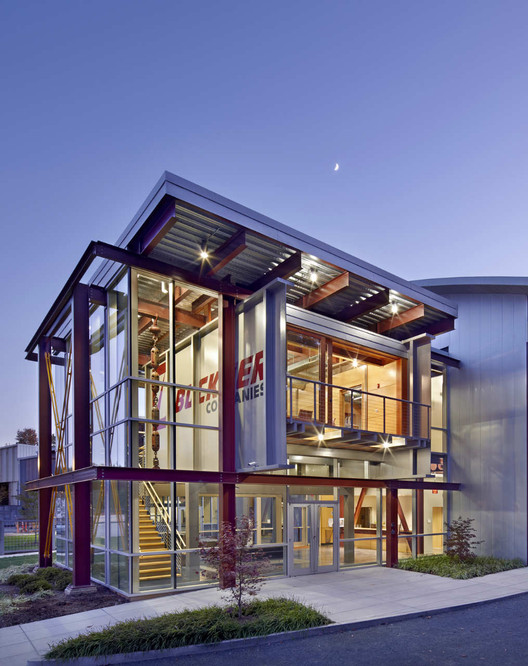
-
Architects: Weinstein Friedlein Architects
- Year: 2010
-
Photographs:James West
Text description provided by the architects. The new headquarters for a nationwide crane leasing and steel erection business was a long-contemplated update to a venerable, family-run enterprise. Business was good and growing, but existing space was cramped and poorly arranged, and increasing competition demanded better teamwork. The owners turned need into opportunity. The Buckner Companies’ headquarters in central North Carolina is a showplace for the steel erector’s trade, a study in material salvage and reuse, and a model collaborative work environment.
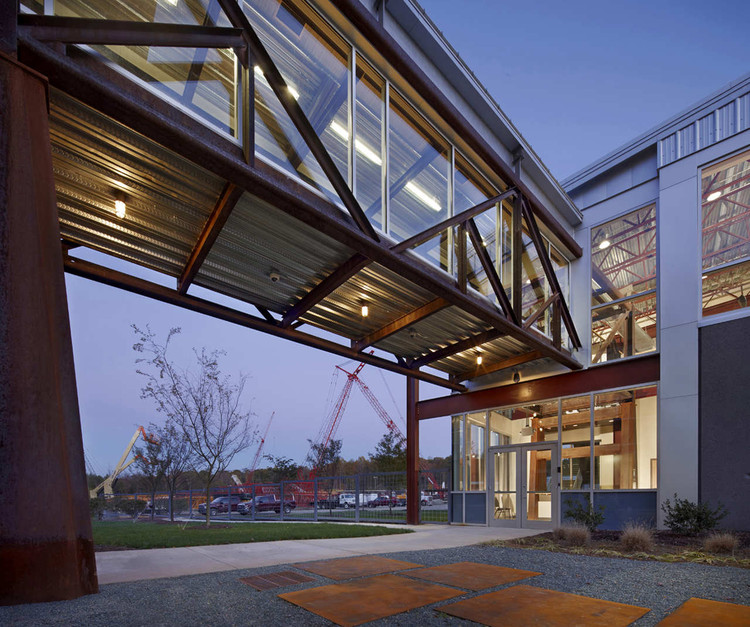
The new building took form around the notion of surrounding a double height space with the offices of project managers and administrative staff, creating vertical, visual connection. The project added 15,000 square feet to Buckner’s existing office building, which was extensively refurbished to make a cafe, exercise area and other community spaces. These shared places, and a second-level enclosed pedestrian bridge linking the new building with the old, are a key to making all employees feel a connection to the new construction.
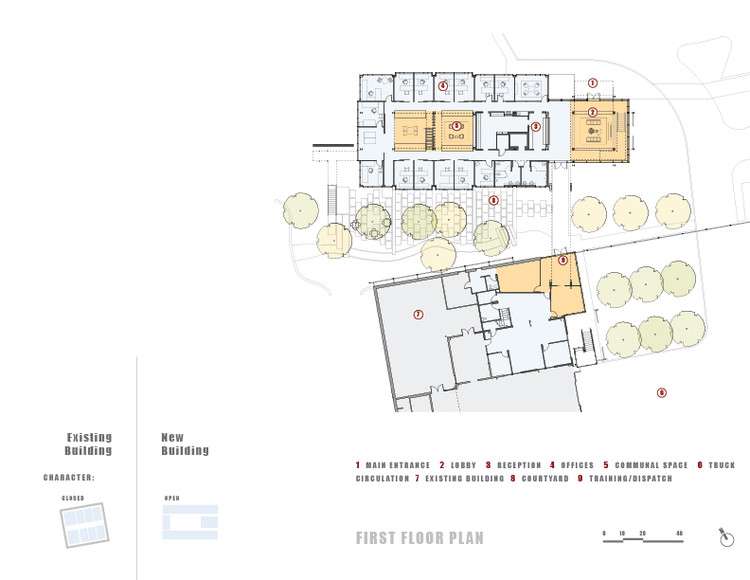
Material choices followed an owner-driven desire to make a place that spoke of the company’s line of work. The site included a crane-rigging yard piled with building parts rescued from various construction sites over the decades. Designers combed the “boneyard” for beams, columns, girders, braces, decking and even old crane parts that could be designed into the project. In the end, 83 tons of steel pieces – more than 40% of all the steel in the building – came directly off Buckner’s yard. The completed project includes reconditioned columns and girders in its exposed steel frame, reused corrugated metal deck to support roofs and floors, and salvaged curved wood glue-laminated roof beams, which were overlapped to create a south-facing clerestory. Even a 15-ton pedestrian bridge is recycled, picked up and moved from a college campus where Buckner first put it in place 30 years before. Two pieces of 15-foot tall former coliseum roof girders make the walls of a new conference room, which cantilever’s out the front of the building and shelters the main entrance and provides signage for the headquarters.
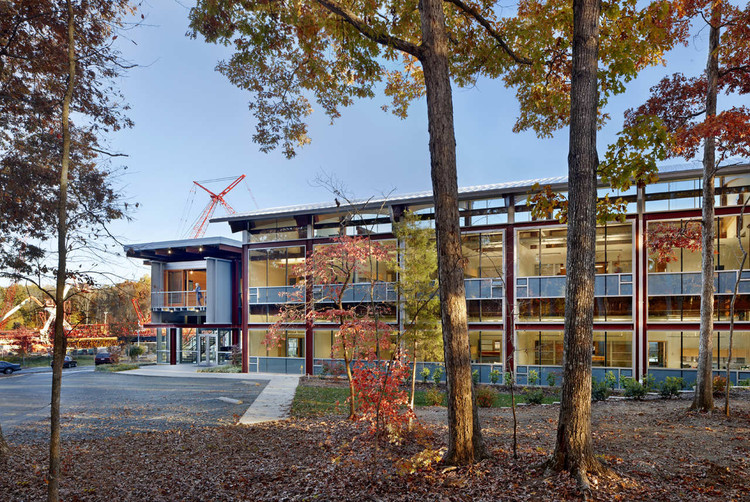
Fueled by the realized possibilities for reusing existing materials, the owner’s challenge grew to embrace an all-points sustainable project. Green building practices incorporated include a chip-and-tar drive, storm water bioretention pond, new materials with high recycled content such as galvalume roofing and linoleum floor covering, and water conservation measures including low-flow toilet fixtures and roof drains supplying a 15,000-gallon cistern for vehicle washing.
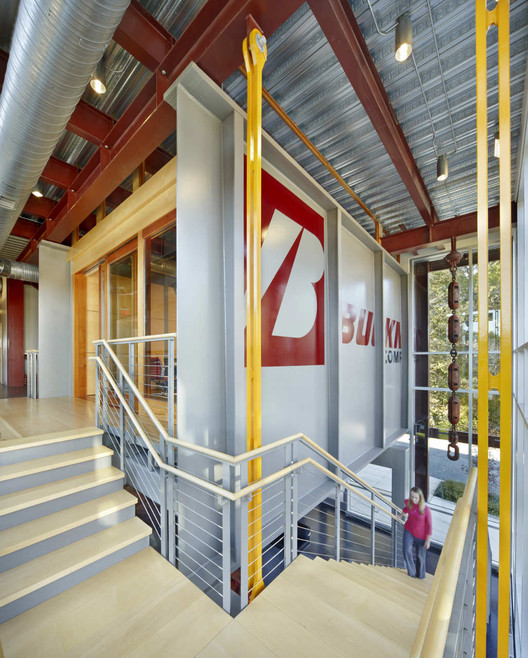