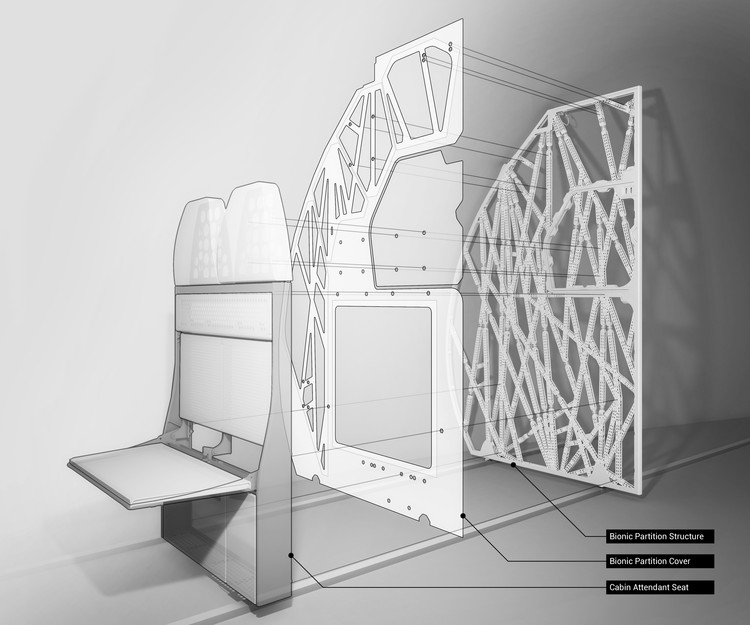
You’ve probably never given much thought to the seemingly basic interior partitions of an airplane, but building codes are a walk in the park compared to the exacting standards of aviation design. Those thin panels that separate the seats from the plane's galley must also be capable of supporting the weight of flight attendant jumpseats and providing a removable section to accommodate emergency stretchers - not to mention the rigorous safety standards and crash testing that aviation components must satisfy. With all of these challenges in mind, The Living, an Autodesk Studio, in collaboration with Airbus and APWorks, have developed the Bionic Partition Project, which harnesses generative design and 3D printing to maximize the structural efficiency of the panel, reducing the weight of an aircraft, and saving fuel. And while this particular application is specific to a single aircraft type, the technological advances could have far-reaching implications.
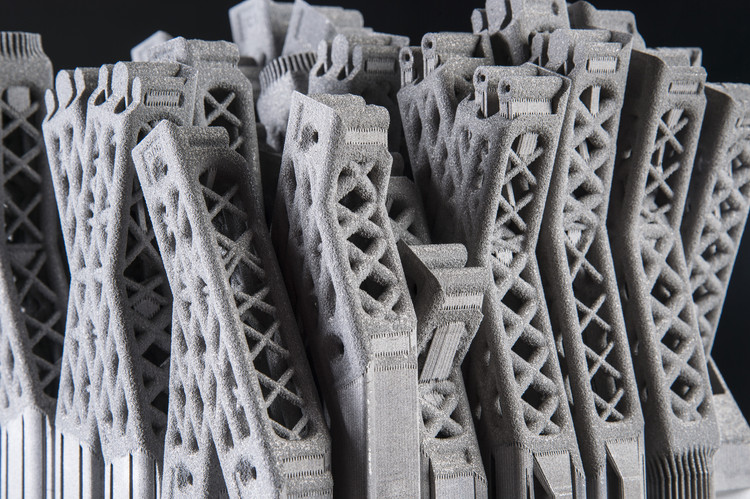
Designers at The Living first established the specific shape of the panel (sized to fit Airbus A320 series aircraft) and the connection points with the plane's shell. In what founding principal David Benjamin describes as "a continuation of broader work by The Living at the intersection of biology, computation, and design," they then used a series of custom algorithms to maximize the efficiency of the panel’s network of structural members in a process that mimics cellular structure and bone growth, as demonstrated in the video below.
The generative design process also informed the design and connections of the miniature truss-like structural members in the panel, which in turn generated the 3D printed parts that fit together to create the overall partition. The result is the world’s largest metal 3D printed airplane component.
Using this generative design process, and 3D printing technology, The Living and Airbus were able to reduce the total weight of each partition by 45%, or about 30 kilograms. And while 30 kilograms may seem minor in the context of a plane that can weigh as much as 93 tons when fully loaded, Airbus estimates that achieving these weight savings across the current generation of A320 series planes could result in a savings 465,000 metric tons of CO2 every year.
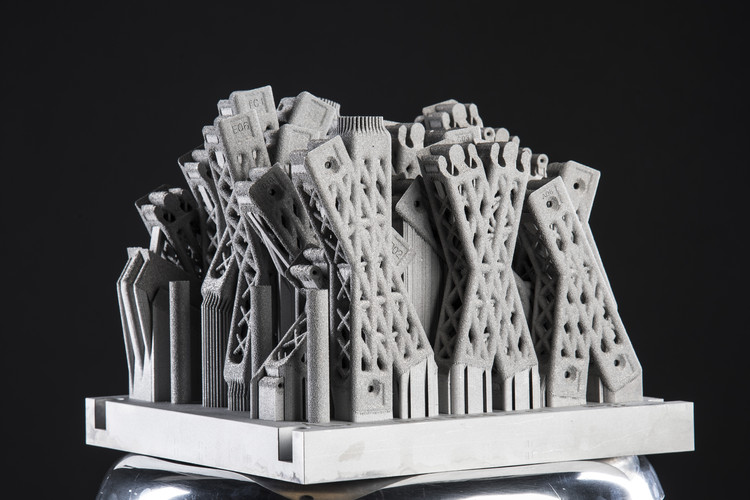
Back on solid ground, buildings don’t need to constantly burn jet fuel to stay standing, so architecture does not face the same urgency as the aviation industry to adopt every possible efficiency. Even so, the generative design process that The Living used in this proposal could help architects develop innovative structural solutions for challenging projects, or maximize the material efficiencies of building components in order to reduce environmental impacts.