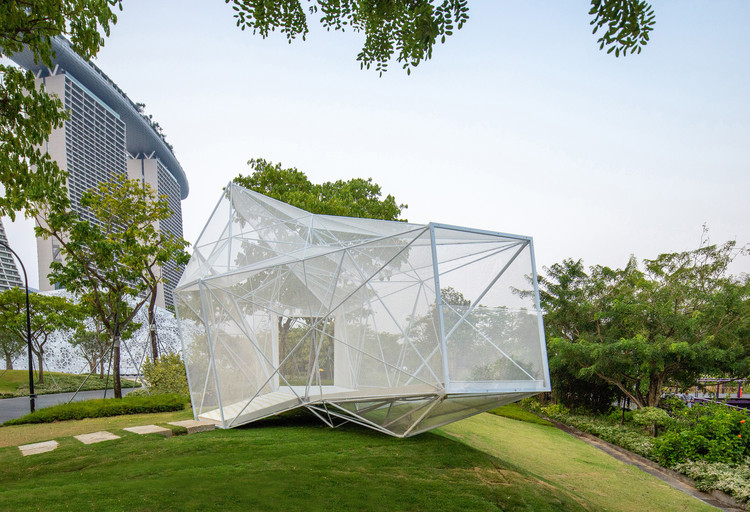
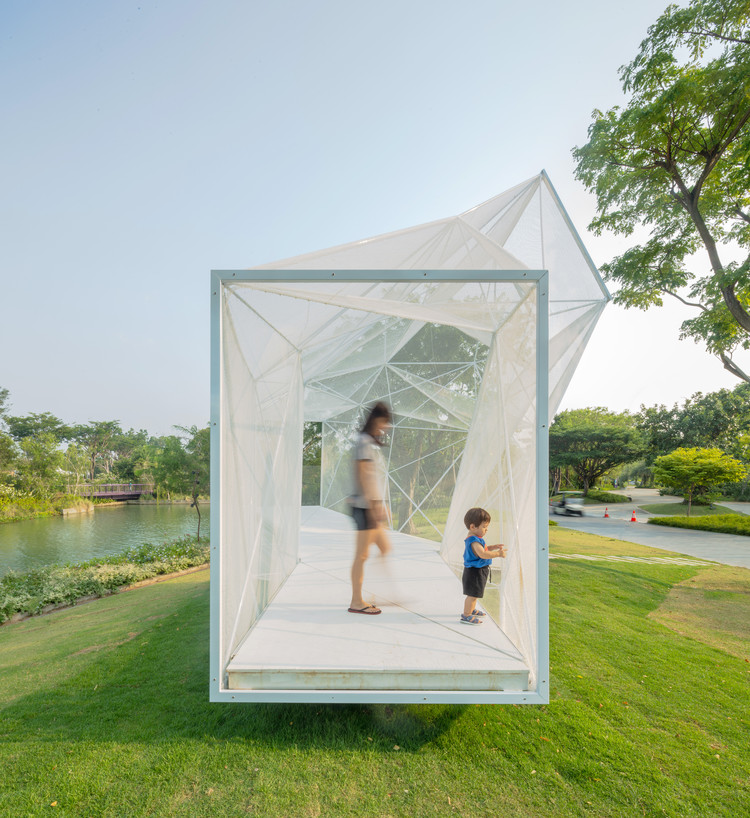
Text description provided by the architects. AirMesh is the world first architectural structure made of 3D printed components in stainless steel, demonstrating innovative digital design and manufacturing technologies developed by AirLab at Singapore University of Technology and Design in Singapore. The ultra-lightweight pavilion, located at Gardens by the Bay, is both a gathering space and a light sculpture.
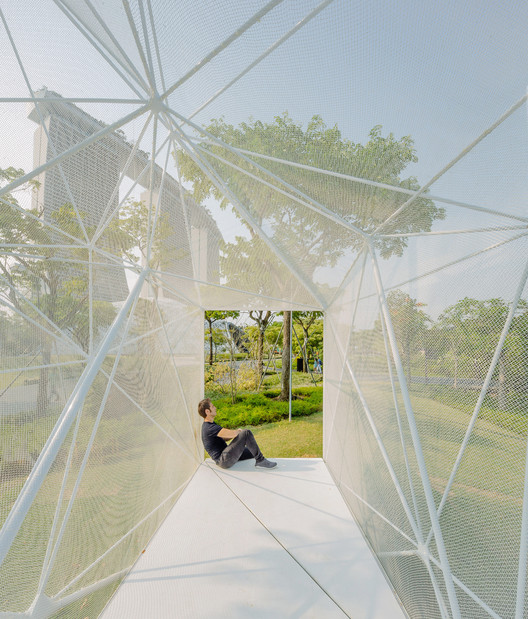
The state-of-the-art design follows Eurocode regulations, and is the first 3D Printed structure that has been approved by the Singapore Building Construction Authority (BCA) for temporary occupation in Singapore. The form of AirMesh is conceived as a polyhedron defined by four rectangular view frames oriented towards highlights in the surrounding landscape: the dragonfly bridge, the silver garden, the Marina Bay Sands, and the pavilion entrance. Its faceted form reinterprets a traditional Chinese lantern, lighting up in dynamic color gradients.
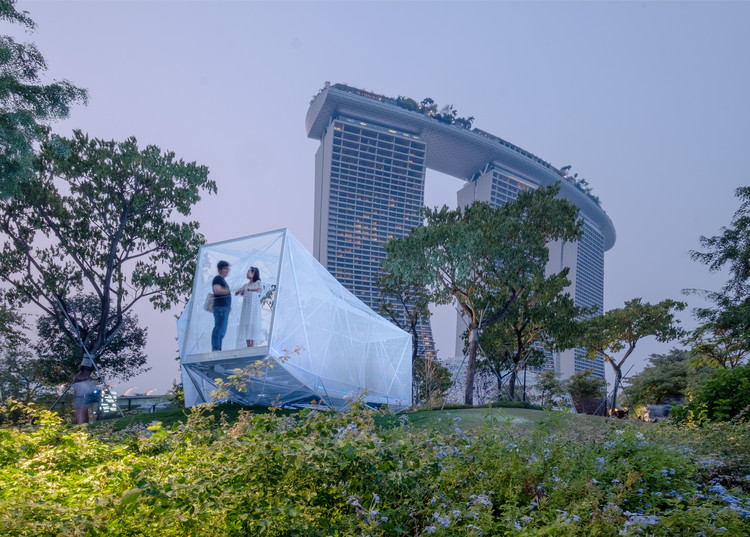
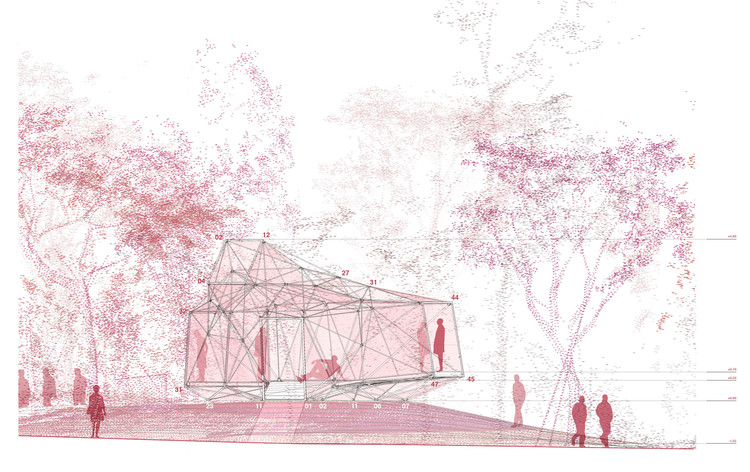
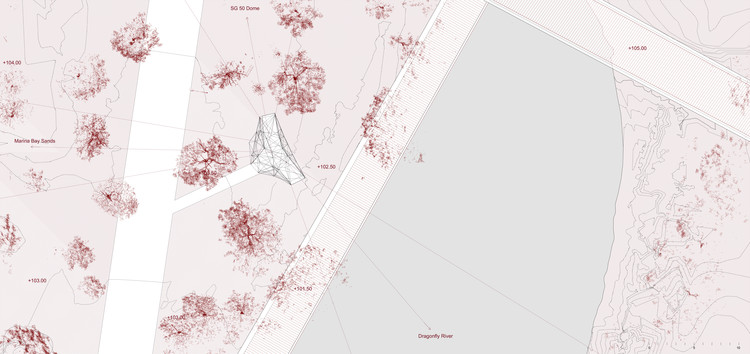
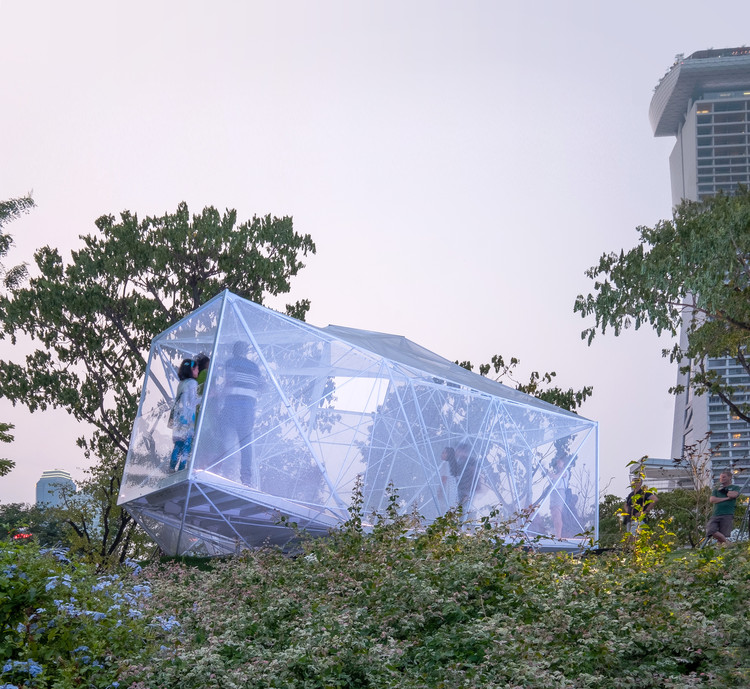
The structure was designed using a custom parametric tool that optimizes the topology of the frame, the section of the bars and the geometry of the node with the objective of creating the most efficient structural design. As a result, the structure presents the optimal configuration and distribution of material where mechanically needed. The pavilion consists of 216 bars of different lengths and sections, and 54 unique nodal joints printed in a steel and bronze alloy.
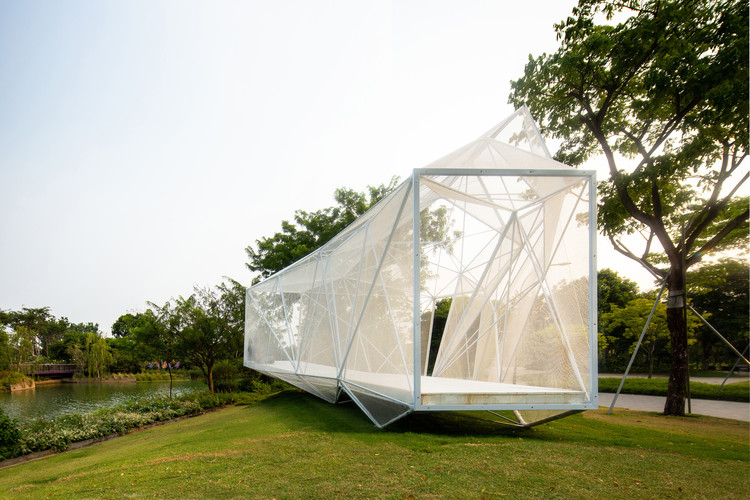
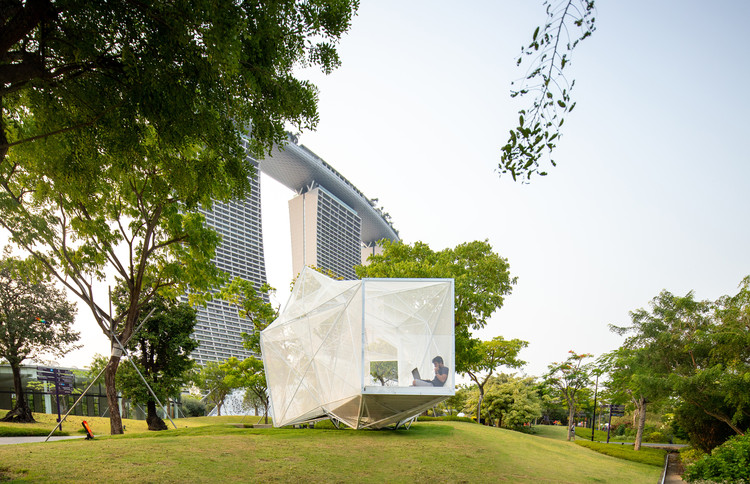
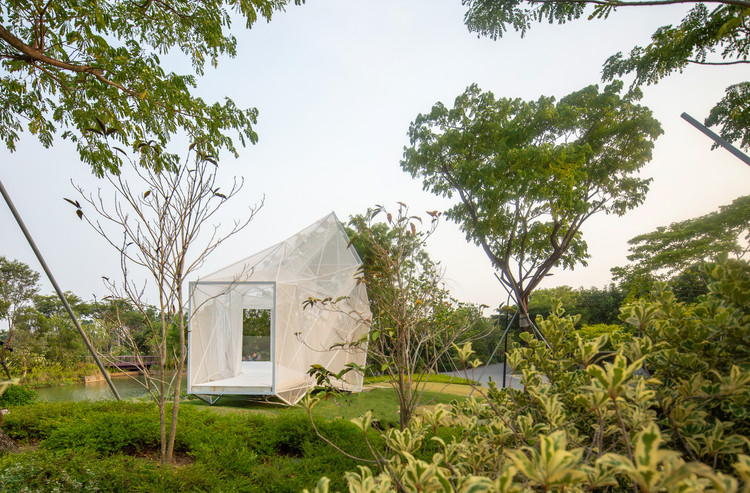
The assembly of the structure took only two days by five people, as a result of big technological innovation applied to the connection of the elements, being able to 3D print the threads inside the nodes to facilitate the assemblage with bolts concealed in the bars. Only hex keys of different diameter were needed to assemble the entire pavilion. The system allows for tolerances of less than a millimetre and perfect fit of components, taking construction in stainless-steel to a next level of rapidity and performance.
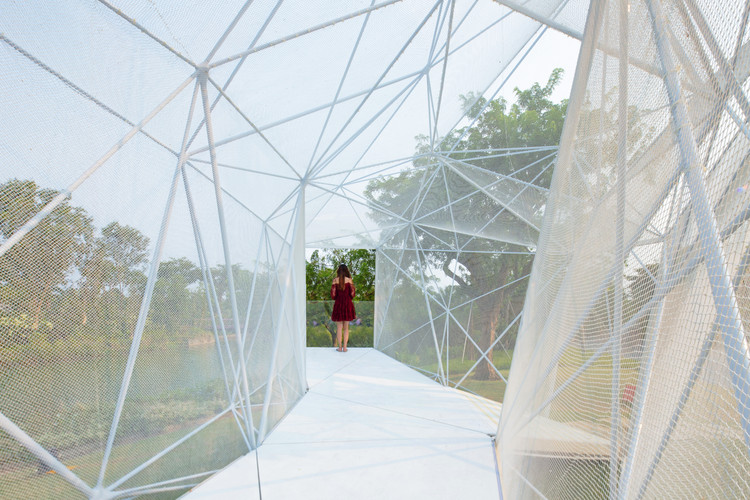
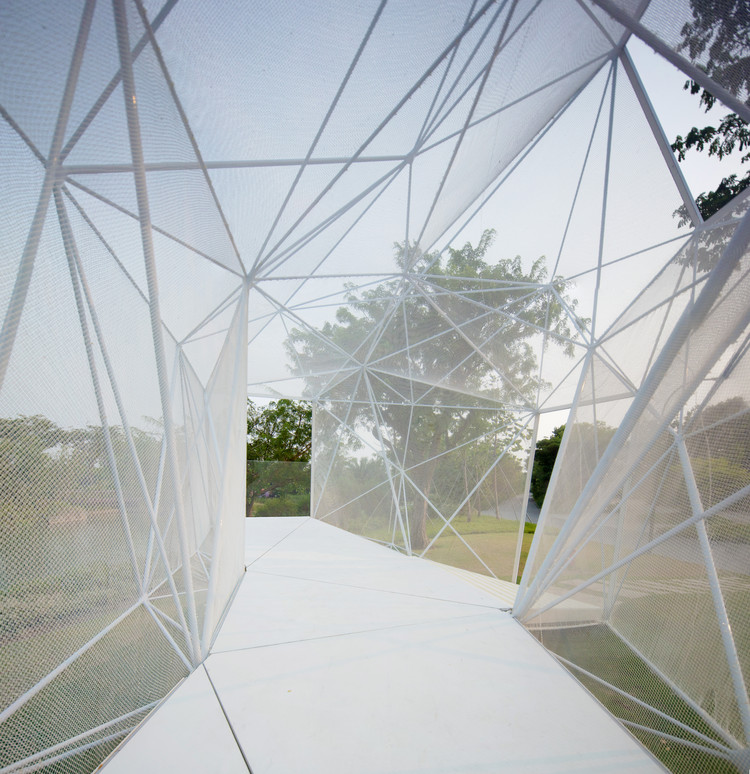
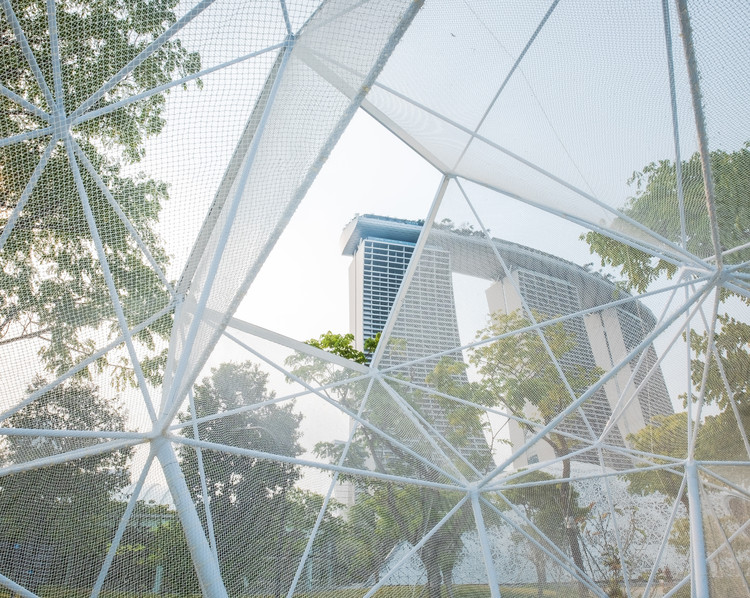
The structure has a weight of 700 kg, and despite its delicate and fine appearance, is able to withstand loads 16 times its weight - more than 11 tones. Typically, current space frames systems consists of a repetition of a regular pattern, primarily due to the impossibility of resolving complex geometries with a limited number of standard nodes. As 3D-printing eliminates the incentive of using standard parts, the economic benefits of using a repetitive pattern is reduced. To design space frames with this greater design freedom, new tools, technology and innovation were required to materialise Airmesh.
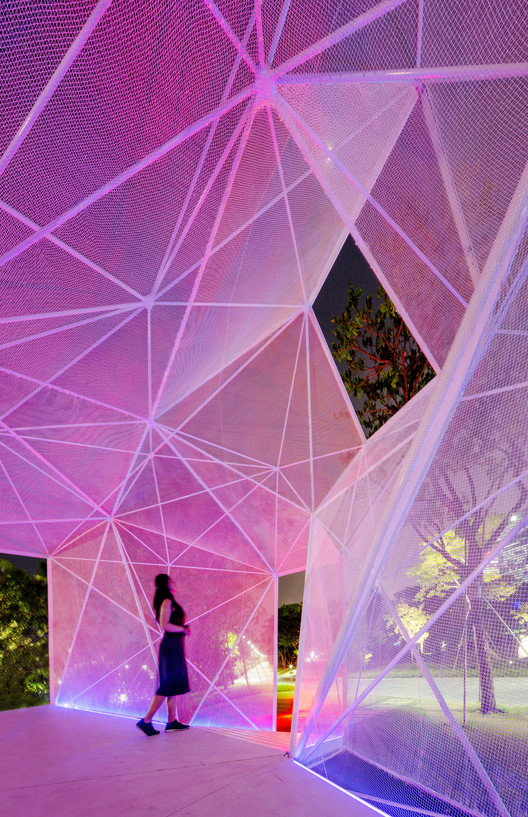
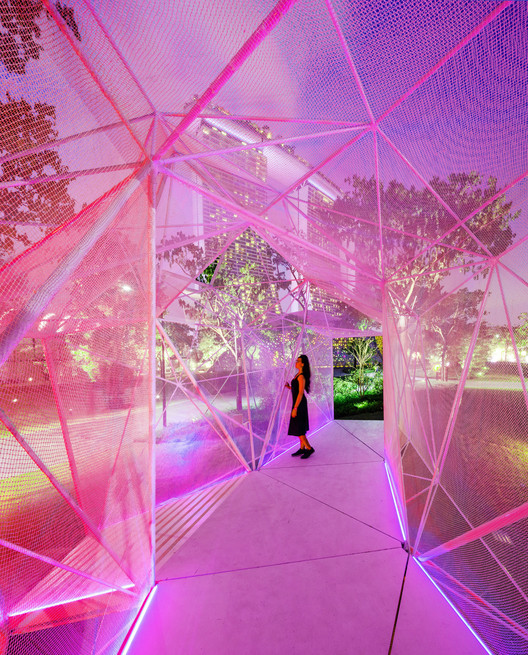
Digital design opens creativity to nearly endless geometric freedom, mass-customization, and optimized, ornamental, multifunctional architectural structures. In tandem, 3D Printing served as a promise to materialize wild design visions into built reality; yet an unfulfilled one due to size, time and cost constraints. AIRMESH approach, rather than 3D printing the entire structure which would result in very high costs of production, combines 3D printed components with standard elements in a seamless way. It sets path for full free-form designs, with a rapid assembly and in a more affordable range.
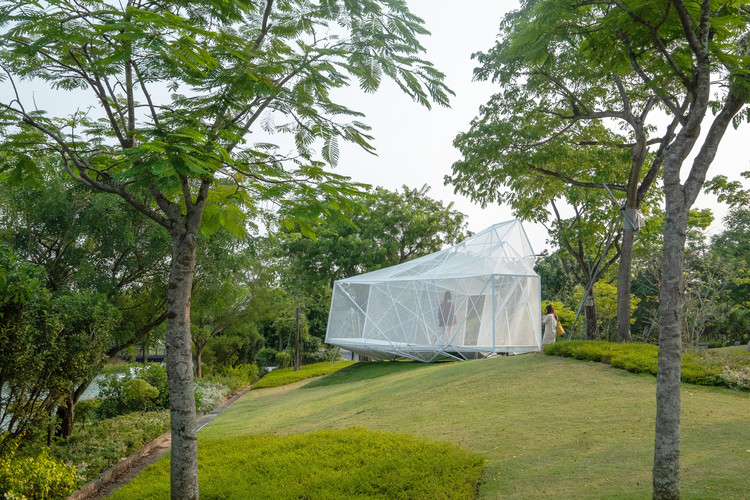
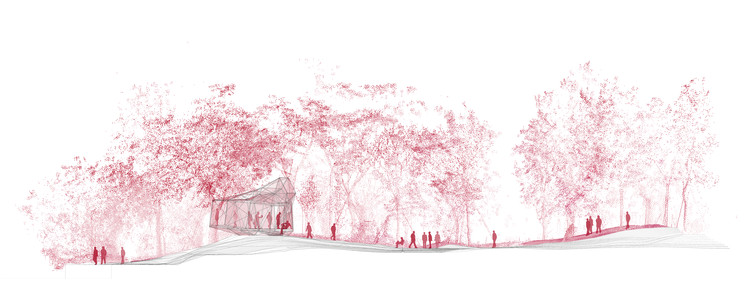
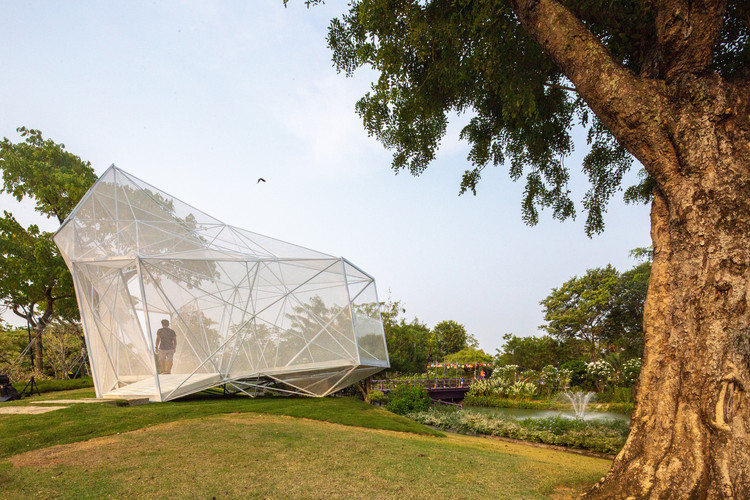
The form of the nodes blends seamlessly with the bars, giving the whole a sense of continuity and structural fluidity across its components. The two-layered breathable skin of the pavilion is a porous fishing net tensed towards the structure. Its transparency allows the breeze to pass and the structure to be seen yet evidences the form and captures the RGB light. The view frames serve as openings for the envelope, where the primary views are presented unfiltered.
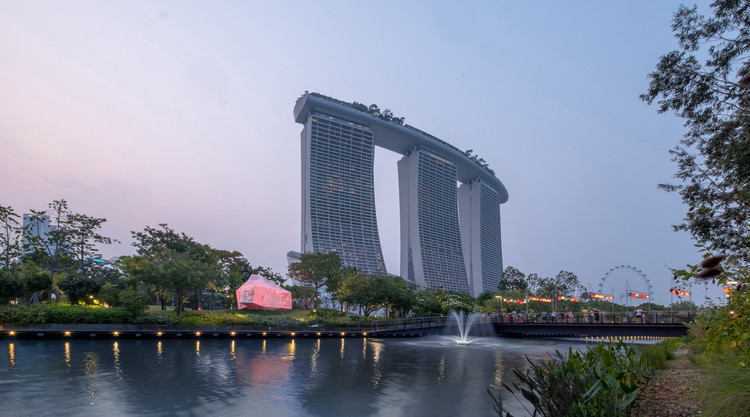