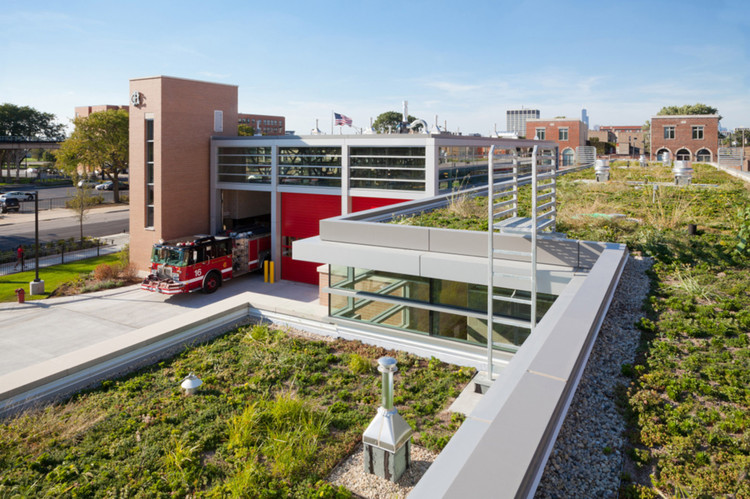
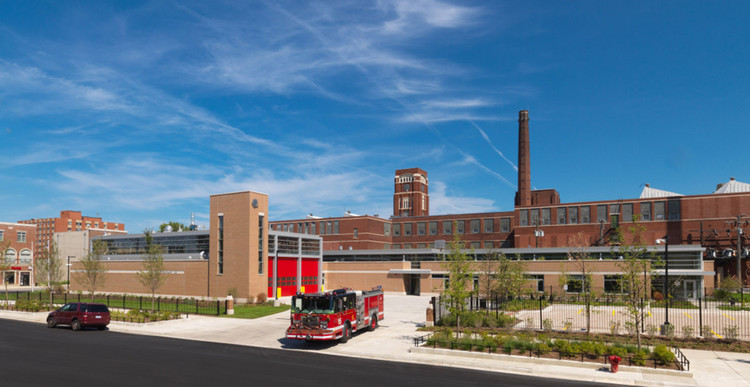
Text description provided by the architects. Design Achievement - Response time to an emergency call can mean the difference between life and death. DLR Group's number one objective for the design of Engine Company 16 was to decrease response times by integrating the latest technology all within a sustainable environment. Using a modern design for living quarters, advanced training options and office workspace for officers, the energy efficient fire house exceeded the City's baseline LEED V2.2 Silver Certification requirements to achieve LEED v3.0 Platinum certification, the first LEED Platinum firehouse in Illinois.
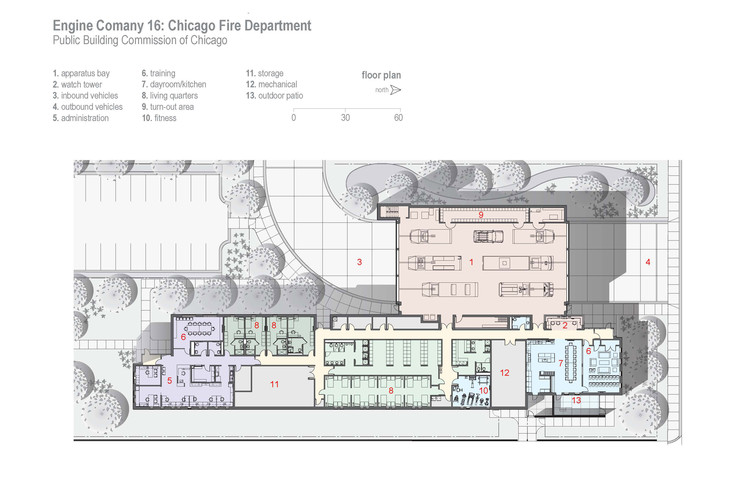
Scope Summary - This new 20,000 SF fire house is constructed on city-owned property and is the first of the Prototype B engine companies. The station includes: a large apparatus bay to house multiple emergency vehicles, full kitchen, locker rooms, toilet facilities, sleeping quarters, officers' quarters, physical training room, meeting room, education room, EMS Field Division South headquarters, haz-mat unit operations with associated storage, a 150 foot communication tower, and parking for approximately 30 vehicles. A clerestory runs the full length of the facility to optimize day lighting. DLR Group provided architecture services for this project.
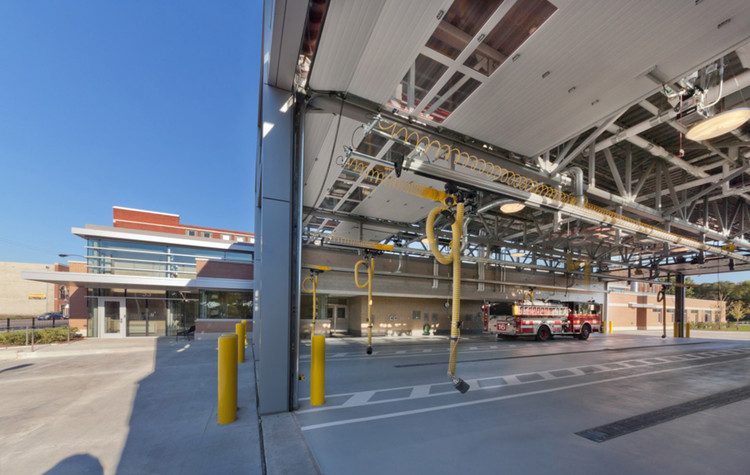
Design rigorously explored strategies for reducing the building's energy use. This new facility achieves a remarkable 52% reduction in energy use compared to baseline, providing operational cost savings in excess of $20,000 annually.
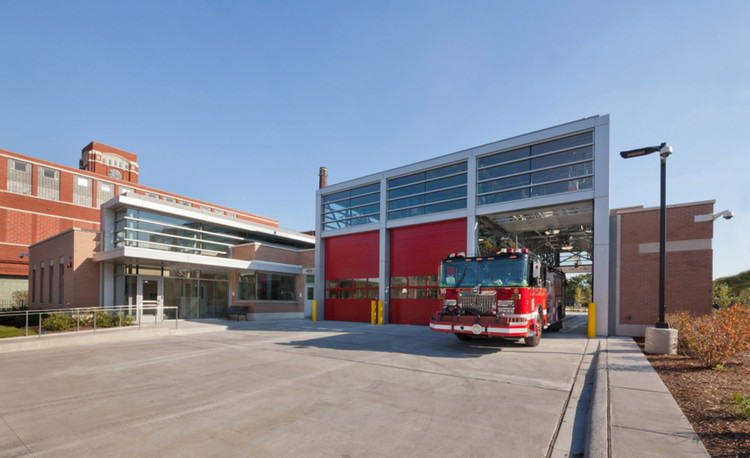
Energy efficiency and sustainability
The station's design evolved from rigorous integrated analysis and a laser focus on energy efficiency. The process began with evaluation of the City's existing fire station prototype, and subsequent redesign of that prototype to reduce its energy use to 41% below a LEED NC 2.2/ASHRAE 90.1-2004 baseline. In then adapting that prototype to the new Engine Company 16 facility, the team employed strategies that further achieved 52% energy reduction over a more stringent LEED NC 2009/ASHRAE 90.1-2007, and annual operational energy cost savings in excess of $20,000. A comprehensive measurement and verification plan validates these operational energy savings, and enables the City to monitor and continually optimize the building's energy performance.
In addition to energy conservation, the design employs diverse sustainable design features that achieved LEED Platinum certification, including:
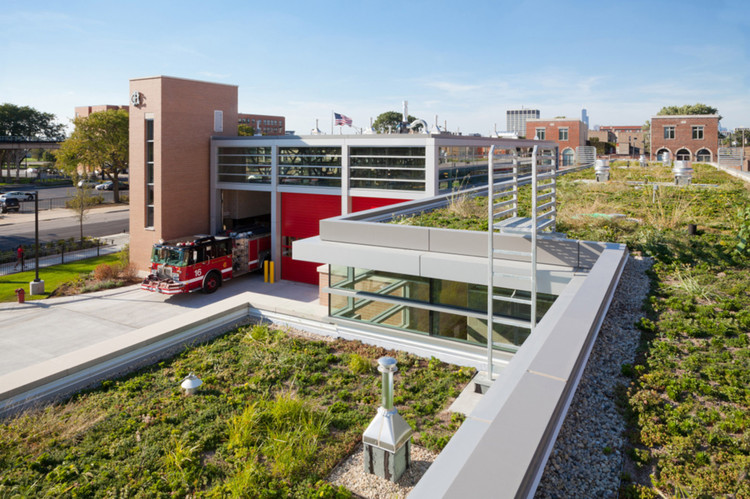
- Geothermal System with water-source heat-pump units
- High Performance Envelope (walls have an assembly R-value of 26 with 3.5” of continuous poly-iso)
- A green roof that reduces storm water runoff
- On-site storm water retention system that repurposes water for washing fire trucks and irrigation
- Permeable paver parking manages storm water on site
- Native and adaptive landscape species
- Low-flow plumbing fixtures
- Lighting sensors for daylight harvesting
- Materials with very high recycled content were used throughout the project
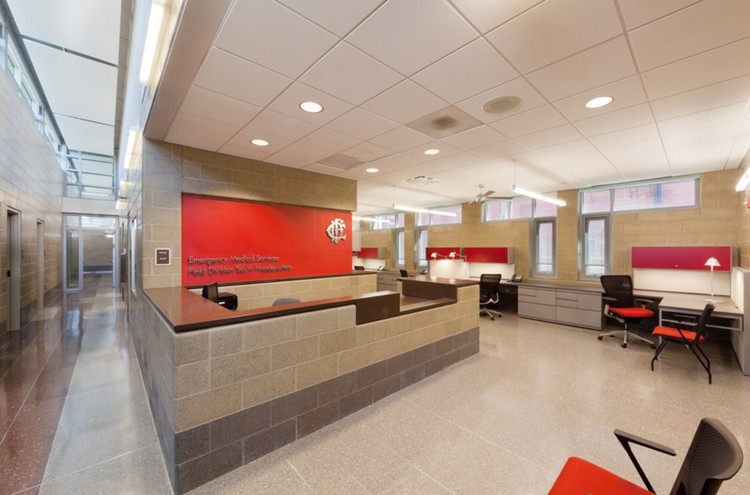