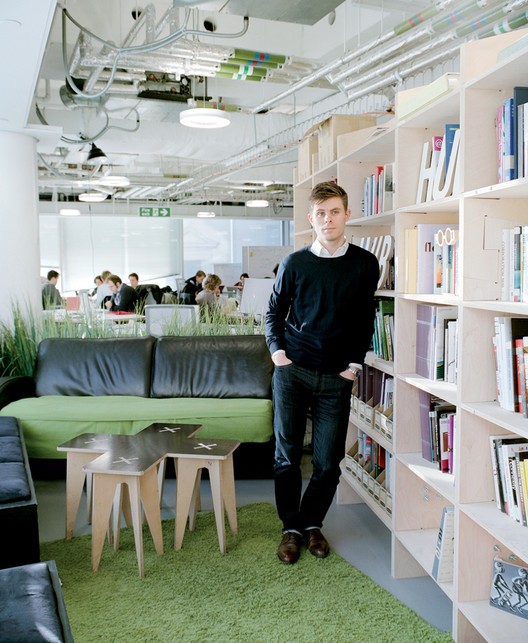
Metropolis Magazine has unveiled its 4th annual Game Changers - including architects Eric Owen Moss and Alistair Parvin, the co-founder of WikiHouse, an open-sourced platform for architecture. In the following article, Jonathan Glancey profiles Parvin and asks: is WikiHouse a threat to architects? Or "a glimpse into our digital design future"?
I first met WikiHouse cofounder Alastair Parvin—not in the flesh, of course, much less in print—courtesy of YouTube. You can do the same by watching his lecture, “Architecture for the People by the People.” In the video, Parvin explains the WikiHouse concept to the 2013 annual TED conference in Long Beach, California. Looking young and trim in a white shirt and blue jeans, Parvin’s voice is chipper and confident as he delivers his provocative idea to the world.
Given that the 1,600 TED lectures that are currently available online have been viewed more than a billion times, you may have already heard a little about the WikiHouse by now. In case you haven’t, it’s “an open- source construction set,” according to the WikiHouse online collaborative. “The aim is to allow anyone to design, download, and ‘print’ CNC-milled houses and components, which can be assembled with minimal skill or training.”
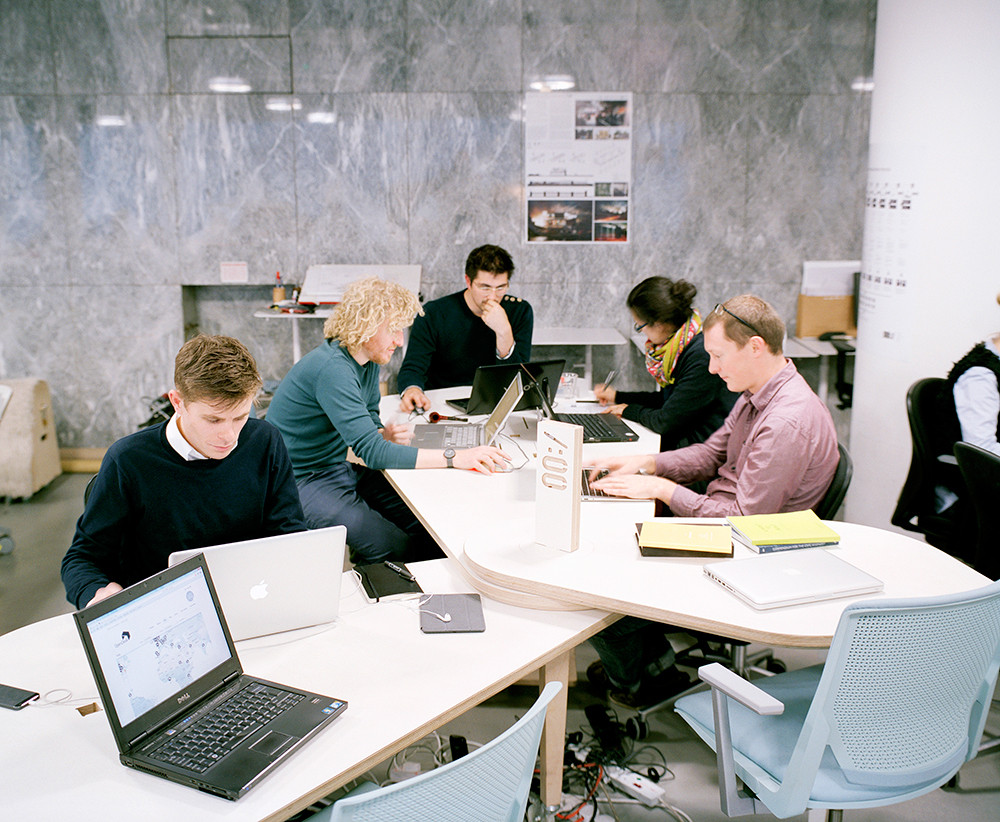
So, assuming you have a Computer Numerical Control (CNC) milling machine using CAD/CAM readily at hand, you’ll be all set to start building your own house simply by downloading the WikiHouse software. If there are things about the standard WikiHouse design you don’t like, you can just edit online. Parvin, a 30-year-old British architecture graduate of Sheffield University, certainly makes it sound as easy as it is desirable: a form of low-cost, well-designed mass housing as easy to slot together as a chair from IKEA, available to anyone and everyone around the globe.
Both on the TED video and in person, Parvin is an assured and populist salesman. And a bit of a WikiHouse poster boy, too. He’s so keen, in fact, that it’s easy to see him as the equivalent of a bright-eyed Mormon missionary setting out to convert the world. When I looked into TED, I was not surprised to find that Chris Anderson, the former journalist and publisher who fronts The Sapling Foundation that runs TED, is the son of medical missionaries, brought up by parents spreading a practical message of Western enlightenment to poor people in Pakistan, India, and Afghanistan. Parvin has something of the evangelical preacher about him, too (as do many people converted to or raised in the all-pervading religion of digital technology and communications).
While WikiHouse is an immediately attractive proposition, there are so many questions to ask one of its leading acolytes that it’s all too easy to sound like a heretic or Luddite when talking to Parvin. I caught up with him in the beautifully crafted New Zealand House in London’s Haymarket, near Trafalgar Square. Inside the late-1950s High Commission building (designed by RMJM), with its rich palette of Greek marble, Portland stone, and New Zealand teak, Parvin works with the 00:/ design studio in a huge first-floor space leased to Hub Westminster, a global collaborative of creative and social enterprises. We sit with cups of tea on CNC-milled plywood chairs at a CNC-milled plywood table in front of a full-scale mock-up of a plywood WikiHouse.
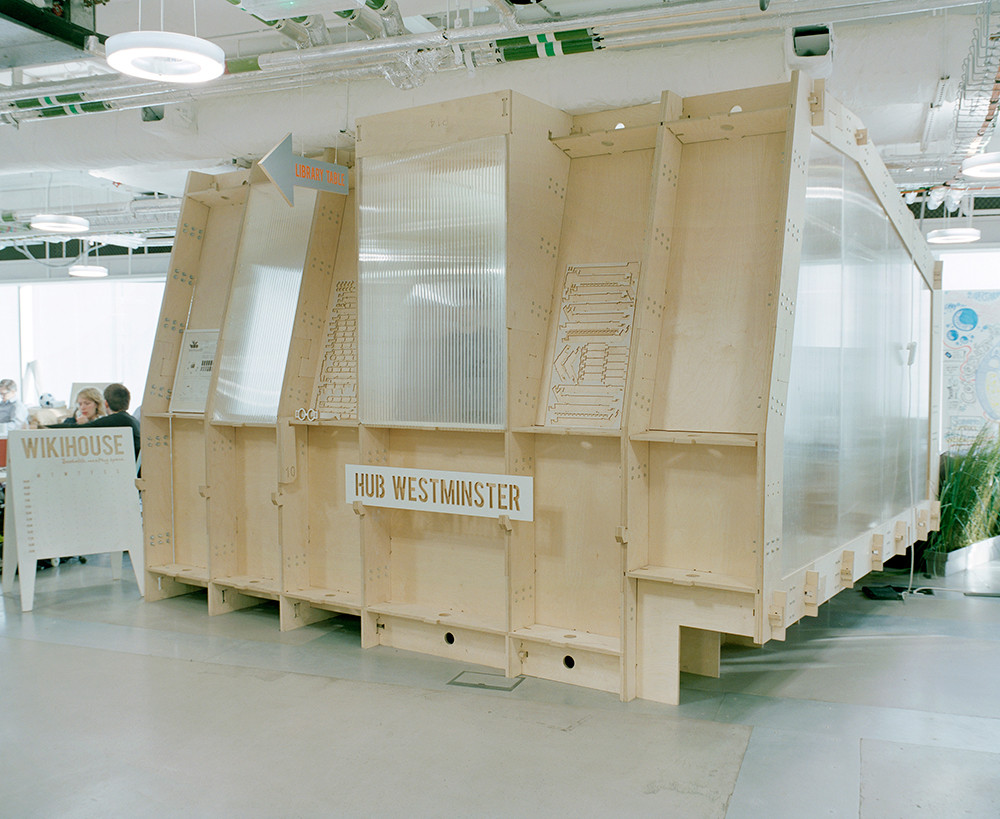
“It’s not just about plywood,” Parvin says. “Plywood happens to be where we started, and it’s a material that works well where labor is expensive. We’re material-agnostic. What we hope people will do is to find the right local materials that work best for them. The idea is that we’ve begun with a ‘chassis,’ or a structure for other people to build on. There’s no need for scaffolding, even though it’s a two-story structure. Very few tools are required. It slots together.
“As for services, we can offer wiring kits that can be clipped to the house, and, as the cost of digital tools and manufacturing drops, the final cost of a WikiHouse will get lower and, hopefully, lower again. We’re aiming for a fully functioning house in Britain costing a maximum of £50,000.”
So where does the architect fit in? Parvin, who left Sheffield University in 2009 and worked for two years with the London studios of Rogers Stirk Harbour + Partners and Feilden Clegg Bradley Studios, has not yet become licensed as an architect (and he may choose not to). “The architect begins the project and helps to refine it. The thinking is not, ultimately, to put architects out of business, but to democratize architecture. An archi-tect in the future can choose to work for a week at a time on a large number of projects, especially working online, rather than for a very long period on a single building. YouTube hasn’t put Hollywood out of business, has it?”
Paul Finch, deputy chair of the Design Council and editorial director of the Architectural Review and Architects’ Journal, believes “the profession should embrace the ever-greater possibilities new technology offers, not only so architects can explore new channels of creativity, but so they can also become a part of the process of ‘editing’ design with the people who use and buy their buildings.” They should, in other words, have nothing to fear from the democratization of design.
Parvin, however, feels that architects “often wear their professional badge as a form of protectionism. We’re talking about open-source design, and I’m sure this can seem uncomfortable to those many architects whose role is justified by their controlling a project through all stages to completion. We’re saying that architecture and, by extension, cities, are made by just one percent of the population, and that this isn’t as it should be. We’re also saying that architecture, especially housing, is procured through a narrow base of designers and building companies, and that it’s time to democratize, and for architects to empower people by working for a lot of small companies, individuals and projects.”
For Hank Dittmar, the respected American-born urbanist and the Prince of Wales’s special advisor on architecture, the WikiHouse is not an idea blowing idealistically in the wind; it has firm historic roots. “It’s not dissimilar from the idea of the pattern book used to great effect to produce affordable homes in the Georgian era,” he says. “In the early part of the last century, Country Life magazine published plans for low-cost homes in popular books. Updating this concept is a good idea, but then we’d need to crack the altogether tougher issue of finding land for self-build and small developments. This could be a role for local authorities and government agencies. They might like the idea in the long term because they wouldn’t have to be the builders, but simply the land assemblers.”
So, how far has the project gotten? Have any WikiHouses been built yet? “Quite a few WikiHouse prototypes have been made,” Parvin says, “and two students in the U.S. have made a small house-shelter that they’re living in called FOUNDhouse, but generally we would say no one has built the first full house yet.There are several on the drawing board. So the race is on!”
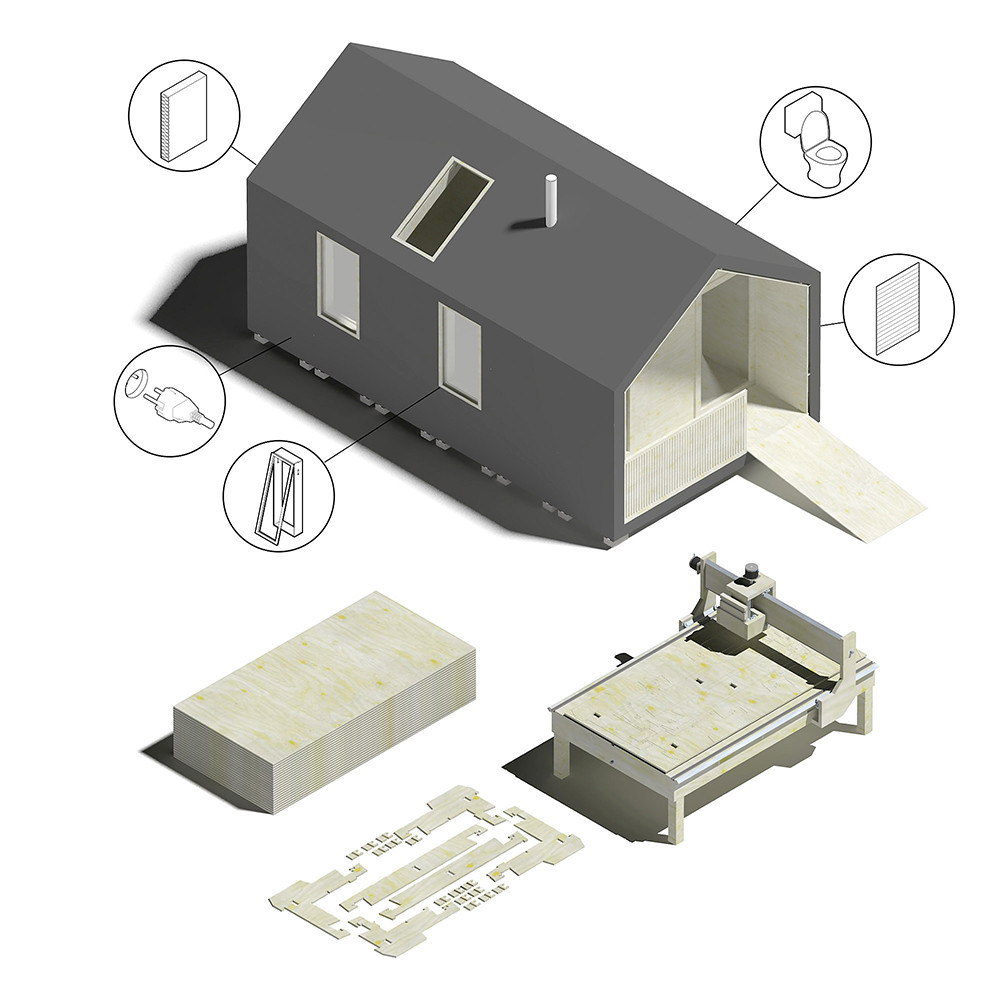
For Cecil Balmond, the renowned structural designer, mathematician, and engineer who has worked on projects as diverse as emergency relief housing to the daring CCTV headquarters in Beijing with Rem Koolhaas and OMA, “there is always the danger of the idealization of solutions to low-cost housing. In developed countries, the idea of democratizing housing design and using new computer techniques is a good one. Even then, the technology is still in its early days and, of course, people can already buy and customize flat-pack houses over the Internet. In developing countries, it can often be best to match local building and craft skills to plans drawn up by architects and engineers to produce the most effective homes whether they’re made from wood or concrete panels or even hides or fabrics over timber frames. The important thing is to not let prefabrication become too complex or costly—and certainly not an ideological process, as it was in the sixties and seventies.”
As Parvin himself says, “Of course there are big problems to solve, especially concerning the availability of new, computer-driven tools and machinery, the availability, cost, and ownership of land.... Obviously, you can’t just download and make a WikiHouse wherever you want to. And there are local planning concerns, too; planners don’t want to work with amateurs.”
It’s hard to say how it might be taken up around the world or exactly what reaction mainstream architects will have a few years down the line. What we do know is that architectural institutes, with the ear of governments and civil servants, have been here before. In 1929, the American Institute of Architects (AIA) made it known in no uncertain terms what it thought of a proposal by one Richard Buckminster Fuller to mass-produce his proposed 4-D prefabricated house. Even though Fuller offered the institute proprietary rights to the design, the AIA ruled, “Be it resolved that the AIA establish itself on record as inherently opposed to any peas-in-a-pod-like reproducible designs.”
The folksy, if pointed, reference to “peas in a pod” design was made, in all probability, because the ever-inventive Fuller proposed to sell his 4-D houses by weight, as with meat, fruits, and vegetables. Fuller suggested a price of 25 cents a pound, adding up to $1,500 given that the prefab building weighed in at 6,000 pounds. (By the same principle, a Model-T Ford sold in its later stages for 22 cents per pound.)
Fuller came up with three proposals for mass-produced, low-cost, prefabricated houses that could be delivered anywhere in the United States by container, and even by zeppelin, and that, in the case of the 1948 Wichita House —an aluminum and Plexiglas structure built by the Beech Aircraft Corporation—could be assembled by hand with a minimum of tools. Fuller designed it so that most of its components weighed less than ten pounds, while the total cost would be about $6,500.
If this sounded too good to be true, it was. To make them in sufficient numbers to be profitable, Fuller needed to have raised at least $10 million on Beech’s behalf. Backers were not to be found. Significantly for the WikiHouse, Fuller’s earlier Dymaxion Deployment Unit (DDU)—an upgraded corrugated steel silo shown in twin-cylinder form to great acclaim at the MoMA in New York in 1941—stalled not because it was a poor or unpopular design, but because the United States entered World War II the following year and the military commanded the very supplies of steel that would have made Fuller’s DDU—at just $1,250 a pop, assembly manual and tools included—commercially viable.
The promise of the WikiHouse project relies on the availability and decreasing cost of specialized digital machine tools and production processes. Time will tell how and where these develop. Meanwhile, millions of people seeking low-cost and adequate-quality homes will continue to turn to simple timber-framed houses, to other forms of well-established prefab housing, and, of course, to trailers. None of these is architecture with a capital A, but they can all make decent and easily acquired homes.
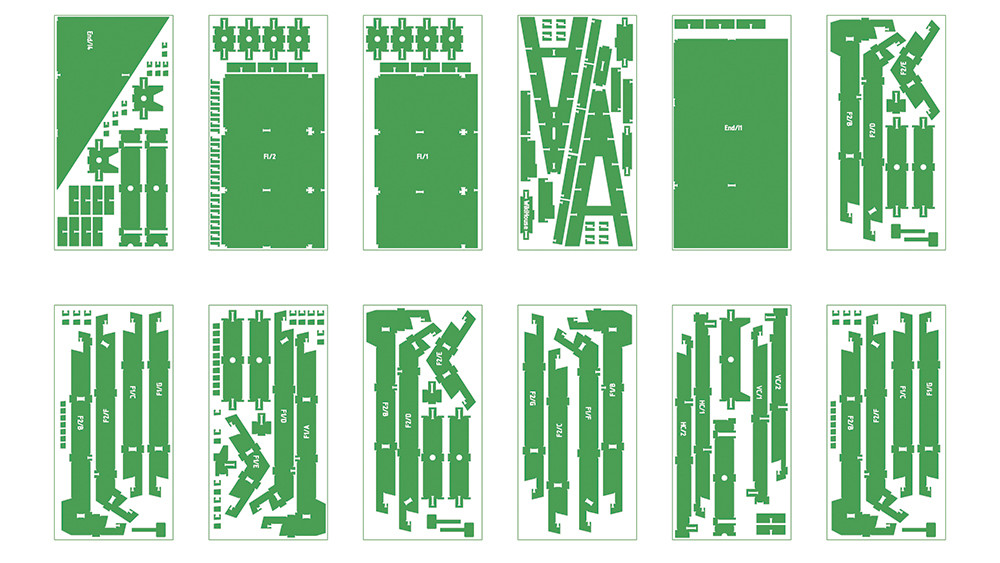
Parvin and his computer/new media–savvy colleagues around the globe have a long way to go. The 3-D (or 4-D, if you consider Fuller) stage of mass production housing lags behind the purely digital design stage. Still, even as Parvin preaches a new and democratic design creed, change is undoubtedly afoot.
When Henry Ford talked to local Michigan farmers, they told him they wanted faster and stronger horses even though they already had steam traction engines. He planned to give them something rather different than either for getting around. If he had only known about the WikiHouse, he would have been running it off a production line at 20 cents a pound. “In a sense, WikiHouse is like a digital-era Ford, or Coca-Cola,” Parvin says, “cheap, simple, appealing, and readily available—but different in that it’s part of a democratic process. Anyone and everyone can be a part of the design process.” Cost aside, this is the ultimate appeal of the WikiHouse, “the bedrock of its long-term future.”
See the rest of Metropolis Magazine's Game Changers here.