.jpg?1582834753)
Craftmanship is back. Following a century of mass production and industrial development, crafts are starting to be revalued and reinterpreted. A new sensitivity towards raw materials, the recovery of local techniques and the defense of small-scale trade are a few of the claims that this comeback represents. Materials such as earth and ceramics, textiles and wood are being reinterpreted by designers, artists, and architects around the world, in search of both their own style and the representation of collective nostalgia.
However, today there are new ways to respond to those old needs. Although an important part of the trend is the recovery of manual manufacturing techniques, today there are technologies that allow emulating these processes in less time and on a larger scale. Is it a new industrialization process? Additive manufacturing, already in use since the 90s, allows the materialization of precise organic forms designed for specific contexts. As an option halfway between uniqueness and the masses, 3D printing has the ability to extend the craft beyond manual labour.
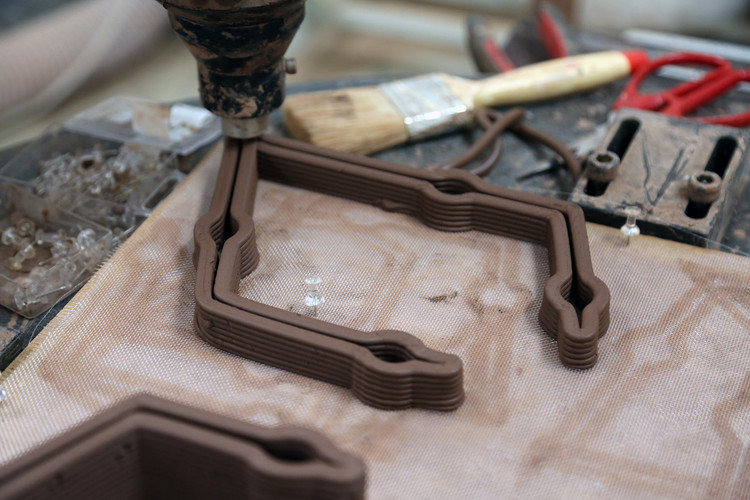
Can 3D printing be considered craft?
It depends, of course, on whether we consider the definition of craftsmanship from the point of view of the manufacturing process or the object itself. The definition and understanding of an object are not exempt from their productive origin, translating into the object concepts of identity and an attitude towards the material. The comeback of the artisanal reflects a change in our disposition towards the natural environment, reflected in an explicit imitation and an abstract allusion to the need for nature. From texture to form, the need for nature has been synthesized in the concept of biophilia, an irrational impulse -some would say instinctive- for establishing a direct relationship with local materials and emulating an ambiance that would improve the human experience in space, impacting even in health.
What are the characteristics of 3D printing that would allow this approach to objects?
-
Additive manufacturing allows unsuspected precision by emulating a digital model. Both the software and the precision of the machine allow the creation of unique objects, preserving both the organic and precise shapes and the superficial imperfections in the final object.
-
Layer manufacturing combines the transmutation of a digital form with a manual control process: changes can be made during the production process, unlike other traditional manufacturing processes such as moulding.
-
While it is not yet globally attainable, it is accessible technology. For about two decades the development of software and machinery for this type of manufacturing has moved from the exclusivity of industrial prototypes to the ability to produce everyday objects, being able to respond more and more to the trend of DIY (by combining ornament and structure) and enabling a cultural adaptation to the technique and its associated aesthetics.
-
3D printing combines aesthetics and sustainability by allowing the use of greener base materials. If we consider the material and the techniques we have to process it as essential factors of the environmental impact of production, this characteristic places this new technique as a valid option when facing a climate crisis.
3D printing methods are now instruments for the artisanal claim for producers and designers, as its broadest value is the possibility of resignifying the machine, the material and the concept of craftsmanship itself. Although it is not easy to perceive as equivalent, this seems to be the ideal time to overcome the fetish of the purity of traditional materials to make way to other substances and techniques that will allow us to ease the load on highly exploited natural resources and re-encourage local production. Additive manufacturing is a tool to compete with generic aesthetics and mass production in the market, as long as we make our way to a much more unexpected architecture.
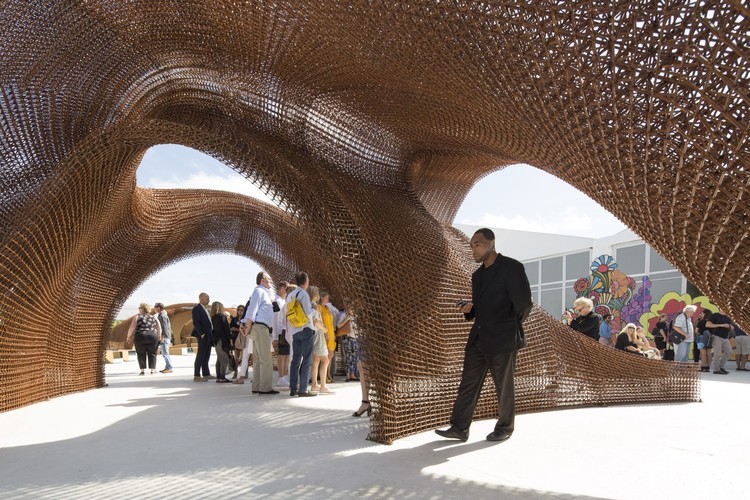