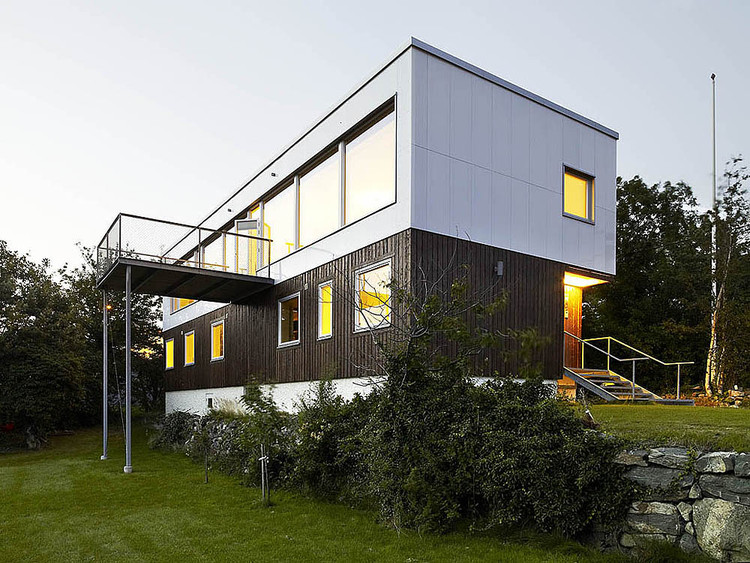
-
Architects: Unit Arkitektur AB
- Area: 210 m²
- Year: 2007
-
Photographs:Krister Engström
Text description provided by the architects. In Hjuvik just outside Göteborg Anna och Marcus Bohlin bought a property containing an old detached house. The area is a pure residential area which has been thoroughly developed over the past 20 years with a great density of houses as a result. It has also led to the paradox that although all inhabitants have moved there for a view of the sea, no sea is visible from their own property as the nearby neighbor’s house is obstructing the view. This, combined with current Swedish building regulation which states that a kitchen, living room, bathroom and a bedroom must be accessible for a disabled person, leads to the tragic fact that despite the proximity to the sea, most people do not see it from the spaces where they spend most of their waking time - the kitchen and living room.
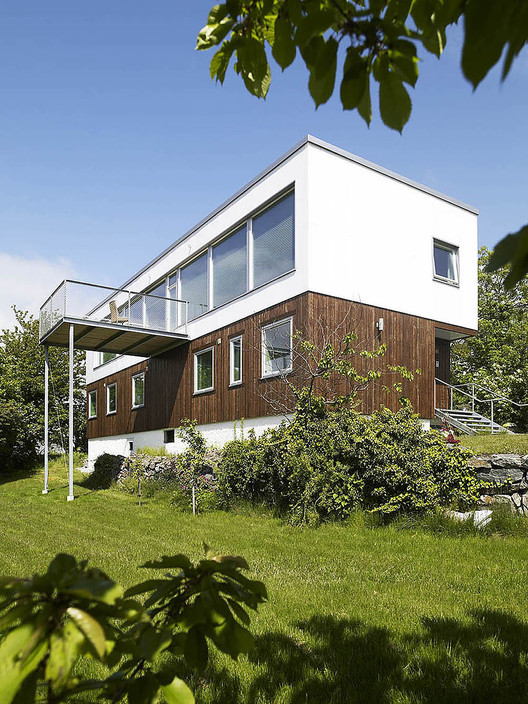
In the initial calculations, it proved too expensive to extend the existing house and it was consequentially torn down. The foundation was saved and thus defined the depth of the new building. Since the ground floor in this case had a dark and cramped position it was desirable to switch the floors - to move down the bedrooms and move up the living room and kitchen. It was possible to prepare for a lifting plate outside of the building, if the house is to be adjusted for a disabled person in the future.
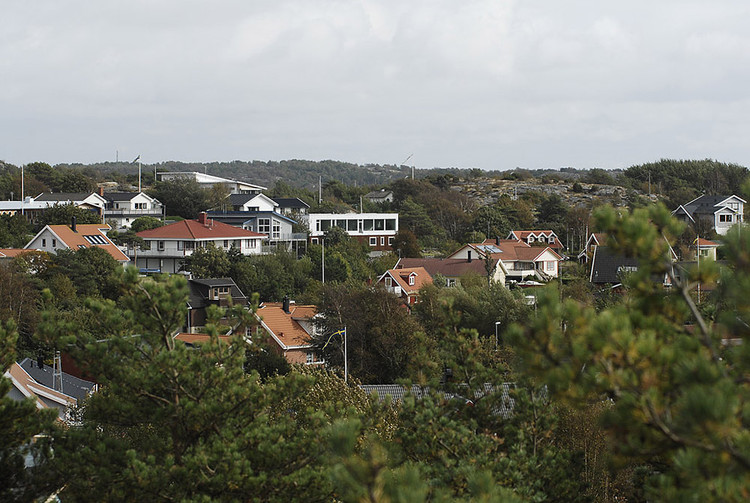
The clients wanted a larger house than the budget really allowed. This was made possible by a genuinely simple geometry and common materials; the outer form follows the logic of the shoebox and the layout is as straightforward as possible. It was the size of the rooms that was defined as a luxury and not building materials.
The materials of the facade reflects the different activities inside the house. The ground floor houses mainly bedrooms, private dwelling and non-representative parts. The facades on this floor are clad with the most swedish of facades - the sawn spruce panelling. This is painted with a mixture of equal parts turpentine, linseed oil and tar - the traditional west coast protective treatment for their wooden landings. This floor has a conventional placement of windows. The upper floor is the representative part of the house clad with a flawless and proper facade material - 5 mm translucent white acrylic plastic or PMMA. The magnificent view is captured with large panoramic windows. A large balcony with a pragmatic steel construction and cheap railing compensates for the lack of outdoor space in connection to the living room.
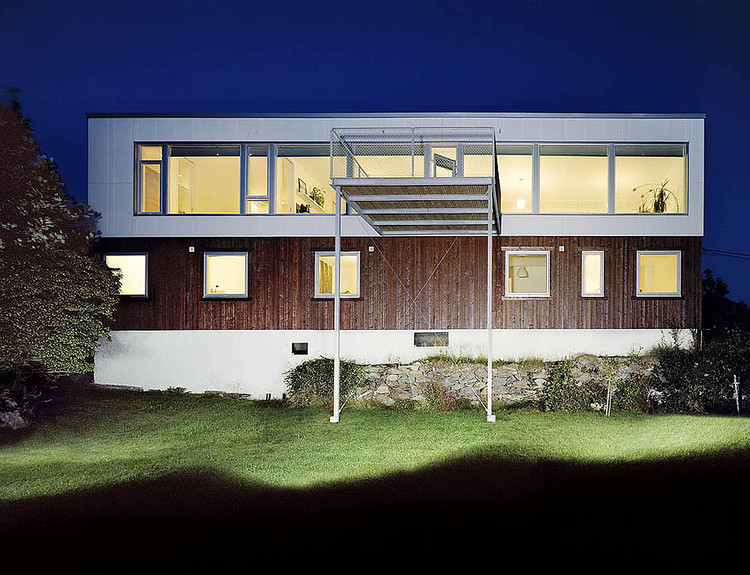
The ground floor has a pragmatic layout built around a transversal corridor with storage as a buffer towards the northeast. On the other side there is a row of rooms. The upper level is inspired by the Moore and Kubly Houses - both designed by Craig Ellwood and built in the 60s - with their free walls only interrupted by sliding doors in closed position.
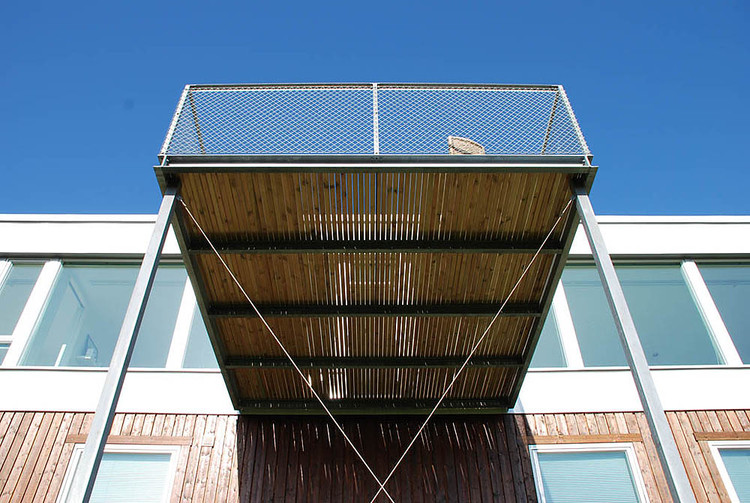
Techno
The facade material for the upper floor consists of 5 mm opaque sheets of acrylic glass. PMMA - polymethylmethacrylate - was developed during the 20’s in Germany and brought to market in 1933 with the brand name Plexiglas. Already during World War II the material was used in a variety of military applications such as periscopes, wind screens, etc.
PMMA has an ignition point of 460˚C and forms carbon dioxide and water during combustion. It has less than half the density of glass and the production requires about two liters of oil to make one kilogram PMMA. The material is UV-stable, making it suitable for outdoor applications.
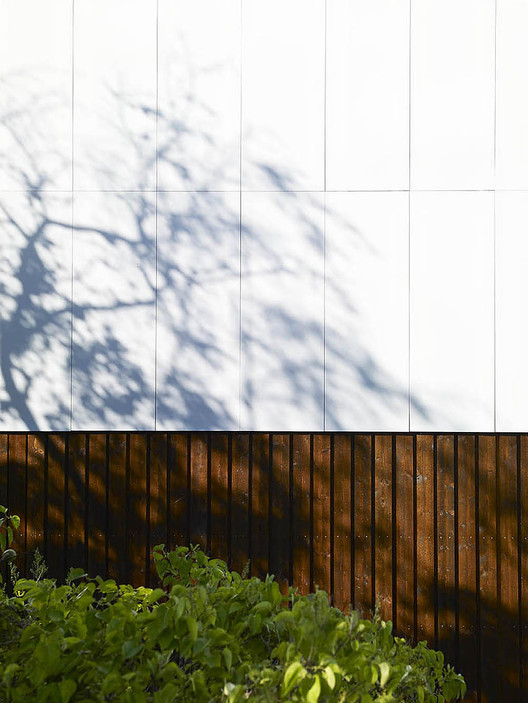
Two factors are important to consider when designing with PMMA. The first is the extreme length extension of this material; in a design temperature range of 100˚C it is estimated to 7 millimeters of expansion per meter. This means that when you can not allow continuous motion you are limited to relatively small sheeting formats. Secondly the plastic is electrostatic and therefore can attract particles and grow dirty.
After examining various attachment methods taking these factors into account, together with 3M we concluded that tape would be the best solution from a technical and aesthetic standpoint. The proposed technique was to attach the sheets with an acrylic foam tape with due dimensions in width, thickness and correct choice of foam. Since there was no prior experience of applying tape on PMMA, 3M conducted tests in a heat chamber to warrant the procedure. Tape thickness must be a third of the calculated thermal expansion; thus a tape of 2 millimeter thickness was selected. The tape was applied to a surface-treated steel batten since a galvanized surface is unstable over time.
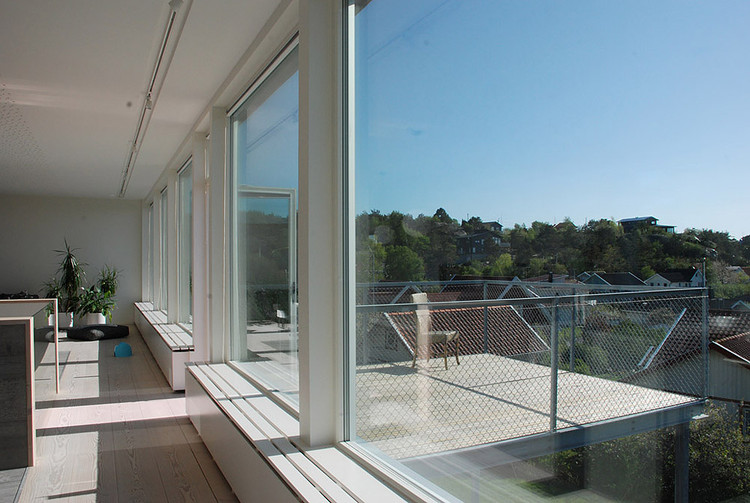
The PMMA sheeting is directly applied to the battens, thus dependent on the ambient temperature being at least 15˚C at the time of application. Due to a historically cold spring the cost was unfortunately too high to keep the scaffolding until the temperature was right. Therefore the sheeting was mounted traditionally with screws on some parts.
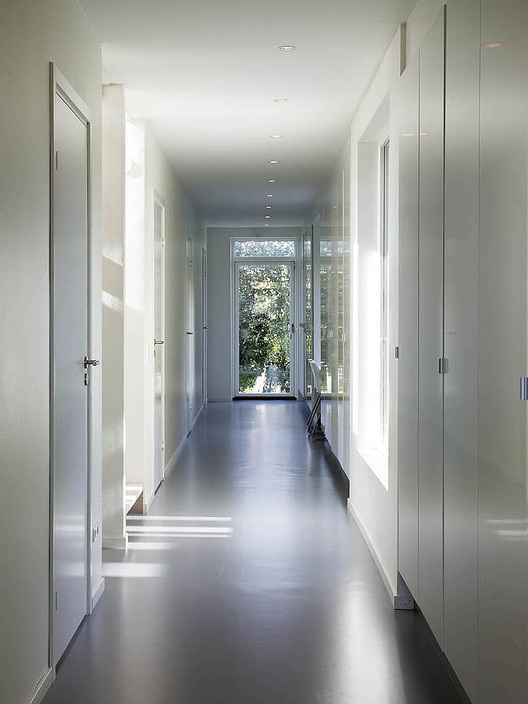