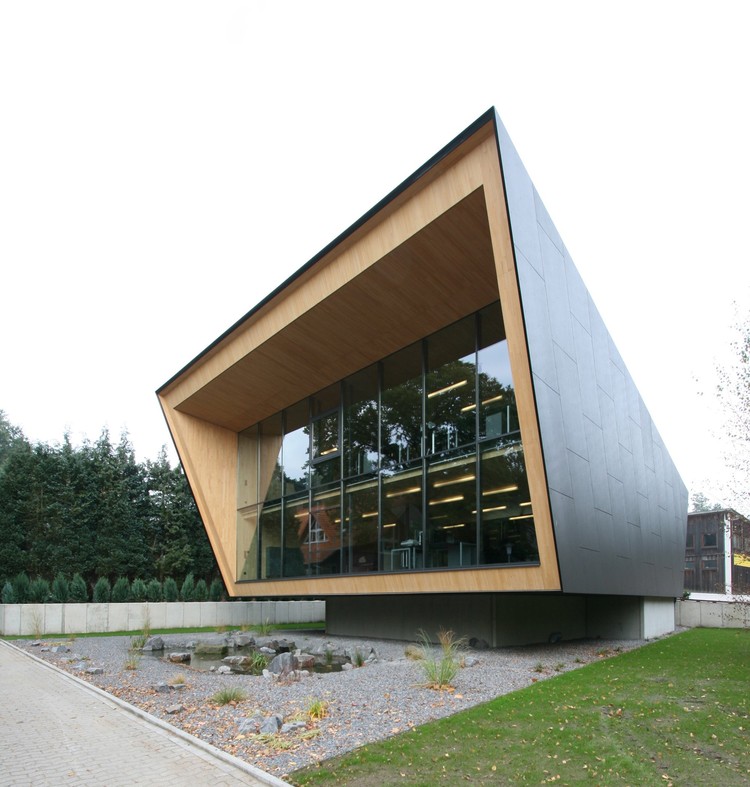
The Headquarters Krogmann in Lohne-Kroge, Germany, by Despang Architekten investigates the numerous characteristics and fundamental opportunities inherent within wood and exhibits a modern approach to the craftsmanship of traditional German vernacular. Designed as a new corporate center of operations for the woodworking company Krogmann, this new office would need to succeed not only in handcrafting a new image for them, but also serve as a catalyst for future growth while showcasing their ability as ‘makers’ in the field of construction. Having worked as the builders for several projects for Despang Architekten, their choice to retain them as the design architects for their own project was a natural extension of an already solid relationship built upon the dedication to quality and progressiveness. As an extension of this article, we also had the opportunity to speak with Principal and University of Hawaii Associate Professor Martin Despang about the process involved in the making of this project.
More details and our Q&A with Martin after the break.
Preliminary site analysis determined that positioning the new structure on the southeastern corner of the plot of land would provide benefits both from an environmental control system standpoint – passive solar gain – and that of a metaphysical nature by means of a symbiotic relationship – through transparent public south face overlooking the village. The site features a north-south sloping gradient, providing an added benefit that contributes to the programming and function of the form. The low-slung north face incorporates the main entrance accessed by means of a catwalk bridge, whilst simultaneously functioning as a wind scoop which thermodynamically dissipates the harsh winter winds. The trapezoidal shape rises up to its apex on the south side, opening up to reveal a fully glazed south elevation – which allows for unimpeded daylighting, passive solar gain during the winter months, and expansive panoramic views.
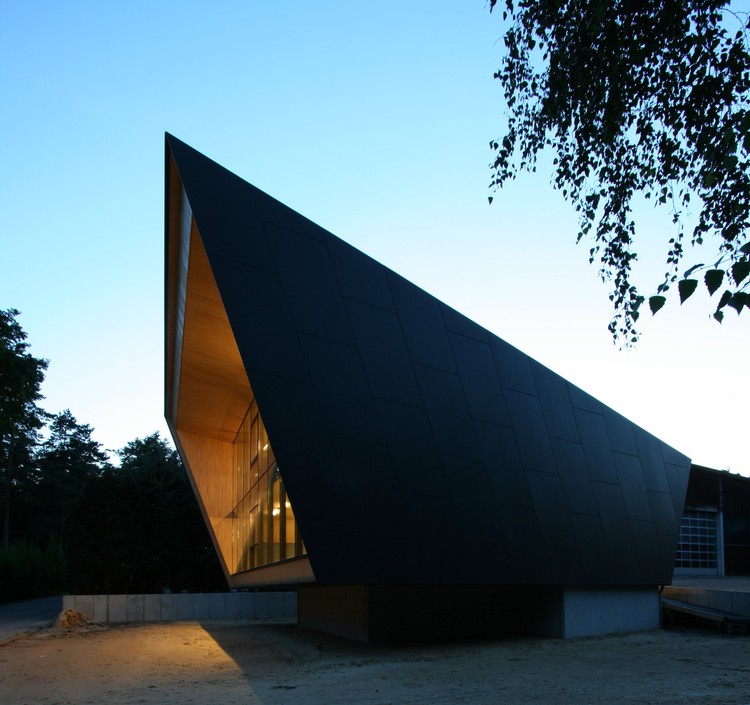
When it comes to the internal programming of the building, careful attention was given to the ability to maintain an open concept that promotes internal communication and a non-hierarchical environment. Despang Architekten looked to the construction and materiality of musical instruments such as the violin and acoustic guitar for inspiration. This resulted in the unparallel surfaces that define the overall trapezoidal shape and the implementation of timber material as the primary finish. Further optimizing the acoustical performance is the addition of acoustical attenuation insulation behind the solid white fir panels – which as an added benefit increases the thermal mass storage of the wall assembly.
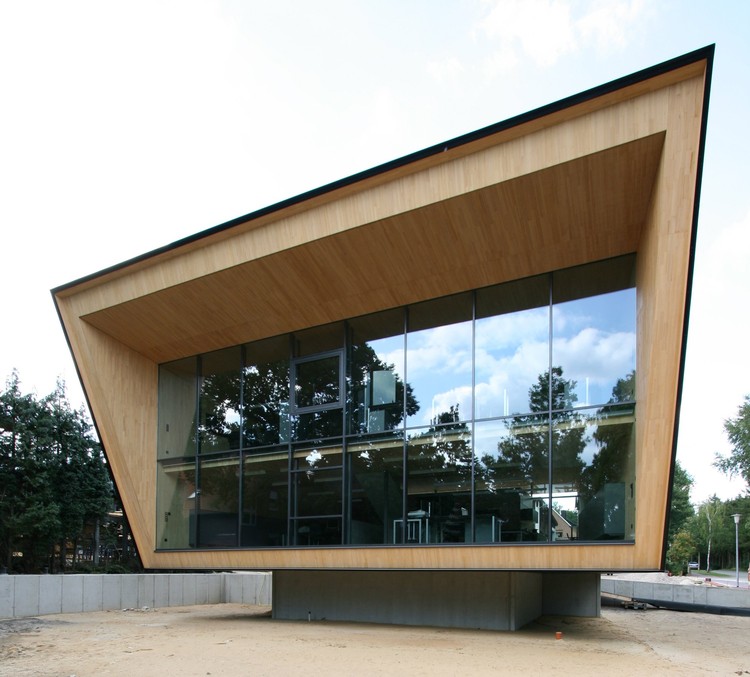
Workstations located at the southern portion of the main floor and mezzanine take advantage of the southern views and abundant daylighting. Utilitarian functions such as restrooms and reproduction rooms are housed in the northern backside of the building cleverly sheathed in rich wooden boxes that contrast the light colored white fir. A sandwich insulated concrete plinth comprises the main floor which encloses the archive room below.
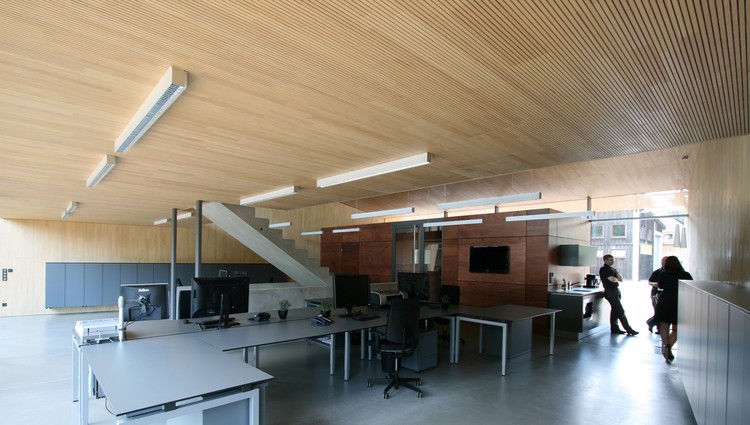
One of the many ingenious details that serve to accentuate the crispness of the wood is the seamless transition from interior to exterior, which terminate at knife edge connections to the exterior cladding. In order to maintain the sharp edges of the exterior and still manage water runoff, a hidden gutter detail ensures that design integrity is maintained while still effectively directing water off the roof.
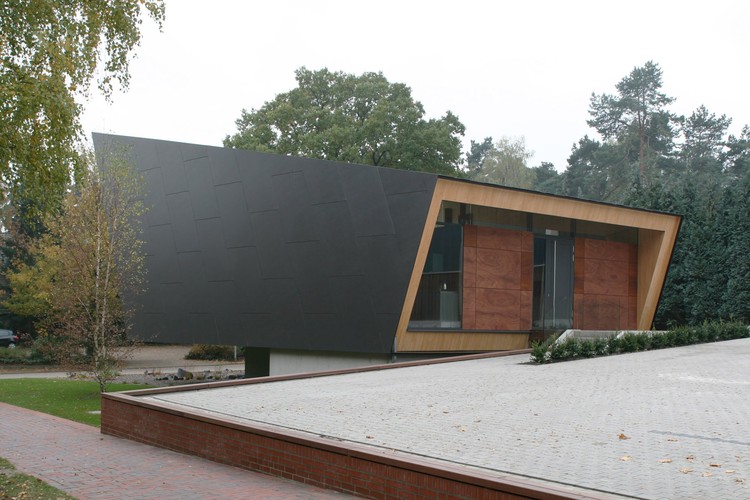
Another detail that warrants expansion is the hidden top and bottom mullion detail, which has the effect of de-materializing the glazing system. This was achieved by recessing the mullions into pockets above and below the elevation of their respective ceiling and floor, and carrying the finishing materials to abutment of the glazing.
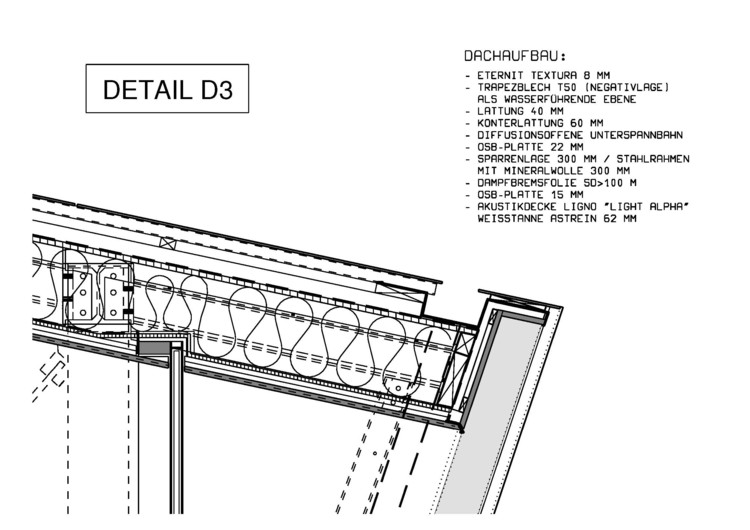
When it comes to the signature black cladding of the exterior, a fiber cement board – Eternit – was utilized as a rainscreen system on all 6 sides. On the roof, the Eternit is secured to metal decking oriented to direct water to the hidden gutter on the north end. This also ensures that there is adequate airflow underneath the panels during heavy rainfall – which is integral to maintaining the integrity of the Eternit.
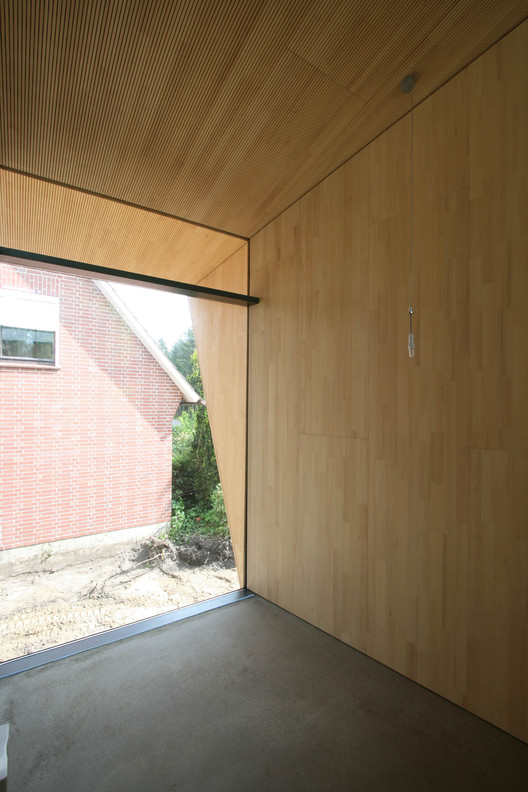
In between the interior and exterior cladding lies the success of this building’s low dependence on grid supplied resources. The strategic use of mineral wool insulation combined with rigid insulation where required make up an uninterrupted thermal barrier. These increased levels of continuous insulation coupled with a calculated building orientation that takes advantage of solar gain are critical elements in Germany’s drive towards Net-Zero construction.
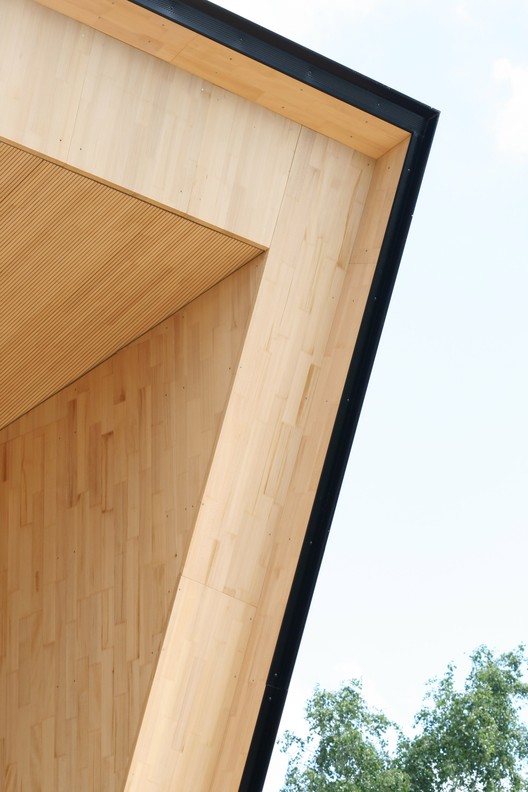
Employing only a simple material palette of wood, concrete, and glass the Headquarters Krogmann takes a refined approach to the construction of high performance buildings with attention to detail through the celebration of its primary materiality.
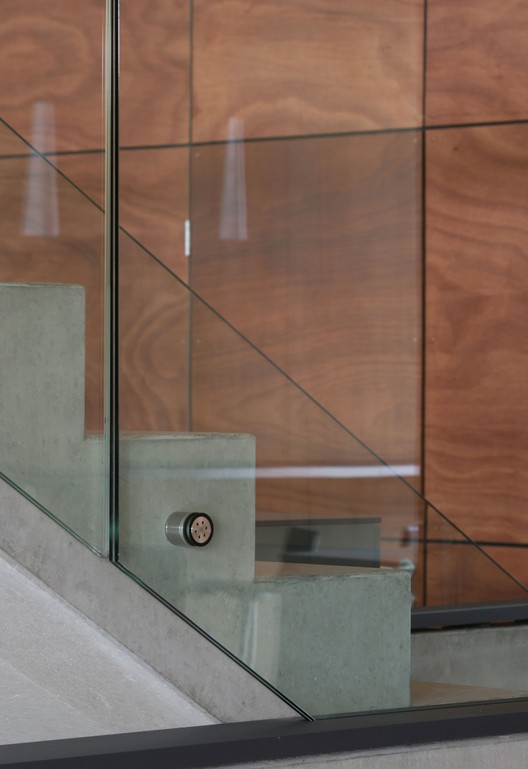
Read on as we discuss with Principal Martin Despang some of the hurdles that were encountered during construction:
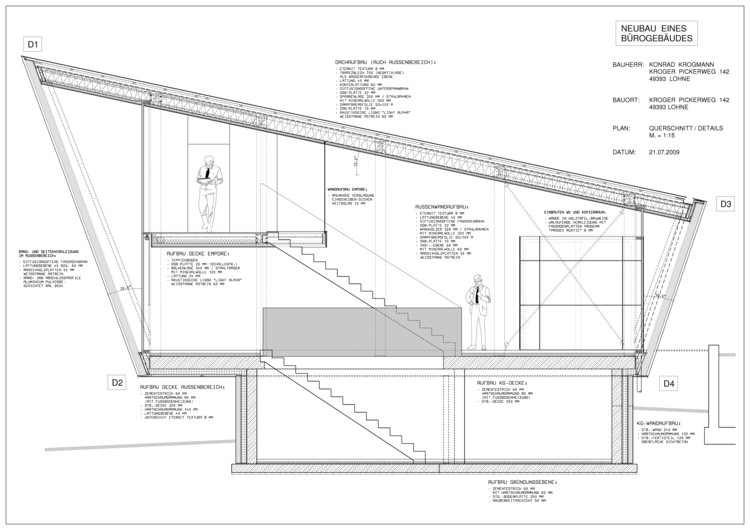
AD – The neighborhood of Kroge is comprised almost entirely of traditional brick residential houses with pitched roof construction. I understand that there was some resistance from the community initially. How did an amicable resolution come about?
MD – Yes, the permitting authorities were initially shocked and called the project an unacceptable alien which does not fit into the existing small town of pitched roof brick buildings. We approached the issue through communication with the local community and showed how the nature and tradition of the small town is not about the brick buildings, but them as an expression of innovation over time. The vernacular way of building in the last century was mainly of half-timbered wood construction with sod brick infill which transitioned to traditional clay brick and fiber cement tiles and shingles for the roofs in the 1950´s to 1960´s. The architectural evolution of the town had not quite progressed the same way ever since, we proposed to jump restart the tradition of innovation. This is what makes the Krogmann Headquarters look so provocative, though in essence it is the continuation of the steady radical evolution of a small town from agrarian to industrial as exemplified by the Krogmann company – a modern cosmopolitan firm in the communicational era.
When it comes to the topic of context, the clients allowed us to define this through a progressive lens that embraces the paradigm a post – fossil 21st century. Since the building is virtually self-sufficient with little reliance on third party energy sources, as prices for heating fuels increase, the expression of the building begins to make even more sense as a catalyst for progressive construction and living. The form of the building is not a provocative gesture, but an expression of the continuation of the tradition of innovation into the 21st century in the small community of Kroge.
AD - The German legislation and initiatives towards net-zero dependency have been quite visible in the past years. How has this played into the design and your philosophy for future architecture?
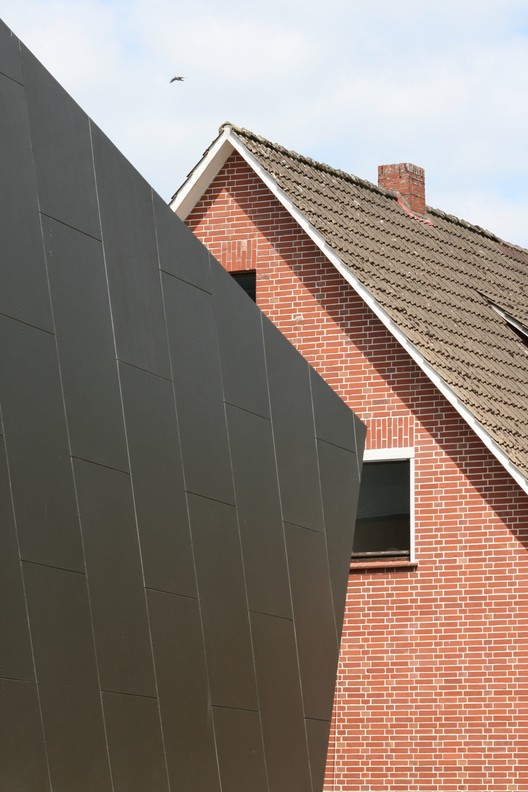
MD – A net – zero building does not necessarily have to have anything to do with architecture. The resulting conflict makes Ludwig Wittgenstein´s differentiating definition of ” architecture being like a gesture and unlike every movement of the human body being a gesture, not every building being architecture” even more timely as when he said it about a century ago.
A ” Passiv Haus” – conceived in Germany – sets forth the most rigorous energy efficiency standards. These standards are typically achieved via construction of a box, insulated with petroleum based Styrofoam, few south openings filled with triple pane glazed plastic windows, and topped with PV panels powering the needed energy. The “PHPP – Passive house Projecting Package” software used is quite sophisticated but the results are often lacking aesthetically.
After our own experience with PHPP design, the Krogmann Headquarters’ intent is to seek out an alternative utilizing the Passive House principles as a guiding tool – orientation, insulation, air tightness and heat recovery. This is then coupled with the client’s and our own related experience, expertise and instinct of master builder and architect in close collaboration.
Designing energy and architecturally efficient and sufficient buildings is the exciting challenge for the emerging post-fossil 21st century architects, which we as educators have the privilege to be part of their motivation, inspiration and maturation.
AD - Having worked closely with the Krogmann company in the past and their expertise in the ‘making’ of buildings, what kind of impact did that have on the execution of the project?
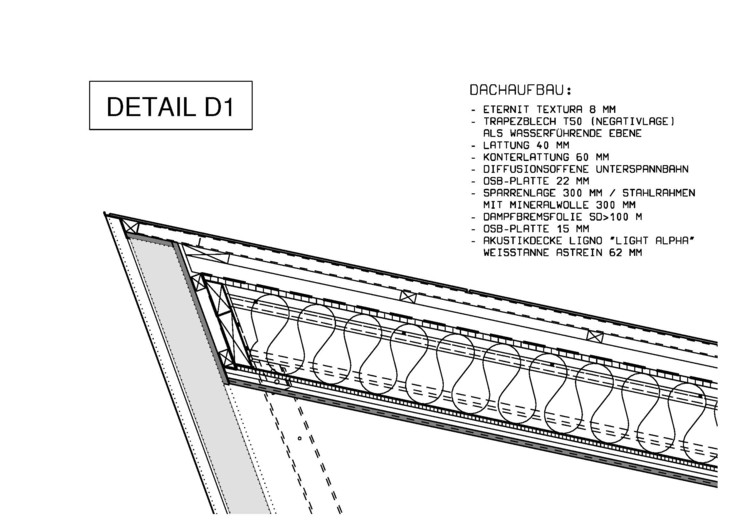
MD – Buildings at their best were always a result of the direct connection of the brain and the hand, the thinking and the making. When Heike and Konrad (clients) came to ask us we thought they had picked the wrong phone number as the previously created together technologically and typologically pioneering solid wood ILAMSI school was wearing the hardest on both of us, which looking back seemed to instead of having separated us bonded us together.
When Konrad (client) said he wanted to be involved in the Contract Documents part, we grinned and said yes we have heard that many times before from the client’s side wanting to save money (at the wrong place). He came to the first meeting with his one to one scale and pencil drawn details to be implemented into his fully CAM manufacturing process and him saying that he learned to think that way architecturally through the ILMASI collaboration (a previous project). Our initial grin turned into the happiest satisfied smile of having gotten as close as possible back to the old collaborative master builders virtue. For us, there is no difference anymore between the “builder” and the “thinker” as both are the other and vice versa in every moment and stage of the project from the first napkin sketch on.
AD – You employ the Eternit panel in a somewhat unconventional method – for roofing – on this building, and it is typically utilized as a wall cladding only. How did you ensure that the product could perform effectively in this atypical position on the roof?

MD – This is a great example on the topic of the rebirth of collaborative master-builder-ship, the call for “Eternit” came from Konrad who wanted his building to be a materialized expression of his business, and he makes almost as much revenue with installing Eternit than with wood. The thinness of the material seemed an ideal materialization in relation to the described Semper methodology of ” earthwork, framework and enclosure” so as to articulate the latter in the thinnest and most effective way as a screen to keep the main elements of rain, sun, and wind away.
The thermodynamic generation of the building form created the roof as the 5th façade. Eternit confronted this unconventional application of their material via a warning to the client about him loosing the warranty for a wall cladding only material. Typically this would have made client shy away from experimentation. However, Konrad become hands on and made a full scale mockup at the time the building was in the pre-schematic design phase, and had it weather tested on the site until construction began. With the positive test results he would not need the ‘extended’ warranty as the onsite testing proved the versatility of the boards. To top it off, Eternit has adopted it as one of their flagship projects as well.
The concluding lesson is that nothing is impossible unless one has tried as the nature of innovation requires experimentation. The custom trapezoidal cut sheets are the Darwinist progression of the 1960´s Eternit shingles.
AD - As an architect who works closely with the wood industry, how have the advancements in wood technology impacted or influenced the work that Despang Architekten create, notably in this project?
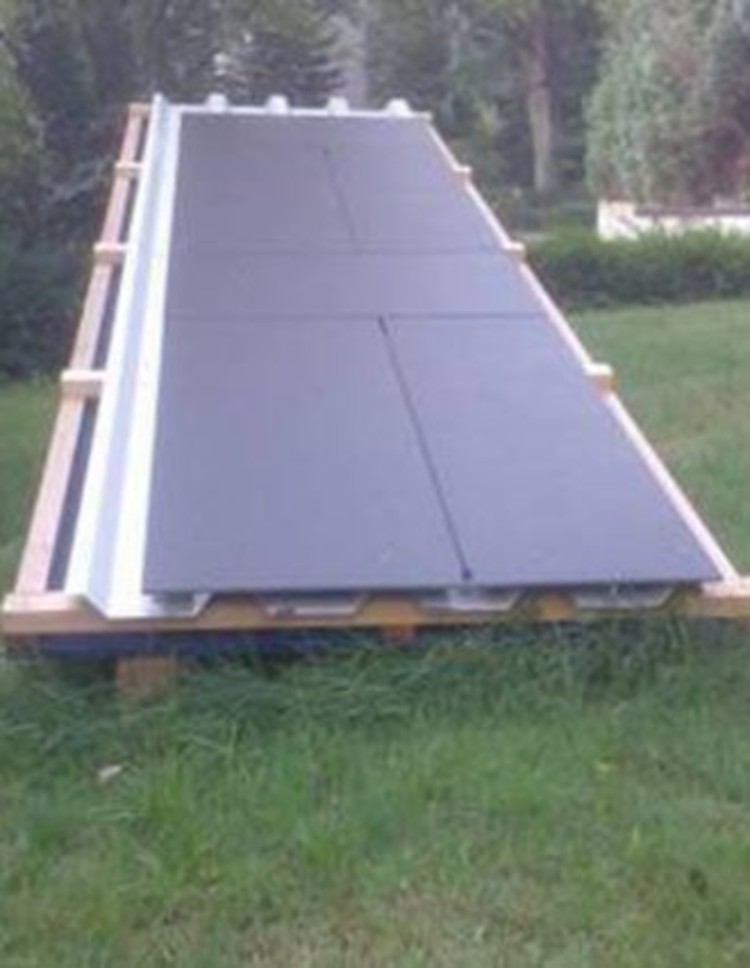
MD – Whereas the collaborative ILMASI School (with Krogmann) was an experimental investigation in solid wood and thermally modified timber technologies of that educational typology, the Krogmann headquarters by the nature of the work / mercantile type looked at and used wood as an inside -out branding with substantial qualities of indoor air and atmosphere performance. We have worked and continue to work with many materials mostly in a stereotomic , mono-materialized way. We find ourselves revisiting quite often our favorite “wood” in interpreting and defining it differently every time.
In the Krogmann Headquarters we have collaborated with Ligno, who is a great innovator in architectural wood systems and technologies. In this project the wood panel is sliced and on its back side stuffed with batt insulation which adds perfection in plan and section through the trapezoidal shape already in the building geometry laid out for acoustical comfort. This is essential for a wide open work space.
Extending the wood research into the profession and classroom by working with students on wood related critical thinking and workshops and lectures with WoodWorks in the US are an important invigorating inspiration for my own critical practice research work and vice versa.
AD - In terms of environmental control systems and the reduction of dependence on grid energy to power the needs of this Headquarters Krogmann, what kind of success has been achieved by implementing passive strategies?
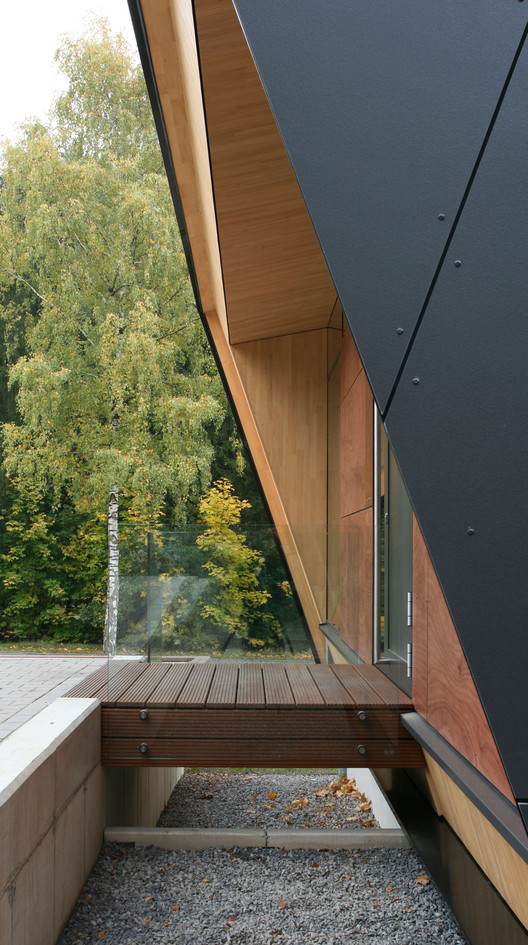
MD – The ultimate success is the happiness and healthiness of the Krogmann team, which was formerly physically disconnected in boxy rooms in their former brick house. The wide open democratic, collaborative, and social work environment in their new work space has made them have more fun, be more motivated, and reduced sick days in their new building. This is way more important than the building being net-zero. PV´s for computers and lights at night are on the roof of the existing manufacturing building adjacent to the new headquarters. As far as the high off the grid performance of the building, the project tries to do this as unpretentious as possible, in not trying to control and not trying to be a system , but rather a more friendly organism hosting its inhabitants.
AD - When it comes to the collaborative effort of your firm and the Krogmann’s, what kind of advice would you offer young architects in terms of the importance of this method of cross collaboration and project delivery?
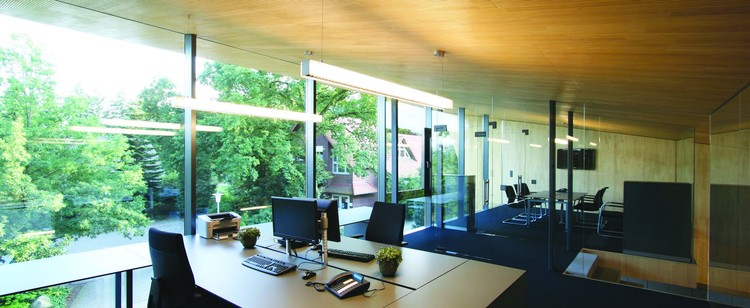
MD – My advice to the young emerging professional would be just that: rather than joining the hectic and exhausting interstate of buzz wordiness – sustainability – which in its current form has become dangerously inflationary as a term, is to follow what they know from other more personal parts in their lives like their partnerships and where IDP / Integrated Project Delivery has worked the best way in being there for each other, open to each other, and talk with each other about everything , to apply that self learned lesson to their profession.
Architect: Despang Architekten Location: Lohne, Germany Project Year: 2009 Photographs: Olaf Baumann