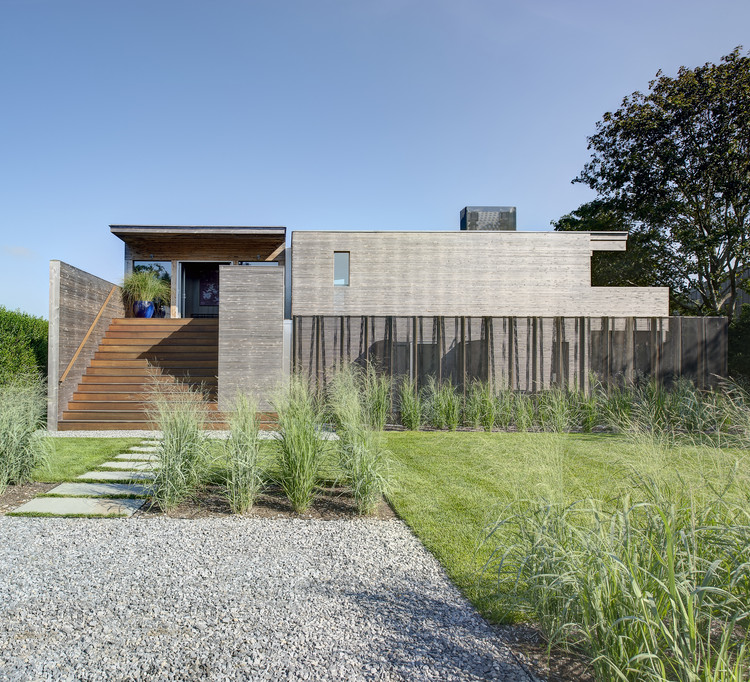
-
Architects: Bates Masi + Architects
- Area: 3100 ft²
-
Manufacturers: Evans + Paul
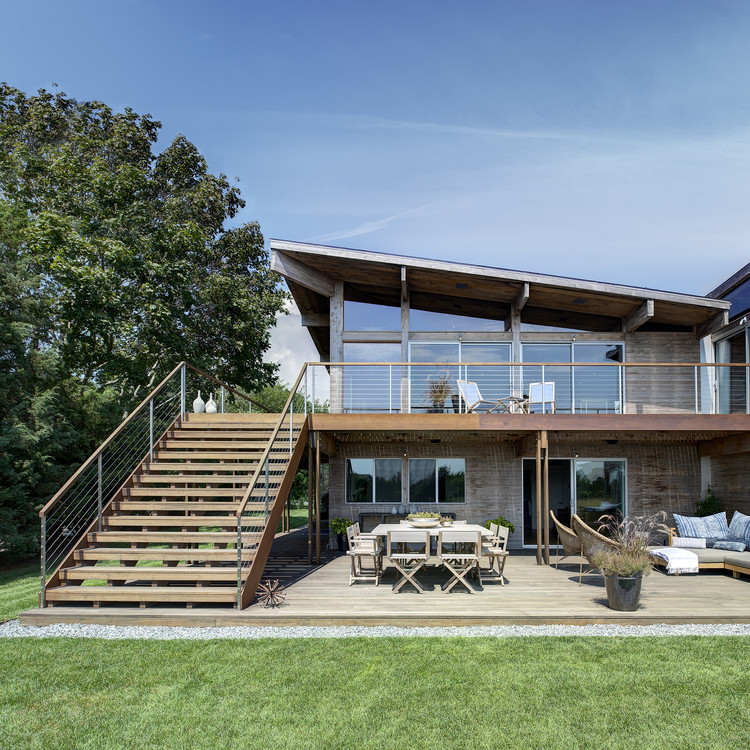
Text description provided by the architects. The waterfront site of an existing 1970’s kit house overlooks layers of wetlands to an estuary, the bay, and the ocean. The client set the parameters of keeping the existing structure while doubling the size of the house with an addition. The existing structure consists of glulam post and beam construction connected with steel plates. One solution could be to mimic the existing architectural language of the post and beam skeletal structure in the addition. Since the existing house clearly expressed the structural system, the addition should also express this. The architect chose to clearly identify the existing system of the house and create a dialogue with a contrasting panelized system in the addition. The new system utilizes prefabricated elements that resolve multiple structural and spatial problems. Examining the strategy of a kit of parts, current material fabrication technologies are utilized to expand on this idea. A different approach to sustainability is explored, minimizing waste by simplifying to the essential components in order to resolve multiple problems, thus eliminating typical construction waste. Using a standard as a precedent and developing a new structural system paired with the latest technologies, a material can accomplish multiple tasks and heighten the experience of inhabiting the space.
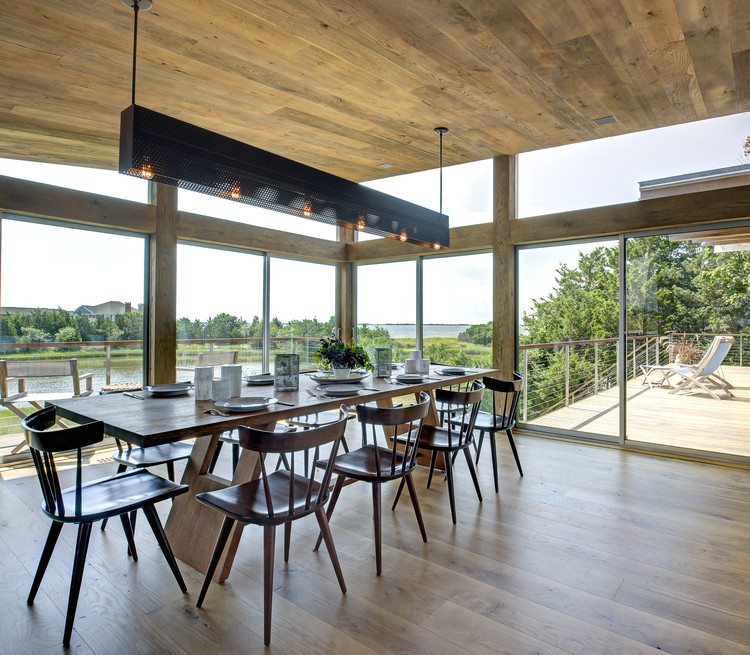
Prefabricated shear wall panels, used in light frame construction in areas that are hurricane prone with high force winds, were studied. Most are made from a light gauge metal folded to add strength and rigidity. For our case the panels were to be exposed and used for more than just a hidden structural component. A standard light gauge 4x8 steel sheet was folded back and forth along the long axis adding the same strength and rigidity to the panel. The resulting 2’ panel locks into adjacent panels and is a structural shear and bearing assembly, as well as a decorative furniture component.
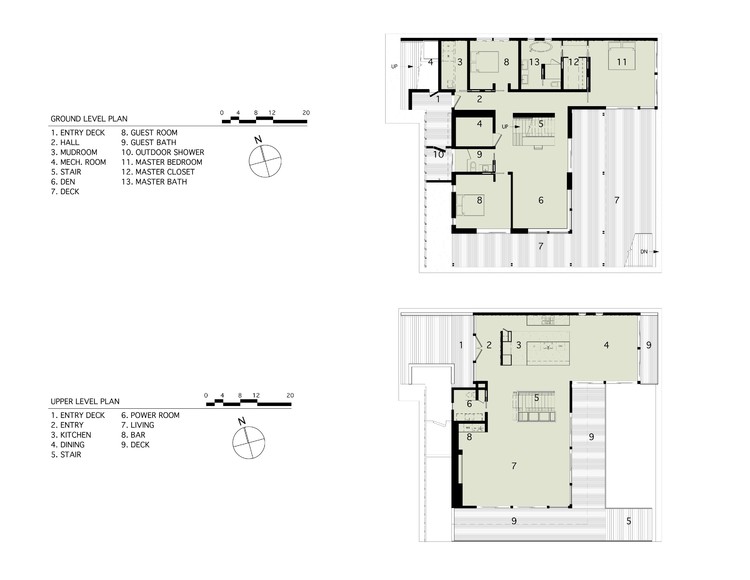
The new structural panels multitask throughout the addition. The solid steel transitions to a perforated panel that baffles the sunlight over windows and doors. The light quality varies throughout the day as light levels transition through the overlapped perforations. Fins that protrude from the wall panels are laser cut to accept shelving, seating and countertops. The same perforated steel becomes the dining room chandelier, and the platform for the stair and desk. This one material is exhausted in its possible uses throughout the house, minimizing the necessity for additional components that require wasteful shipping and packaging. The secondary infill material is used through both structures, on the floors, walls and ceilings to unify the old and the new.
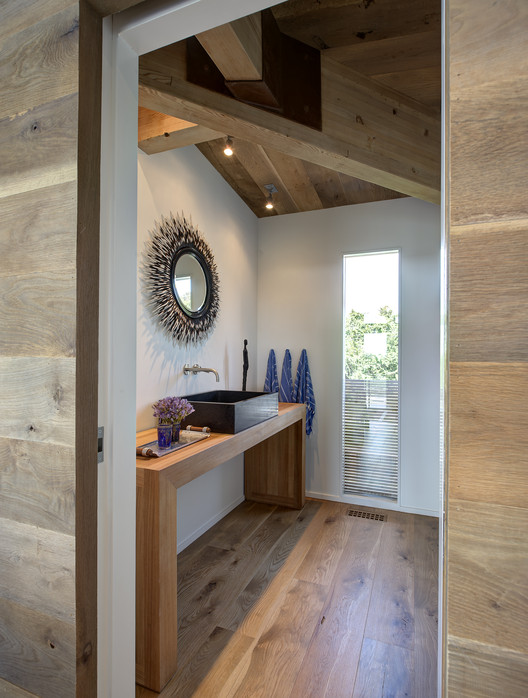
Using new technologies to fabricate customized panels from a standard product accomplishes several things: less material is necessary to achieve greater structural strength, multiple programs can be integrated into one material, waste is minimized resulting in a more effective approach to sustainability, and the dialogue between the existing and new structural systems elevates the experience of inhabiting the space.
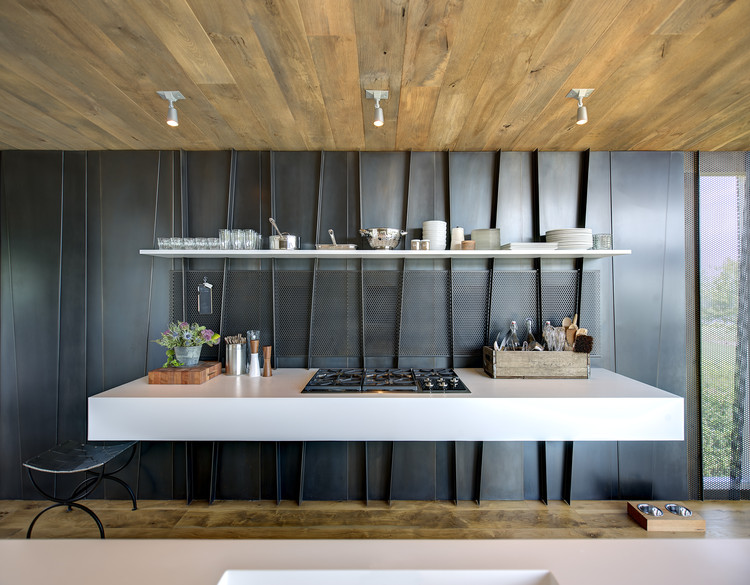