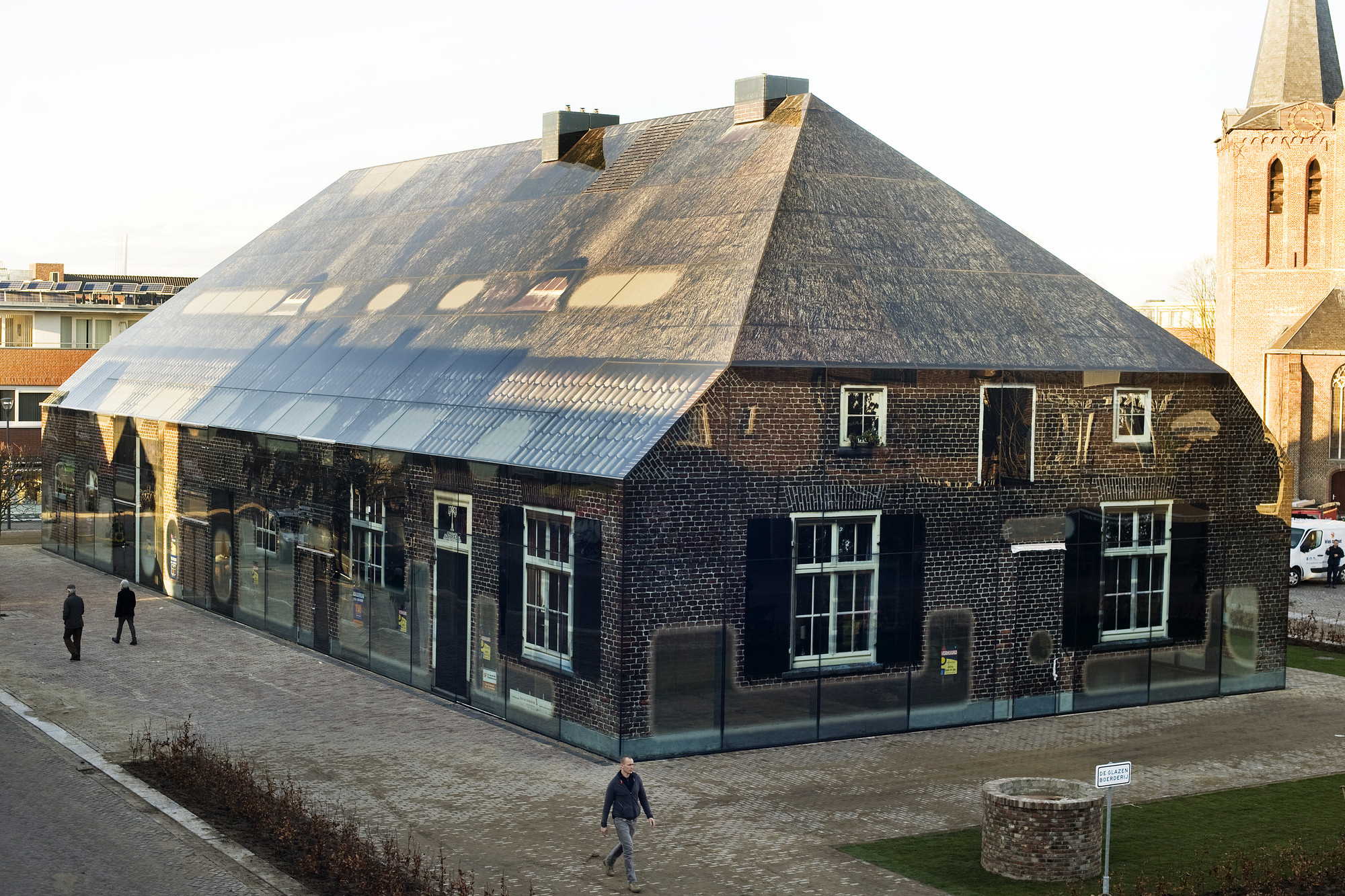
If you search the web for information on MVRDV's Glass Farm, you'll find plenty of people writing about the project's 33-year history, and about its context in the small town of Schijndel. You'll even find plenty of people theorizing on the nature of those glass walls, and the relationships between image and authenticity and between modern technology and modest tradition. But strangely, you'll find almost no information on how the project made use of Digital Ceramic Printing, a relatively new process which was able to handle the many colors, variable transparency and fine tolerances required to display an entire farmhouse facade across a thousand glass panels.
In this new installment of our Material Minds series, presented by ArchDaily Materials, we spoke to MVRDV's project leader on the Glass Farm Gijs Rikken, and to Niv Raz, an Architect at Dip-Tech - the company who produces the printers, ink, software and support required for the process.

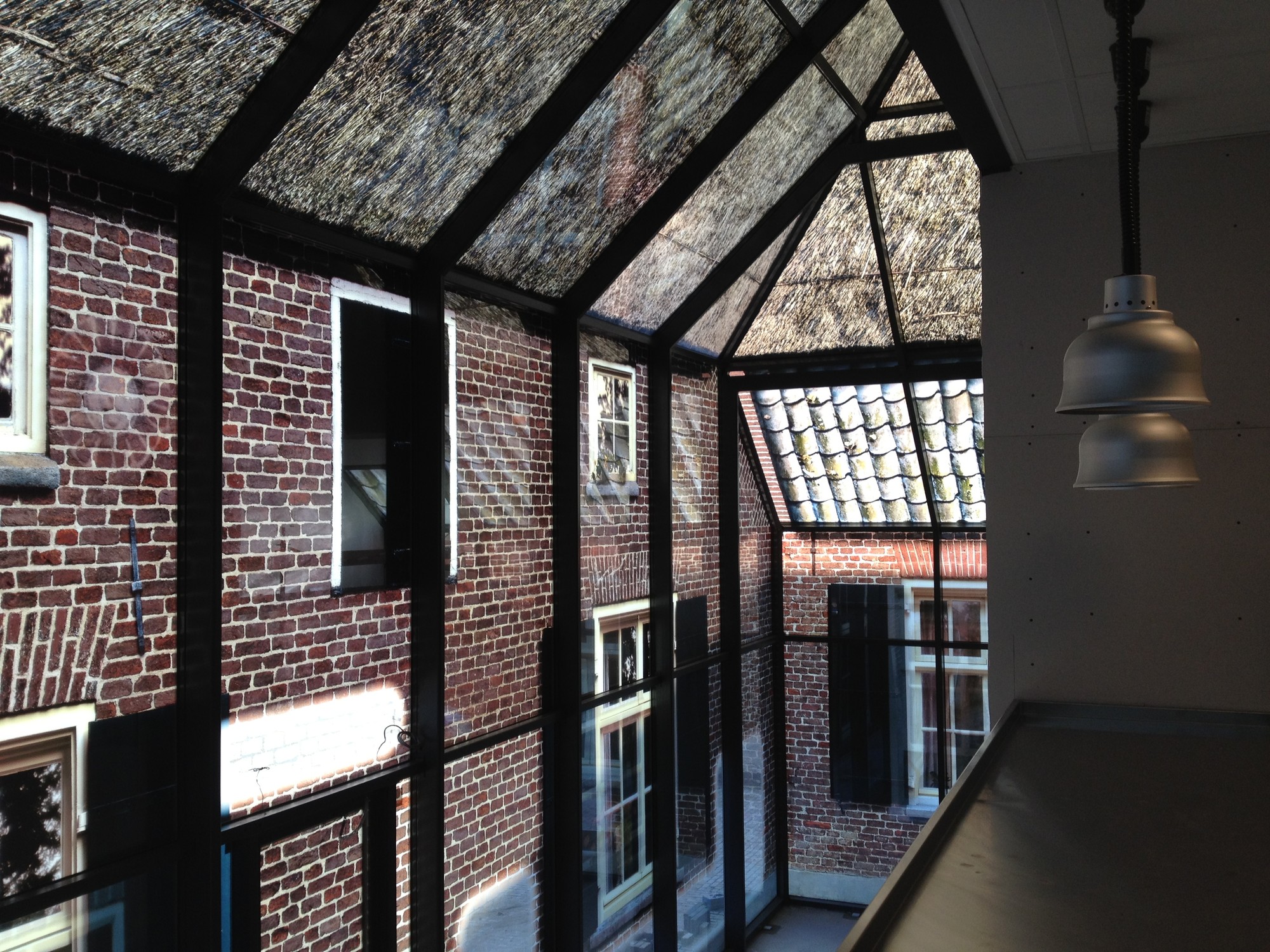
Would a project like the Glass Farm have been possible before the advent of Digital Ceramic Printing? What would the alternatives have been, and what advantages does Digital Ceramic Printing have over them?
Gijs Rikken: DCP did not yet exist in its current form when we started developing the concept of the Glass Farm (or Ghost Farm as it was called at first). We were struggling to achieve the desired effect of a farm image displayed on a glass shell by means of using standard fritting techniques, because back then this meant a mono-color frit with a lot of repetition (to reduce costs on the molds) in the overall image. But then AGC Mirodan [part of AGC Glass Europe, the company that printed the glass and customers of Dip-Tech] took a leap of faith, and showed us a possible alternative. DCP provided high resolution prints on glass, in full color, without the need for molds or repeating elements. That changed the game completely.
Niv Raz: Without Digital Ceramic Printing, the integrity of the glass designs for Glass Farm would have been compromised and the vision for the project would not have been actualized. The alternatives might have been traditional silk screen printing or printing on laminated foil. However, given the limitations of these technologies, such as accuracy and color, positioning, and alignment between gaps in the panels and external durability, it would have been impossible to achieve the desired results. Digital Ceramic Printing easily overcomes these obstacles.
Are there any limitations to the images that can be created with Digital Ceramic Printing?
Niv Raz: Digital Ceramic Printing is a cutting-edge technology and companies like Dip-Tech are actively and continuously conducting research and development to further advance digital ceramic glass printers, inks and software. With this, color, functionality and application possibilities only keep on expanding. For example, today glass panels up to 18m long can be digitally printed, whereas up until a year ago, this was not possible.
It is important to add that digital ceramic inks are composed of natural pigments, which does impose a slight color limitation, as with all ceramic inks. Dip-Tech has developed unique image processing software which greatly alleviates this limitation. As a result, with Dip-Tech printing it is possible to achieve precise color matching, and reach a wide color range.
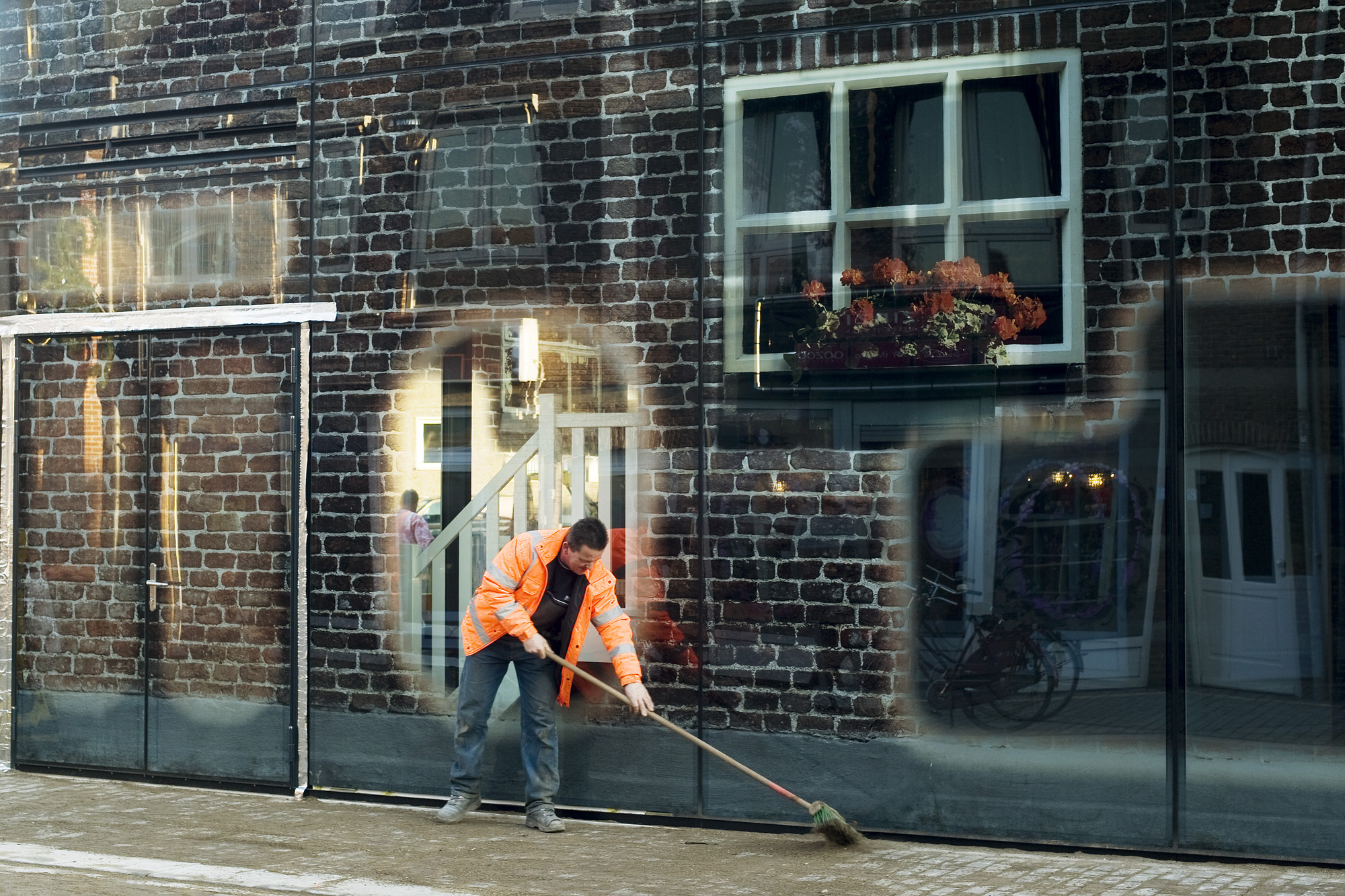
What was your experience like using this technology for the first time?
Gijs Rikken: Innovation always takes extra time and input, but the rewards are also worth it. For the Glass Farm the biggest challenge was to achieve an ultra-high and continuous quality. The complexity of the all-glass facade and the relative newness of the printing technique made this a very delicate operation. The DTP-work that needed to be done for this project was big – a few terabytes. There were a thousand different pieces of glass, varying from 8 square meter panels to 0.05 square meters, and tolerances were very low. Everything needed to fit exactly.
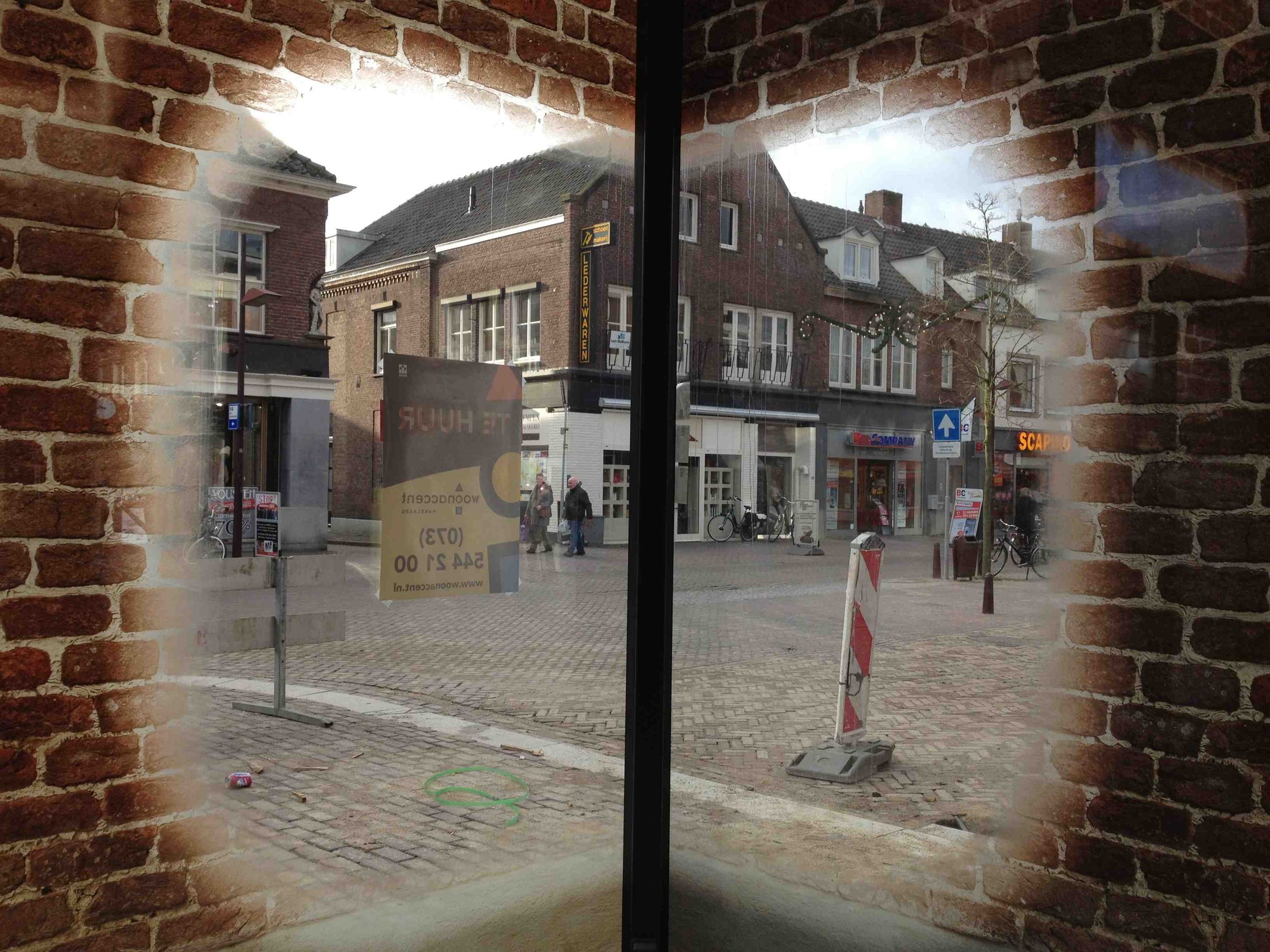
Is the Glass Farm the most ambitious project you have seen in its use of Digital Ceramic Printing? If not, what is the "cutting edge" of the technology?
Niv Raz: The Glass Farm is certainly a good example of extensive use of digital ceramic printed glass. Beyond that, there are many projects that have optimized the use of Digital Ceramic Printing: Hanjie Wanda Square, designed by UNStudio and printed by Glas&Tongue, has a circular vector pattern printed across panels of varied sizes and needed the perfect alignment of digital printing; Shigeru Ban's Cardboard Cathedral, printed by Metro Performance Glass, where digital ceramic printed glass was used to reinterpret the original rose window; and Ryerson University's Student Learning Center, designed by Snøhetta & Zeidler Partnership Architects and printed by Prelco, which combined Digital Ceramic Printing with other energy-saving glass processes to enable the LEED certified building to be 60% glass, while most such buildings are only up to 40% glass.
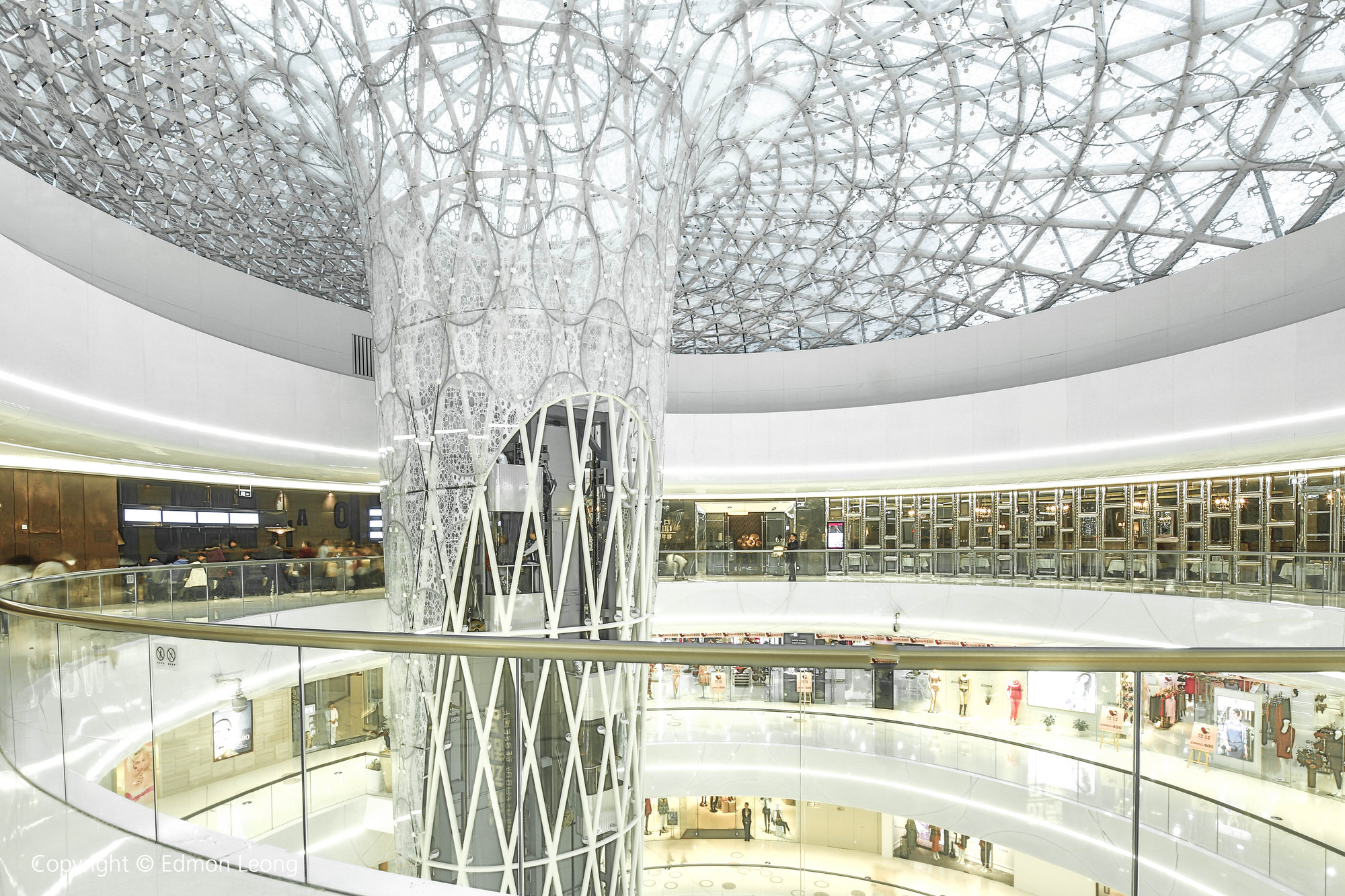
How does the Digital Ceramic Printing Process alter the performance properties of glass? What should designers bear in mind when specifying this technology?
Niv Raz: The properties of the glass don't change; but the printing does improve glass functionality and enables greater freedom of design. Other glass processes such as lamination, insulating, coating and bending can still be applied as with unprinted glass.
Digital Ceramic Glass Printing does offer high levels of sustainability by actively playing a role in heat gain reduction, better control of interior and exterior temperatures, and reducing reflection. Dip-Tech has developed an energy saving calculator to effectively measure and evaluate these savings.
Architects can fully exploit their creativity, and feel free to design without considering the number of panels required and a wide color range possibility. The technology is very flexible and suitable for any graphic content, and offers unprecedented control of transparency, translucency, and selective transparency. This is applicable for all interior and exterior, residential and commercial glass applications. Architects should also be aware that Digital Ceramic Printing is a process where they are supported from start to finish, and a lack of familiarity with the technology should not limit them from tapping into its potential.
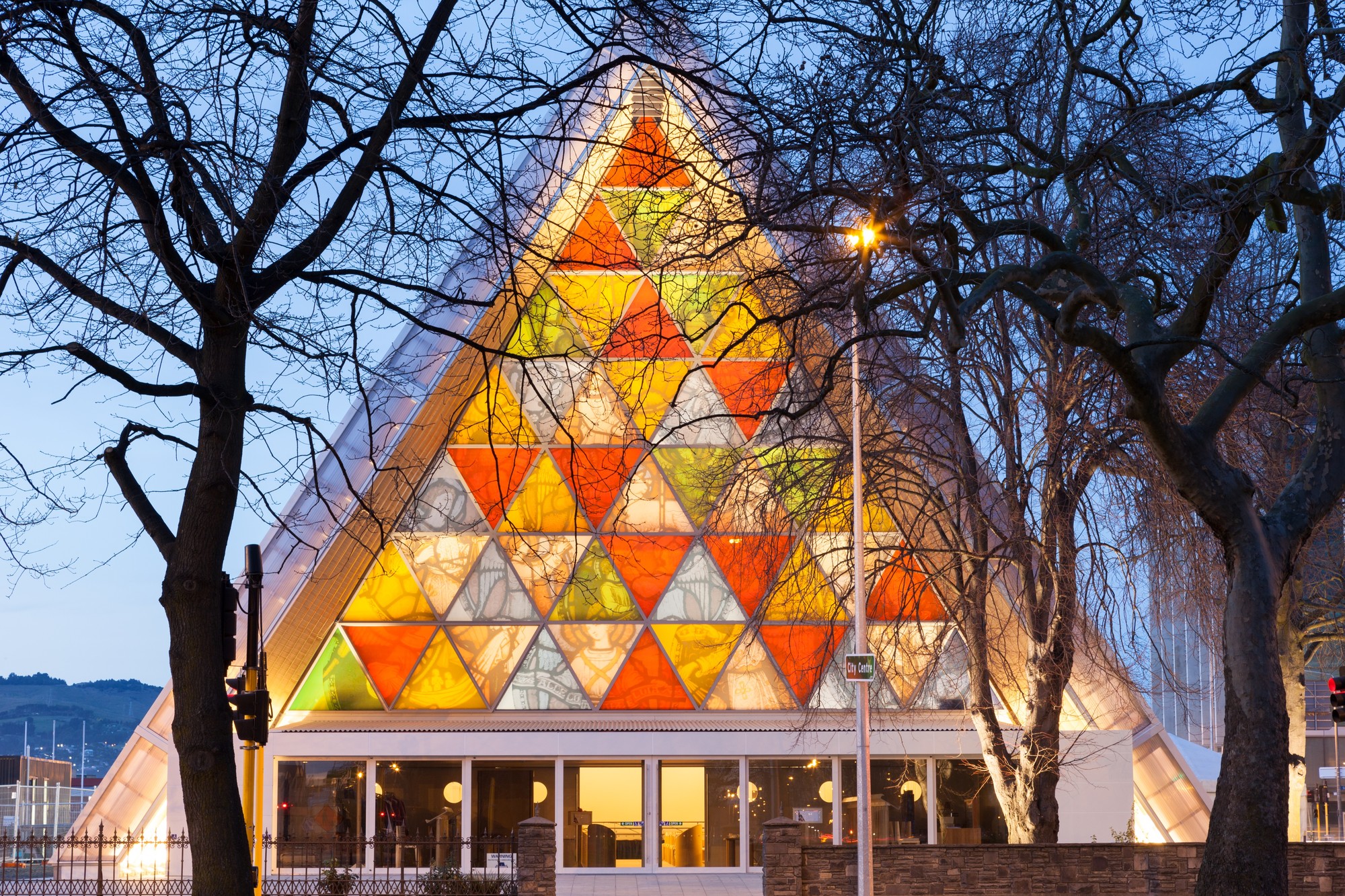
Are there any other considerations relating to Digital Ceramic Printing on Glass - what is its cost related to plain glass for example?
Niv Raz: Digital Ceramic Printing offers unprecedented functional performance, durability and design possibilities. These attributes can enable cost savings in multiple areas, both in terms of original construction cost and in the long-term operation of a building. Of course the process of printing on glass adds cost compared to plain glass, but much of that can be offset by the associated savings.
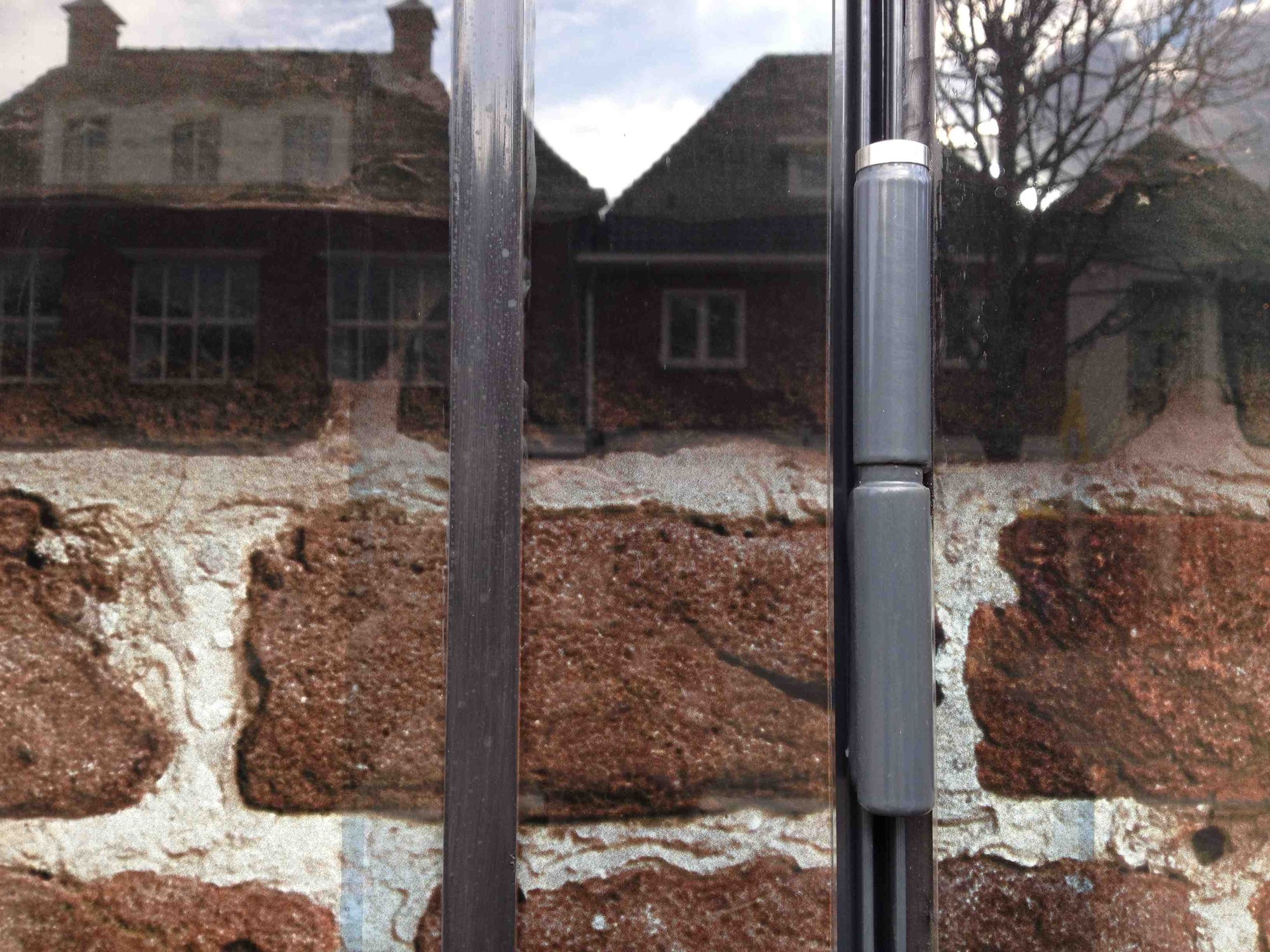
Gijs Rikken: This little anecdote is something that seems irrelevant but made a big impact on the design. At a certain time, we discussed the minimum width of the silicon seams on the outside of the building. What width did they need to be? Why were they so wide now? They were a full 25 millimeters at that time, which is quite narrow already of course, but they broke up the overall image nonetheless and we needed to minimize them.
Façade engineer Brakel Atmos replied that to be able to lock the glass plates into place, someone needed to be able to reach inside of the gap between two glass plates with his fingers, grab hold of a little steel plate and twist it 90 degrees. This manual procedure defined the 25 millimeters widths of the gaps and therefore the silicon seam that would be the finish of that gap. So we asked if there was someone around who had thinner fingers, maybe smaller hands? We wanted 20 millimeters and asked Brakel Atmos if that would be possible. They were hesitant at first, but then they found a way in which a worker with small hands could manage it. And now the seams are 20 millimeters and they look fantastic!
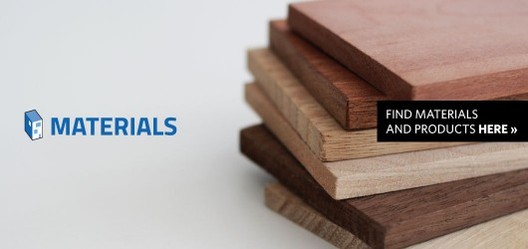