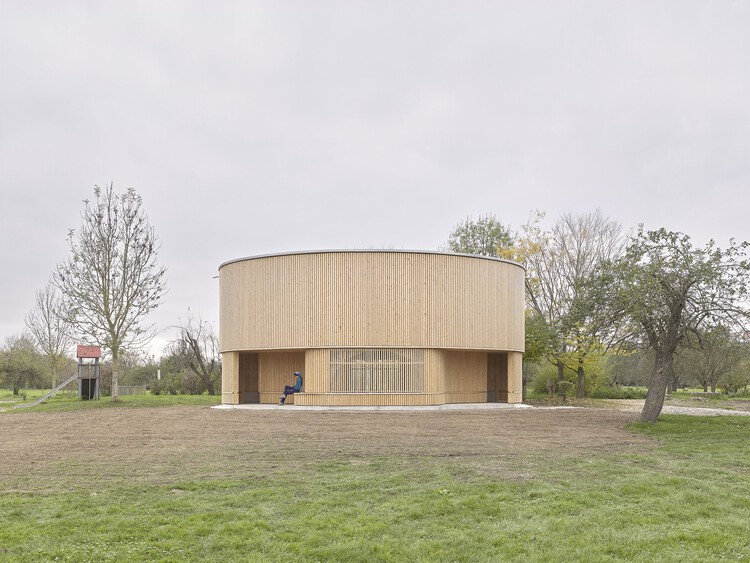
-
Architects: HFT Stuttgart
- Year: 2024
-
Photographs:Achim Birnbaum, Andreas Kretzer
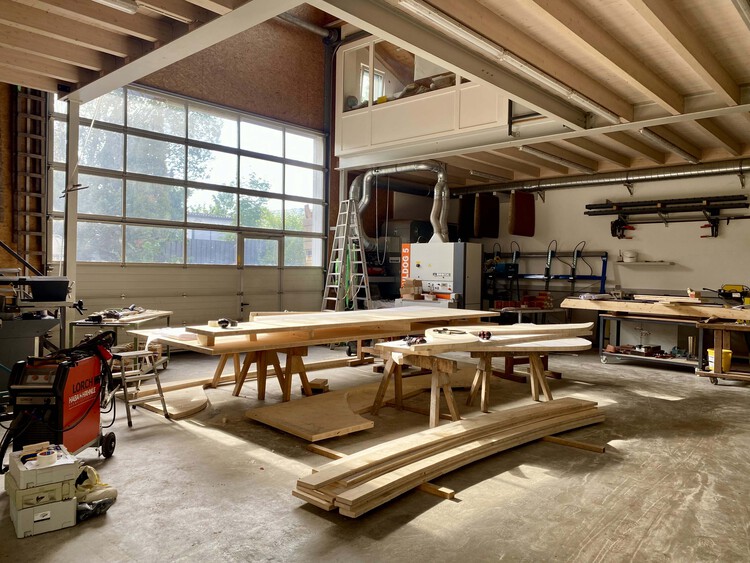
Text description provided by the architects. For the construction site of the new main railway station in Stuttgart (Stuttgart-Ulm / Stuttgart 21 railroad project), geometrically complex concrete formwork made of cross laminated timber was used to create the goblet supports, skylights and arches of the railroad tunnels and edge connections. Once the station has been concreted, the formwork is no longer used, but disposed of as hazardous waste. This end-of-life scenario does not do justice either to the high quality and performance of the material or to the special geometric features of the formwork elements. Therefore, the Stuttgart 210 research project (www.stuttgart210.de) is investigating ways of preserving the material of the formwork elements and enabling them to be reused in the sense of upcycling by turning the building materials into the primary construction of new buildings. A key component of the project is research into all relevant parameters for building with reuse components in living labs. In addition to the theoretical investigation, the research results will be subjected to a practical test in four pilot projects - the living labs in Ingersheim, Marbach, Stuttgart and Mannheim. The experience gained there will in turn be incorporated into the research project. "Living labs as test spaces for innovation and regulation make it possible to test innovative technologies, products, services or approaches under real conditions that are only partially compatible with the existing legal and regulatory framework. The results of such experimental spaces, which are often limited in time and space, provide the basis for the evidence-based further development of the legal framework. Experimental clauses are often the legal basis."
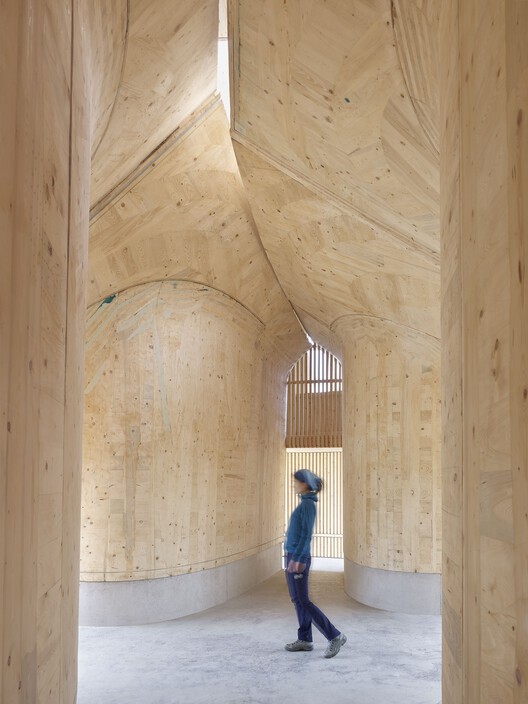
Living Lab in Ingersheim - The living lab Ingersheim is the first pilot project to be implemented and will function as a youth hangout by the river Neckar. The municipality of Ingersheim, north of Stuttgart, had applied to implement a design in 2023 that consisted of two particularly geometrically complex formwork elements. Unfortunately, however, these two parts were lost on the construction site of Stuttgart's main railway station. The search for an alternative design therefore resorted to elements that were initially deemed unsuitable: very large and difficult to transport formwork for the pedestrian tunnel at the southern end of the station. Although a particularly sculptural interior could be formed with these elements, it seemed hard to create a geometrically sensible building envelope with their geometry. The design therefore envisages a building envelope made of solid structural timber, board formwork and threelayer panels, which is placed on top of the formwork elements and forms an autonomous, elliptical shape on the outside. On the one hand, this rendered it possible to create roof and façade surfaces that protect the formwork elements from the weather with relative geometric simplicity. On the other hand, this shell, which conceals the formwork elements from the outside, is part of the architectural staging: The spectacular geometry of the formwork and its fascinating wooden surfaces reveal themselves to visitors only upon entering the building. International Workshop - What is special about this project, however, is the construction process, in which mayor Simone Lehnert succeeded in generating broad support in the community and deploying many volunteers. Various craft firms got involved - some of them on a voluntary basis. In addition, the oval shell made of spruce boards and battens was prefabricated and assembled by more than forty Turkish, Indian and German students on the Master's degree course in Interior Design at Stuttgart University of Applied Sciences in a twoweek workshop. The group of students also fine-tuned the surfaces of the formwork elements and the benches, worked out fitting pieces for gaps and added missing parts. The municipality, the local German Red Cross association, the Ingersheim sports clubs and local volunteers supported the accommodation and catering for the workshop participants. The "hump day" with two guest lectures was organized by the Häfele company in the Blackbox at Römerkastell Stuttgart. The Würth company made a significant contribution to the success of the project by generously donating the screws and safety equipment required for the timber construction.
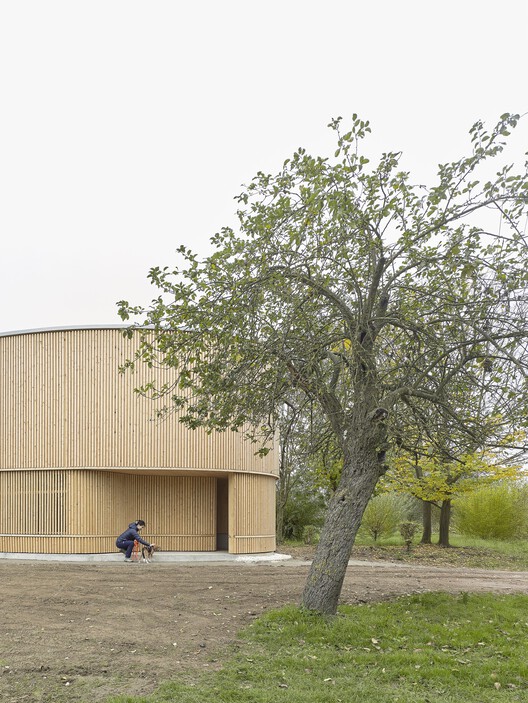
Functionality - The use of the formwork from the Stuttgart railroad station turned the planning process upside down: usually the function and spatial program are determined by the client first and then the implementation via design and construction determines the materiality of a building. However, in this research project the starting point of the designs was always the reuse of very special formwork elements. The most sensible designs possible were developed from the geometric diversity of all the elements. These designs were first checked for the availability and transportability of the underlying elements. Only when the technical and logistical feasibility was clear, potential clients were contacted via various networks and offered the designs and formwork elements for implementation. The municipality of Ingersheim had previously identified the need for a youth hangout in a public survey. This relatively open usage description left enough room for interpretation to appropriate the design for this purpose. The composition of the 12 formwork elements forms an interior space with two narrow entrances to the east and west and a widening, cross-shaped floor plan. The generous ceiling height and pointed vaulted ceiling give it a sacred appearance. This area receives daylight via large windows to the north and south and an indirect skylight. The additional measures in the building envelope provide weather protection for the structure and interior and also form five seating niches with elegantly curved wooden benches - three on the outside and two on the inside. The entrances are concealed behind the battens of the shell, so that no direct view of the interior is possible from the outside. The movement is indirect, labyrinthine and creates an intimate atmosphere. Load-Bearing Structure - The formwork elements stand on a floor slab and base walls made of reinforced concrete. A light and reversible foundation using screw foundations did not meet the high requirements for flood protection on the building site. In order to be able to adapt the base walls to the specific geometries of the formwork elements, the elements were first positioned 50 centimeters above the floor slab. Only then the plinth strips were formed, reinforced, anchored and concreted. Together with the reuse formwork elements, they form a kind of timber-concrete composite construction. An extension consisting of four timber panel walls acts as bracing together with supports and carries the roof. It consists of a simple beam layer that rests on the panel construction walls and a surrounding edge beam. Planking of the beam layer made of three-layer boards forms the roof surface with sloping insulation and flat roof waterproofing. The upper façade area (floor-strip formwork made of spruce boards) consists of prefabricated elements that are suspended from the parapet of the roof. An intermediate level between the façade and the formwork elements reinforces the façade. The ground floor façade was installed on site.
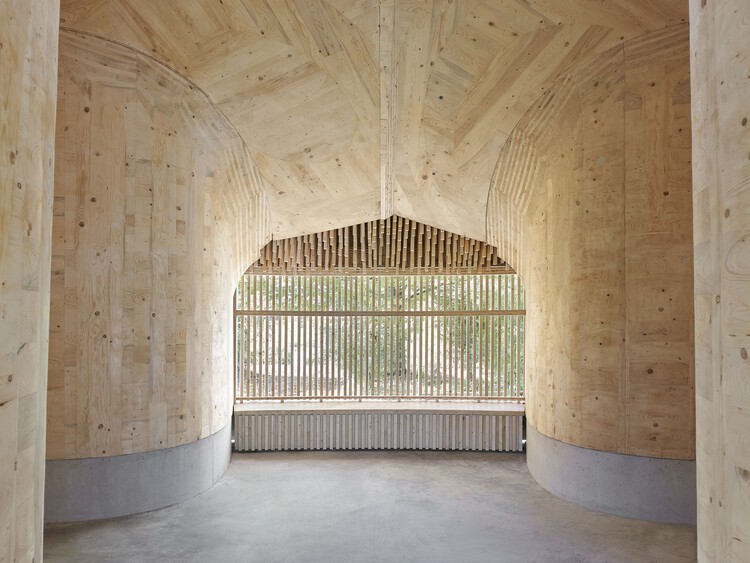
Circular Construction - The formwork elements form the essential part of the supporting structure and all interior surfaces. The outer shell consists exclusively of solid wood, which is reversibly screwed together. Apart from the roof waterproofing, neither foils or underlays nor adhesives or paints were used. All wooden surfaces remain natural. In addition to structural, physical and aesthetic issues, the research accompanying the experimental building also examines the legal framework for the use of reuse components. In this way, the specific legal framework for the reuse of building components can be further developed and generalizable recommendations for experimental construction can be drawn up. Exceptional Architecture - The use of the formwork of the Stuttgart 21 station offers the opportunity to create unique architecture that would not be affordable under normal conditions. This is because the three-dimensionally curved wooden surfaces are extremely complex to produce, with meter-thick layers of multi- and cross-laminated timber milled into the desired shape using a robot arm that can move in eight axes. The present design combines a special selection of formwork elements (of which there are no more identical parts) to create a textile-looking, tent-shaped interior, which is, however, made of solid wood. In addition, any boat lacquer that formed the formwork surface for concreting (and incidentally preserved the elements) was removed manually using electric planers. This process and the subsequent treatment with parquet and random orbital sanders revealed a unique wooden surface that has a Damascus steel-like structure due to the amorphous, three-dimensional milling of the parallel layers of cross-laminated timber.
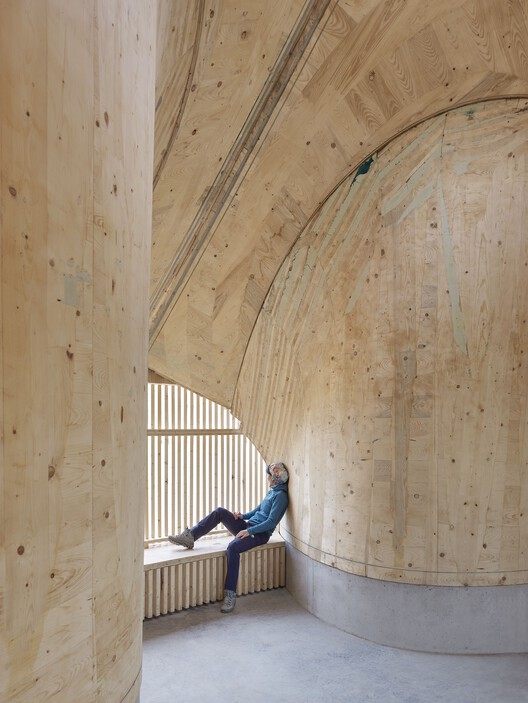