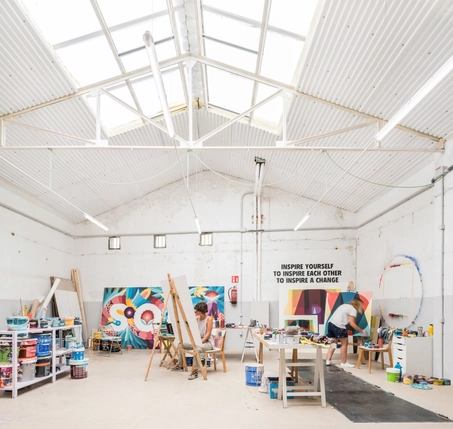
Recent statistics suggest that if someone lives until they are 80, around 72 of those years will be spent inside buildings. This makes sense if we bear in mind that, when not at home, humans are working, learning or engaging in fun activities mostly in enclosed, built settings. Contemplating current events, however, this number is expected to grow. In an increasingly chaotic and uncertain world, marked by the ongoing effects of climate change and the global pandemic, the desire to stay indoors in a protected, controlled and peaceful environment is stronger than ever. Architects face an important challenge: to create comfortable, productive and healthy interiors with well-regulated parameters, considering factors like indoor air quality, daylighting and biophilic features from the initial stages of design. Of course, this involves choosing materials sensitively and accordingly, whether it be by avoiding certain health-harming components or by integrating non-toxic products that soothe and promote wellness.