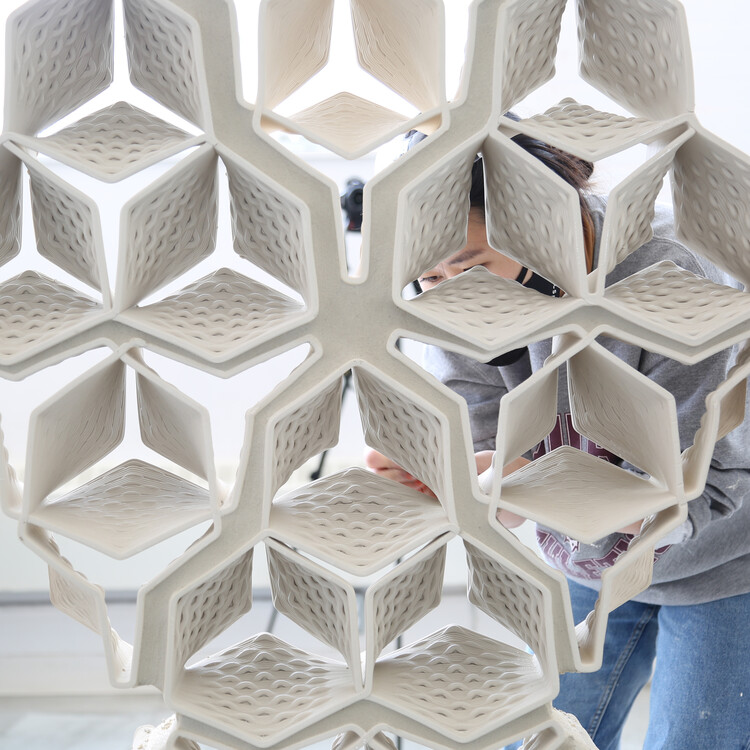
Since the 1980’s, 3D-printing has offered new ways of developing architecture, engineering, and objects of daily use. When it comes to digitizing analogue processes, it is vital for users to become familiar with current tech innovations and their benefits. HIVE Project reshapes the art and craft of building in clay by combining traditional ceramics, smart geometry, and robotic precision to construct a masonry wall composed of one hundred seventy-five unique 3D-printed clay bricks.
HIVE: A 3D-Printed Masonry Wall
During 2021, a Waterloo University team in Toronto, Canada, completed the construction of an office space privacy wall. This structure was not only distinguished due to its aesthetics, but also for the fact that it was erected by an advanced 3D-printer in which, “like a honeycomb, the aggregation of hexagonal units produces a strong materially efficient structure”, according to the team.
The design of the wall plays with variations in the opening and closing of the clay bricks that create a distinct atmosphere. The layout allows both privacy and light to pass through the wall, provoking a noteworthy setting that divides but also manages to keep the space as a whole.
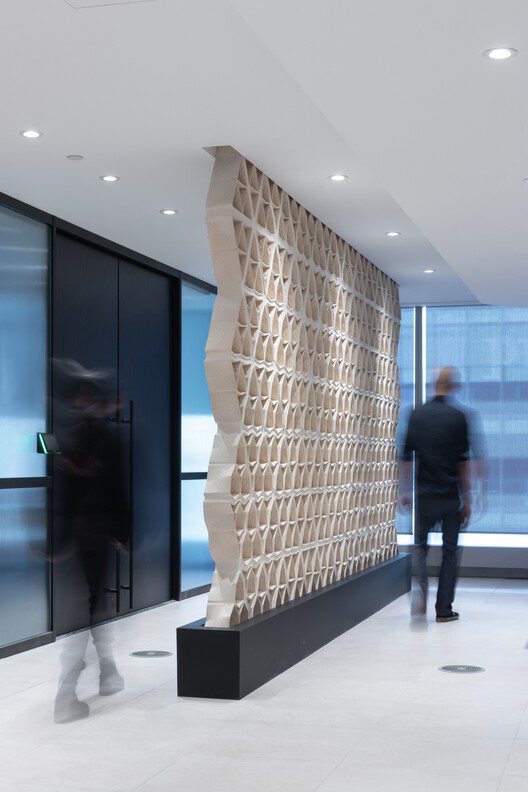
HIVE’s Project Development
Canada’s first 3D-printed masonry wall was born after a complex development where the team tested different materials, designs, and fabrication processes before accomplishing their goal. According to the team, the project’s approach aims “the spirit of traditional ceramic craft with robotic precision, offering new avenues for material expression and geometric complexity within this field.”
As one of their goals was to acknowledge the natural properties of clay – a stable and long-lasting traditional material – they assembled diverse clay mixtures adaptable for an innovative 3D-printing process. Within the combination of digital and analogue models, HIVE introduces the concept of ‘digital craftsmanship’ as a new construction process.
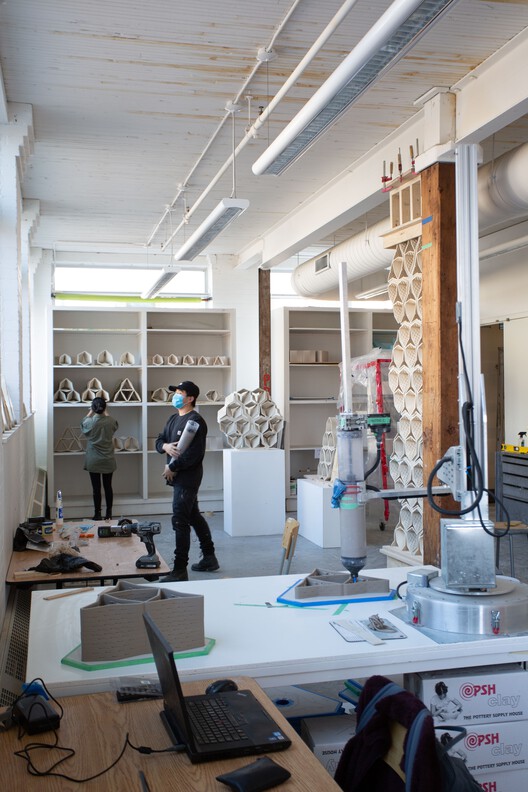
The 3D-Printing Process
3D-printing is known as an additive manufacturing process that creates three dimensional objects from a digital file. Through a layering method of cut cross-section files, the printer creates an object of diverse materials, shapes, sizes, and qualities. Inside their Waterloo University lab, the HIVE team proposed a construction process that combines the knowledge and experience of a historic material with the advantages of new discoveries.
The creation process of the masonry wall consists of three main steps, beginning with the design and selection of the best pattern to form the wall. The process follows with the production of a handmade clay mixture that aims to obtain the malleability and fluidity needed to shape the clay units. Lastly, a robot takes the lead and 3D-prints the already designed digital pattern through sliced layers of clay.
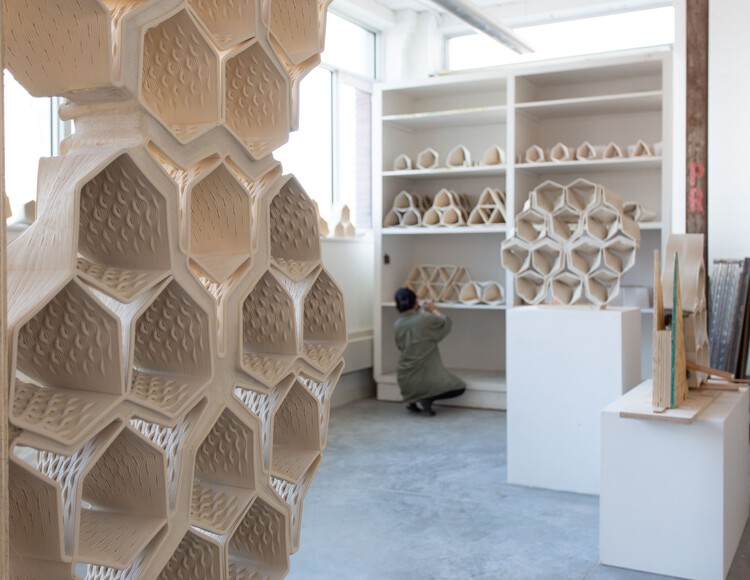
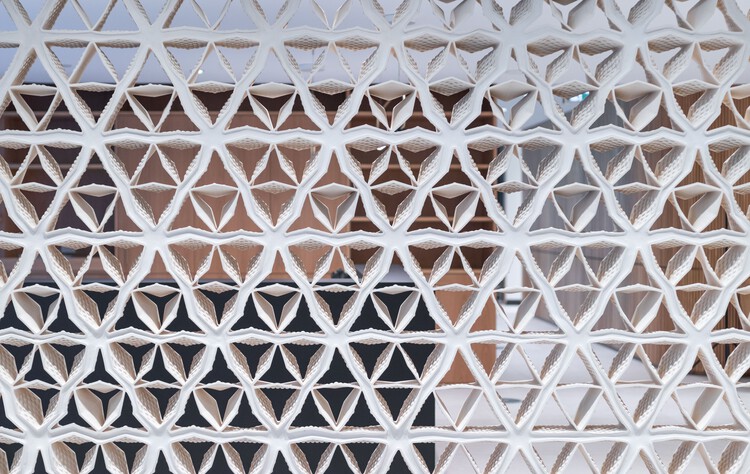
The Wall: Strong and Aesthetic
The result of their work was a 2.3m x 5.4m 3DP masonry wall for a reception space. After the team researched and tested different mock-ups, they were able to computationally design a geometry of units that assures the feasibility of the wall.
Raised through the association of triangular bricks composed of four hexagonal shapes, the 3D-printer not only creates a stable and permeable wall, but also an artistic object with a unique pattern, texture, and color. The resulting “honeycomb” pattern displayed by the wall was possible because of the design freedom of a 3D-printing fabrication process.
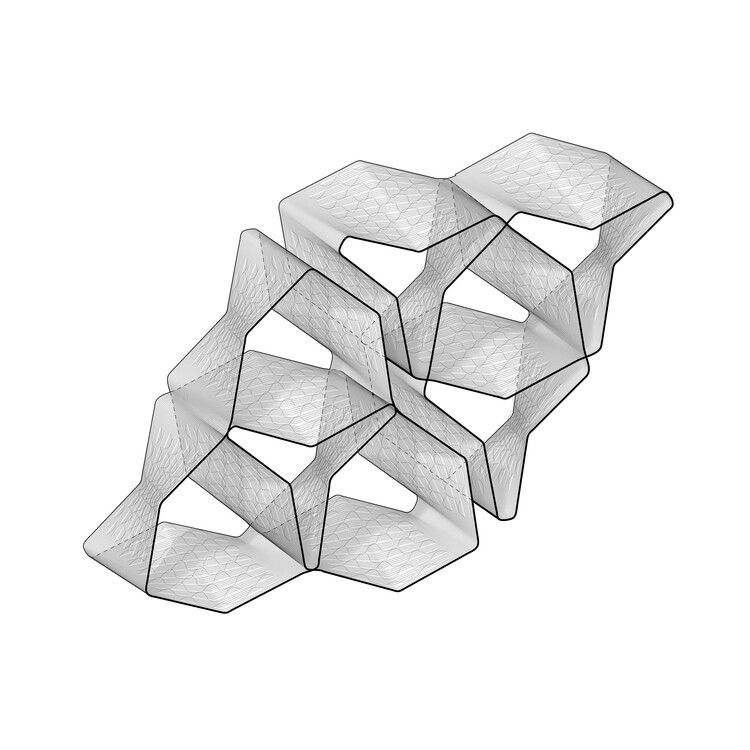
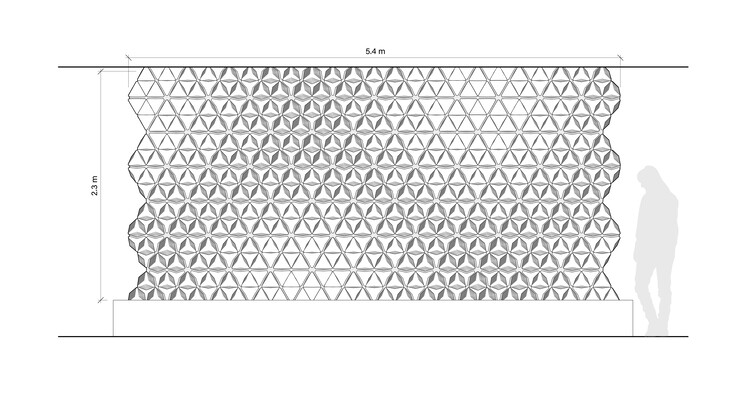
Nascent Technologies and Architecture
The Digital Era provides a meeting space for both innovation and challenges. Technologic advances combine well-known analogue processes like masonry construction with digitization. 3D-printing and its capacity to produce large prints offers an attractive and economically tempting intersection between technology and architecture.
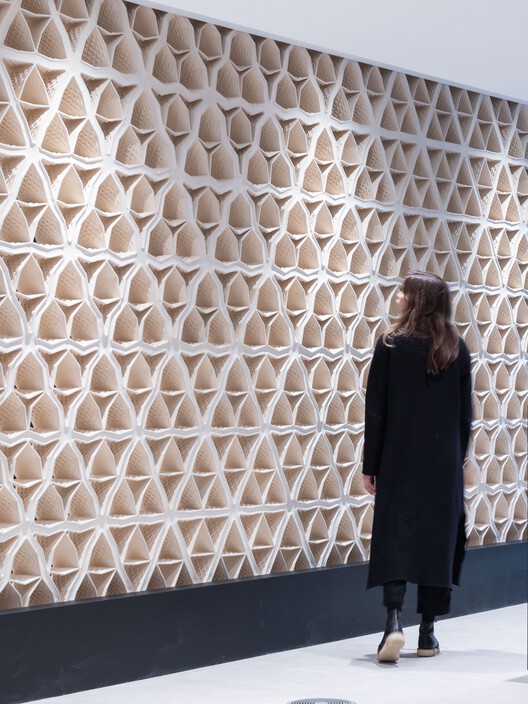
Project’s Credits and Support
HIVE was designed by a six-member research team - Ye Sul E. Cho, Ji Shi, Meghan Taylor, James Clarke-Hicks, Isabel Ochoa, and David Correa - from the University of Waterloo in partnership with the Investment Management Corporation of Ontario (IMCO). The project was commissioned by SDI Interior Design and technical and financial support for 3DP masonry research came through the Masonry Works Council of Ontario.