
Each material has its own peculiarities and, when using it for building, the design and construction process must accommodate these characteristics. A steel-framed building, for example, must be designed with a certain level of accuracy so that components and parts, usually manufactured off-site, fit together during assembly. A wooden building can have its cross sections drastically modified according to the species and strength of the wood used, or even according to the direction of the loads in relation to their fibers. With bamboo, no pole is exactly the same and each one tapers and curves differently, which requires a different approach when designing and building.
But how is it possible to work with a material with so many challenges and possibilities?
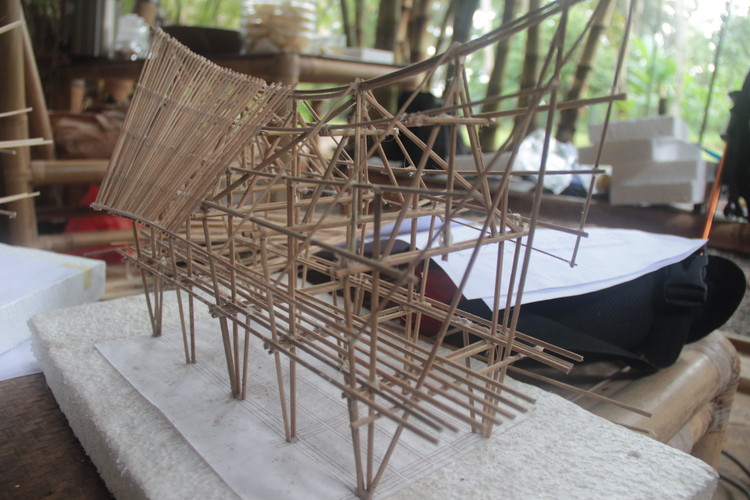
Building with bamboo requires, above all, a new way of thinking about the project and the work. According to Ewe Jin Low, a lead architect at IBUKU, "to learn how to build with bamboo, you must rather unlearn a little of architecture." This does not mean that it is necessary to forget what you have learned during college, quite the contrary. It concerns understanding the material and respecting its peculiarities, its natural irregularity, the way it grew and even how it was cut. In other words, unlearning means leaving behind some preconceived ideas about architecture and admitting that a bamboo building will never be accurate to the millimeter, will never have perfectly round dimensions, and it is therefore impossible to think of it structurally as you would think of concrete or steel. A designer must take into account that a natural and raw material such as bamboo has memory, has differences in color, size, and strength—and therein lies its beauty.
Along with sketches and conceptual images for reference, models play a vital role in the design process of bamboo projects. As well as being very important during the design of a new building—in volumetric and structural studies—they are the main documentation of the projects developed by the IBUKU office. Generally created at a scale of 1:50 or 1:25, sticks are used which are scaled according to the sections of each species of bamboo to be used in the constructed building. When the design is finished, approved and ready for construction, two identical models are made. One goes to the site and the other stays in the office, in case of loss or breakage. What is more interesting is that the model, constructed in the same material, behaves structurally in the same way as the constructed building, and through it you can test issues such as structural spans. During construction, the model is often revisited so that dimensions can be verified, or doubts can be resolved.
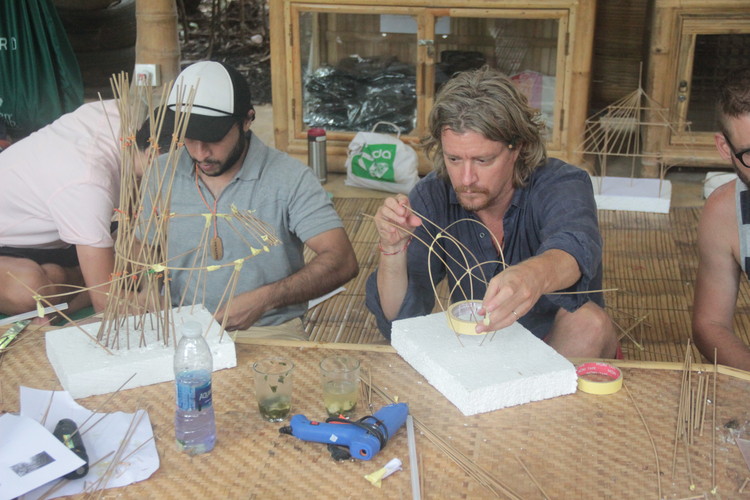
The organic forms developed in IBUKU's projects are generally best represented in scale models, where one can clearly see all the structural components and how they work together. The models are both a design element and a form of documentation for the construction. However, "traditional" technical drawings are also developed. Sections and floor plans are important, especially for the interiors, for the electrical and plumbing installations, and for sending to other professionals involved in the project.
During the Bamboo U course, participants were able to work with bamboo models, developing pre-designed models and also developing their creativity through their creations. In this way, they were able to better experience and understand the characteristics of bamboo, its elasticity, resistance, and potential. At the same time, a skilled model-maker was developing the final full-size construction model during the final days of the course with the help of the participants.
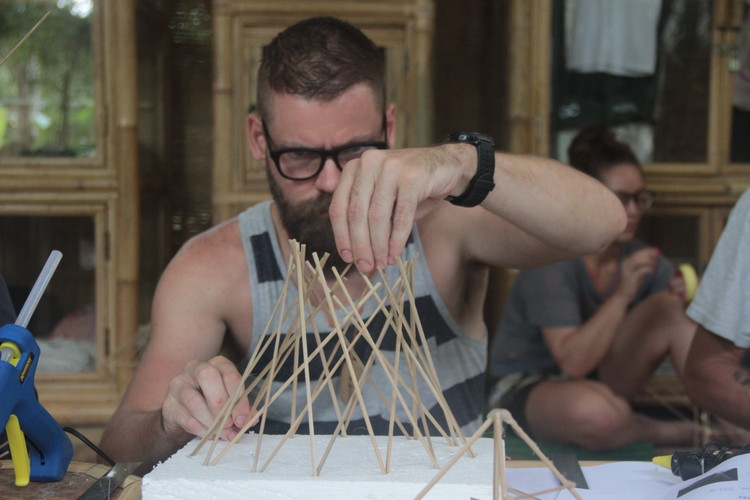
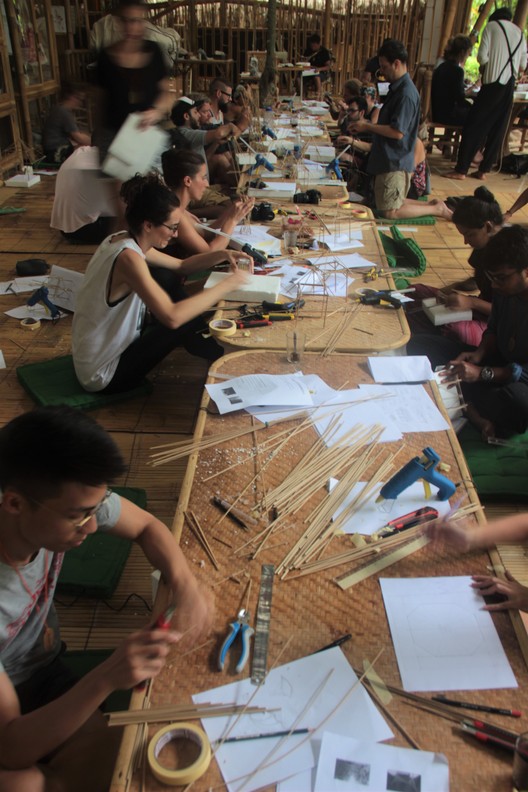
Two of ArchDaily's editors, Eduardo Souza and José Tomás Franco, were invited by BambooU and the bamboo design firm IBUKU to be part of this amazing experience, hosted by The Kul Kul Farm at the Green School in Bali, Indonesia. Check out more information about the next courses here and follow BambooUBali on Instagram.