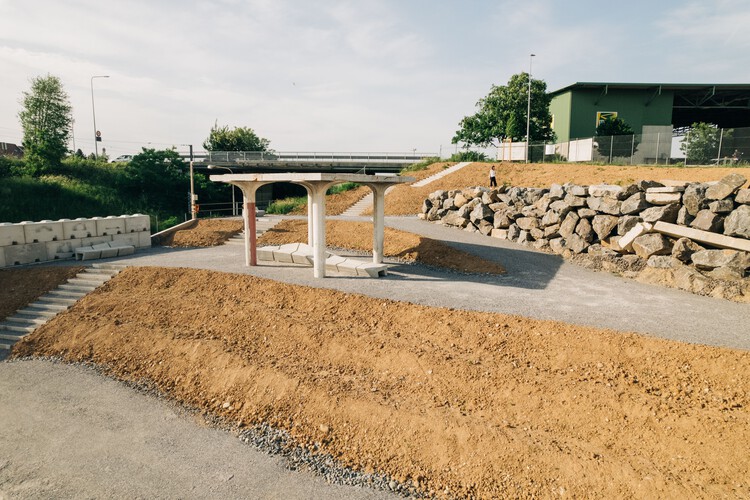
- Year: 2022
-
Photographs:Marc Schneider, Ryan Luke, Girts Apskalns
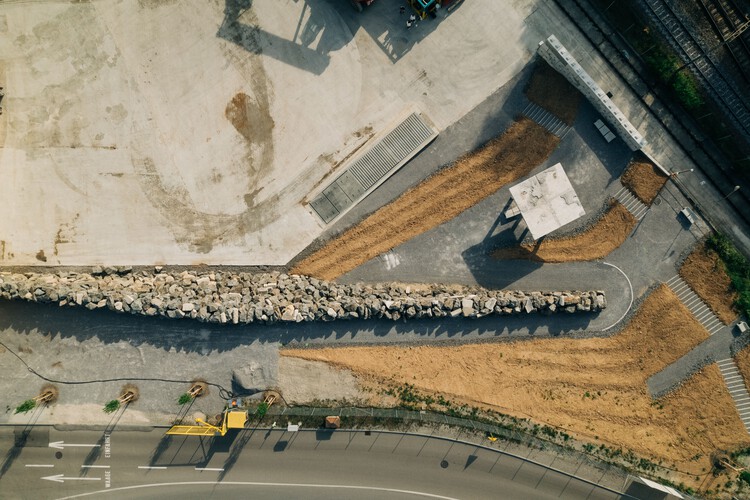
The Circularity Park Contains a Robotically. constructed retaining wall and a terraced landscape and is accessible to the public on the outskirts of Zurich in Oberglatt, Switzerland. It was conceptualized and built over a one-year period in 2021 and is the demonstrator of pivotal research in autonomous construction, robotics, and architecture conducted within the National Centre of Competence in Research (NCCR) Digital Fabrication at ETH Zurich. It is built on the campus of Eberhard AG, a local leader in sustainable construction and recycling for the building industry, who additionally supported the project with materials and construction innovations. The two ongoing research projects behind the robotic stone wall and the robotic landscape at the ETH Zurich investigate the design, control, and computational tools needed to enable autonomous robotic construction processes directly on the construction site, using as-found building materials and local soil. Additionally, a team at Gramazio Kohler Research, ETH Zurich implemented its digital concrete Eggshell technology for the robotic production of the park’s benches.
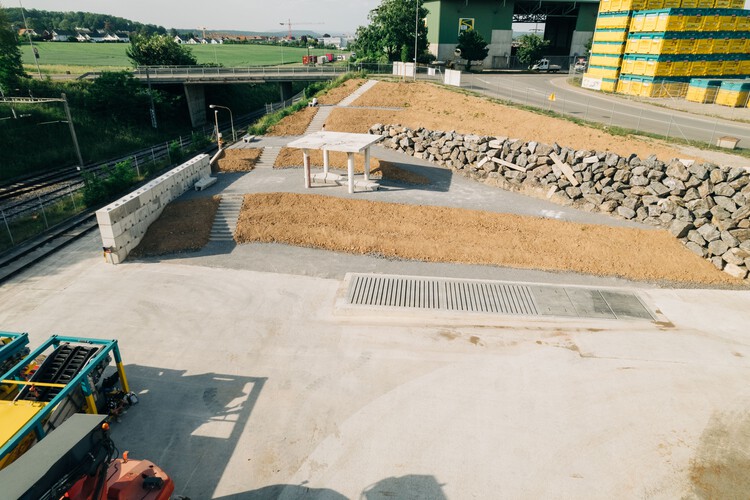
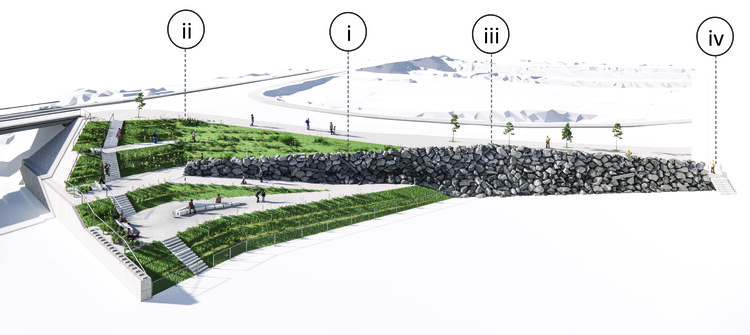
Sustainability. As the building industry is a major contributor to global greenhouse emissions, it is critical to leverage new technologies toward more sustainable building practices. One such avenue is to rethink and reshape the embodied energy of material systems that are used in construction. In particular, developments in on-site robotic building methods offer the opportunity to leverage context-specific, locally sourced, or upcycled materials that are inexpensive, abundant, and low in embodied energy. This park showcases several examples of such sustainable building practices. The construction of the dry stone retaining wall utilizes upcycled concrete and locally sourced stones. Moreover, in collaboration with Eberhard AG, several other ecological materials are integrated into the construction of the demonstrator: the drainage gravel in the wall’s backfill is recycled from railways, while the stairs at either end of the wall are built from reclaimed stone facade panels, and a repurposed concrete staircase extracted from the same site.
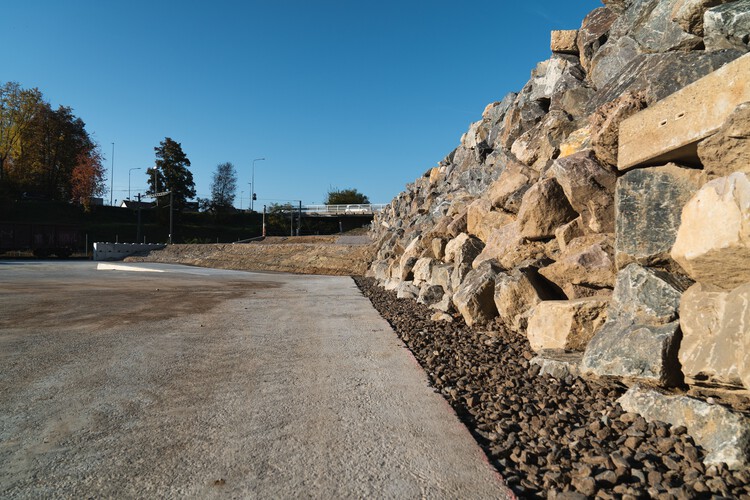
Robotic Stone Wall. The aim of the research behind the robotic stone wall is to autonomously construct masonry structures on an architectural scale, using found and readily available materials such as waste concrete and stones. The process is realized with the robotic excavator HEAP (Hydraulic Excavator for an Autonomous Purpose), a customized Menzi Muck M545 12t walking excavator developed by the Robotic Systems Lab, ETH Zurich that is currently the most advanced robotic excavation platform to be applied to complex construction tasks. Building with locally sourced boulders and waste concrete has the potential to drastically reduce the environmental carbon footprint of construction for specific applications. While such dry-stone masonry walls have historically been widely utilized for partitions, retaining walls, and terracing, there are many complexities associated with their production, calculation, and verification that make them less viable in the context of modern construction. This project demonstrates that computational methods, machine vision approaches, and new control methods can be successfully integrated to handle the geometric variety of stone and rubble shapes in an adaptive building process that unfolds in an unstructured construction environment. The permanent retaining wall at the Circularity Park represents the largest demonstration of this method: the structure is 65 meters long, 6 meters tall at its apex, and consists of 938 individual elements (boulders and concrete demolition debris, with an average mass of over 1000 kg each)—placing it among the largest robotically fabricated structures in existence.
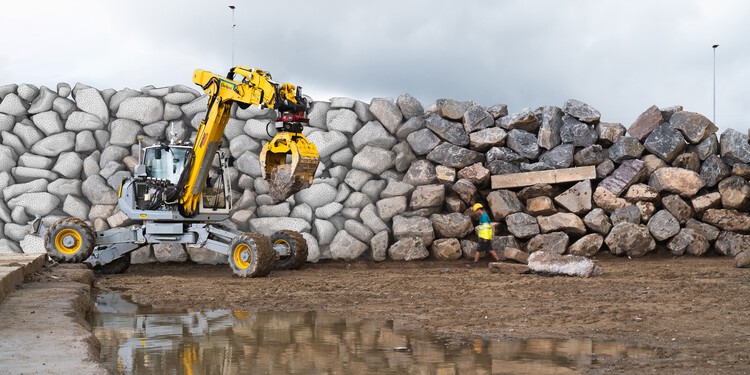
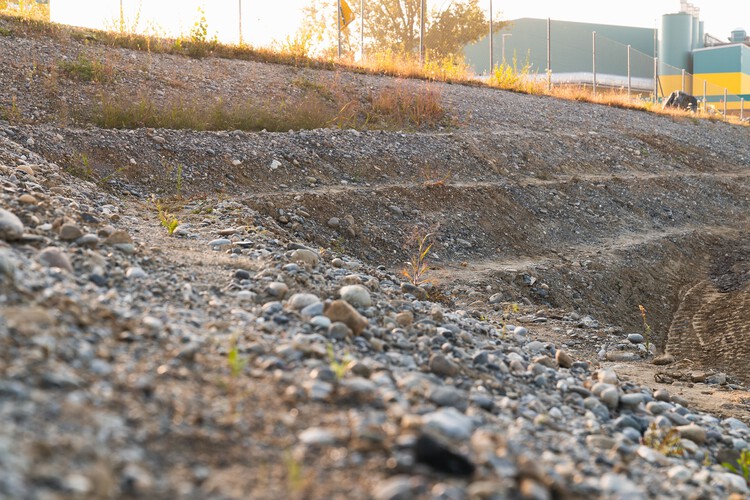
Robotic Landscapes. The project Robotic Landscapes aims to develop computational tools, technologies, and workflows for automated and digitally controlled landscaping, reaching a precision for complex shapes that could not be achieved through manual excavation methods. The process also utilizes the HEAP robotic excavator, equipped with a bucket, to bring the plans of the landscape architect to reality. The robotic landscape in this park serves the purpose of facilitating pedestrian circulation by connecting the large differences in elevation between the top and bottom of the retaining wall. Four large embankments are built with high accuracy by the robotic system, where each embankment contains smaller steps that support local plant growth while controlling water runoff and erosion.