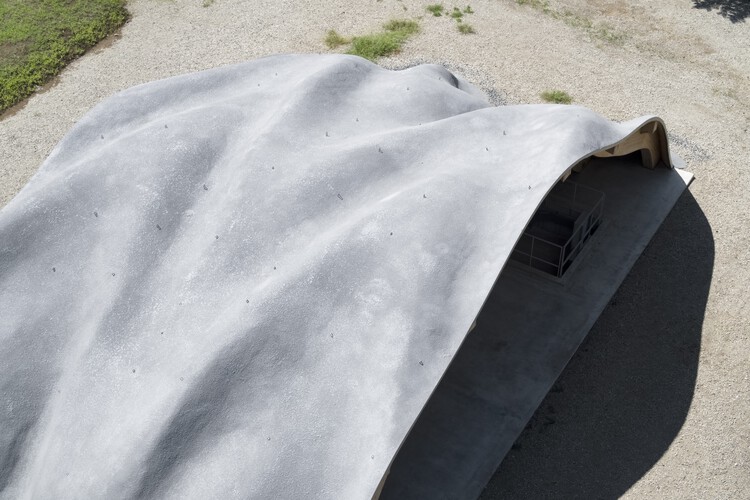
-
Architects: VUILD
- Area: 295 m²
- Year: 2023
-
Photographs:Takumi Ota
-
Lead Architect: Koki Akiyoshi
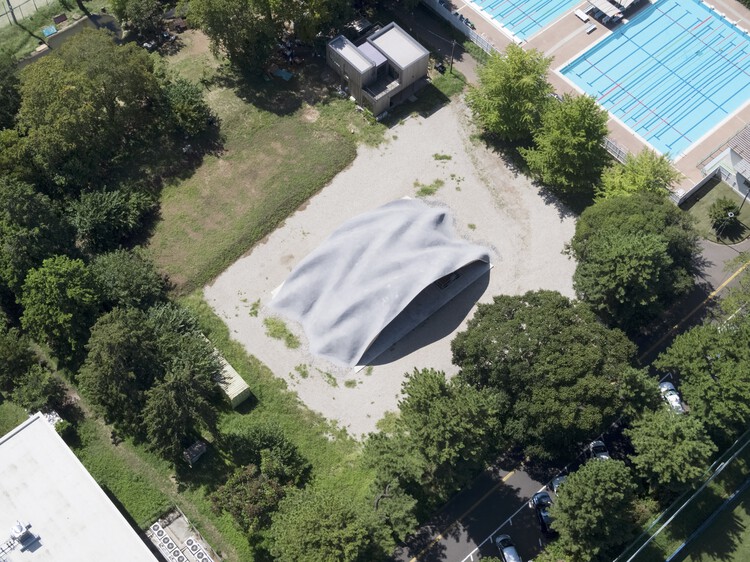
Text description provided by the architects. This facility, “The Learning Architecture for Learners,” was constructed as a project of the Educational Incubation Center's Explayground,’ which promotes collaborative efforts between industry, government, and academia at Tokyo Gakugei University, Japan.
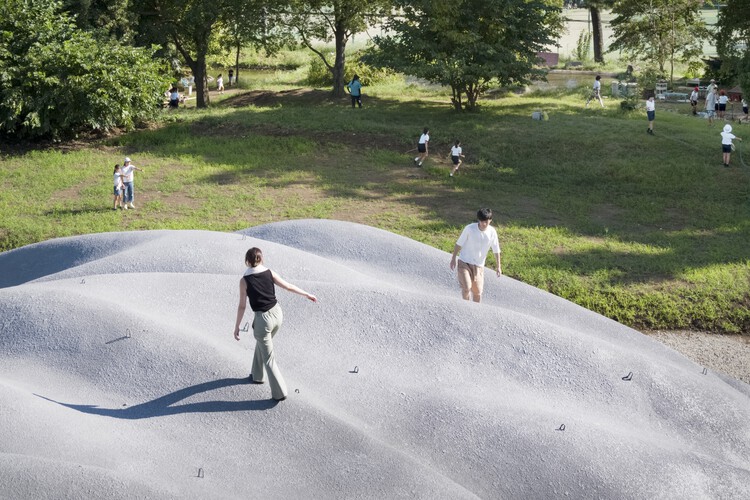
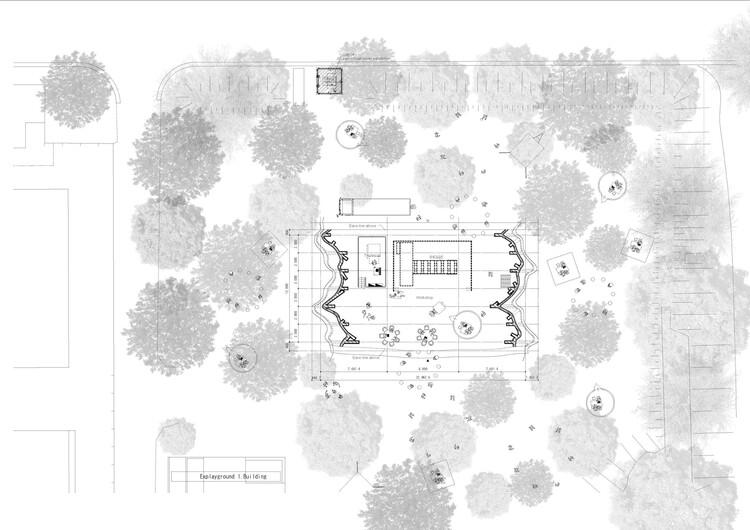
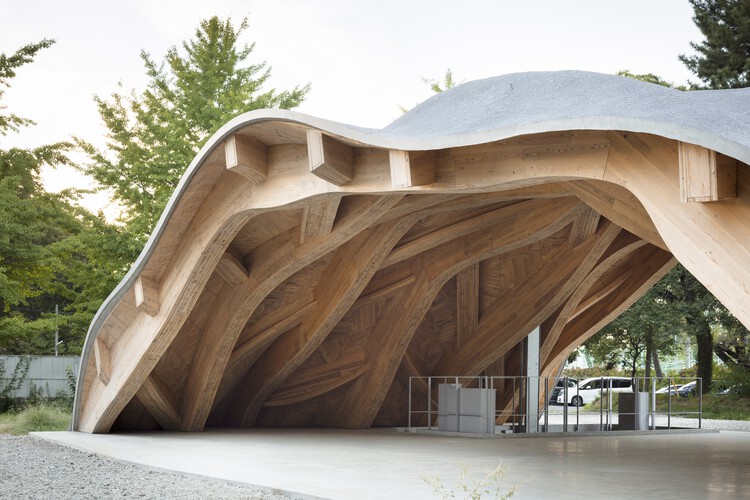
The structure is a reinforced concrete structure using CLT as formwork, with CNC-machined wood beams and panels used as formwork for the concrete slab, leaving a "residual formwork" as the finished surface. This is an unprecedented use of a concrete formwork in Japan that functions as the primary structure. A CAD model was automatically generated using a geometric algorithm, and a CAM path for 5-axis CNC machining was created using the CAD model as an auxiliary line by the VUILD parametric team. All pre-cut components were produced in the VUILD’s own factory using a 5-axis CNC machine. The CNC machine that machined the formwork will be installed also in the completed building, which will be used as an open facility where anyone can experience the advanced manufacturing technology and create the necessary space and place by themselves.
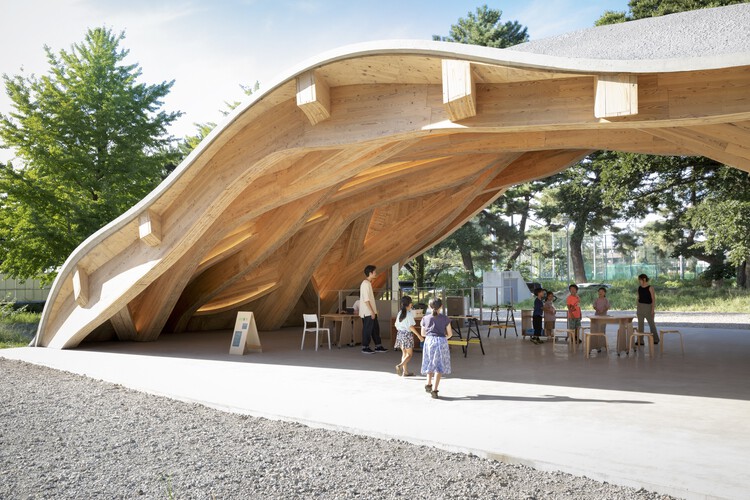
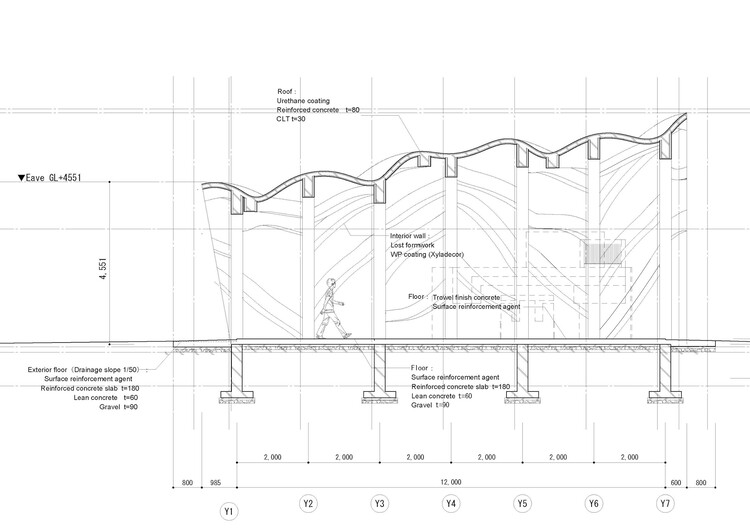
Design Process - The design challenge was to create an open space that would serve as a place to implement new public education for the next generation, as well as an expandable space with no finished form. In addition, an extreme and experimental architecture as itself a learning material was required. Therefore, VUILD decided to create a large-span versatile space using a 5-axis CNC milling machine. The constraint was given to cut out CLT panels up to 240 mm thick, for which repeated simulations were conducted to optimize the overall shape and the convenience of the cut-out. Material optimization and form simplification were performed with construction in mind.
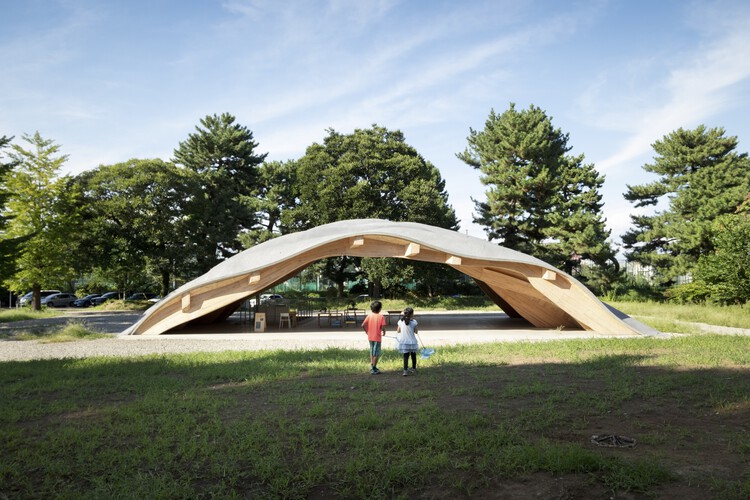
Unit Construction Method + Remaining Formwork - The CLT beams were designed with the longitudinal section as a sine curve, and the amplitude-phase was shifted in the cross direction to create a strong shell. As for the shape, after repeated studies, it took a roof shape that mimics the veins of leaves found in nature. The depth of the shell was created by constructing the cross-section in a zigzag pattern, and the strength of the shell was added by shifting the phases of the zigzag cross-section into three layers. The three-dimensional CLT panels were cut into units at the VUILD’s in-house factory and joined to the beams on site, and the panels were connected to each other with metal fittings. Concrete was poured into the beams, and the structure was developed into beams on the veins and a slab covering the spaces between the veins. The wooden beams span 25m, and the concrete slab is only 8cm thick. This construction method has been applied for a patent as JP 2021-042568, and as a highly versatile construction method, it reduced the cost to 60% of the normal shell construction method.
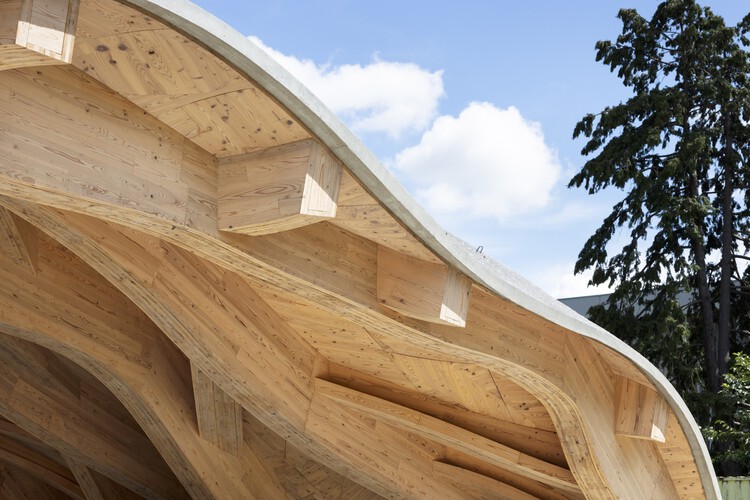
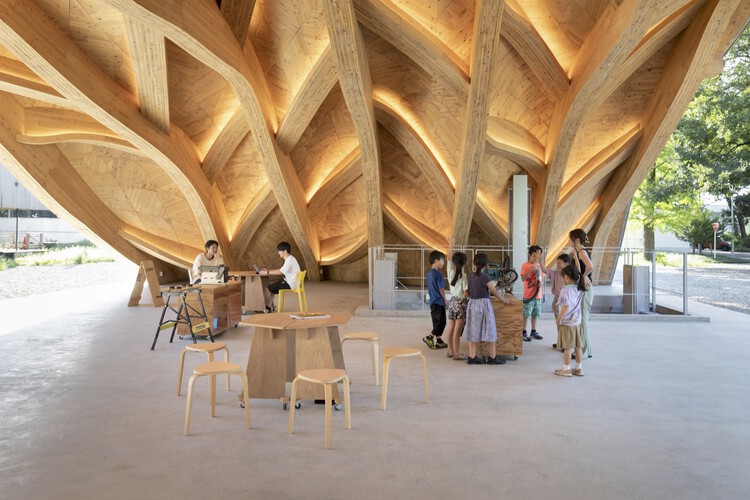
The 3D data was shared with structural designers and used for analysis, thus avoiding human errors. This data could be cross-checked in all aspects of design check, structural analysis, and part creation for fabrication, which enabled a rapid process.
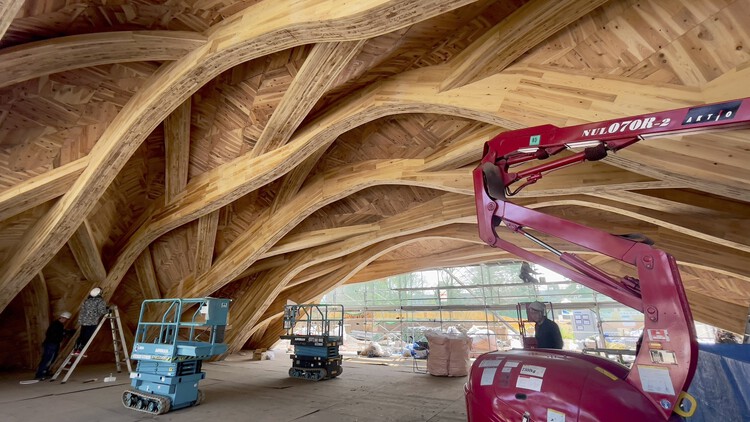
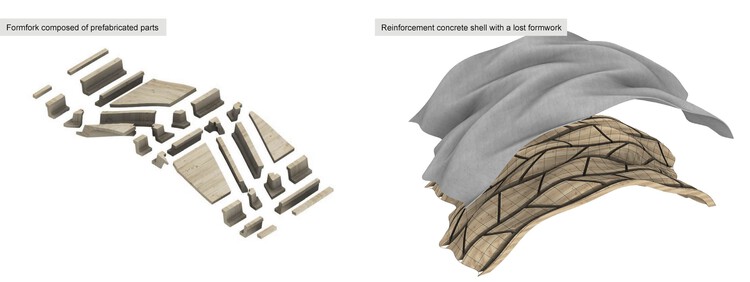
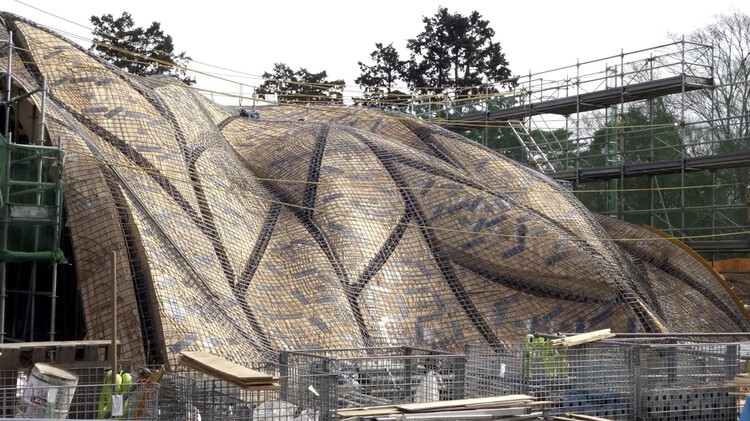
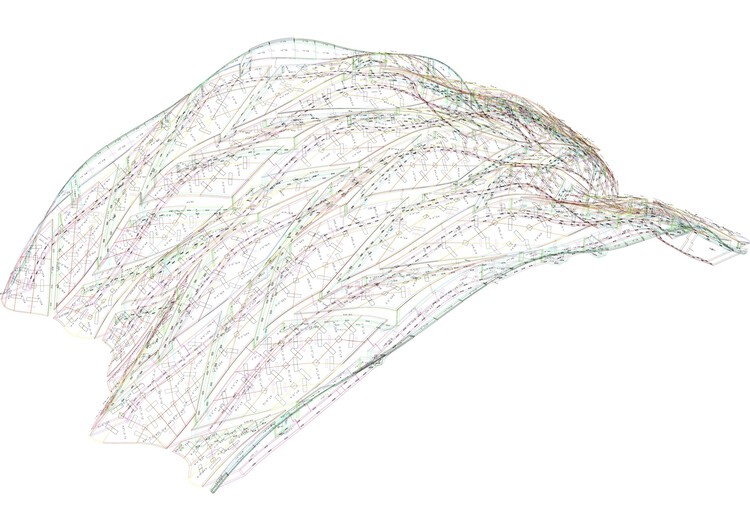
Streamline from machining data creation to material procurement and construction - 5-axis machining features tilting and rotation, which required optimization to take them into account; paths had to be created specifically for 5-axis cutting, and the number of parts was complex, with a total of 360 CLT panels to machine a 963-part formwork. An in-house parametric team developed a geometric algorithm for free-form surfaces that could automatically generate CAD documents. The path creation flow was also designed to reduce the amount of manual machining after the machining. In areas hidden by concrete, the surfaces were roughened within appropriate tolerances to reduce machining costs.
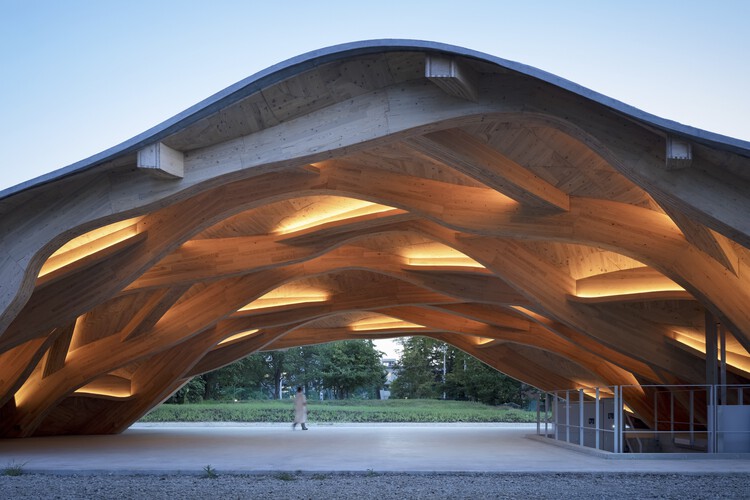
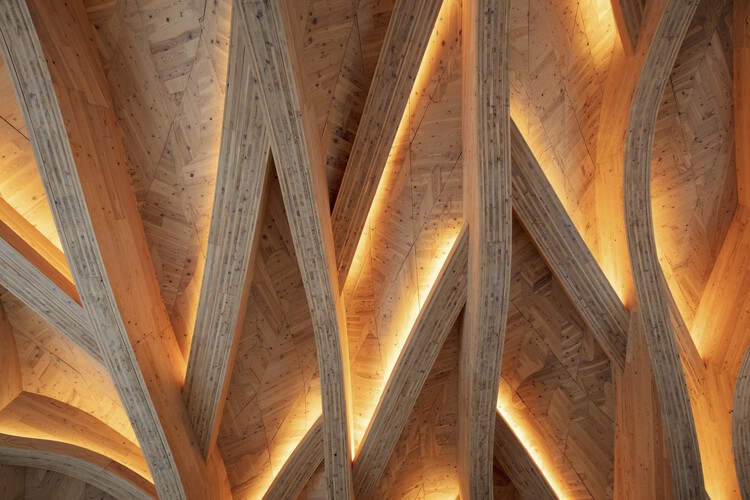
Panels were placed efficiently to reduce costs. An algorithm for automatic panel placement and shape generation achieved this objective in a short period of time, and multiple types of CLT boards were fabricated with a maximum size of 1,350×4,000mm. CLT boards were available in four different thicknesses between 60 and 210mm, and a 3D diagram indicating thickness with color coding was created. This made it easy to place the parts in different thicknesses of CLT panels. By sharing this flow with the structural team as well, we were able to create a system for optimization in terms of both structure and construction convenience.
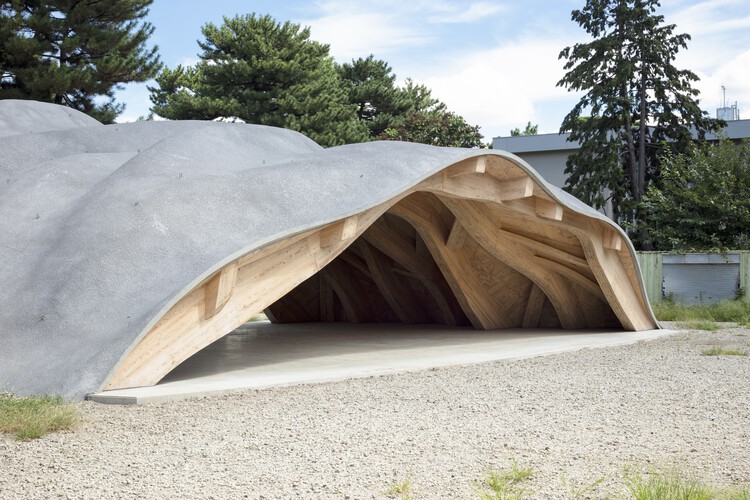