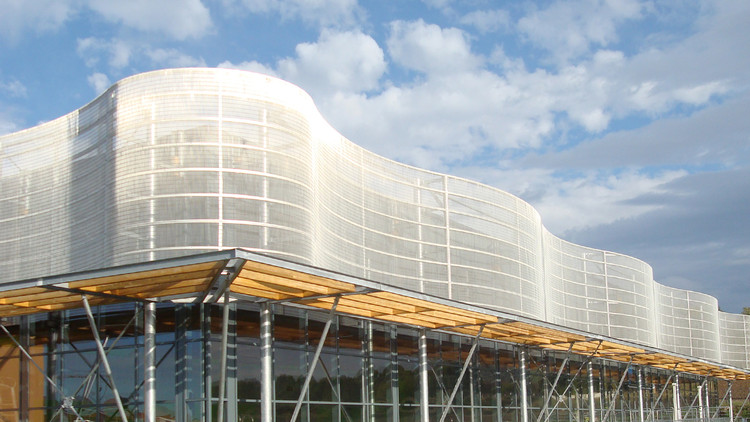
From creating a new parking structure with an awe-inspiring aesthetic to retrofitting an existing building, architectural wire mesh provides versatility and durability which makes it unique from other design material options.
What is Architectural Wire Mesh?
Wire mesh - also commonly referred to as "wire cloth" or "wire fabric" - is a versatile metal product that can be used effectively in countless applications. Popular uses for wire mesh include steel wire mesh partitions, wire mesh for building facades, and PVC wire mesh for machine guards. From industrial to commercial applications, wire mesh is a versatile metal product with unlimited potential. Often overlooked as a facade solution, wire mesh has a number of benefits and features which make it a viable construction material.
A wire mesh facade is a series of singular wire mesh panels assembled together, forming a one-of-a-kind structural exterior. In most cases, facades are installed by tensioning mesh panels to the height of the project, with substructural support at the top and bottom of the panel.
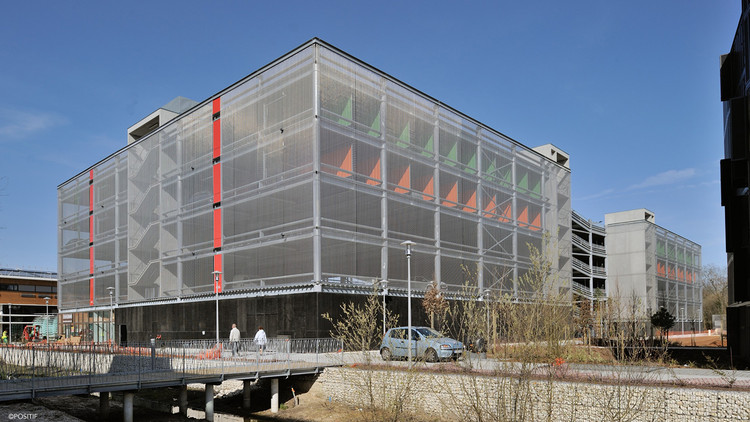
Wire mesh constructions also facilitate comfort by providing protection from the sun and absorbing sound. Manufactured from high-quality stainless steel, architectural wire mesh offers good corrosion resistance requiring minimal maintenance. Tried-and-tested fastening systems enable mounting solutions to be customized, which guarantees optimum safety in even the tallest of buildings and the strongest of winds.
Mesh elements can be tensioned over several stories using flat tension profiles, clevis screws, and pressure springs. A solid substructure for absorbing the resulting loads is required at both the upper and lower faces of the structure. Intermediate mounting is provided at each floor level by means of a round tube and wire connectors running behind the mesh.
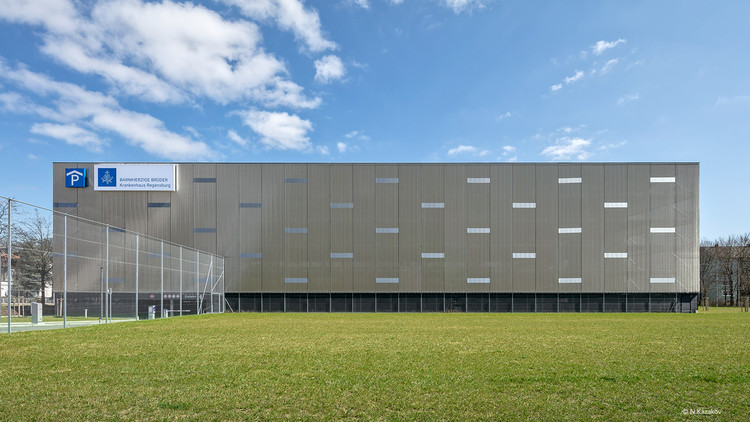
What are the Components of a Wire Mesh Facade?
The substructure, clevis hardware, flat tension profile, pressure spring, the intermediate tube, and wire mesh panels stand as the most vital.
- The substructure serves as the foundation of the facade and is attached directly to the building.
- The clevis hardware is placed along with the top and bottom flat tension profile. The purpose is to connect the mesh panel to the substructure frame.
- The flat tension profile is a clamp placed at the top and bottom of each mesh panel. These clamps allow the mesh and clevis hardware to be attached with ease.
- The pressure springs are located in the bottom or top substructure and provide a safe means of tensioning the mesh.
- The intermediate tubes are designed to provide additional support throughout the length of the facade. The specific placement of the intermediate tubes allows them to prevent the panels from moving.

6 Benefits of Architectural Wire Mesh for Facade Claddings
1. Large-Scale Surfaces: Architectural mesh can be tensioned over the full height of a building, short or tall. This reduces costs dramatically compared to other materials such as perforated plates or expanded metal. A substructure is only required at the top and the bottom mounting points. The different levels of the building require intermediate fixings that can be designed for significantly lower horizontal loads.
2. Quick and Easy Installation: Typically, the building will already have the substructure in place. This includes both the top and bottom as well as the intermediate tube holders. If the intermediate tubes, substructure at the top and bottom, and the clevis hardware attached to the substructure profile are preinstalled, the contractor will simply need to lift the wire mesh panels and attach them to the hardware, put on a defined pre-tension, and clip the wire connectors to the intermediate tubes.
3. Long Life Cycle: Architectural wire mesh stands out for its extreme durability and is almost maintenance-free due to the use of corrosion-resistant stainless steel and robust mounting technology.
4. Natural Ventilation: The transparency of architectural mesh provides a natural ventilation system. It is possible to customize the open area of the mesh so that the project-specific requirements of ventilation can be achieved.
5. Safety Feature: Stainless steel wire mesh can be used as a guardrail system for protection in spaces such as multi-story car parks or for claddings on external staircases and balconies.
6. Sun Protection: Architectural wire mesh acts as an effective sunlight protection solution, in particular, to filter incident light and reduce the warming of the building.
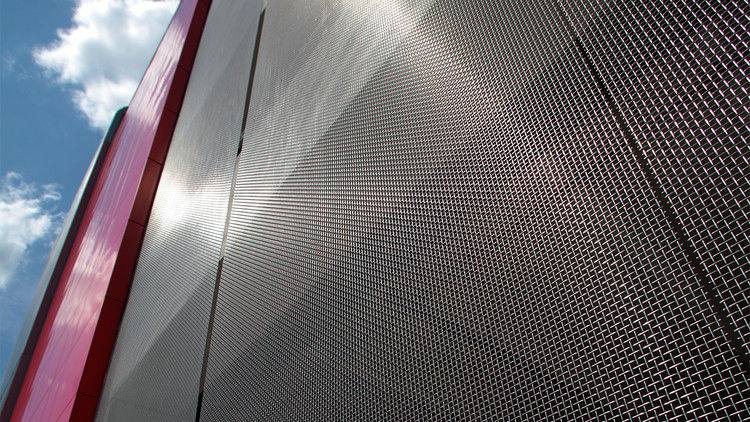
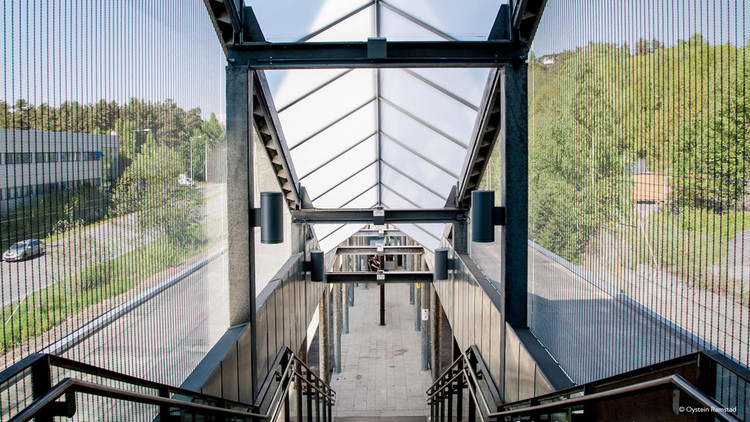
Architectural Wire Mesh Facade Mounting Solutions Explained
When it comes to wire mesh panel attachment systems, there are two primary choices: a flat tension profile attachment system and an eyebolt attachment system. But each attachment system is designed to work in specific situations with special shapes.
So, what exactly is the difference between flat tension profile systems, eyebolt attachment systems, and other special systems?
Mounting Solution 1: Flat Tension Profile
Wire mesh elements can be tensioned on multiple levels using a flat tension fastening solution consisting of flat tension profiles, clevis screws and compression springs. Especially in exterior applications, the structural characteristics require the use of compression springs. The compression springs give sufficient elasticity to the wire mesh when exposed to the respective loads, however, a solid substructure is required to absorb the resulting loads on the upper and lower faces of the facade. Intermediate mounting is provided at each floor level by means of a round tube and cable connectors that are placed behind the screen. The flat tension profile fixing solution can be used with all kinds of wire mesh panels except cable mesh panels.
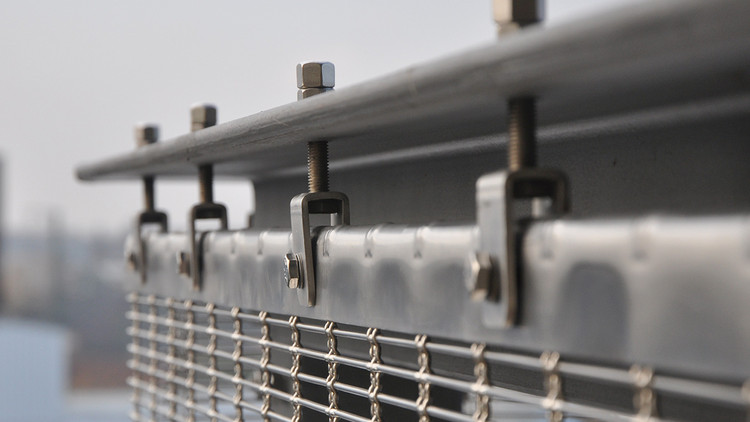
Mounting Solution 2: Round Bar with Eyebolt
With the slide-in round bar and eyebolt fixing system, wires are removed from the metal mesh and replaced by a load-distributing round bar. Eyebolts are used to clamp the stainless steel mesh to a substructure. This fixing system is suitable for cable mesh with groups of warp wires.
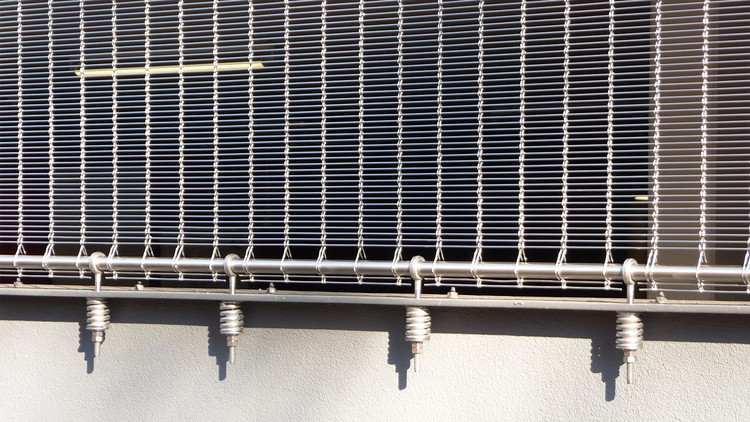
Mounting Solution 3: Special Shapes
Each project has its own specific requirements. Whether curves, angled edges, or cut-outs, special mounting solutions can also be implemented. They are individually determined and implemented with planners and contractors.
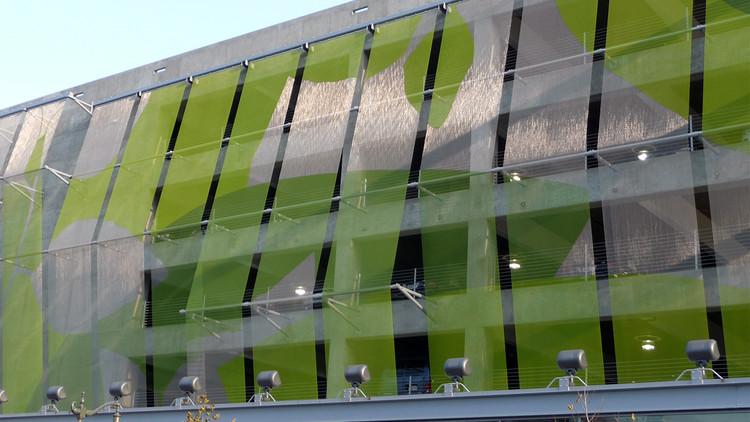
How To Maintain a Wire Mesh Facade
Once the wire mesh facade has been installed, minimal maintenance is required. Tension adjustments are not necessary if installed properly; however, yearly visual checks are mandatory. As far as cleaning is considered, the stainless steel qualities of the mesh allow most debris to be washed away by rain.
To learn more about wire mesh as an architectural facade solution, click here.
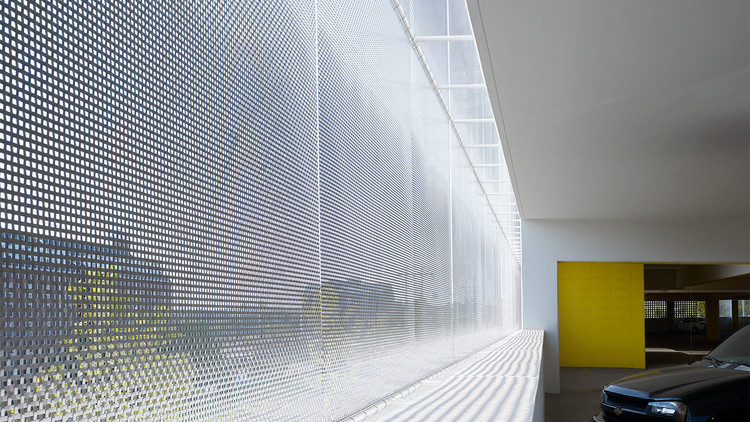