.jpg?1544663294)
-
Architects: gad·line+ studio
- Area: 300 m²
- Year: 2018
-
Photographs:Guangkun Yang, Stray Bird, Jiaxin Shi
-
Lead Architects: Fanhao Meng
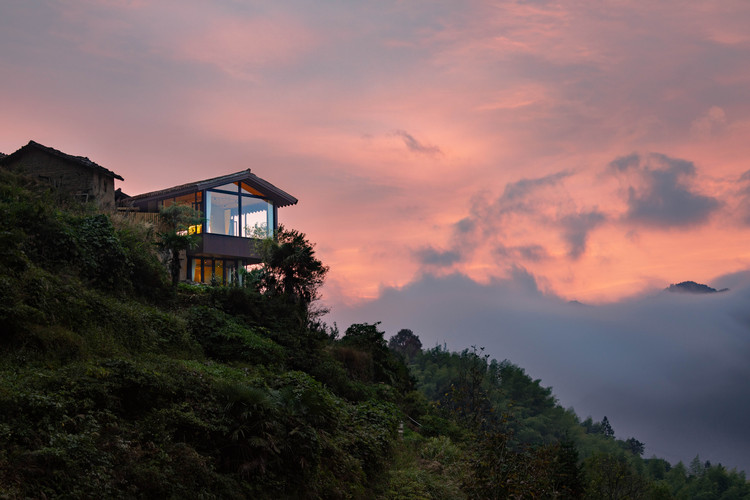
Background
“The returning paths westwards are congested; there is rare communication once in the south; only this utopian place exists as a secret garden”. As this old poem describes, Songyang has been hailed as the "final secret place in the south of the Yangtze River” since ancient times. 15 kilometers away from Songyang County and in the depths of the Dazhong Mountain, the ancient village Chenjiapu is built above the cliffs with a history of more than 600 years. It is up in the sky and surrounded by mountains on three sides, facing the deep valley.
Chenjiapu Village is built along the mountain and its settles are distributed along the terraces of the mountain which embraces a fall down more than 200 meters. The overall appearance indicates it as a typical southern cliff settlement-cluster of western Zhejiang. Nearly 100 residential buildings are mostly rammed earth-wood structures, retaining the complete traditional village morphology and built environmental features.
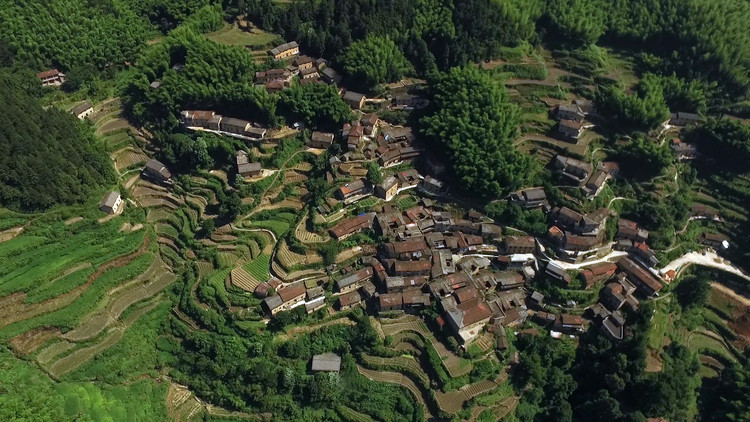
It was the harvest season when the first time line+ studio visited the village. When the sun shines on the village and the cliff, the rammed earth walls are so bright and beautiful. Every family were drying their own sweet potatoes in front of the doors, turning out a field of golden colors.
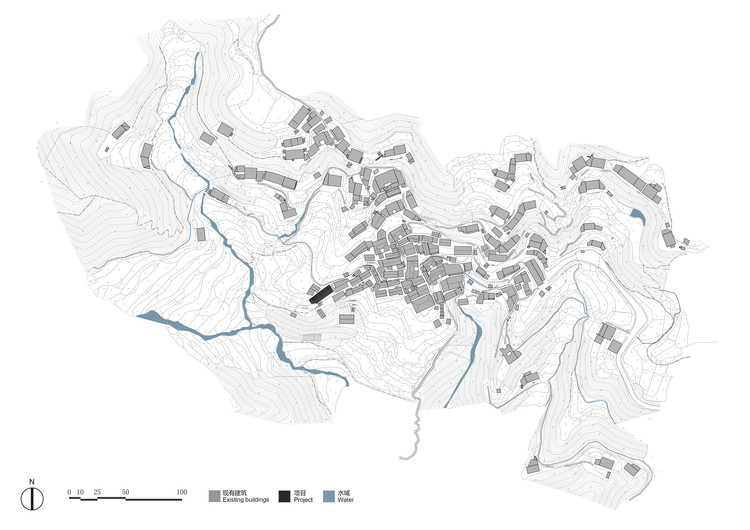
The task of line+ studio is to transform two traditional houses on the southwest side of the village. The two dwellings are typical rural houses in southern Zhejiang, three sides of which are rammed earth walls and one façade is the adjacent to a stone retaining wall with a traditional wooden roof structure. When the cars arrived at the entrance of the village, it couldn’t move forward. It took about 300 meters to walk to the project site. However, the village hillside-path twisted and steep, the narrowest part of the path only allowed for one person to pass through.
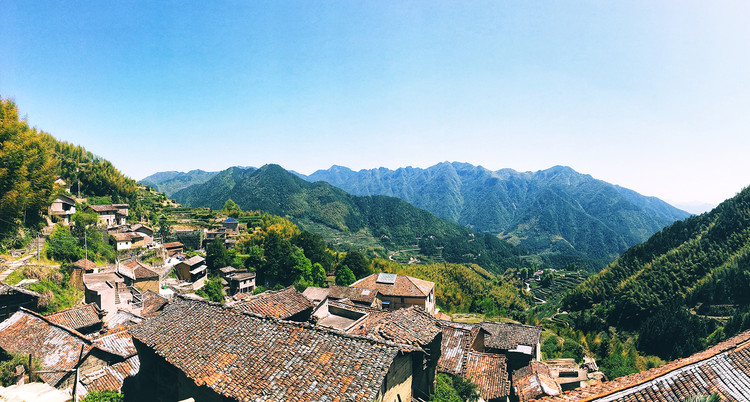
Limitation and Requests
As Chenjiapu Village is one of the historical villages in Songyang County, whose government has very strict regulations on the feature-control of traditional historically protected villages. However, the project owner hopes that the reconstructed space will have a sense of experience and comfort, and can respond to the outside invincible scenery.
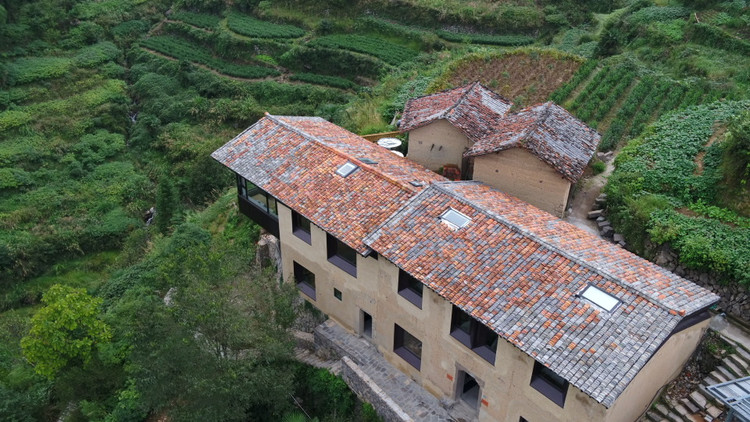
Therefore, line+ studio has developed two strategies at the beginning of the design process to respond to the two seemingly contradictory requests. The design always follows two parallel lines in the whole procedure: first is to study the local construction system of Songyang residential settlements, and to conclude the spatial structure and stable construction features that are compatible with local natural resources, climate environment, complex terrain, production and lifestyle and cultural characteristics, which provide design basis for maintaining the traditional settlement features; The second is to use light steel structural system and fabricated construction technology and implant new programs, to adapt to the harsh on-site working condition so that meeting the urgent construction timeline and providing better building physical properties at the same time.
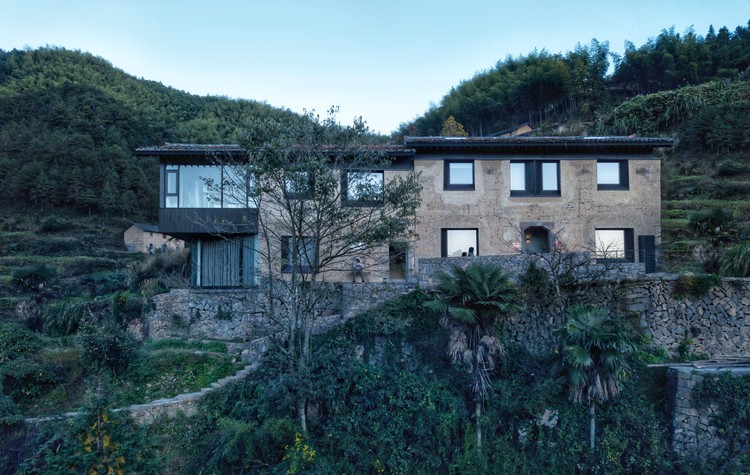
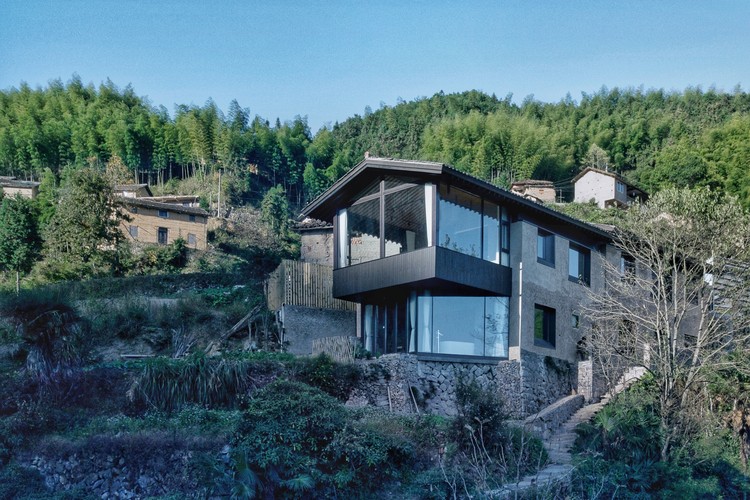
Research on the Tectonics of Local Rural Houses
The design begins with surveying and mapping, sorts out the tectonics system of local rural settlements, and analyzes the current applicability of its composition and characteristics. The researches include construction material ratio, construction technology, site planning and environmental climate adaptation.
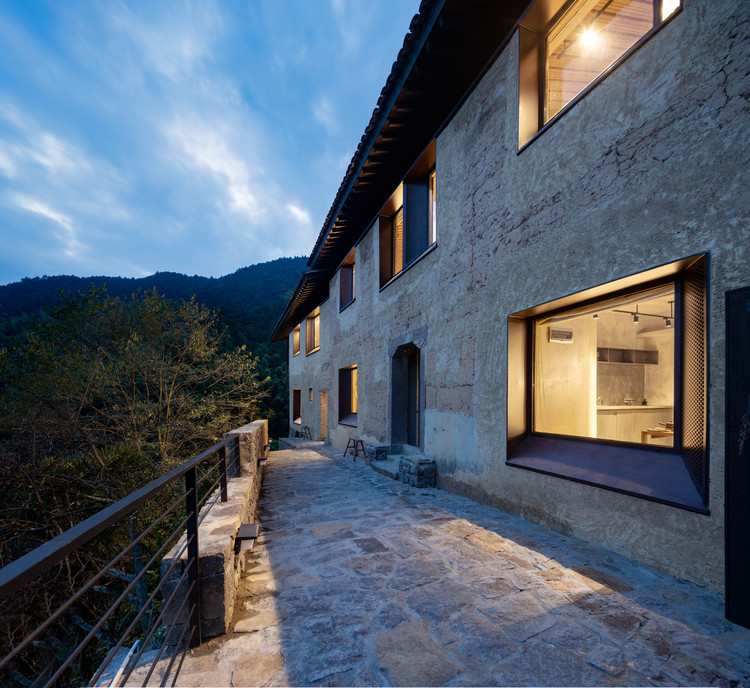
The team not only visited local traditional craftsmen, collected work methods, perceived material characteristics, and learned the traditional construction process. At the same time, we also consulted with modern bauxite technology professionals to adjust the material ratio, optimize material properties and technical processes, and learn the bauxite repair technology.
Finally, based on the previous survey and mapping, the team sorted and classified the architectural elements and materials with local features, roofs, walls, doors and windows, structural details, and etc., and established local materials and engineering pedigrees. Afterwards, the reference basis for the updated design was revised.
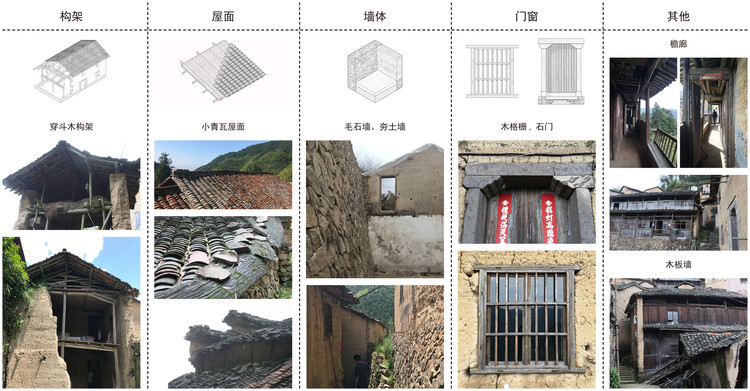
Structural Form Selection
The project is located in a remote mountainous area, transportation is inconvenient, large-scale construction machinery cannot enter, which gives more challenges for the modern space transformation these two traditional houses. In order to cope with the severe construction environment, the design begins with the structural form, and integrates various factors, and decides to adopt a new light steel assembly structure system.

The structural beam column as a basic unit is in a section size of 200 x 90mm. It is cold-rolled and made of two C-shaped steel clasps with a thickness of 2.5mm. The units are bolted instead of welded which ensures smallest structural unit to solve the transportation problem. This bolt-connection mode and the high prefabrication rate are very convenient for on-site construction and installation.
.jpg?1544662354)
Space Transformation
The rammed earth walls of the two residential dwellings are relatively well preserved so that the design keeps all of them. The interior space of the original building is divided into very small units. The wooden truss has also been in disrepair for a long time, so has to be demolished and replaced by the new light steel structure. The new structure was separated from the reserved rammed earth walls to prevent the walls from undertaking the load from the new structures.
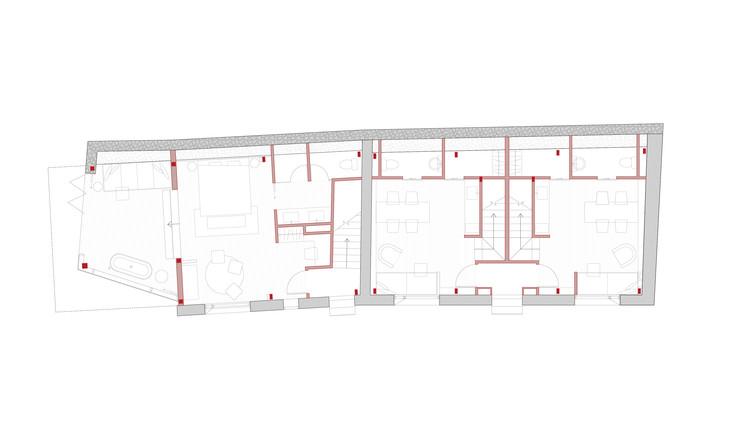
Building 1 is located at the end of the village and has a high degree of privacy. The west side of the building faces the canyon and the view of the landscape is excellent. Therefore, it is designed as two flat rooms on the upper and lower floors, and the west side is mainly made of transparent floor-to-ceiling glass allowing the users to enjoy the landscape. The south side as the main façade remains the feature of rammed earth wall to make the building blend with the traditional features. The first and second floors share the entrance, and the circulation space is close to the side of the building gable.
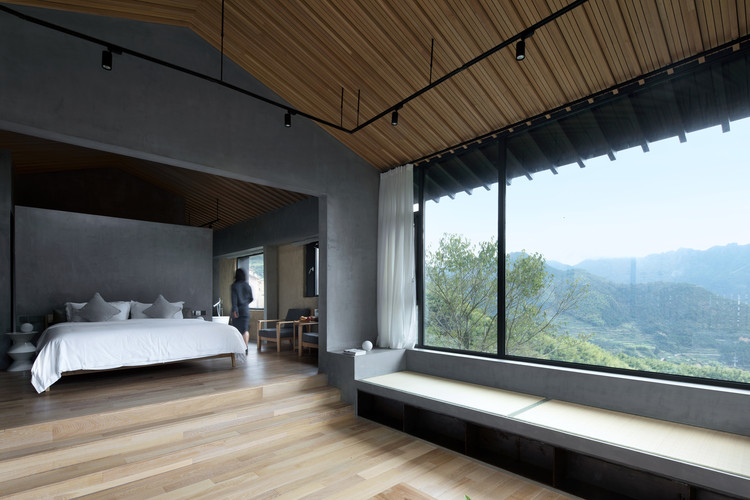
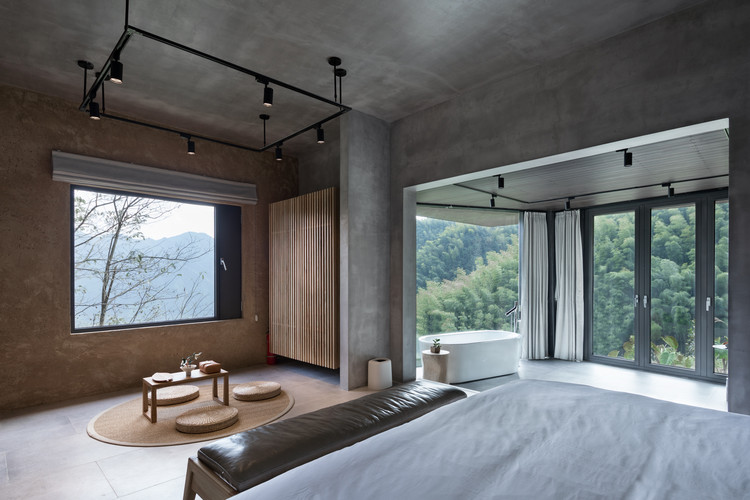
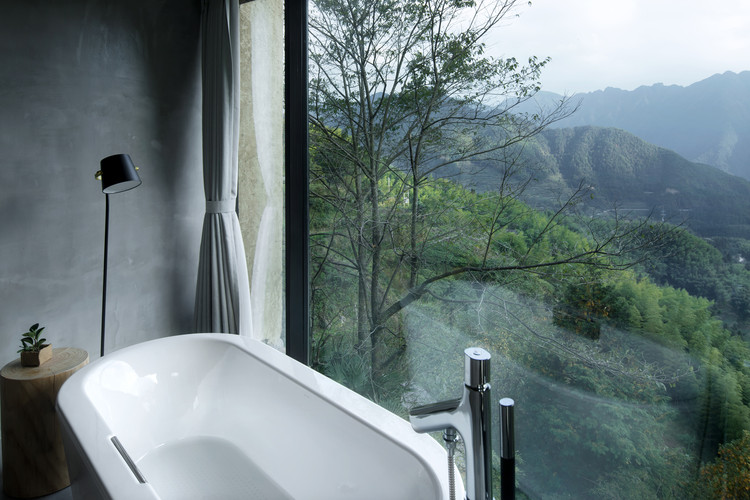
The south side of Building 2 is close to the road. Considering the privacy of the living space, the room is designed as LOFT space, in which the living room is on the ground floor with a landscape sofa-bed by the window and the second floor is the bedroom whose bed and bathtub are facing the landscape.
.jpg?1544662121)
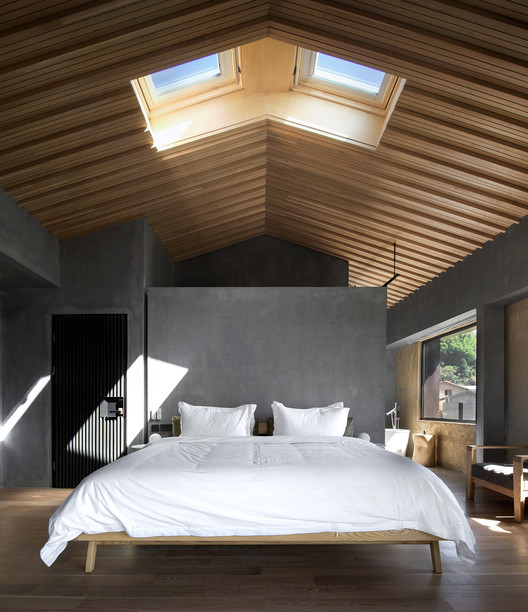
The heights of the original old buildings were so low that they cannot meet the needs of modern living spaces. Therefore, we will raise the original building roof, and the increase height is distributed both to the upper and lower floors in a reasonable way to reserve space for indoor equipment installation and also create a comfortable living experience. On the western side of Building No. 1, the original brick house has already collapsed and abandoned. We built according to the size of the original plot, and cantilever a glass volume on the second floor, which can be used as an extension of the indoor space and better to enjoy the canyon landscape.

Assembly Construction Process
Demolition and Protection
First of all, the building quality assessment of these original rural houses was conducted. The parts with potential safety hazards were removed. The parts with good building quality are preserved and reinforced by using and the recycled materials such as wood, grey tiles, bricks and stones.
The Foundation
The basic dimensions of the original building are measured to ensure that the new structure is within the original plot. The foundation layer is ensured stable. The design uses a flat foundation and the reinforced column foot structure. The foundation structure and the reserved rammed earth walls are kept a safety distance in between to ensure the safety and stability of the bauxite wall as well as enough space for construction operations. Integrated pipelines are pre-buried, the floor heating is laid.
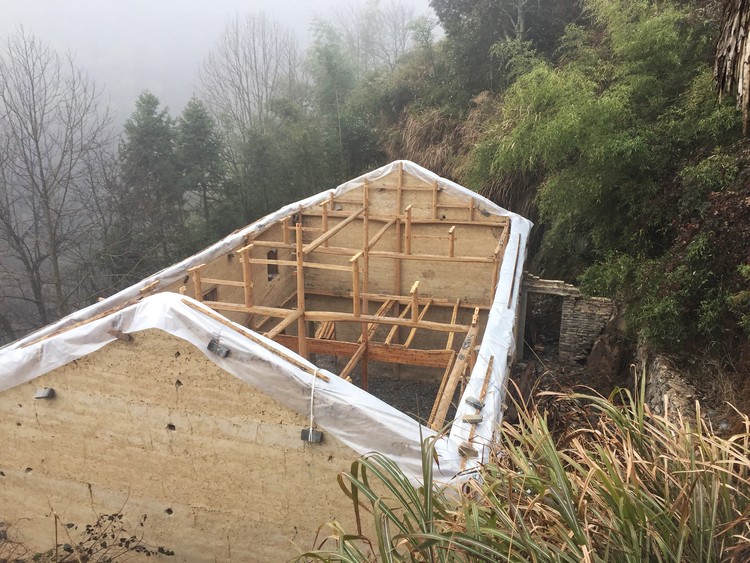
Main structure
The structural unit are prefabricated, then packaged and transported to the project site. According to the prefabricated details, the workers assemble the structural unit rods on site and complete the main structural part in only one day.
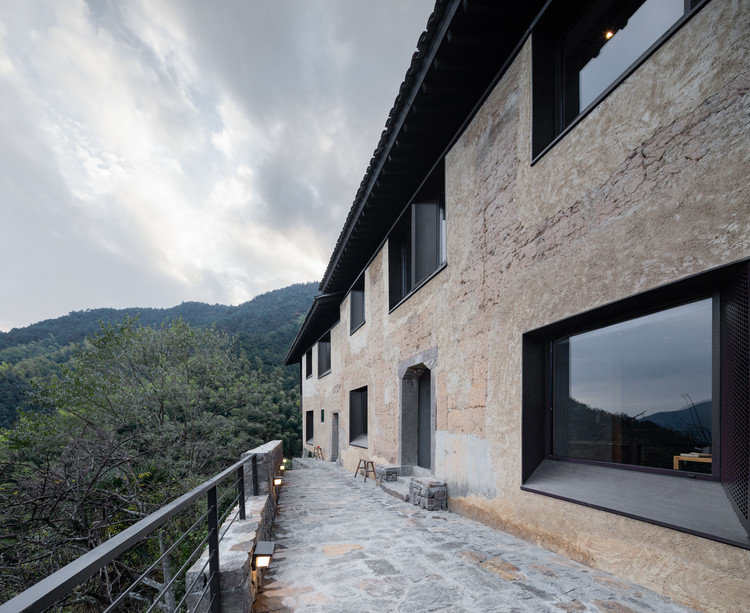
Floor and interior partitions
The renovation plan adopts the exterior-interiors integrated design and construction method. Therefore, the indoor partition wall, stairs, pre-buried pipeline can be prefabbed in the factory and assembled on site to ensure construction accuracy. The partition walls are made of C-type light steel as the skeleton, the metal mesh plate covered, and filled with EPS foamed concrete inside. This makes light weight, good thermal protection and sound insulation partition walls which are conveniently constructed.
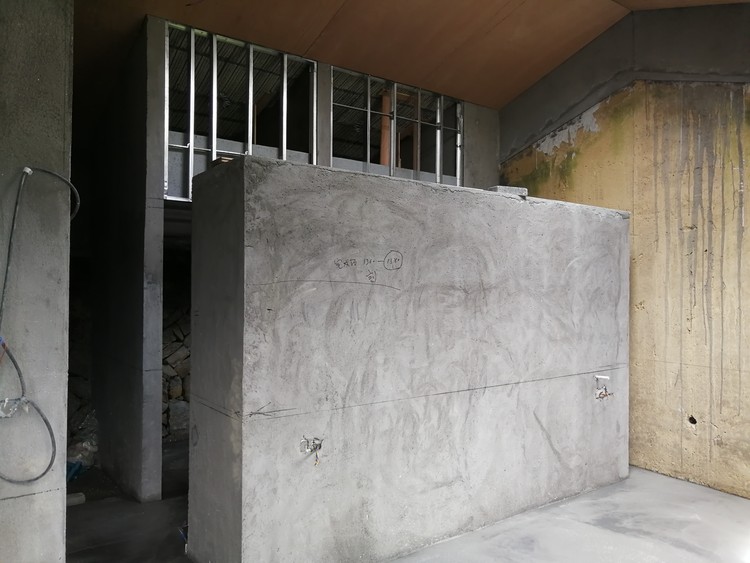
Renovation Process of Residential External Enclosure Structure
Protection and repair of rammed earth wall
In order to retain the original wall to the greatest extent, therammed earth wall is separated from the newly-built structure to avoid the loads; the second floor is raised due to the increase of the indoor floor height, and the new external wall below the cornice is designed in the form of curtain wall and attached to the main steel structure. The local peasant construction workers use traditional handicraft techniques to repair the rammed earth walls, as well as sprayed a protective layer onto the interior walls. The original entrance door and the stone door covers are completely preserved.
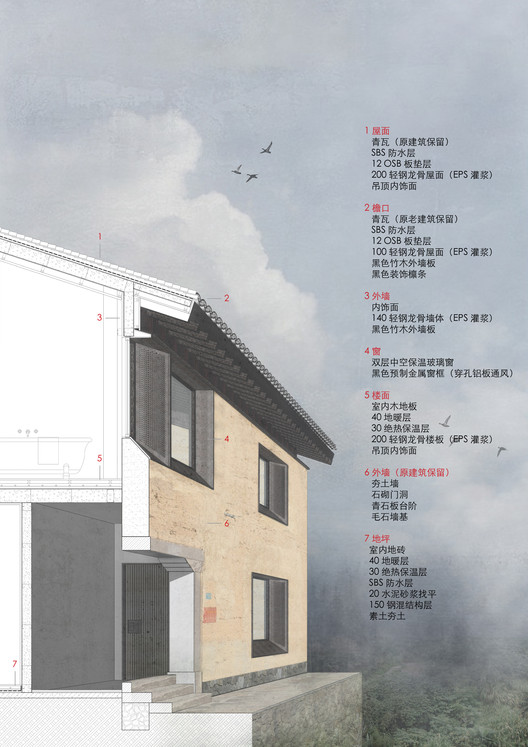
Stone Retaining Wall
The local rural houses in the village conform to the topography and landforms, and are built on the side against the mountain. Most of the houses are using stones as the retaining wall. The design intends to preserve this structure that expresses the characteristics of the regional construction. First of all, it is necessary to repair and reinforce the stone retaining walls to ensure the structural stability. Mountain soil contains water so that there is seepage on the stone. This is solved by pre-burying the drainage pipelines. The gaps between the stones are poured in with concrete and coated with waterproof layer, creating a comfortable indoor living environment.
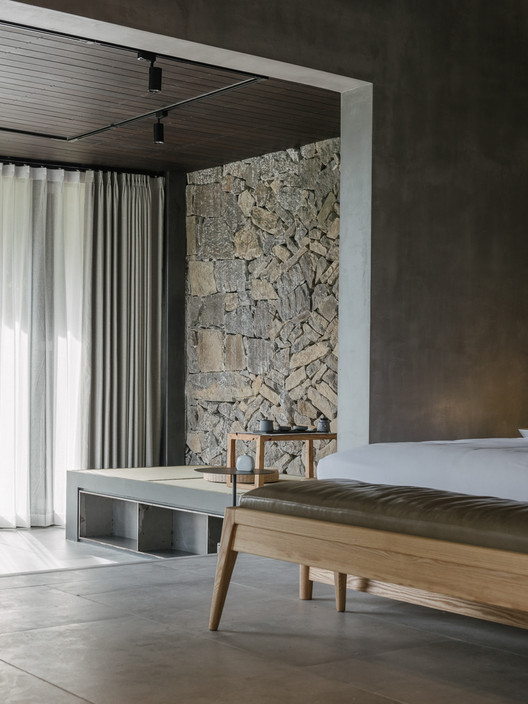
Door and window system upgrade
The openings of the traditional rural houses are small, which are unable to meet the needs of the guest rooms for lighting, ventilation and views. In order to improve the lighting environment and landscape view, the original door and window openings were enlarged, and then the modern door and window systems are installed to ensure the airtightness of the exterior protective structures and enhance the thermal insulation performance. The specially designed aluminum perforated window frames not only provide ventilation, but also ensures a simple and consistent facade.
.jpg?1544797220)
Preservation of the tile roof
The light steel-structured roof is filled with EPS foam concrete and covered with waterproofing membrane. The design uses the grey tiles recycled from the old buildings as the surface layer, which not only responds to the regional culture, but also reflects the sustainable ecological concept. At night, in order to allow guests to enjoy the beautiful starry sky, skylights are added to the roofs above the beds.
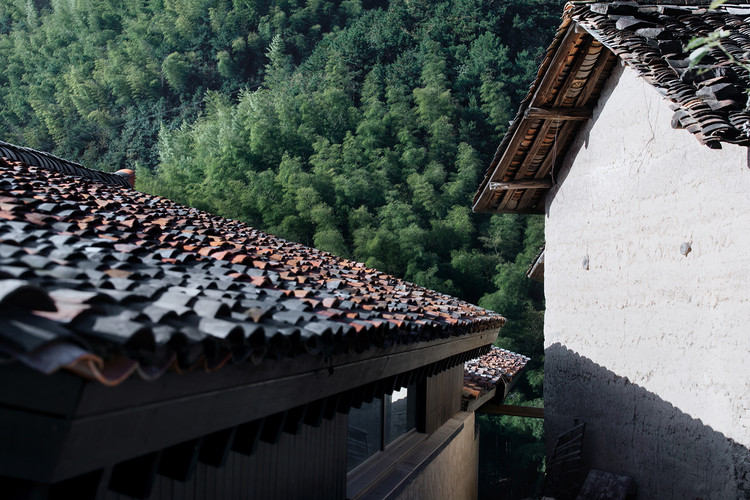
Conclusion
The purpose of historical cultural village protection is for its better development. It confronts the strict control guidelines of the local and traditional features but still needs to meet the requirements of new programs. The development of the countryside not only needs to face the natural environment and traditional context, but also needs to create a high-quality space that meets the needs of modern life. line+ studio attempts to combine traditional craftsmanship with industrial prefabrication in this rural transformation project. The light steel structure equips the modern space with a lightweight skeleton and at the same time the traditional rammed earth walls feature it with local characteristics. At the same time, the materials are collected locally, and the old materials are recycled and reused to realize the unity of opposites between “new and old, heavy and light, real and virtual”.
