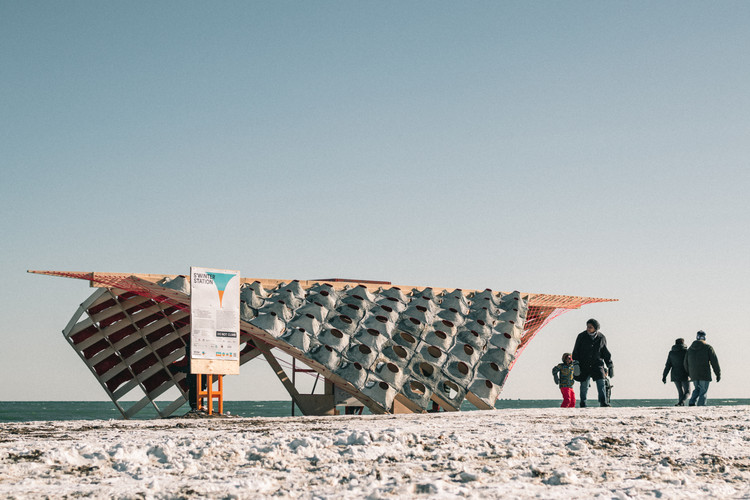
The construction industry has experienced severe changes in recent decades. Historically, it counted on abundant labor and a false notion that natural resources were infinite, but nowadays the sector has struggled to find innovations that will allow it to become more sustainable, especially considering its enormous impact and importance in the world. In addition, the recent Covid-19 pandemic changed several factors and dynamics, demanding creativity from designers to overcome challenges. In some cases, the design process itself became subject to changes. The S'Winter Station project, developed by students and teachers of Ryerson University's Department of Architectural Science, is one of these examples which relied on existing visualization and manufacturing technology for its completion.
The project was developed as the result of a competition, the Winter Stations 2022 International Design Competition, to reimagine Toronto's lifeguard stations during the winter months, when they are not typically used. The theme of this edition was resilience and this project was one of the 6 finalists. According to the designers, “The intention of S’winter Station is to express the resilience of the surrounding beach and the Canadian public as a dynamic transition between summer and winter.”
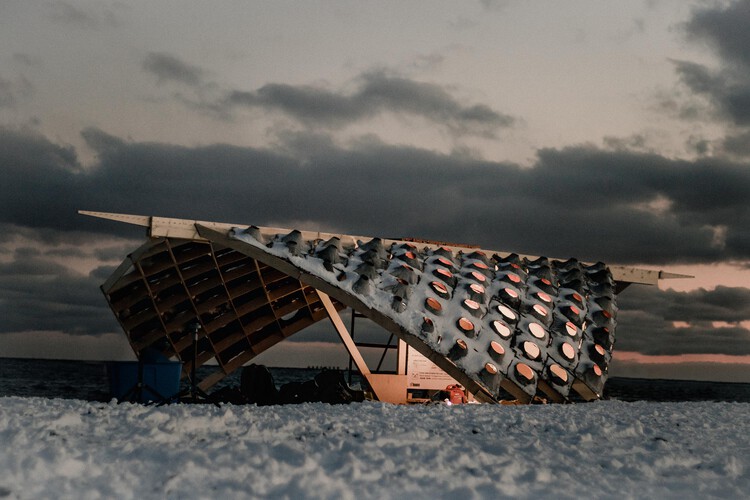
According to the project description, sent by the team:
“The forces of nature are relentless. Like the falling snow of the sky and the shifting sands of the beach, the pavilion embraces local wind, snow, and sun conditions. Following these identified directions of force, the pavilion’s wings embody movement by harnessing snow and mitigating strong winds. Beach towels have been formed into dynamic concrete panels with variable apertures. These panels control the amount of light and snow allowed to enter, while also creating unique views outwards. Together, the panels and wings protect users and encourage them to engage with their surroundings. Where the lifeguard station, beach towels, and marine ropes are more frequently used in the summer, the pavilion achieves resilience by employing these objects in the winter. The pavilion acts as a shelter for the community where winter conditions are celebrated by harnessing and adapting to natural forces.”
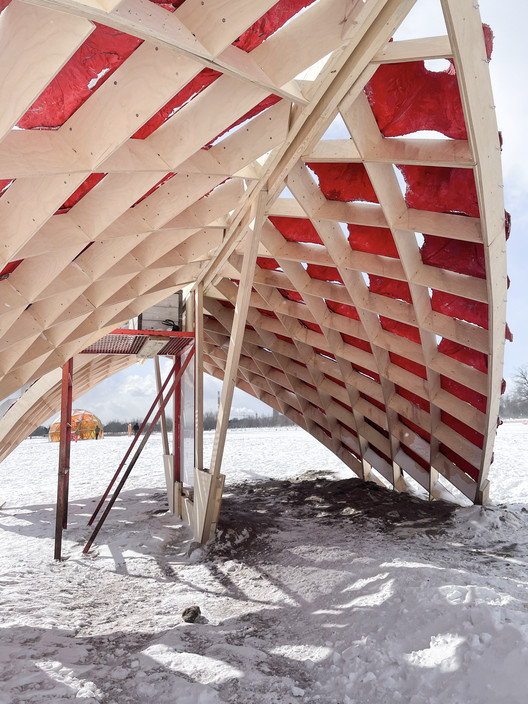
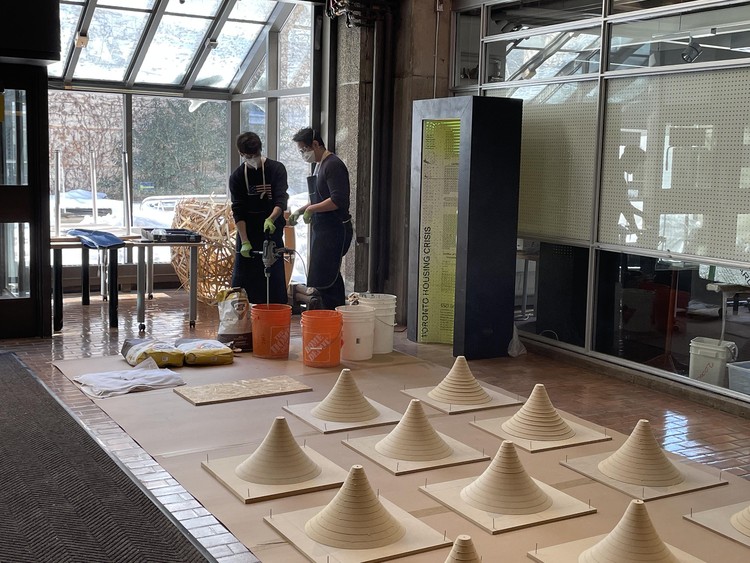
Technically, the project comprises a 13-meter length pavilion created using two distinct elements: the box frame and the concrete textile coating.
The structure consists of 270 CNC (Computer Numerical Control) cut pieces made out of baltic birch plywood, mounted on modules and hoisted to erect the structure, fitted to the existing lifeguard station. Textile concrete pieces were used to fill these modules, inspired by an activity developed at a children's camp, in which children created flower pots from beach towels covered in concrete. Ariel Weiss, leader of the project, points out that “Rather than creating flower pots, the design team chose to create a responsive and sculptural cladding. Using four unique aperture conditions, sectional pieces of a conical mold were cut out of MDF on a CNC router and assembled into large molds for the towels to form over. After fabricating the conical molds, beach towels were then organized into four unique aperture sizes and different circular holes were cut into the center of each type of towel. These towels were then dampened with water and saturated with a concrete sand mix. After saturation the towels were placed on top of the molds and left to dry for two days. Throughout the drying process the concrete towels were covered and continuously sprayed with water in order to ensure a stronger cure. With four unique aperture conditions, a total of 150 panels were created, cataloged, stacked, and shipped to site for installation.” The massification of this process in the construction sector could possibly be a solution to textile waste. Clothing and textile materials are notoriously hard to recycle, with around 85% of it being sent to landfills or burned in the United States alone.
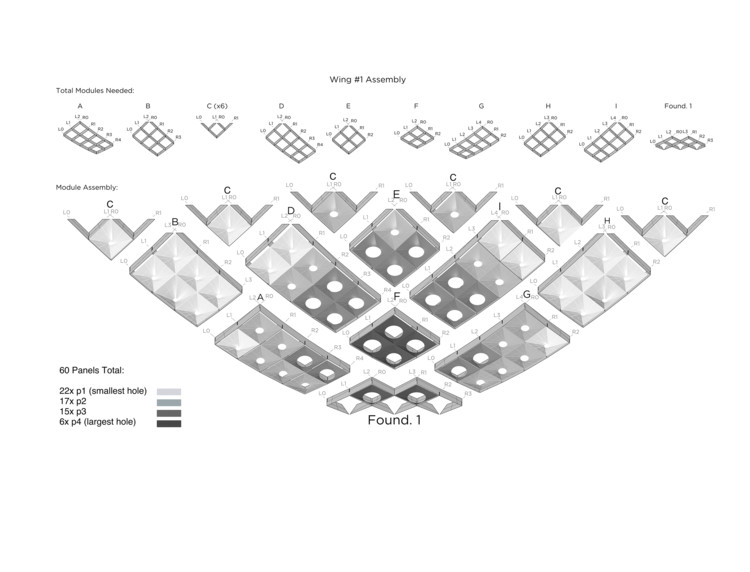
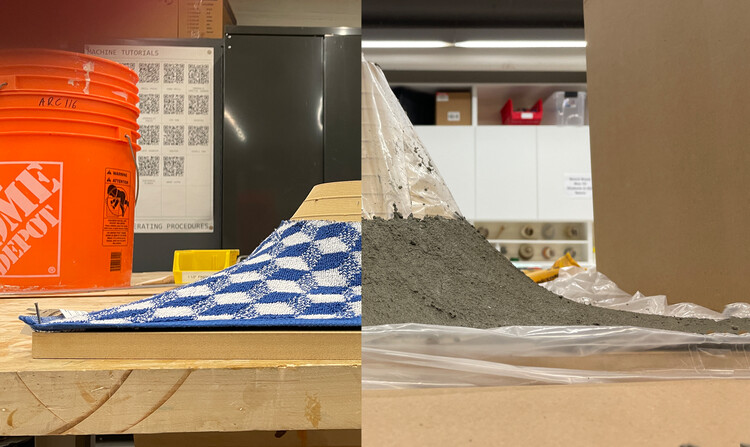
Another innovation occurred in the process of prototyping and manufacturing the pavilion. As the team began fabricating the pavilion during the COVID-19 lockdown, the they took advantage of various digital tools, alternate realities, and visualization techniques in order to ensure the pavilion was feasible and effective. While conventional modeling and visualization techniques were also used, the team used VR with Quest 2 in order to walk through the pavilion in real-time. In all stages of the project, the team also used AR with Hololens 2 in order to develop the pavilion and visualize it at a 1:1 scale. Weiss mentions that “Virtual reality was absolutely essential to the design and fabrication of this project. During the schematic design of the project both virtual and augmented reality were considerably used as a visualization tool in order to walk through the pavilion in real time. Because the design team was tasked with designing the pavilion during a COVID-19 lockdown, virtual and augmented reality were perfect tools for visualizing form and scale. This let us actually experience the design before creating it, and it informed a lot of decisions during the design process.”
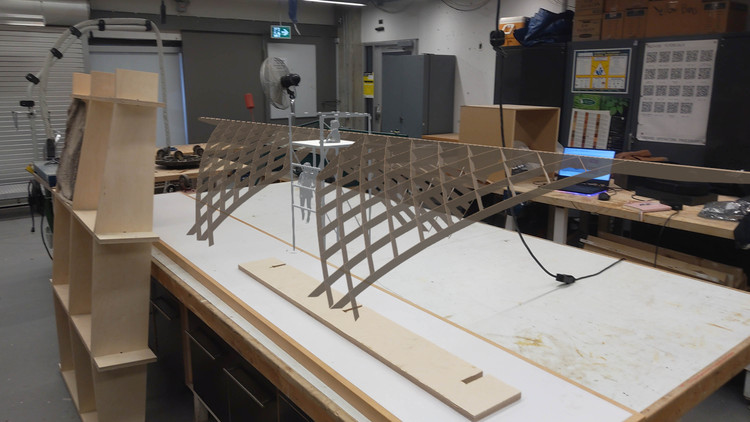
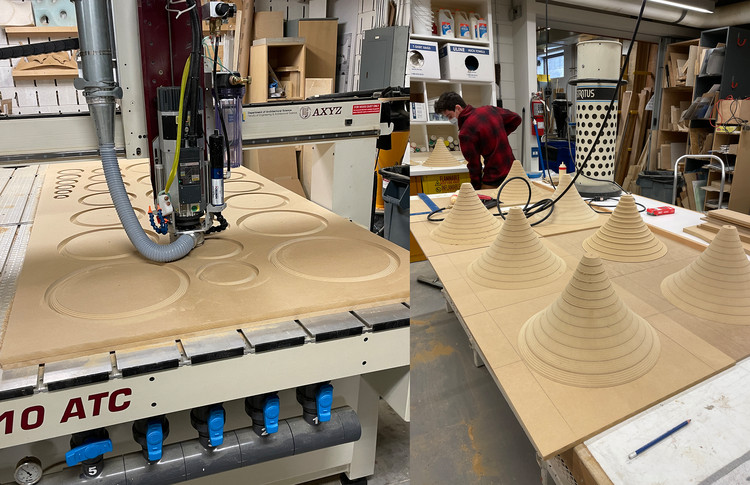
Ariel Weiss also indicated that “Where a unique textile-concrete panel might take 3-4 days to fabricate, using augmented reality the team was able to manipulate hundreds of digital panels on top of physical models instantaneously. Beyond prototype models, augmented and virtual reality was also used in order to refine errors that might’ve occurred during the design process. 1:1 scale models were projected in conjunction with physical space in order to test feasibility. In this example we learned that some cladding panels were actually impossible to install given their position.”
The three-dimensional visualization, therefore, transcends the rendering, constituting a key component for an increase in process efficiency. Although on a reduced scale, this project shows interesting possibilities regarding the upcycling of materials and, above all, innovative methods of drawing, prototyping and construction.
This article is part of the ArchDaily Topics: The Future of Architectural Visualizations, proudly presented by Enscape, the most intuitive real-time rendering and virtual reality plugin for Revit, SketchUp, Rhino, Archicad, and Vectorworks. Enscape plugs directly into your modeling software, giving you an integrated visualization and design workflow.
Every month we explore a topic in-depth through articles, interviews, news, and projects. Learn more about our ArchDaily topics. As always, at ArchDaily we welcome the contributions of our readers; if you want to submit an article or project, contact us.