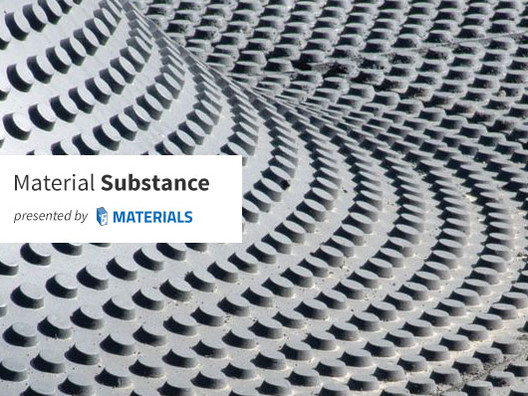
The following is the first article of Material Substance, a column, penned by Christopher Brenny and presented by AD Materials, which investigates the innovative applications of materials in architecture.
A material is nothing without a process. The characteristics of plastic, for example, vary dramatically depending on where and how the raw material is applied during the forming process. The same material can be used to create a bag, a solid container, or a woven textile. The difference between a disposable water bottle and carpeting is so distinct that one could not make the material connection without some foreknowledge of the manufacturing process of each.
The result of this material ecosystem is a scenario in which design and manufacturing must inform one another. This connection often moves so slowly in the building industry that it is difficult to perceive and very slow to adapt. Shape memory alloys such as nitinol (muscle wire), for example, are gradually moving into public nomenclature. While the novelty of such materials is ripe for exploration, application has proven difficult as the cost of such materials is quite prohibitive. Shape memory alloys, unless they are developed using more abundant metals such as aluminum, will likely remain a niche product developed for very specific applications.
Memory plastics, while less developed and responsive, have significant potential to become a familiar fixture in our daily lives. Combining this technology with the lightweight, structural capabilities of foamed materials, our preconceptions of the portable and flat packed may soon transform from disposable and insubstantial into something much more beautiful and valuable.
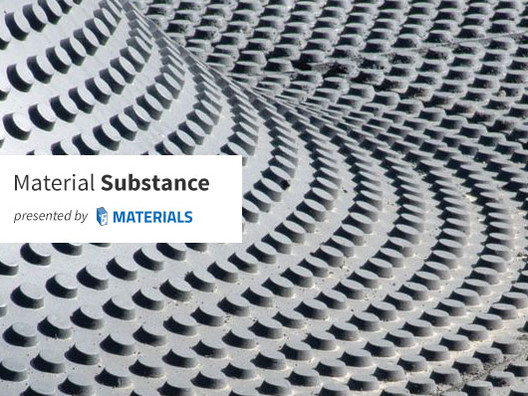
Carl de Smet combines material science and design in his firm Noumenon to push the boundaries of shape memory application. Polyurethane furniture is engineered in such a way that its behavior takes on characteristics suitable for transport and self-assembly. Eschewing the Ikea Allen wrench approach, Noumenon’s website states outright that “the material is the mechanism; packing = product.” Prototype chairs are shipped in compressed bricks that expand to their final shape under the appropriate stimulus.
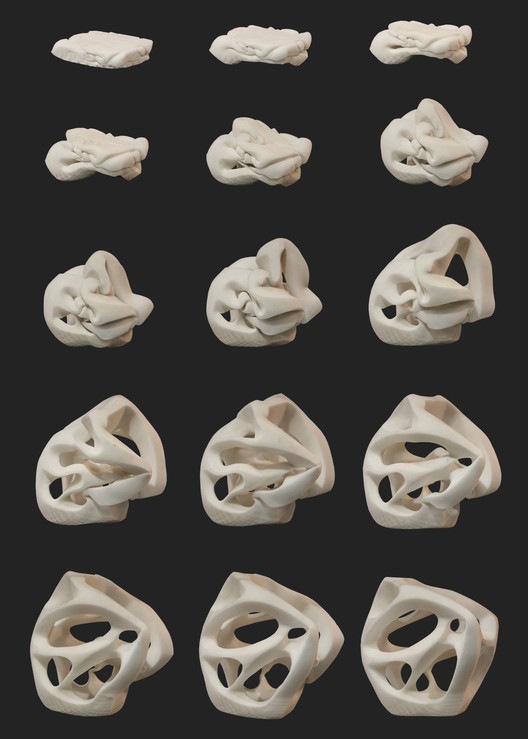
While nascent, this technology has far-reaching applications, perhaps even for mobile or emergency relief shelter. The memory material in question can be both milled and injection-molded. According to de Smet:
“This is a kind of a polyurethane, or PU. In the car industry the fake leather is made out of PU. So we can do it like fake leather or fake wood; it’s just the finishing of the molding process. It depends on the moulding and how you present it.”
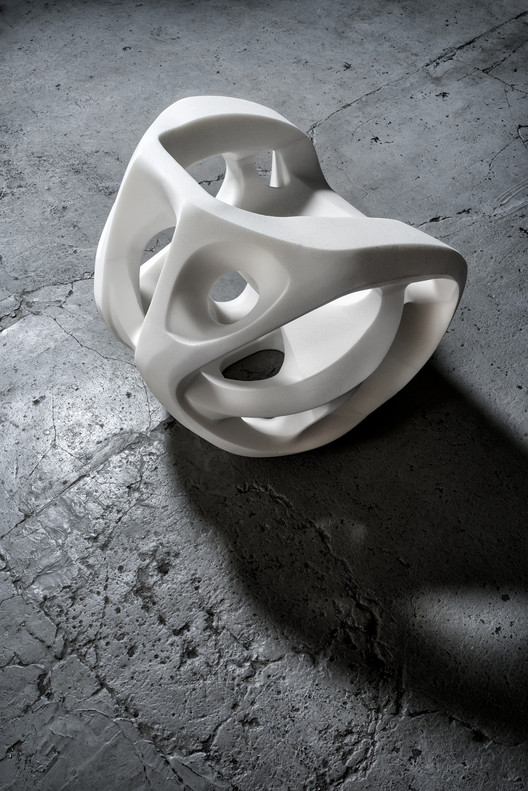
The prototype furniture itself is dense enough such that it “is rigid, so it’s strong, which means you can use it as a structural support. And when it becomes hot and when it wants to change form, it becomes soft.” The current formulation is programmed such that it expands into its imprinted memory shape at roughly 70°C. Like nitinol, current can also be used to trigger the memory response.
Of course, this emergent technology is not without its problematic nuances. While polyurethane is created through an exothermic process, its volatile constituent ingredients and blowing agents (used to create foamed polyurethane) have a questionable environmental history. It is not biodegradable and usually downcycled rather than recycled.
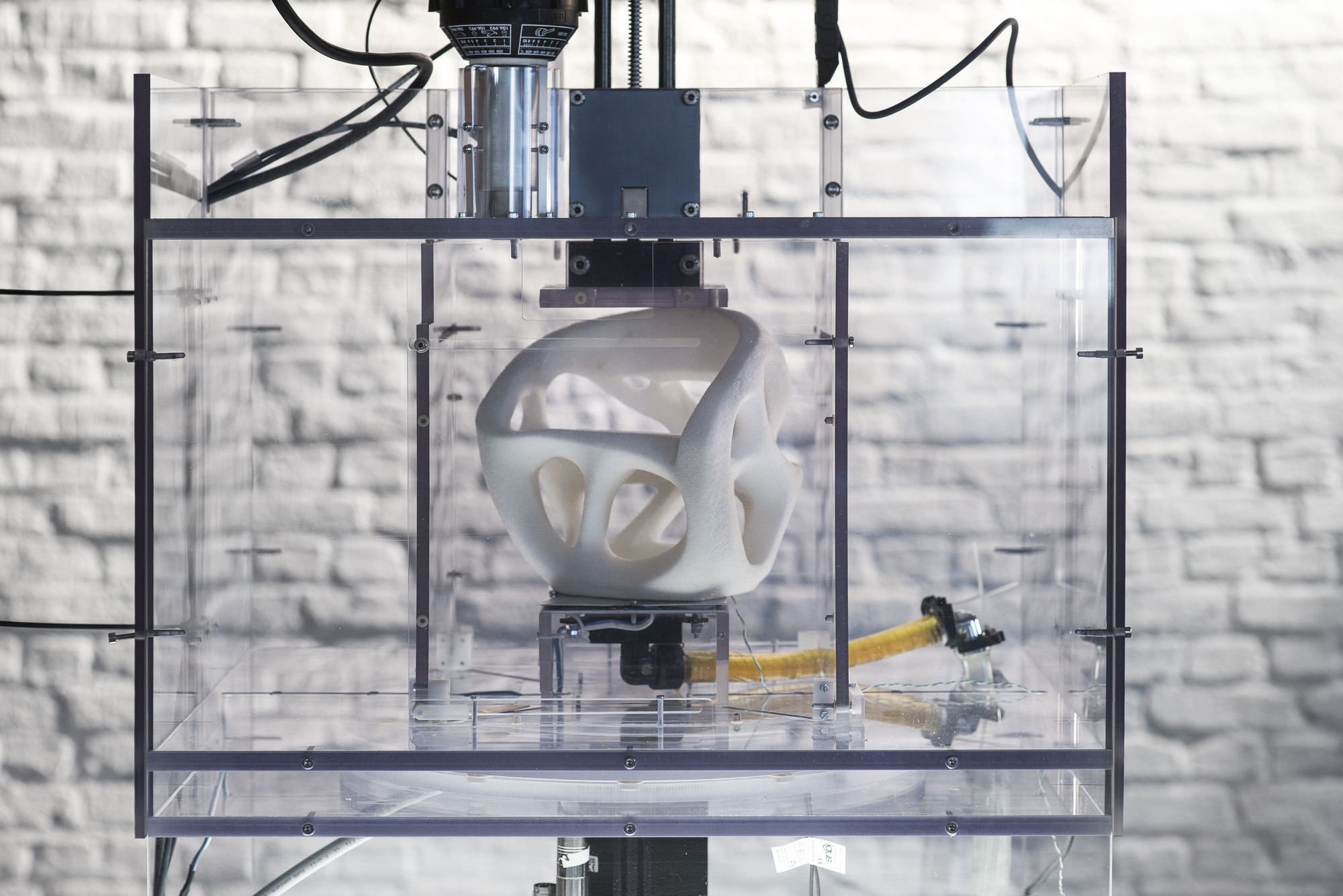
Nonetheless, if we elevate the status of flat pack into something that is to be valued and maintained, the issue of disposal becomes less urgent. Further, development of plant-based plastics may provide a suitable alternative. In combination with the single-material application used by Noumenon, this technology may soon prove revolutionary.
References
This article was adapted from two articles originally published on Material Strategies: Designing the Machine and Foamed Memories.
Christopher Brenny is a Master of Architecture graduate from the University of Minnesota College of Design interested in the intersection of biology, architecture, and emerging materials. He is currently a designer at NewStudio Architecture.
.jpg?1396292066)