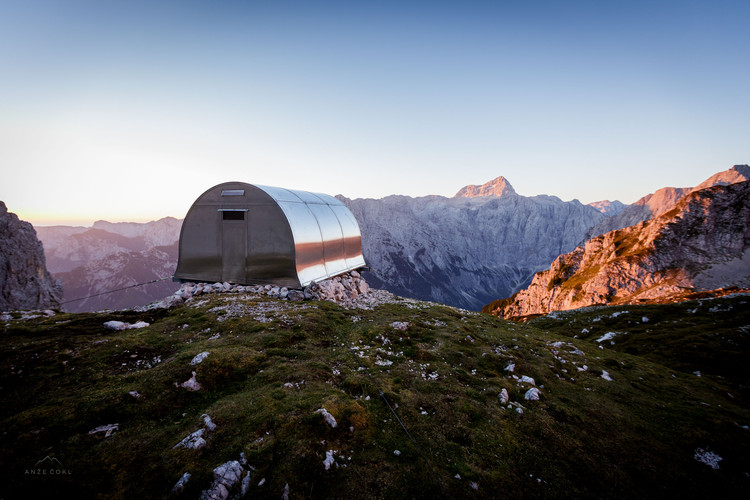
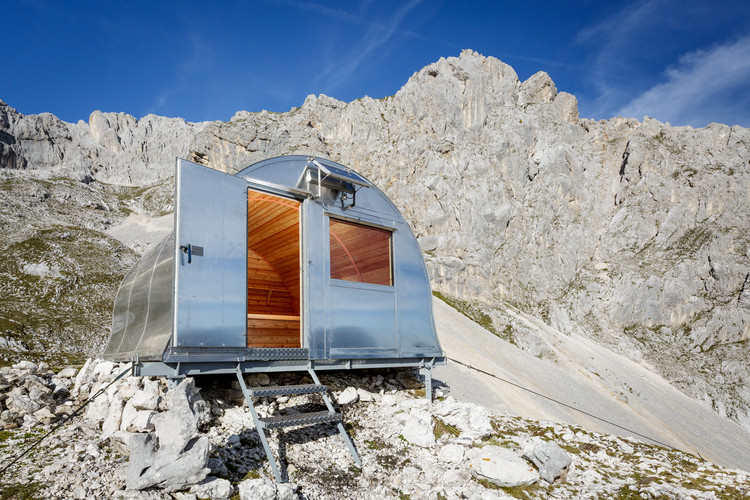
Text description provided by the architects. More than 80 years ago, visionary minds of alpine climbers in Slovenia decided to build alpine shelters in the Julian Alps. In 1936 there were no access roads. What used to take climbers and hikers days, takes a couple of hours nowadays. With better infrastructure and general access however, parts of Triglav National Park’s most sacred places still remain pristine and less visited.
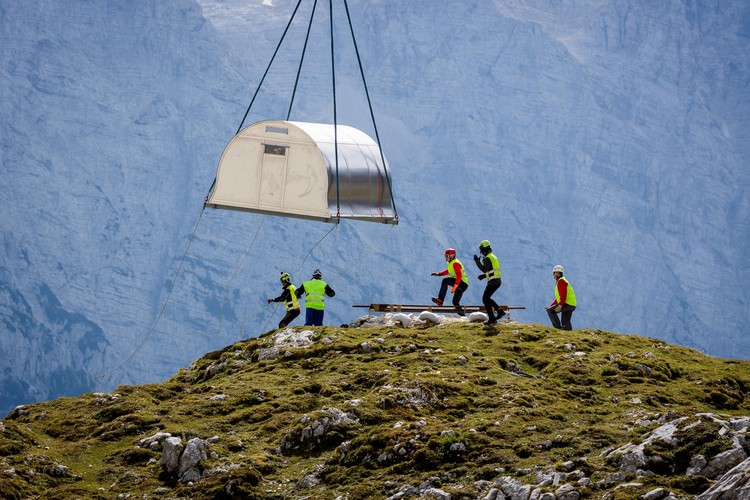
In 1936 Skala club members had decided that building small, but functionally ingenious alpine shelters, would save time and effort to climb mountains and make them more accessible for exploration. Bivak II na Jezerih was built on the designs of engineer and mountaineer Karlo Korenini. Together with climbing buddies, they have transported over a ton of wood and steel on their backs alone and built the shelter on the spot! It was in service for respectful 80 years, especially considering the harsh environment and relatively basic materials available at the time. However, wooden construction finally gave way and deteriorated the the point of breaking down.
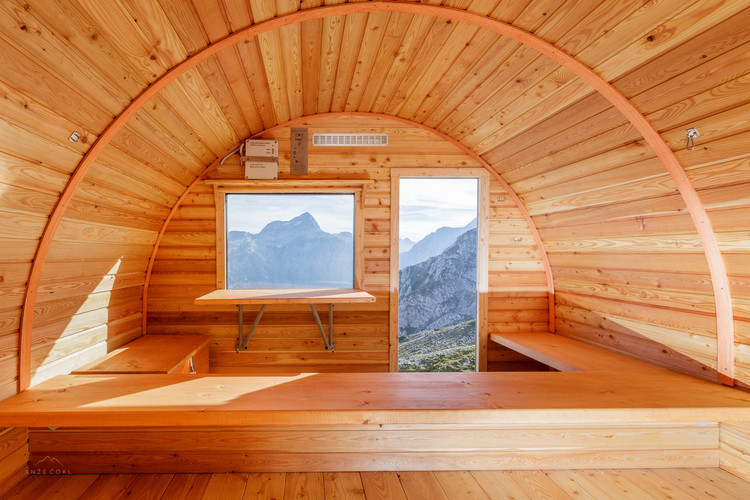
The original 1936 bivouac was airlifted on a custom made platform so that it would not crumble into itself. It was donated to the Slovenian Mountaineering Museum as an exhibit.
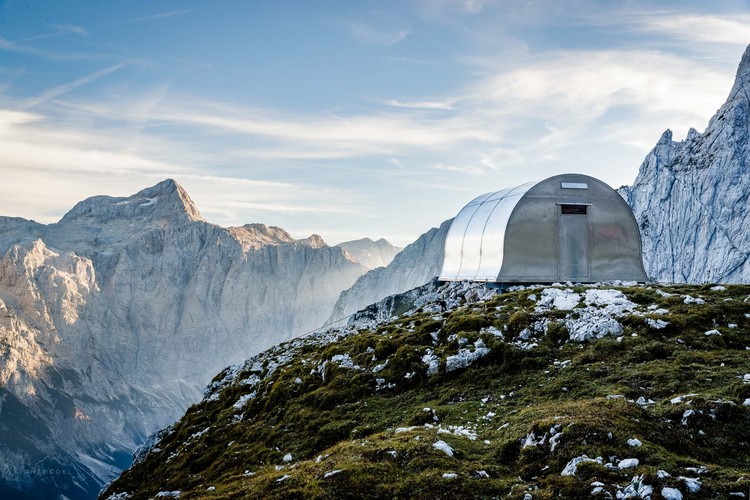
Main restrictive factors affecting the design were thus set both by highly restrictive policies of the Triglav National Park and the extreme mountain weather and conditions as well as air-transportation limitations.
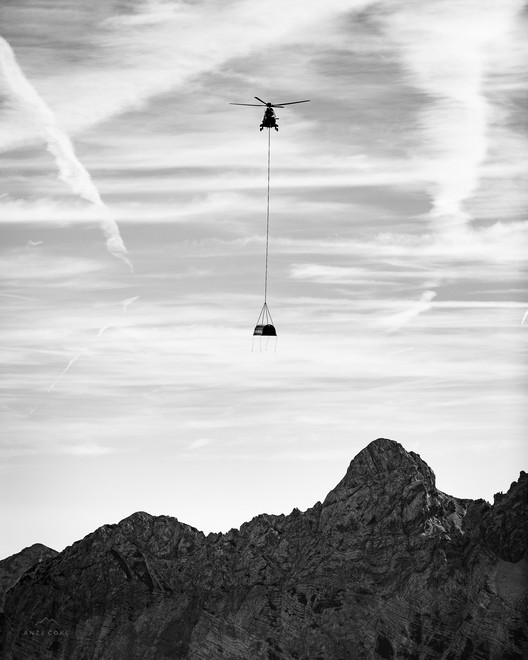
The following criteria had to be met:
- bivouac has to withstand winds of 200 km/h
- finished bivouac must not exceed the 1300 kg of total weight as this is the limit of the available air-lift helicopter for the area and height
- bivouac’s gross volume must be within 10% plus/minus of the original
- due to remoteness of the area the bivouac must be built as easy to maintain as possible
- the bivouac must be cozy and give priority to function over general attractiveness
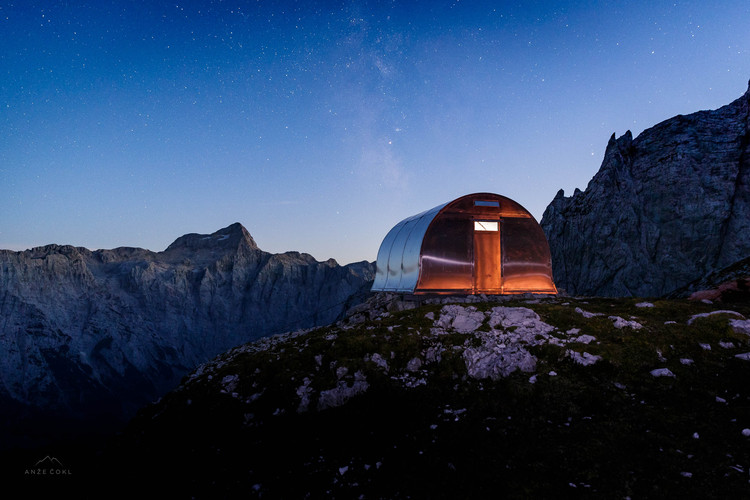
Bivak II na Jezerih was thus conceived on the basis of the 1936 bell-shaped original, retaining traditional outline, but with major improvements to construction, use and finishing materials and details. All with functionality and ease of installation and maintenance in mind.

Beside the extreme environment with hurricane force winds and few meters of snow and general exposure, having a relatively useful space on an area of less than 9m2 for 6 people is a challenge. With a folding table, overlapping bench (when sleeping feet are below and you sit from the other side), a box for accessories which you can also sit on plus many other details, make up for a better living comfort in the mountains.
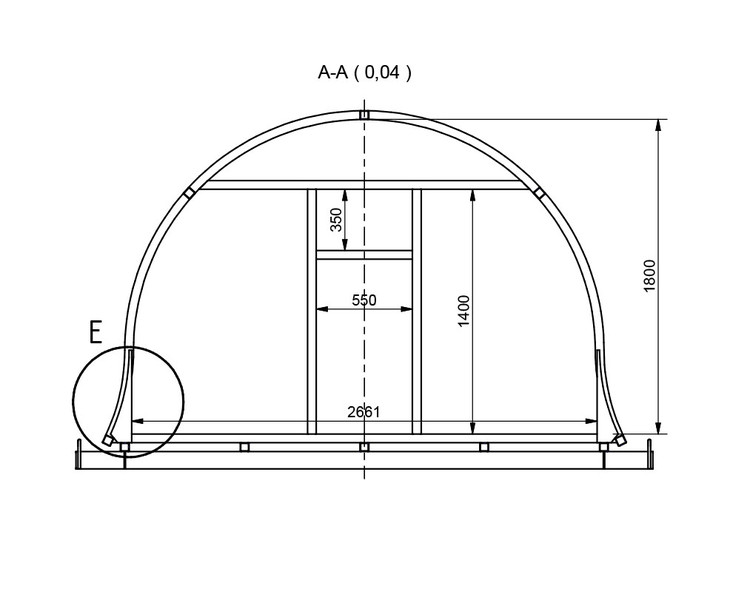
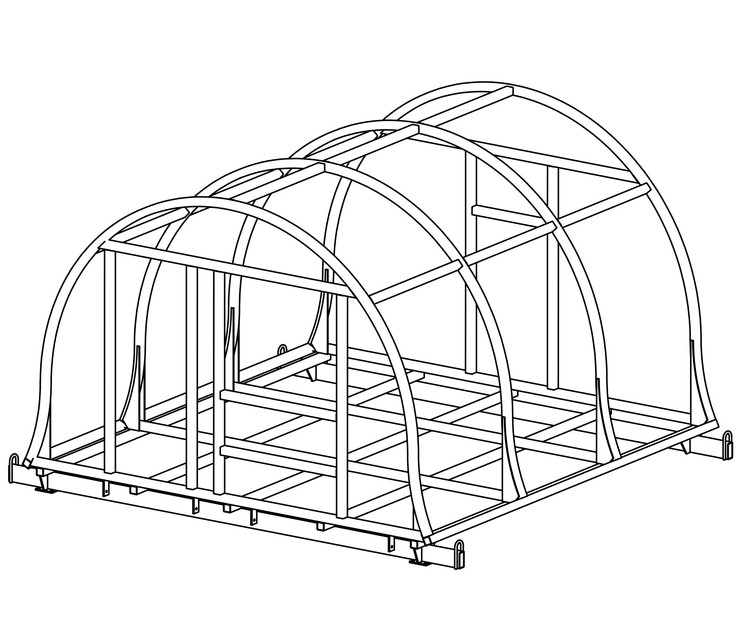
Having respected ingenious architects and builders of the 1936 and especially the solutions which proved to be working for almost a century, the newly built and vastly improved bivouac now stands open after over 600 hours of voluntary work for the mountaineers and climbers and the test of time.
Product Description. IMPOL Group 2 mm EN 3103 Aluminum was chosen as the main material for the harsh environment of the high alpine world, both from practical and aesthetic reasons, with limestone rock gray color blending nicely with the material in the sensitive alpine world.
The aluminum has a great look, low weight, is long lasting and is easy to work with. It was delivered in pre-cut plates from a roll by IMPOL Group. Plates were laser cut and trimmed in the workshop and pre-bent for later fixing. The aluminum had a natural look and finish of the EN3103 and with the passing of the time will get it’s final (somewhat oxidized) look, without any need of using paints or whatsoever, blending in the environment even better.
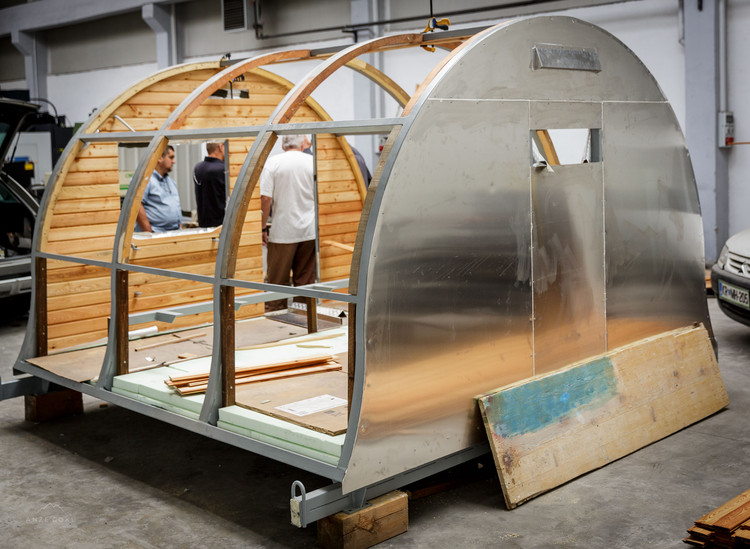
Aluminum EN 5754 of 4mm thickness with 3D pattern was also used for the entrance and floor, dividing the sleeping part. It was wrapped up on all sides to the verticals (wood) and welded, so it also holds water that could come off of wet boots of snow or equipment. There is an opening on one end where water can escape out of the bivouac. Aluminum for the floor is durable, non-slippery, and can withstand pressure of crampon points, should there be negligence or emergency by mountaineers walking in with crampons still on.
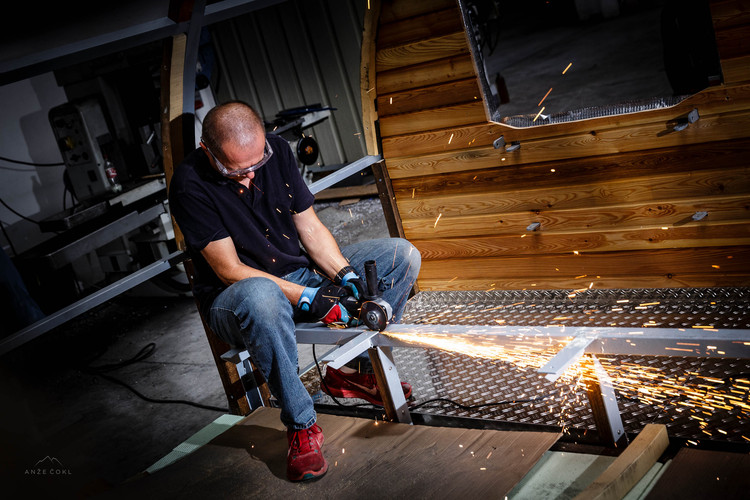
Construction was made of 4 mm steel, welded and optimized for low weight, galvanized and painted. All points of contact with aluminum were specifically protected to prevent negative galvanic cell effects. Special care was also taken with the selection of proper screws and at all points of contact.
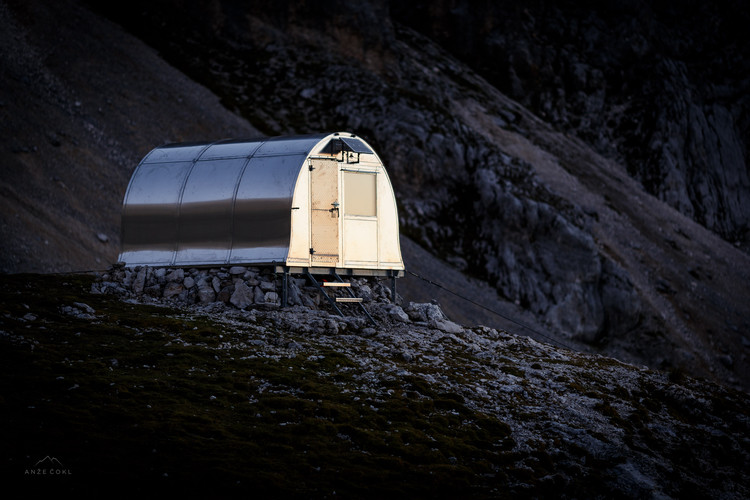
REFLEX provided specialty glass that is both safe and has protective features with superior insulating capabilities. The biggest concern was that the glass would not break before the final installation on the mountain due to the difference in altitude and thus pressure at the time of the production and before being installed on the mountain.
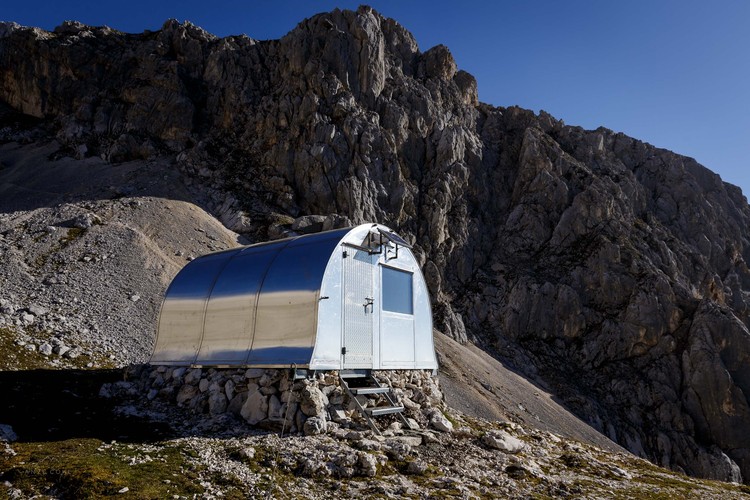
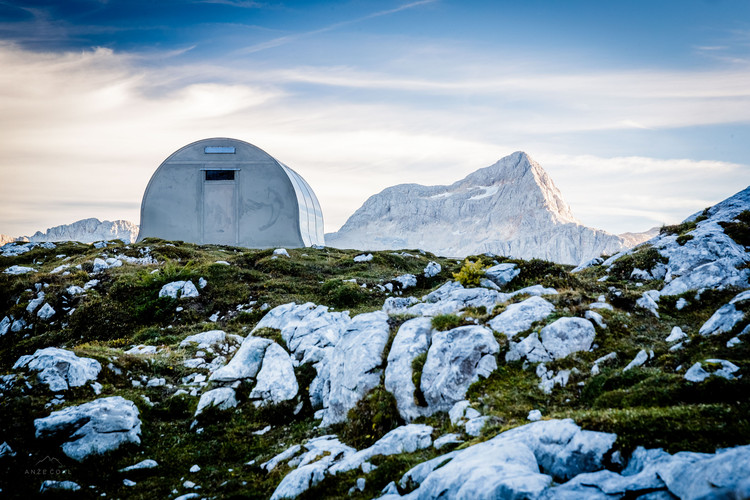