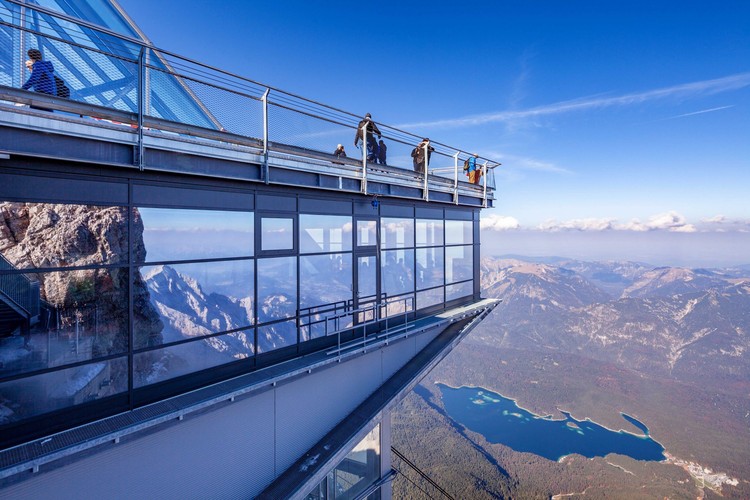
While glass is generally singled out as the weakest part of a building, it is not always true. With technological advances and the continuous innovations of the industry, there is glass that, even while allowing natural light to enter an environment, can protect the building from fire. Beyond fire, there are also other threats such as hot gases, smoke, and heat transmission, which put the safe evacuation of people and the protection of property at risk.
Building codes in most countries define the required level of protection of building materials, parts, systems, and other elements classified for fire resistance and reaction to fire (flammability). Normally these requirements are set out in the relevant laws, standards, or technical instructions and vary depending on the building type, its use, height, and the number of occupants who could be potentially threatened in the event of a fire. In Europe (European Norm EN13501-2. E / EW & EI) fire-resistant glazing is categorized into three classifications.
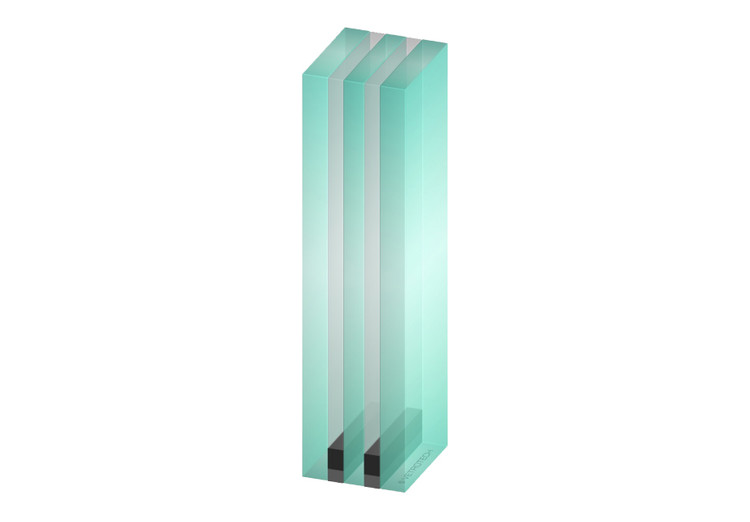
1. *E* Integrity or “E” is the ability of a construction element with a separating function to withstand fire exposure, without the transmission of fire to the unexposed side as a result of the passage of flames or hot gases. This may cause ignition either of the unexposed surface or to flammable materials adjacent to that surface. Category E represents the ability of the glass to symmetrically withstand high thermal stress and prevent early breakage due to its high tempering.
Using tempered glass is a type of safety glass manufactured with the aid of heat or chemicals used to strengthen the glass. This process is sometimes referred to as “tempering.” Tempered glass can be up to four times stronger than typical annealed glass of the same size and thickness. Other benefits include more tensile strength (it can bend easily without breaking), wind resistance, and if it breaks, tempered glass shatters into rounded cubes rather than pointy shards. This is perhaps the most important pillar in determining the safety of glass in the event of a fire emergency.
2. *EW* Radiation “W” is the ability of a construction element to withstand fire exposure, so as to reduce the risk of fire transmission as a result of radiated heat. The element may also be required to protect people in the vicinity.
The Radiation Control factor is an important part of this classification. Thanks to a special heat-reflective coating that offers partial radiant heat reduction, it is possible to prevent fire from spreading and create safe evacuation passages.
3. *EI* Thermal Insulation “I” is the classification for full heat insulation, providing the highest level of protection from fire. EI-classified fire-resistant glass compartmentalizes fire for up to 120 minutes.
Below, we review Vetrotech Saint-Gobain's passive fire protection glass solutions, capable of effectively resisting such threats and saving lives.
Zugspitze Mountain Station / Eibsee, Germany
In July 2018, the conversion of the mountain station for the new Bavarian Zugspitze cable car line was completed with the opening of the Panorama 2962 summit restaurant. Designed by Hasenauer Architects, the new extension of the building on Germany's highest mountain offers spectacular panoramic views thanks to expansive glazing. Its fire-resistant glass panels ensure safety at the mountain station. The production, delivery, and installation of the glass demanded tremendous efforts from everyone involved.
The main challenge was to equalize the pressure in the glass between interior and exterior, in the highest construction site in Germany, just under 3,000 meters above sea level, where 176 square meters of Contraflam glass panes were installed in this harsh environment.

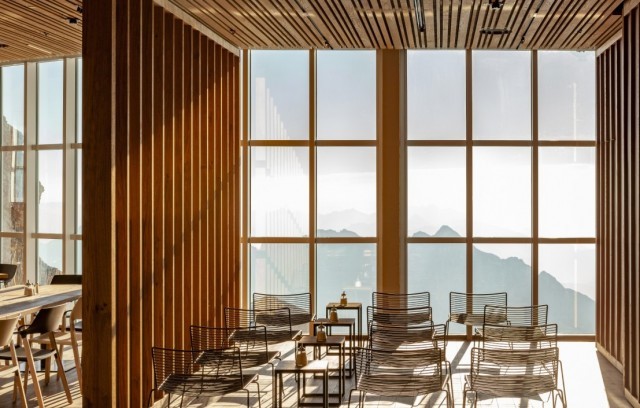
Westland Distillery / Seattle, WA, USA
The centerpiece of the Westland Distillery in downtown Seattle isn’t just the single-malt whiskey – it’s the gleaming, colossal copper and stainless steel stills. Due to local regulations, a two-hour fire enclosure was required, which didn’t permit the owners to showcase their equipment in the tasting room the way it would deserve to be shown. Rather than relegate the stills – which are the largest west of the Mississippi – behind walls, architects at Urbanadd turned to Vetrotech for a solution that would meet fire safety requirements but still allow visitors a free view to the inside of the distillery.
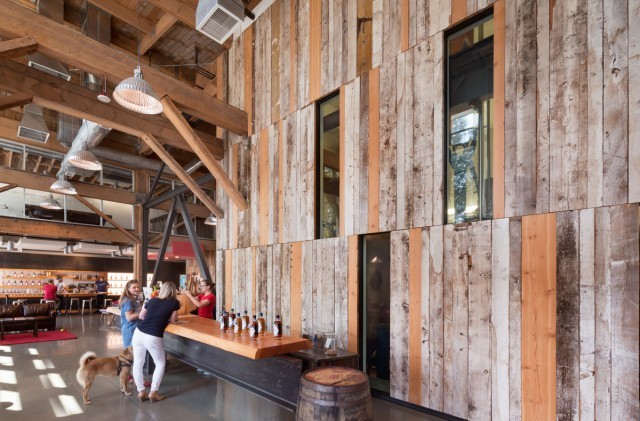
The resulting three-story interior enclosure is comprised of metal studs and multiple layers of drywall and wood sheathing. The interspersed panels of Vetrotech Contraflam 120 fire-resistant glass in VDS frames allow the wall system to meet two-hour fire safety requirements while keeping the unique distillation process in full view for visitors.
The distillery was looking for an elegant solution that could allow visitors to view the inner workings of the plant. Regulations require stills to be behind walls. Needed to block radiant heat, yet still provide for high light transmission and visibility, Contraflam was a unique solution that incorporated safety, regulations, and aesthetics.
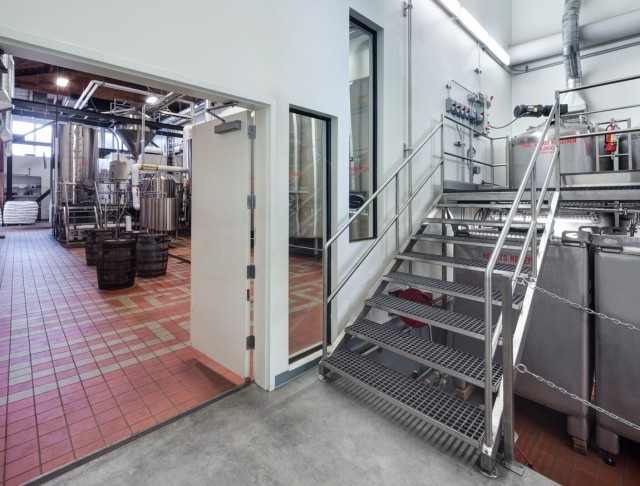
The Texelstroom (TESO) / The Netherlands
Perhaps the most unique application of Vetrotech is the Texelstroom – a ship built at a cost of almost €56 million – that links Den Helder on the mainland and the island of Texel in the Netherlands. TESO has sailed in this area since 1907 and has a total of 15 vessels that are used for the crossing between the island and the mainland. The new Texelstroom has the capacity to hold 1,750 passengers and 350 passenger cars. Thanks to the innovative energy management system onboard, the motor of the ship runs on CNG (compressed natural gas), instead of diesel.
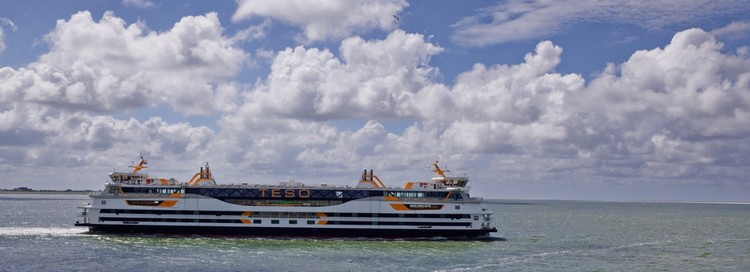
Furthermore, it features 700 m2 of solar panels installed on the roof and a water recycling system to flush the toilets. The company supplied insulating glass as double-glazed units with a low-E coating. Some were processed with a special screen-print to protect the glued joint from UV-rays. Heated glass panels (Thermovit) were also used for the wheelhouse to prevent the glass from freezing over and misting. In order to protect the people and infrastructure in the event of a fire, Contraflam fire-resistant glass was installed in various applications.
The production of the panes was one of the projects' main challenges since almost all required very unique individual diamond shapes. In total, approximately 1400 m2 of Contraflam A0 and A60 DGU glass with Planitherm XN II low-emissivity coating and Thermovit (heated glass) were installed onboard TESO.
"The biggest challenge was the extraordinary size and unique shapes of many of the glass panes. Kinon was able to fulfill this very complex demand with the use of a maximum of machine and processing capabilities available on site," said Fabio Otto of VetroTech's Kinon production facility in Germany.
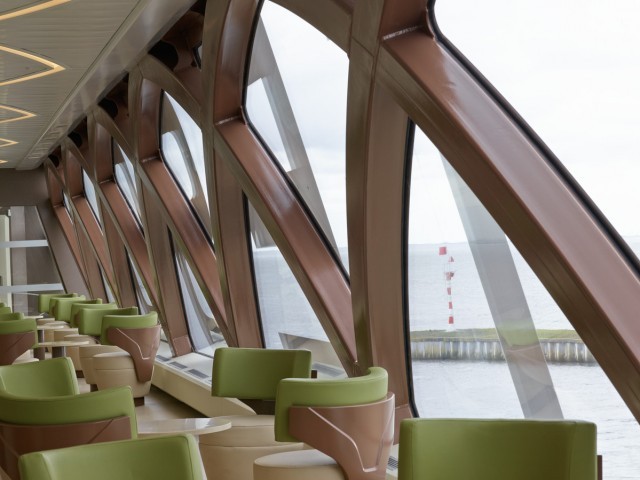
Med 360 Headquarters / Leverkusen-Manfort, Germany
At the end of June 2018, the new Med 360° company headquarters (the central administration of its service areas) was moved to Leverkusen-Manfort. At the heart of the light-flooded building is the 225 m2 glass atrium, providing employees with bright and open workplaces and protecting them from fire and heat at all times, thanks to the Contraflam EI 30 fire-resistant glazing.
The interior offices house a total of 250 employees, located around the atrium, who are supplied with natural daylight thanks to the large glass surfaces (which also provide beautiful views of the center of the building). Some of the space was designed as "open-space" offices with multifunctional zones, others as larger individual offices. Further areas offer various functionalities including meeting rooms, lounges, telephone booths, etc. Medicke Fassadentechnik GmbH installed a total of 339 m2 of Contraflam EI 30 fire-resistant glass in the atrium, 172 m2 of which was used as fall-protection glazing and a further 22 m2 with an alarm, providing secure access to the offices to prevent unauthorized entry.
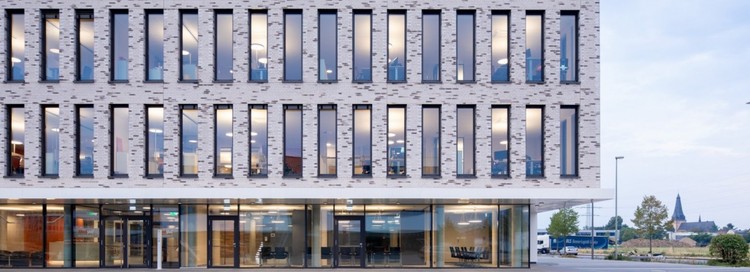
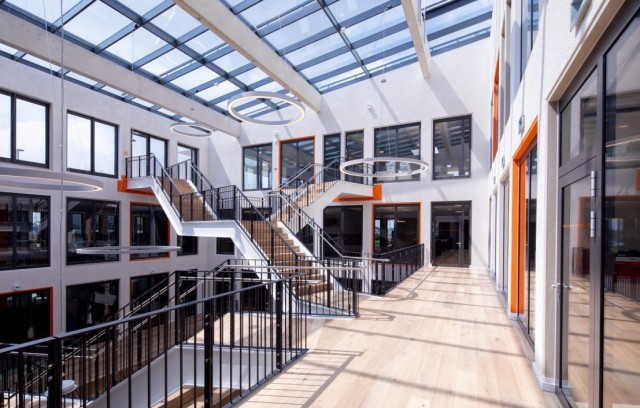
To see more projects by Vetrotech Saint-Gobain, click here.