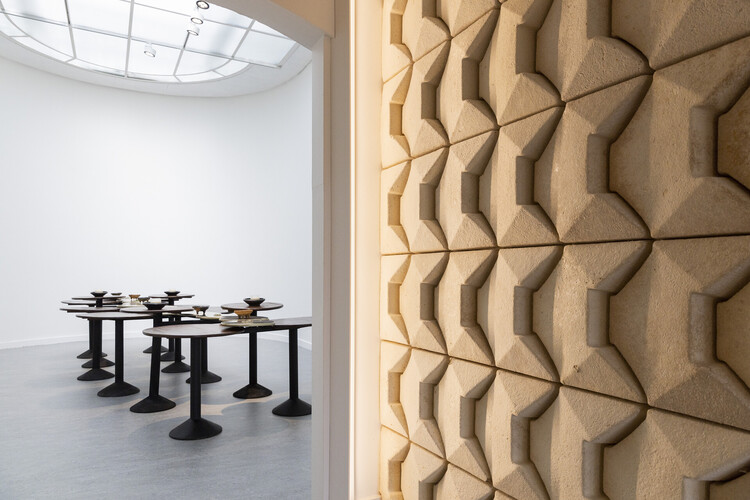
But to answer that question even further, I’ve been working with water treatment using agrowaste and one of the plants we use is called Moringa, very popular for tea and supplements, similar to Spirulina. One of its byproducts is a sort of flour that is very good at treating toxic water, especially textile waste water. It makes all the bad stuff come together and sink. The resulting sludge is another byproduct with many heavy metals and other stuff you don’t want, and we are exploring making bricks out of it.
We have to rethink what we are using since the beginning. If you are going to accumulate all of these toxic metals into one chemical, they will show up somewhere down the line. Agrowaste is a wonderful material substrate for capturating and bonding it, but this is not the problem: the problem is way back, when we started using heavy chemicals.
RB: It is really good to see these byproducts being reused and becoming new materials, and all these recycling and upcycling trends all over the world. But if we think of the whole production chain and its impact, we realize we should start thinking about these issues in the design stage, and it’s wider than architecture, it goes to the whole society...
ML: Because of the nature of my research, placed between agriculture, food and architecture, when I think of designing a material, I start much earlier. When I worked with coconut I realized that the life of the fruit when it’s growing on a tree, in a very specific climate, that is the start, that is where all the conditioning for the material’s properties begin.
My work over the next few years will focus on what it means to design a building material not with the goal on the building phase alone. What if the goal is to figure out how the building returns to the soil?
We are in such a huge crisis now where most of what we produce is completely incompatible with the chemical and biological systems present in the land, and that’s why things take too long to degrade, to go back to the soil. These conditions are not separate from the building performance. Architecture lifecycle should encompass both what our buildings do to materials and how the environment deals with the materials after. But that is a huge challenge, we have to understand much better what happens, what our soil is made of, what’s in our materials. That is a paradigm change, so I don’t expect it to happen anytime soon.
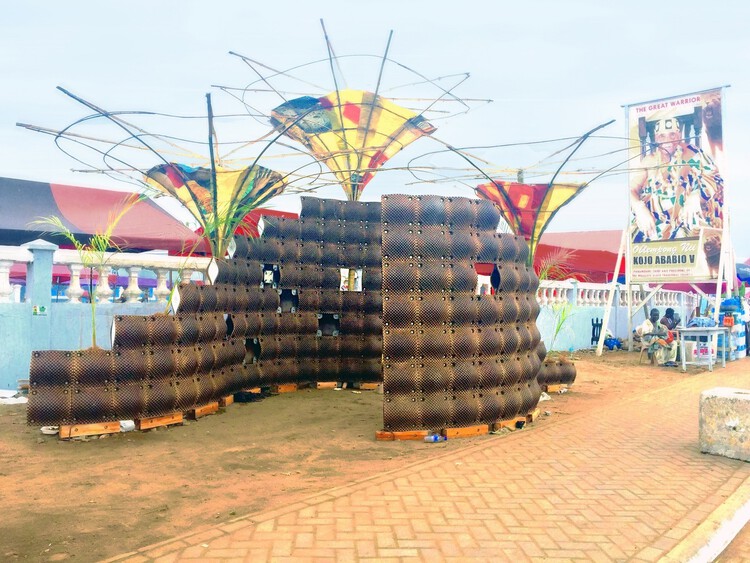
RB: What kind of products we can deliver right now, with the current technologies, that can supply to the architectural and building industries?
ML: Lower density insulation stuff is already a reality. In fact, I came late to the wave of biowaste insulation products. In buildings, acoustic paneling made of agrowaste is probably the one of the most promising areas because people pay for acoustics things they can see, and there’s a high degree of customization in the materials. In terms of cost, you spend relatively less per area of material if compared to the products we usually find in the market. On the other hand, none pays that much for insulation trapped behind the wall, so you really have to stay low and bring down your cost of production — something that can be achieved with large scale collaborations with agriculture producers.
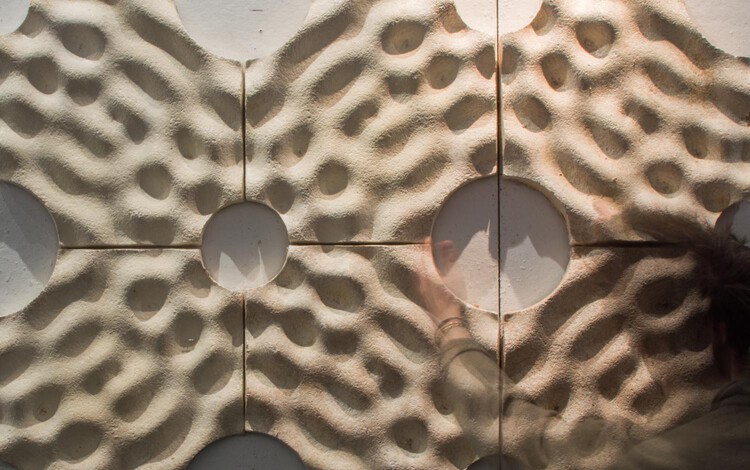
The medium-density fiberboards are catching-on and there are a number of companies that are doing these biocomposite panels that are pressed. Obviously, it becomes a more energy intensive process when you apply heat and pressure. The competition is also difficult. If you compete with other medium-density fiberboards and plywood brands and manufacturers, your price range is tough. Also, your customization options are typically not as broad in terms of colors, textures, and waterproofing. Your product will tend to be more expensive, seen more as a luxury bespoke application.
The higher-density materials are really difficult because you have to get very high quality, strong fibers and resilient glues. It also depends on the quality of the byproducts because they are all different — and that’s the beauty of agrowaste: just as food, it changes from place to place depending on the characteristics of the soil and air, making it unique and deeply rooted in that specific geography.
RB: It has a lot to do with the food industry, as the same fruit — the coconut — grown in Brazil and Ghana, for instance, have very different chemical characteristics.
ML: Yes, and it also has a lot to do with seasonality as well. Differently from monoculture, where you have corn or soy dominating the landscape all over the year, when working with small-scale agrowaste you know that in the raining season you will have a ton of this or that, which will lead to unique building products delivered seasonally.
Besides that, for your building materials production chain to withstand climate at critical periods of time, you cannot rely hugely on one crop otherwise it would annihilate several other species. And as disease comes, the whole industry falls apart, which has happened to the coconut industry in the past. There are so many lessons from monoculture that inspire a different model for food, consumption, and agrowaste production.
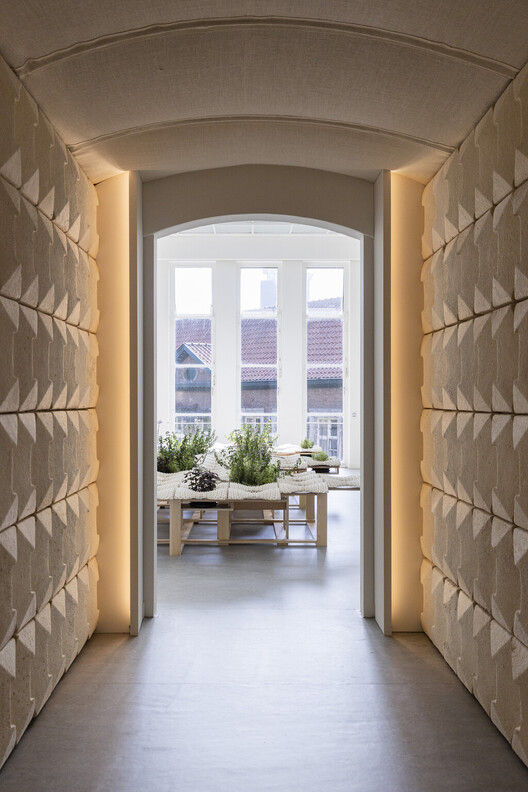
RB: This is truly holistic thinking. It’s not just food or the building industry, it is pretty much life on the planet.
Do you have any experience or have heard about the differences between the agrowaste from transgenic and non-transgenic food? Perhaps the byproducts from organic food have more nutrients — just as the food itself — and therefore have more value for the building industry?
ML: This is a good question. I don’t know specifically about corn and soy, but we have a lot of genetically modified coconuts dominating the industry in Ghana, and I would expect a more standardized composition in the hybrid species rather than the organic ones, with relatively less differences in the levels of sugar and lignin. And although this is more predictable in terms of production, usually you don’t have the structural performance you want, or maybe not the right type of sugar to feed the mycelium. To be fair, I never saw any research on that but I would expect the same in the corn or soy industries. When you are out in the wild, with more severe climate conditions and more nutritious soil, you get a stronger plant, so it is not hard to imagine you are not getting much structural value from transgenic food grown in poor soil.
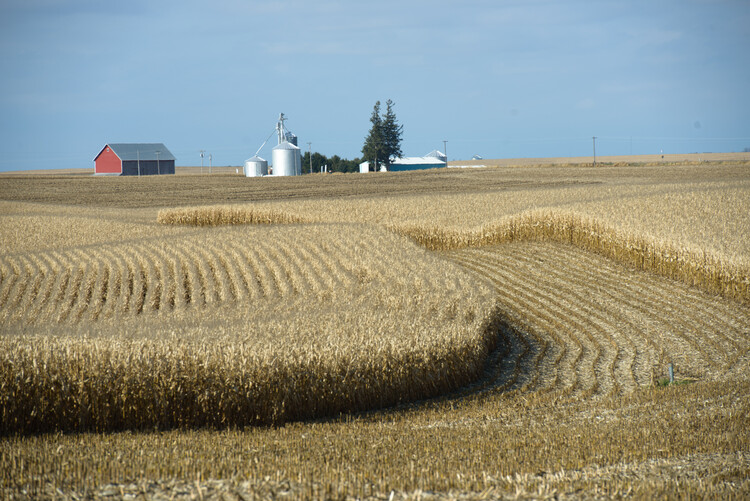
RB: Yes, it is surely not hard to assume that. To conclude this conversation, can you talk about the main challenges these products face nowadays to ultimately get into the market?
ML: One of the most common questions I receive is how do these materials deal with fire. The lower-density insulation products made of mycelium have excellent fire performance — when they burn they create a layer that protects the core against the flames. It also doesn’t release toxic fumes as many other synthetic products. Water performance, on the other hand, can be improved with several coating products also applied to wood.
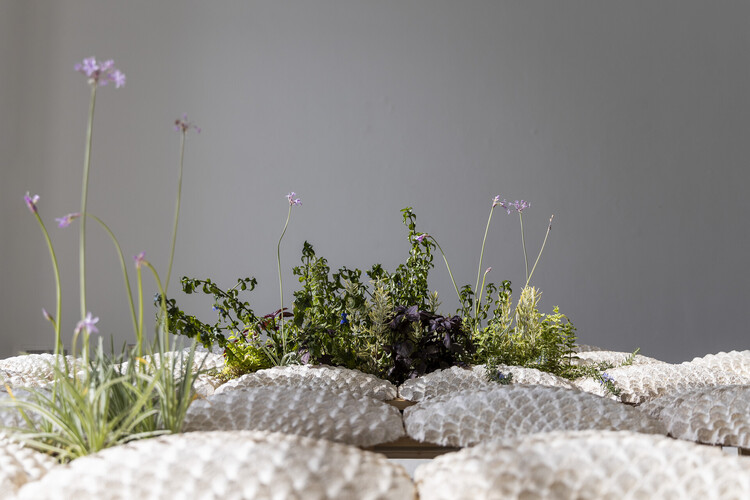
I think the biggest issue is how architects and designers integrate them in the building. We have lived so long in sealed environments with inert materials — glass, steel, concrete — but these mycelium products are breathing, and if you do not allow them to get in contact with the air they cannot deal with all of the moisture or heat they may absorb. I am not romanticizing vernacular architecture but there is so much intelligence in terms of understanding how your roof and your façades get hot, how the moisture changes from one side to another of the building, and how all of this moisture and heat can be released from the architecture.
For me the biggest issue is how we design with these materials, and the architecture lifecycle planning. It’s still expensive to produce them compared to conventional ones, so thinking about a distributed material production, as well as the afterlife of these materials, is crucial. There’s a lot more room there and I am excited to work and collaborate with people on that — it’s an exciting problem to deal with nowadays.
This article is part of the ArchDaily Topics: New Practices. Every month we explore a topic in-depth through articles, interviews, news, and projects. Learn more about our ArchDaily topics. As always, at ArchDaily we welcome the contributions of our readers; if you want to submit an article or project, contact us.