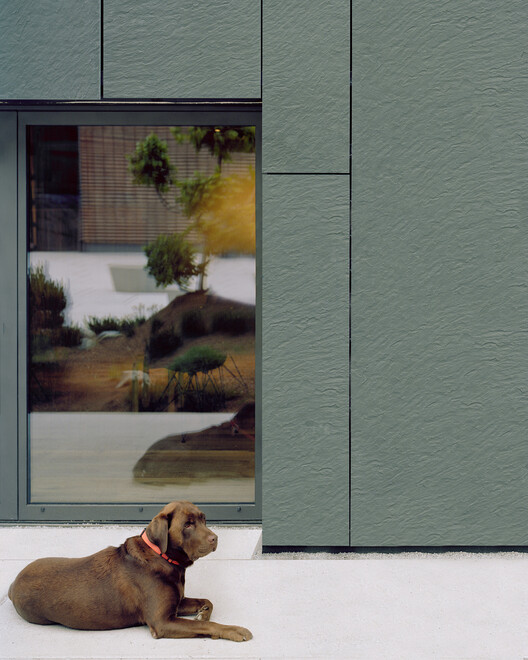
Although we usually think of climate change as something that should be addressed by research institutes, governments or official reports, private companies also play a key role in affecting change, as they are on the front lines of production and innovation. This is especially true in the field of construction, as it is an industry that moves a significant amount of resources and people, but also exerts a huge impact on the environment. Unfortunately, not all companies take on this challenge, although this is slowly changing and can be seen in a number of successful examples. One of these is the case of Rieder, which embarked on a journey to become “Climate Positive” by 2030 and, more notably, set the example when building its new headquarters.
One of the major challenges facing the construction sector is to reduce the use of cement, an essential raw material for concrete production, which is the second most consumed product in the world, only after water. This is because cement is one of the great villain of greenhouse gas emissions. Just to get an idea: if cement were a country, it would be the third largest carbon dioxide emitter in the world, surpassed only by China and the United States. But is cement really essential for concrete production? Wolfgang Rieder, CEO of Rieder Group, is convinced not, and believe in possible substitutes for cement. He has applied these precepts to his company's products, which has become a pioneer in CO₂-reduced façades.
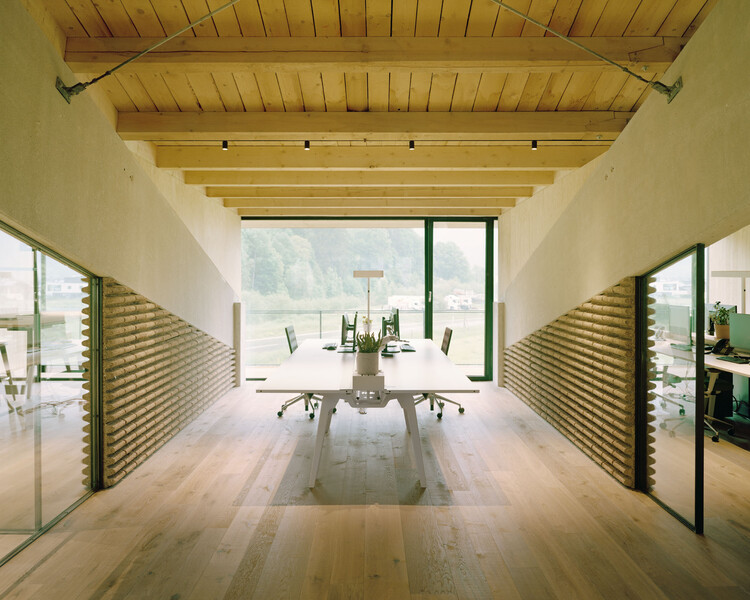
The company intends to be carbon neutral in 3 years. According to Wolfgang, “We have identified the levers where we can intervene in order to produce and operate in a CO₂-neutral manner by 2025. Now, we are implementing our plan, evaluating the results and developing them further." This jump from carbon neutrality to carbon positivity will be done through innovations in material combinations, digitization, radical reduction in waste and extension of the useful life of products and buildings. A good applied example is glemm21, the new Rieder headquarters in Maishofen, Austria.
This is not a new building, but a remodeling of a disused bus depot that has become the company's "greening" testing laboratory. “Not to build anything new, but to use what is already there is known to be the best way to save grey energy and not to seal any additional areas. So we tried it out on ourselves”, says Wolfgang Rieder. Around 1,000 tons of CO₂ could be saved during the transformation of the former bus garage into the future-proof headquarters glemm21, which corresponds to the annual electricity consumption of 1,000 three-person households. In addition to the ecological factor, the building has several historical components that give it a particular identity, such as concrete columns, recycled steel and a pine wall dismantled from another building.
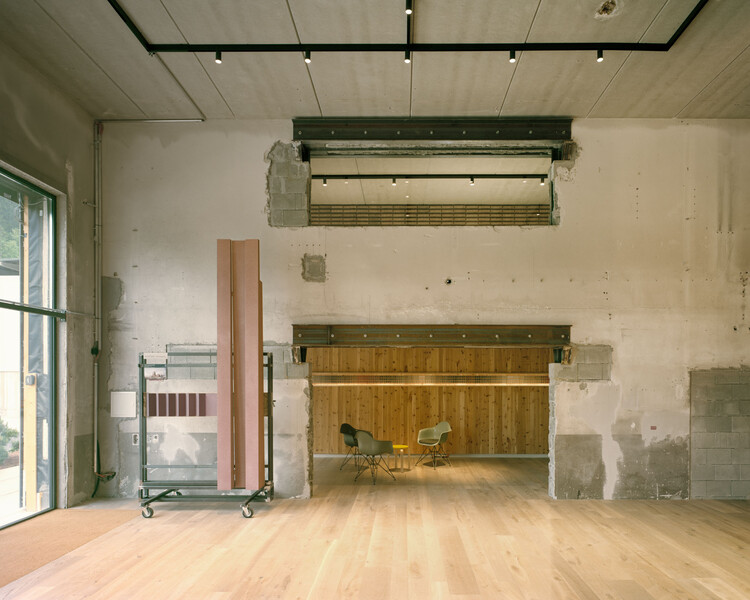
But in addition to reusing existing buildings, increasing material life is essential to achieving more ecological and sustainable architectures. The company was inspired by Opus Caementicium, a mixture of stones, limestone, water and pozzolana (volcanic ash from the region around Naples), which becomes extremely resistant when dry, lasting thousands of years, as seen in some ancient Roman constructions, such as the pantheon. In the case of Rieder's façade panels, cement is gradually being replaced by natural and local pozzolana, whose production emits significantly lower CO₂ emissions. These are agglomerant materials whose silico-aluminous composition differs from Portland cement only by the absence of the calcium element. When properly ground and hydrated in the presence of lime or even cements, they react and form high quality cementitious compounds and durability.
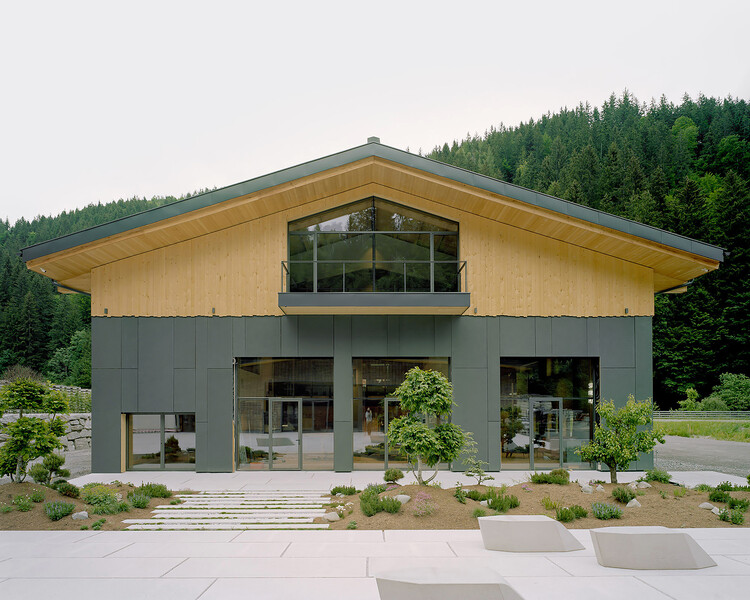
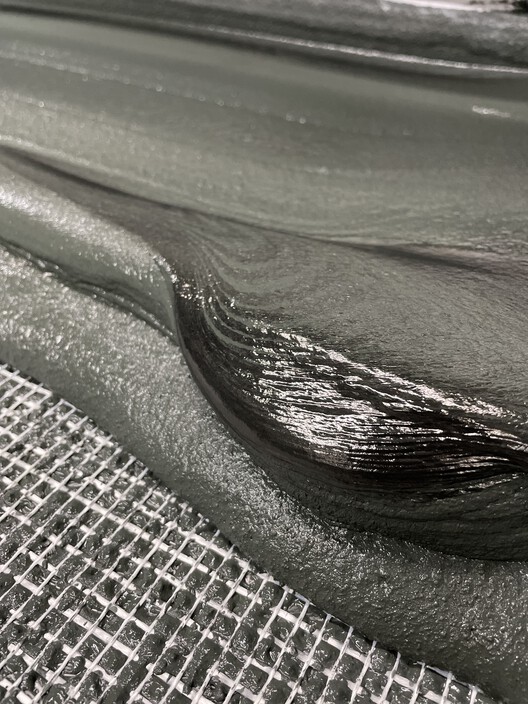
These are the panels that line 400 square meters of the new Rieder building's façade: the concrete skin, made of glassfibre reinforced concrete. The texture and the greenish shades resemble a natural slate surface, but there are a wide variety of colors and textures that can be chosen; the concrete façade coating product can fit a variety of dimensions, distributions and types of buildings. The main difference is that 50% of the cement in the concrete matrix has been replaced by alternative materials, resulting in a 30% reduction in CO₂. The plan is to fully substitute the cement step by step. In addition, the material requires no maintenance, and individual elements can be easily replaced.
According to the company, the plan is to convert its entire product range to cement-free material by 2027. This would make Rieder the first manufacturer of low-carbon façade panels made of concrete. And cement-free concrete is just one piece of the puzzle in a company philosophy that focuses on sustainability in the broadest sense.