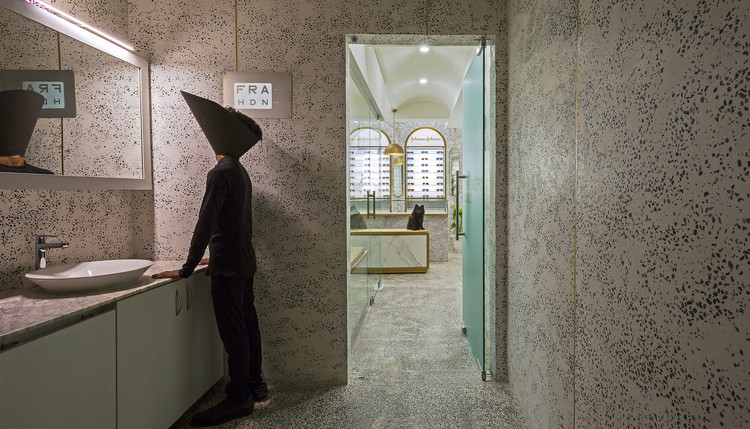
Terrazzo is made by combining a cement base (sand, water, and cement) with a mixture of ground minerals - like marble, granite, and quartz - and can be applied to almost any surface, vertical or horizontal. The technique, produced using a completely hand-crafted method, was used worldwide in the construction of modern buildings and is noted for its durability, resistance (to water and abrasion), and easy maintenance. This made it a go-to material in the creation of flooring for houses and the common areas of residential and office buildings.
Today, terrazzo is experiencing a revival as one of the key trends in contemporary architecture. Here, we will discuss the whats and hows of terrazzo and illustrate some of its uses in current projects.
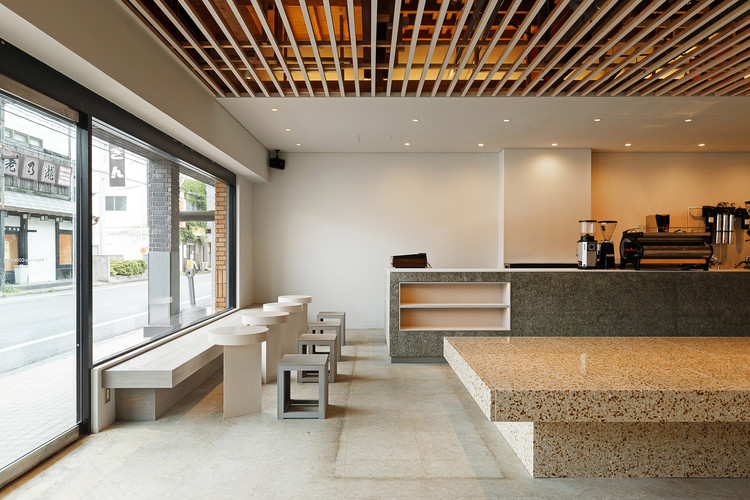
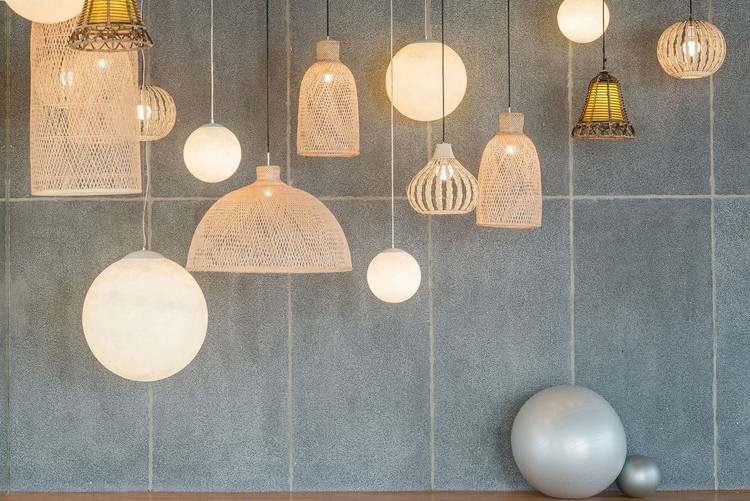
Terrazzo offers a wide range of aesthetic options based on the size, type, and color of stones used in the mixture as well as the type of finish used (polished or washed).
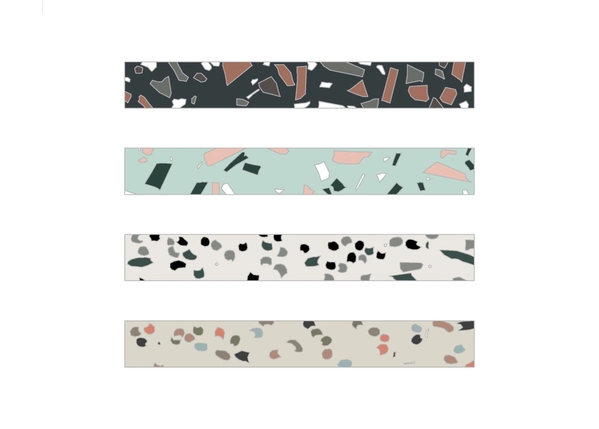
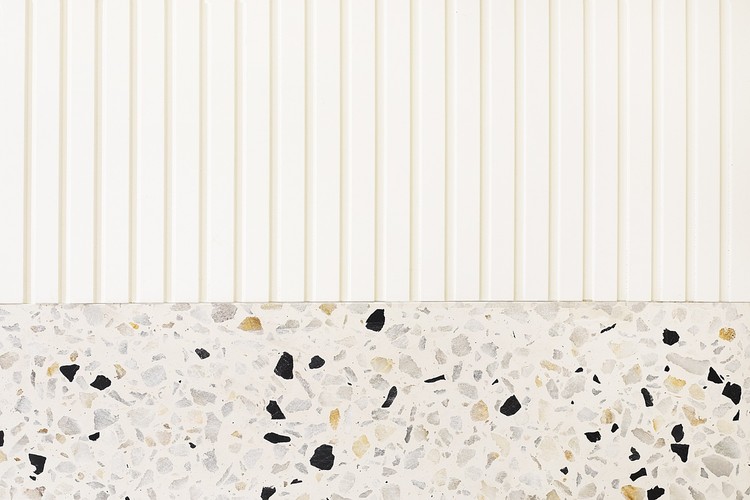
Application
There are two kinds of finish for terrazzo: polished and washed (or "fulget") and both can be applied to any surface, no matter if it's flat or curved. Polished terrazzo is seen mainly in dry, indoor spaces while washed terrazzo is used for wet, outdoor spaces.
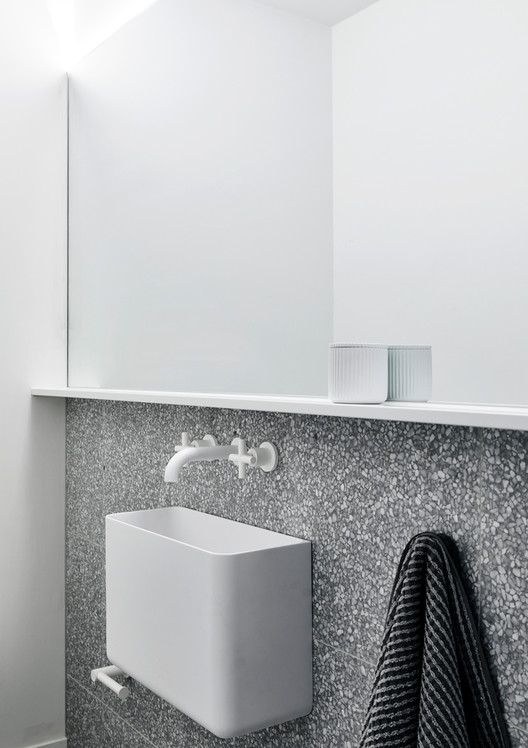
Fabrication
Terrazzo is a type of facing that is molded in situ or "on site." This means that it is applied immediately to the desired surface. This can present challenges since, once applied, it's impossible to correct any flaws in the base layer.
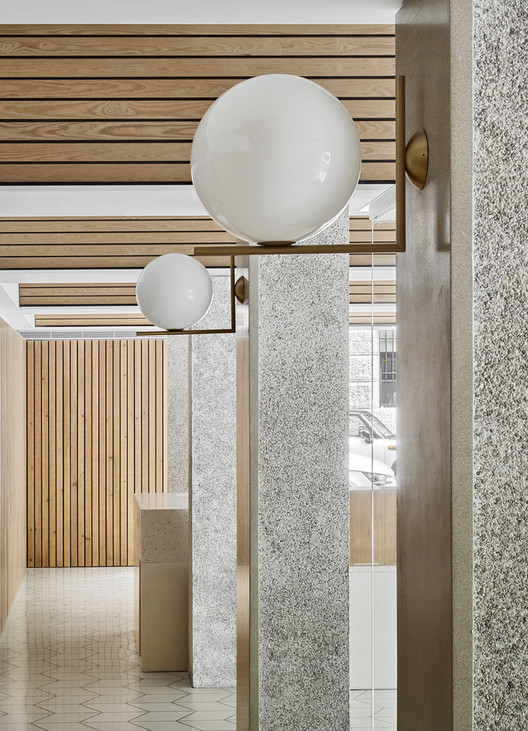
Composition
Terrazzo consists of a mortar made by mixing cement with ground marble. The mixture's exact composition depends on its use. For example, it's 50kg of cement to 80kg of marble for floors and 25:40:80 kg for walls (in this case lime is added). Color is added based on a project's specific requirements and it's possible to opt for different additives like sandstone, glass, and other stones. It's always a good idea to consult with suppliers about the properties of each mineral, especially regarding their resistance.
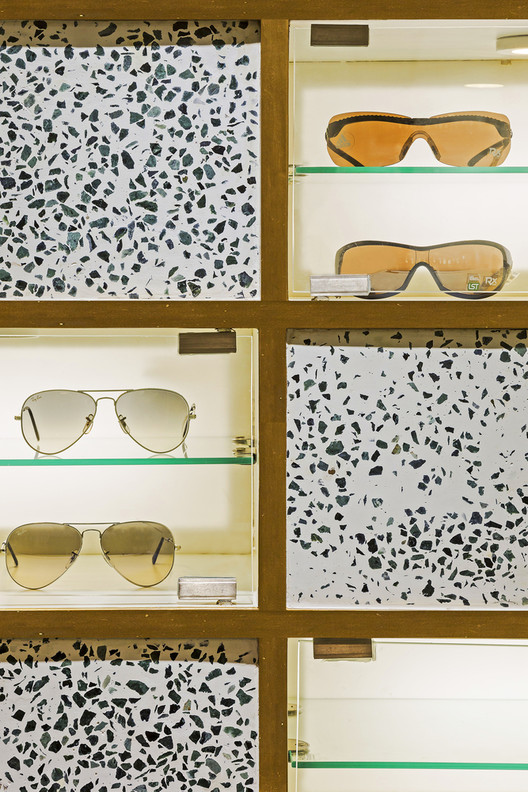
Installation
On top of the precautions that should be taken when installing the majority of facings found on the market today (an incline between surfaces, surface roughness, base adherence, a surface's impact resistance, a slope in a wet area or the flatness of a dry area) you should also consider the different processes involved when applying terrazzo to either floors or walls.
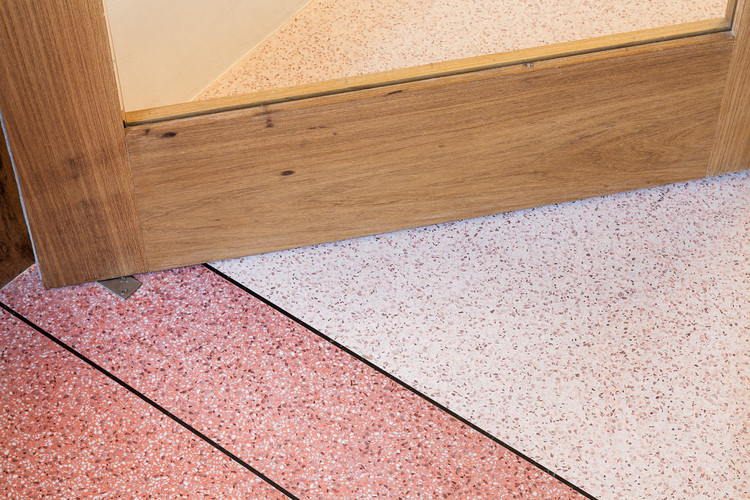
Floors
- Prepare the level of concrete surface according to the finished floor, decreasing the thickness of the terrazzo in accordance with the granulometry of the mineral being used in the project.
-
- Clean and wet the concrete surface.
- Apply a wet 3-5cm layer of levelling consisting of washed coarse sand and cement. The proportions of the mixture should be 4:1kg. The resulting surface should be flat, compact, with no depressions or protrusions, and should have the necessary gradient.
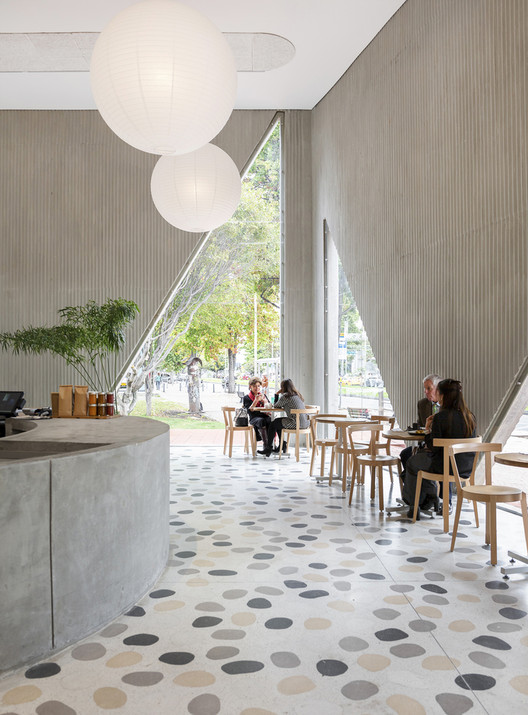
Walls
- Clean and wet the plaster surface.
- Apply a wet 3-5cm layer of leveling consisting of washed coarse sand and cement. The proportions of the mixture should be 5:1kg. The resulting surface should be flat, compact, with no depressions or protrusions, and should have the necessary gradient.
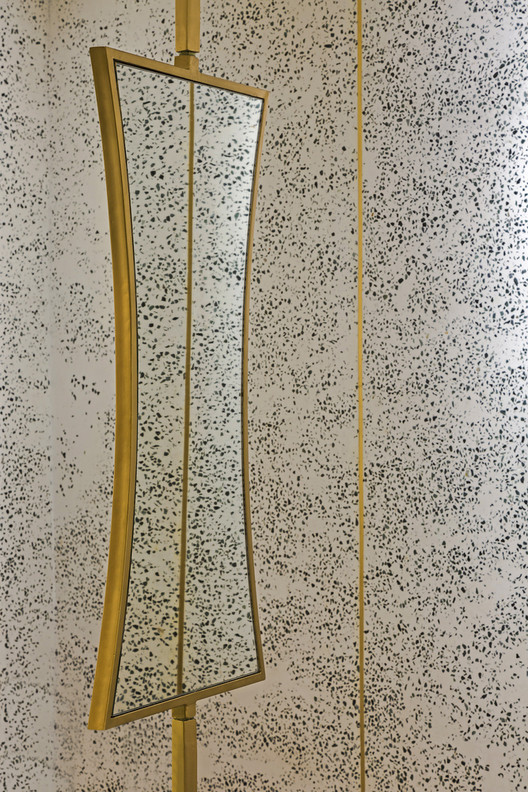
Installation Steps
- The surface should be washed and clean.
- Plastic or metallic terrazzo divider strips should be placed for each application, ensuring an even surface (the size of the dividing strips should be determined by the granulometry of the stones or the specific project requirements).
- An important detail is that terrazzo facings should be applied using maximum 1.2 x 1.2m panels, contained using rectangular dividers, made of brass, plastic, aluminum, or wood, that will be removed once the terrazzo is laid. It's a good idea to use a 1x1m modulation to ensure an even result for the facing.
- After placing the dividers, the level layer should be wetted to ensure the facing's adherence to the base.
- The terrazzo mortar will be applied and spread over the base. When the mixture has higher granulometry, the layer should be compressed using special tools or machines.
- Finally, the terrazzo mortar should be smoothed.
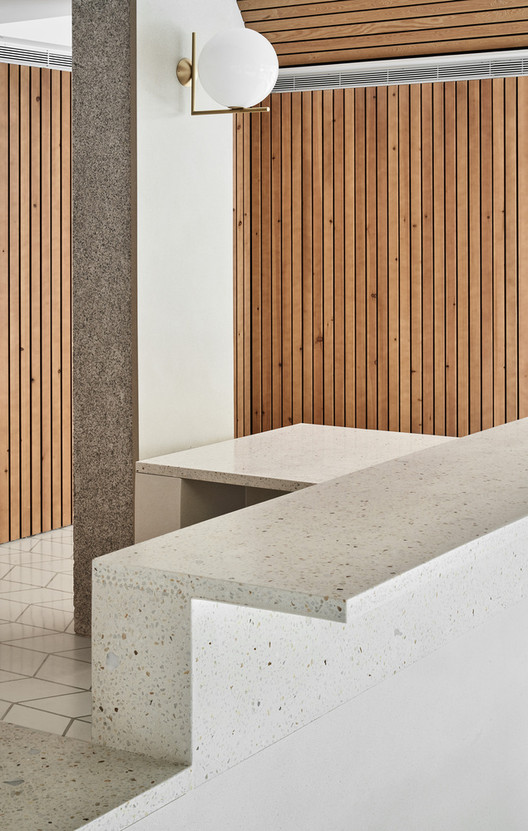
Finishes
Polished Finish
After letting the mixture dry (for 5 to 7 days), the first round of mechanical polishing can begin. Next, the floor should be cleaned completely to apply the stucco, correcting any flaws along the way. Wait another 2 days before removing the excess stucco. On top of this, it's necessary to do a final polishing, manual or mechanical depending on the project. For the resin application, the floor should be completely clean and dry. The estimated time to begin applying the resin is 5 to 7 days (acrylic resin) and 20 to 22 days (polyurethane resin) in order to let the cement dry and set.
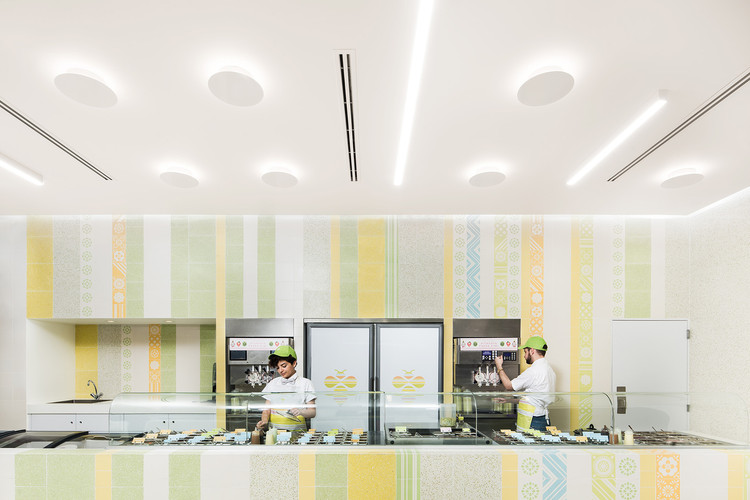
Washed Finish (Fulget)
After drying, the facing will be sponged to remove the excess cement. After 2 days, an acid wash should be applied to clean the stones on the surface.
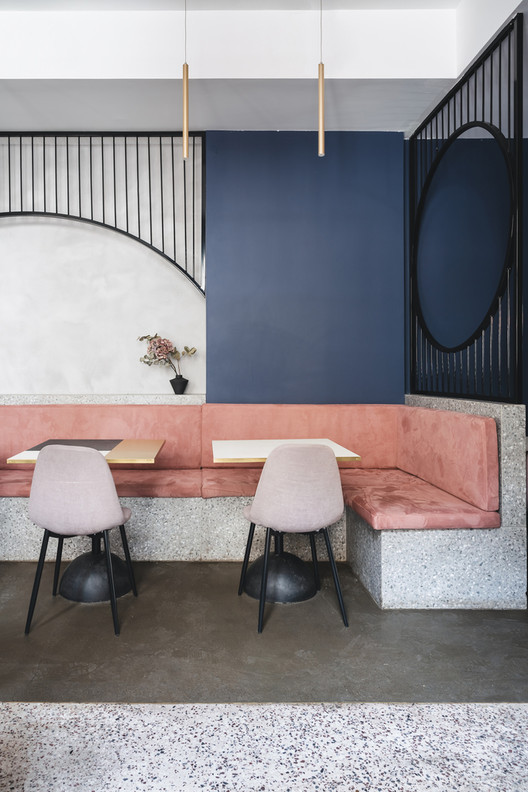
Maintenance and Care
Polished Terrazzo
Regular cleaning should be done with neutral detergents or soap powder. Never use bleach or other acids. The frequency of waxing will be determined by the use and traffic over the surface. After applying the wax, apply a sealant for better crystallization.
Washed Terrazzo (Fulget)
Cleaning with a machine or other automated system should be done using settings that evenly disperse the cleaner. Never spot clean and use only neutral detergents or soap powder. Avoid using bleach or other acids.
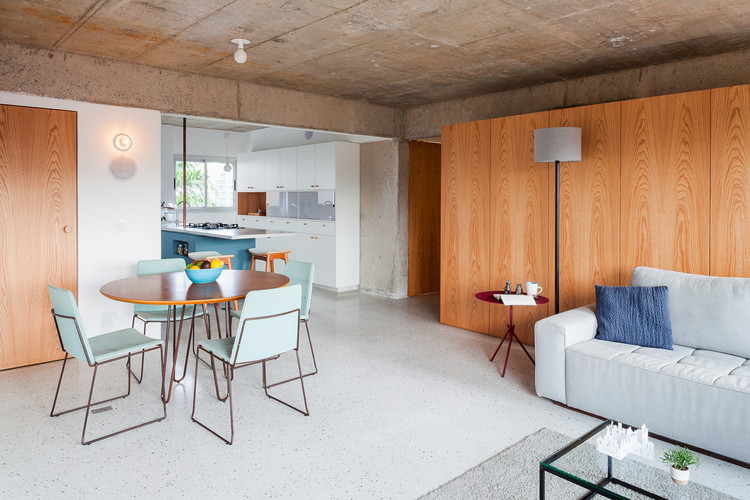
Important Observations
As we mentioned before, terrazzo is produced and installed using a completely handcrafted technique, meaning that, no matter how precise and careful the application, cracks and other imperfections are likely as well as uneven coloring in the rock and cement mixture.
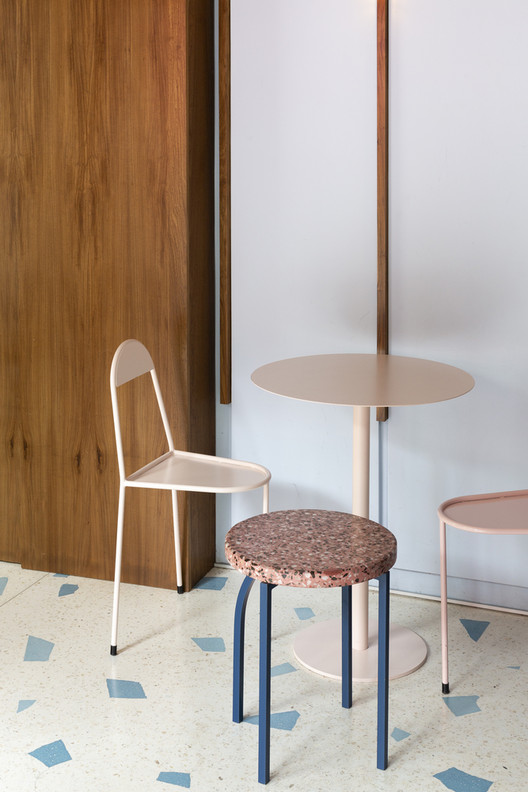
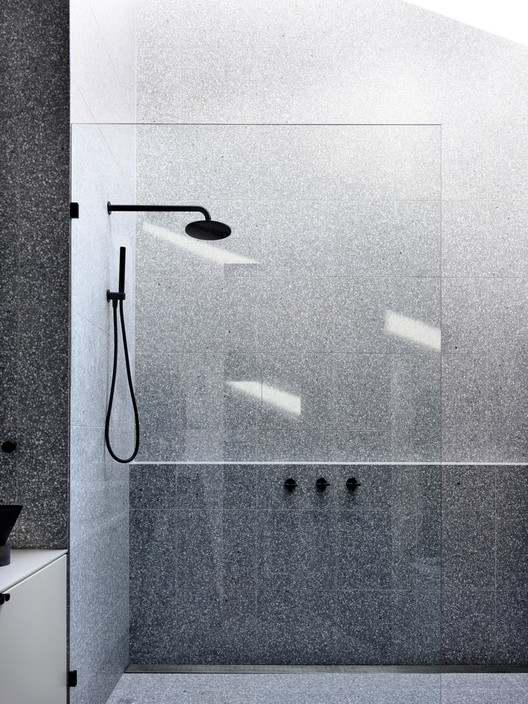
References
[1] "Technical Specifications for Terrazzo and Fulget", disponível em <https://casafranceza.com.br/granilite-e-fulget/>. Access May 14, 2019.