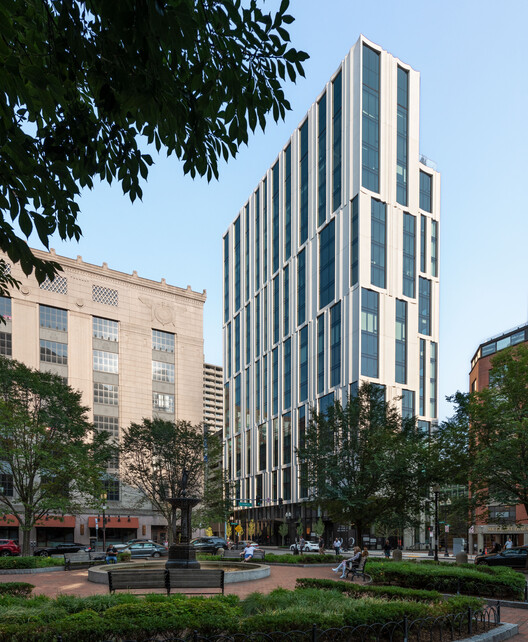
-
Architects: Höweler + Yoon Architecture, Sasaki
- Area: 146000 ft²
- Year: 2022
-
Photographs:Chuck Choi
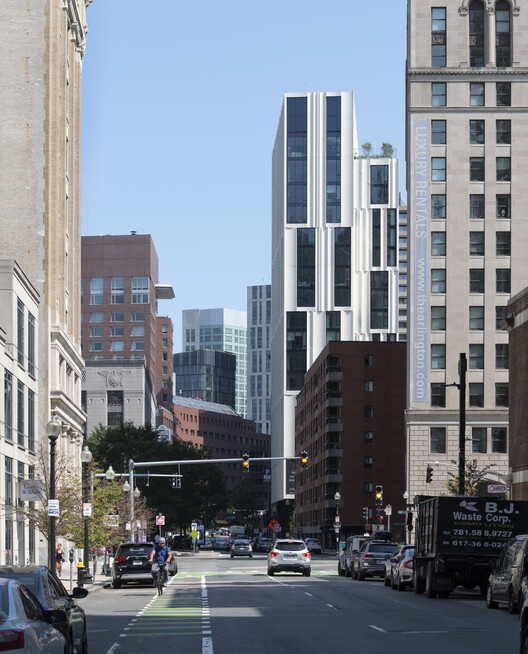
Text description provided by the architects. Situated between two neighborhoods, 212 Stuart Street negotiates the intimate residential scale of historic Bay Village and the high-rise scale of Boston’s High Spine. Moving away from the more traditional all-glass high rises in the city, the team sought to bring quality and depth to the urban façade. Employing an innovative approach to materials and construction, the building’s distinctive façade consists of fluted piers that vary in scale across the envelope and resonate with the masonry detailing of the historic neighborhood.
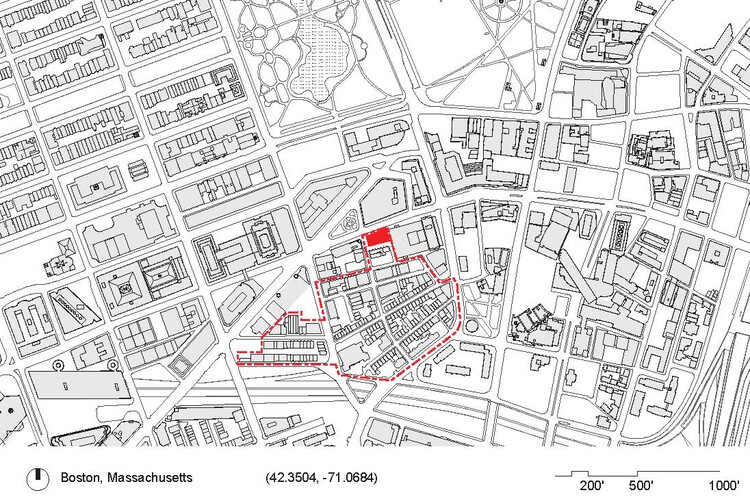
212 Stuart Street operates at several scales in the city. When viewed from a distance, the building meets the sky with a distinctive silhouette. At the street level, the building meets the ground in a way that immediately engages with the sidewalk and streetscape as stoops, planters, and ironwork create a dialogue with the residential context of Bay Village. This nineteen-story building also contains two townhouses that complete the north side of the Bay Village streetscape.
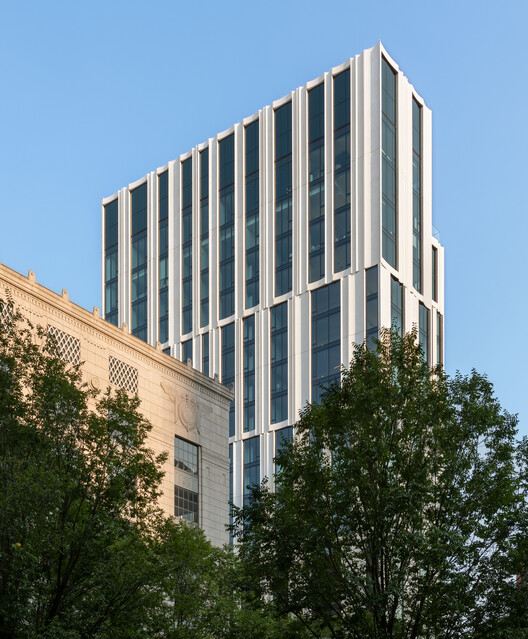
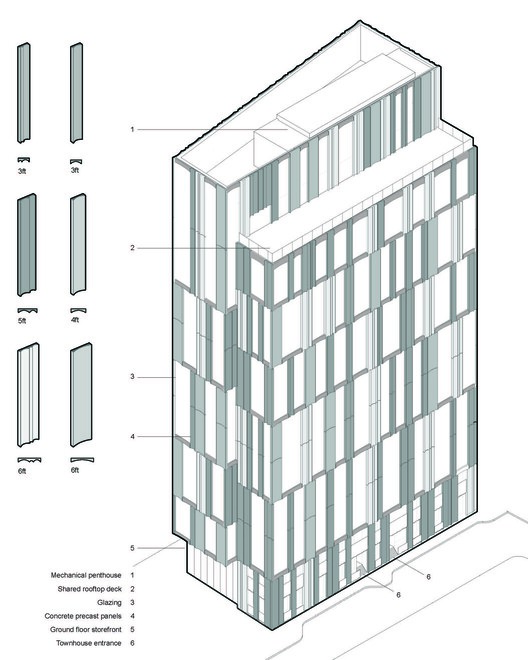
The project’s location—a small, irregularly shaped site that was formerly used as a parking lot—presented several design constraints, including its tight urban context. The building envelope was coordinated with precast concrete fabricators and façade installers in the early phases of design and construction to minimize friction during construction. The design pushes the limits of the fabrication of the multi-story concave panels, typically either 20 or 30 feet high, across eight primary molds to reduce installation time by optimizing construction sequencing. The irregularly-spaced concave panels (fabricated locally by BPDL) and multi-story, recessed glass infill panels emphasize the building's verticality and create a part-to-whole relationship that makes 212 Stuart Street distinct within Boston’s skyline.
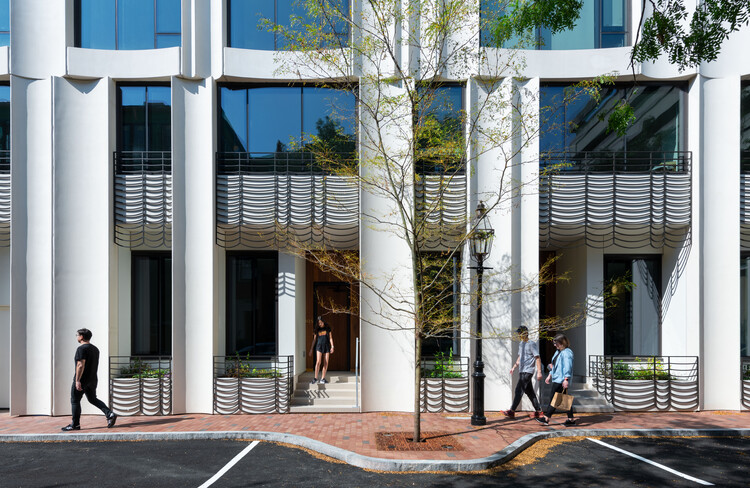
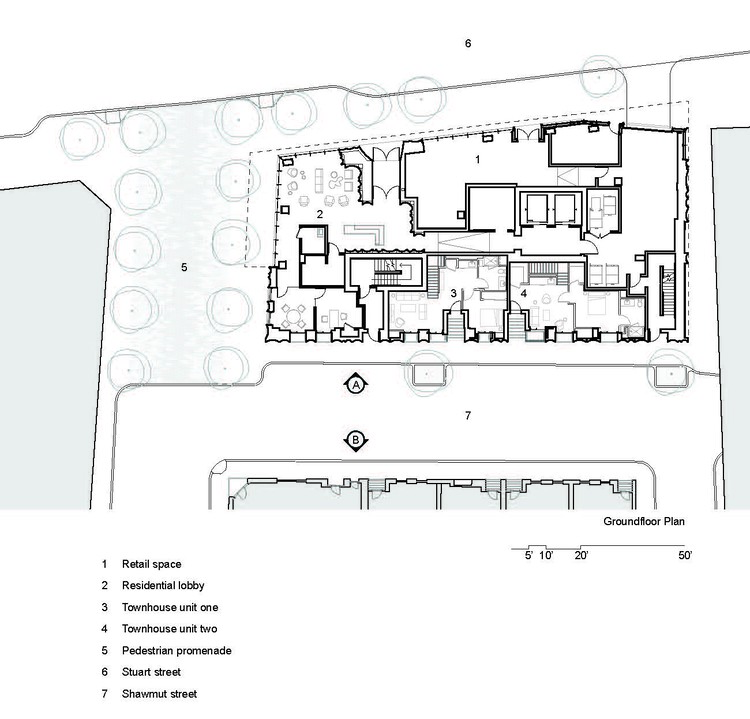
The panels were carefully tagged and ordered at the plant and loaded onto trucks in the exact sequence they would be installed. At the site, the panels were picked by crane directly from the truck and hung on the building, saving a time-consuming staging process. Glazing for the residential units takes the form of a floor-to-ceiling window wall with spandrel glass at the concrete slabs. The thickness of the panels ranges from 12 inches at the ends to five inches at the center which allows for dramatic depth and shadow while also allowing for the facade to be partially self-shaded.
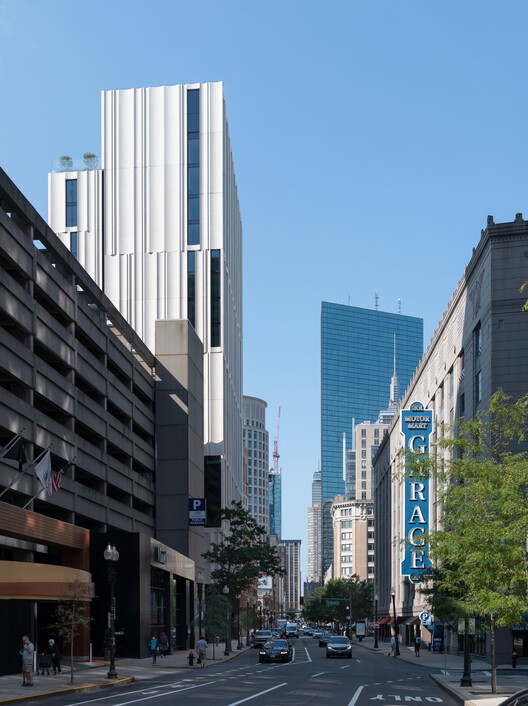