It is difficult to find someone who never played LEGO as a child. What if, like LEGO's, we thought of buildings as great assembling games? U-Build is a modular wooden construction system developed by Studio Bark to be easy to build, pleasant to inhabit, and simple to deconstruct at the end of its useful life. The system removes many of the difficulties associated with traditional construction, enabling individuals and communities to build their own homes and buildings. The system uses precision CNC machining to create a kit of parts, allowing the structure of the building to be assembled by people with limited skills and experience, using only simple hand tools.
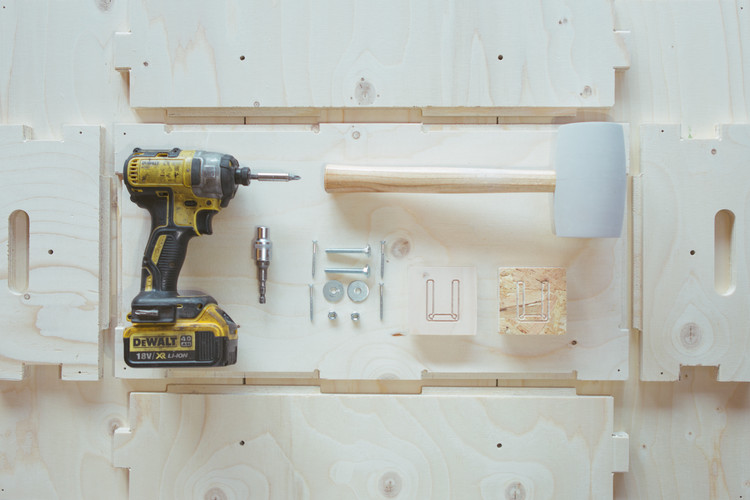
According to the architects, the design principles of U-Build arose from the desire to make construction truly accessible and self-built, opening the practice of self-managed construction to the greater public. Rather than relying on conventional single-use materials, the U-Build system is reusable, environmentally responsible, and incredibly economical, without sacrificing quality. Read, below, an interview we conducted with Nick Newman, Director of U-Build:
Eduardo Souza (ArchDaily): Can you explain what U-Build is, how it works, and what the intentions were when creating this system?
Nick Newman (U-Build): U-Build is essentially a system of giant building blocks. They arrive flat packed, are assembled into 'human-scale' boxes, and are stacked up to form walls, roofs and floors: the fundamental building blocks for any design project. U-Build is designed using parametric computer software enabling complex designs to be coded into simple components, and 'cut out' at a local CNC workshop, following distributed manufacturing principles.
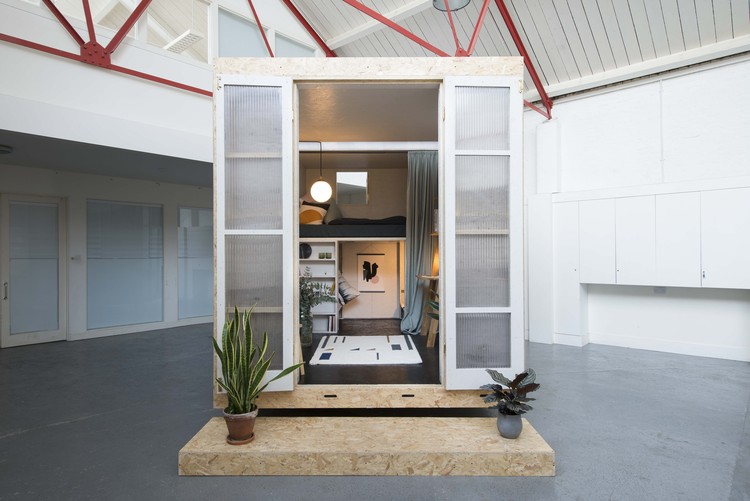
U-Build's aim is to make construction simple, and accessible to a much wider range of people. We have had 3 year old and 80 years building boxes, and people with no prior experience of construction.
We think that inclusion and empowerment are the best ways of improving our societies. How can we build back better, when we don't know how to build?
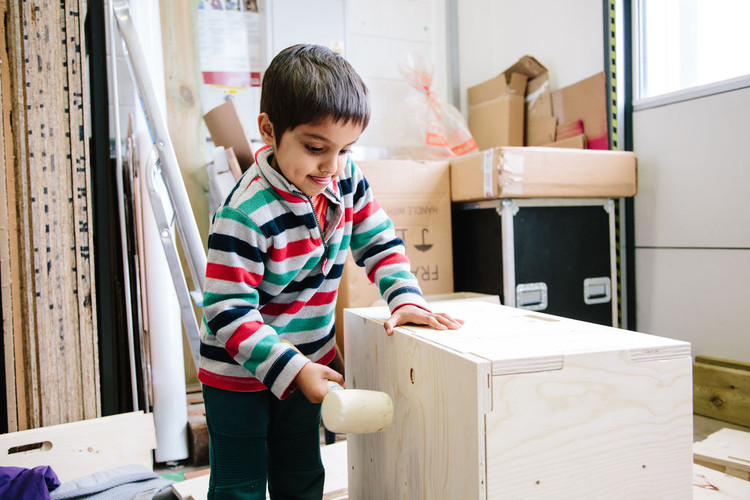
ES: What materials are used?
NN: We use plywood for the main frame, natural insulation (sheep wool / wood fibre), and locally sourced cladding materials. We also use galvanised bolts and screws for the connections, butyl rubber for the roof, and a UV stable breather membrane.
There is no perfect material for building, but we think that wood comes pretty close.
_Lenny_Codd.jpg?1615379439)
ES: What other sustainable solutions can be incorporated into the system and how?
NN: One of the main principles behind the system is that the individual elements can be taken apart again. This means that there is much less waste, which has a big impact on embodied carbon calculations. The system is also designed such that it does not need a concrete foundation, or plasterboard walls, which allows a big saving in CO2.
ES: What were and still are the main technical challenges?
NN: You would think that it is very easy to design a stackable box, but in fact this has been the hardest challenge. We have needed to prove that the system works structurally, solve airtightness issues, optimise the parts for manufacture and yet make it all easy to assemble. We have solved a number of these issues using prototypes, parametric software, and collaborations with innovate consultants such as Structure Workshop. As a self-funded startup, the main challenges to overcome lie in certification for the mass market, but really the obstacles are the high cost of these tests, rather than the technical ones.
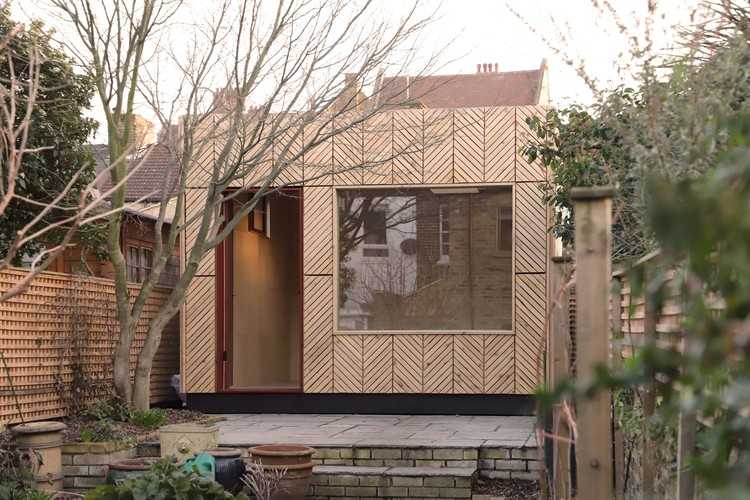
ES: Up to what scale does U-Build offer to build? And in relation to construction costs, under what conditions is it viable?
NN: U-Build in its current form can be built up to 3 storeys in height. The roof system can span around 5 metres without using external beams, or 6m plus if beams are incorporated.
In terms of construction cost, we are aiming to provide high quality at a standard price, rather than standard quality at a budget price. It is great that we are able to do this already, given that we are a startup business, but we see ways of making big savings as volumes increase. There are also ways to make it cheaper on a small scale, for example if a community has access to its own CNC machine.
ES: What is the level of freedom in the project? What are the possibilities of different design configurations?
NN: This is where we think that U-Build comes into its own. The modules work to increments of 150mm, so they can be set out in a wide configuration of options. We focus primarily on rectilinear designs, which are the easiest for people to build and have the maximum material efficiency. We do also make pitched roofs, and bespoke pieces, but the key for us is to make sure that they are still straight forward to assemble, and disassemble. As we iterate new versions of the software algorithm, we increase the functionality each time.
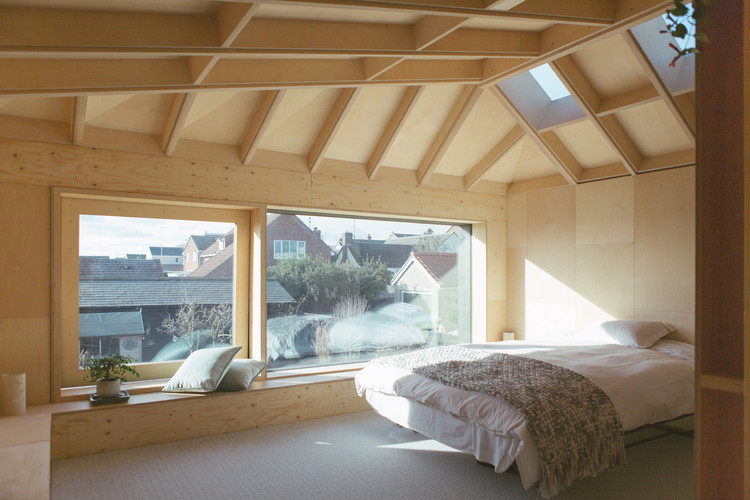
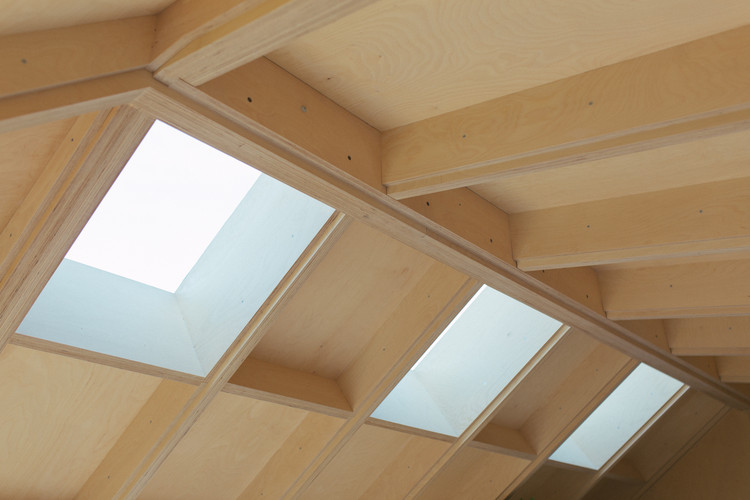
ES: How can the system contribute to improving access to housing in dense cities? And how does it relate to the circular economy?
NN: In the wake of the pandemic there are a large number of empty office buildings and spaces which are being underutilised. Non-permanent buildings solutions enable people to occupy spaces that would not have been affordable using a conventional single use materials. If the client owns the elements of the building, they become assets, which can be taken with them. This means that buildings are no longer the preserve of the landlord, they can instead be owned by the tenant. Many people describe this as circular economics but we just think it is common sense.
_Lenny_Codd.jpg?1615379536)
ES: Since the idea is to give the client more and more autonomy to create the project and build, what will be the role of the architect in the future, in your opinion?
NN: We are not replacing the design community, we are simply upgrading their building blocks. We are already working with a number of practices who see U-Build as a way of delivering their client's projects with better cost certainty, flexibility and environmental performance.
We feel that by increasing the ability for clients to engage in the build process, they become more likely to understand the benefits of good design, and invest more into the design community.
Studio Bark is a pioneering architecture firm based in London, offering ambitious environmental architecture with a practical approach to research, design and construction. In 2018, they were named AYA ‘Sustainability Architect of the Year’. The team combines rigorous environmental principles with an elaborate contextual approach, working closely with clients to realize their aspirations. Find out more about the office on its website, and get more information about U-Build at this link.