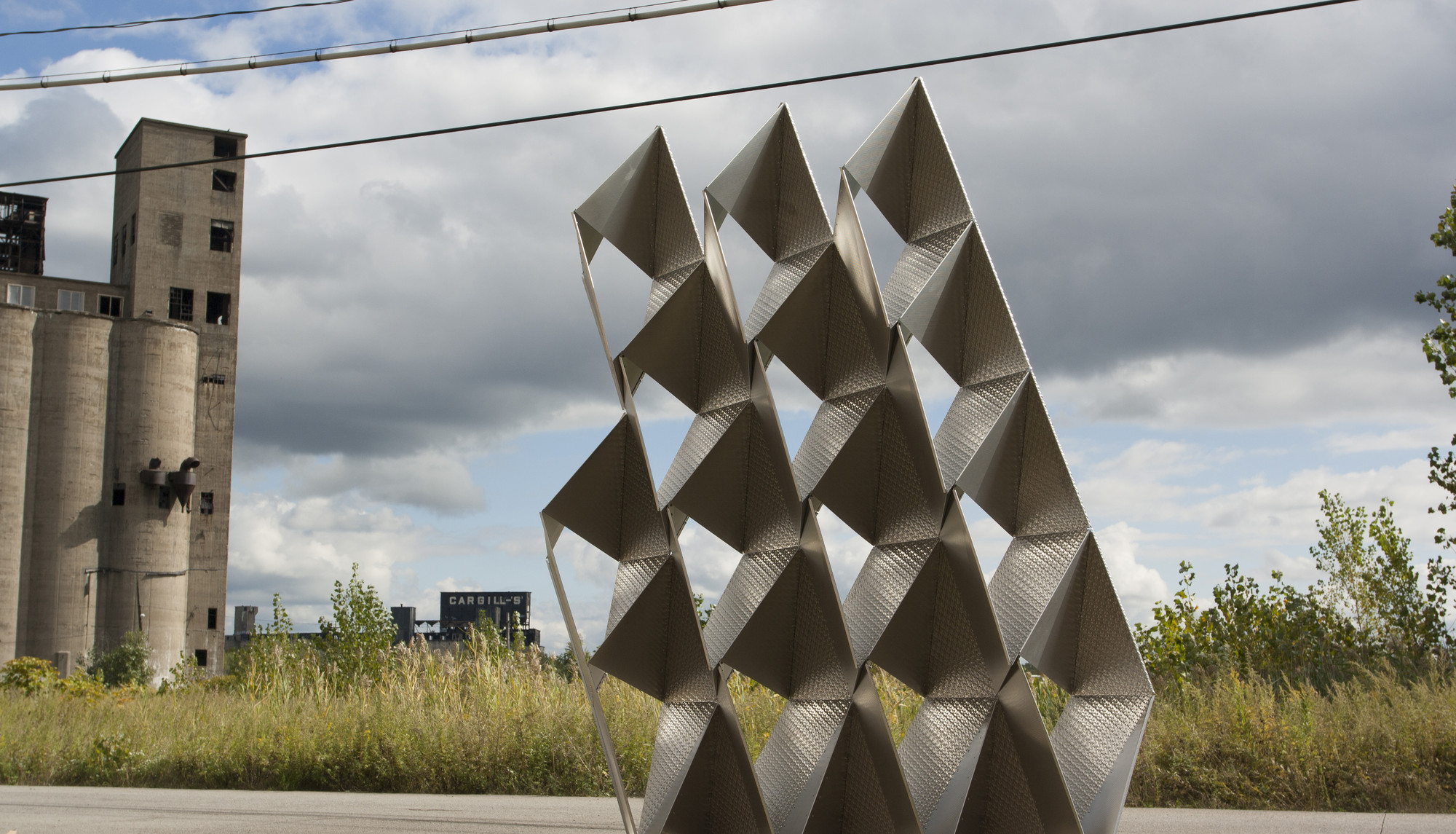
TEX-FAB Digital Fabrication Alliance’s 2013 international digital fabrication competition titled - SKIN is announcing the overall winner: 3xLP.
A total of 68 entries from across the globe representing 14 countries on 5 continents were narrowed down to 4 finalists and 4 honorable mentions in July by the First Round jury consisting of Phil Anzalone, Maria Mingallon, Gregg Pasquarelli, Randy Stratman, and Skylar Tibbits. The Second Round juried by James Carpenter, Neil Denari, Mic Patterson and William Zahner conferred and selected from the finalists 3xLP. All four finalists were exhibited at the ACADIA Adaptive Architecture Conference at the University of Waterloo in October, 2013.
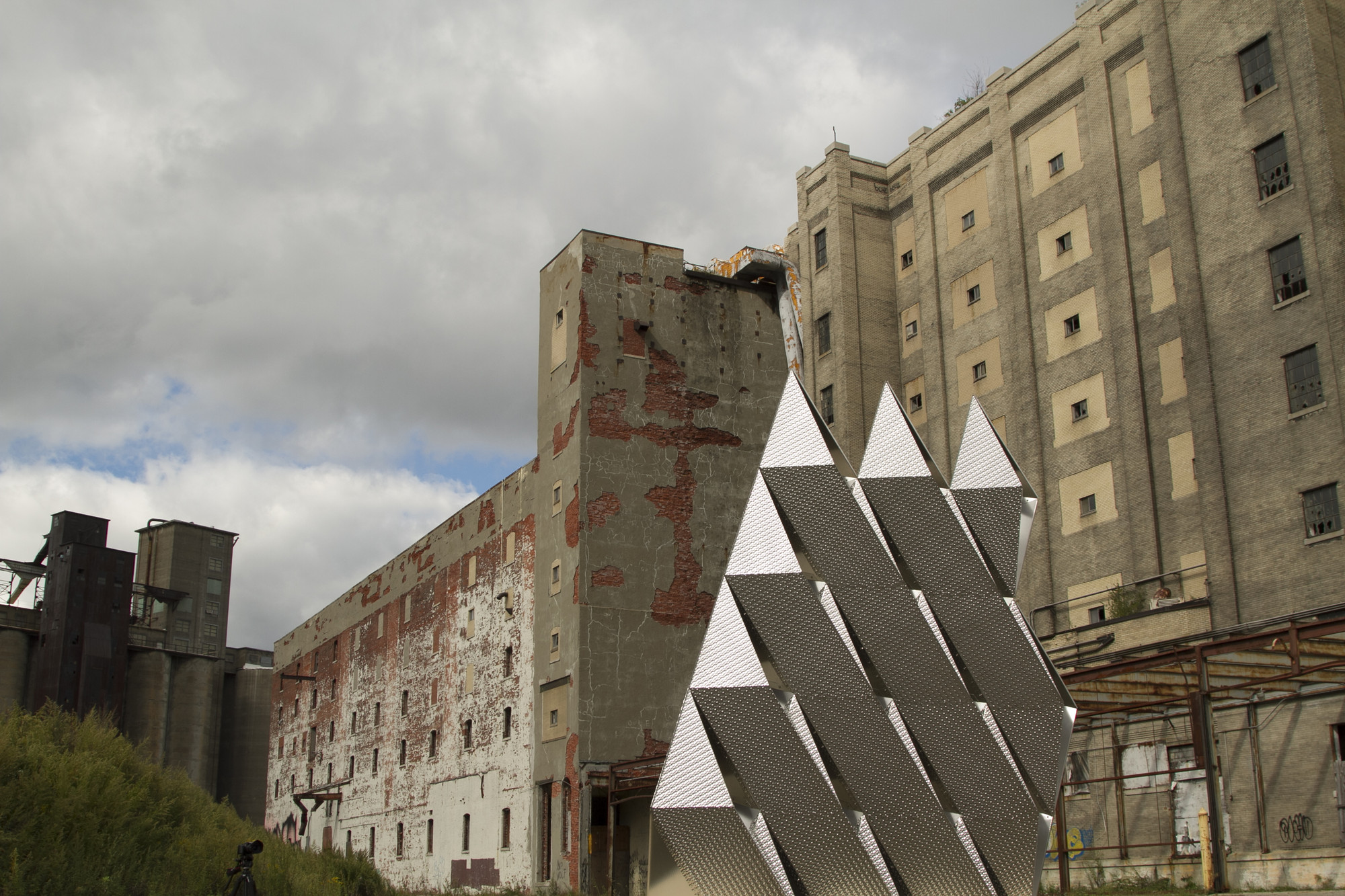
The jury deliberated for an hour via teleconference with TEX-FAB to determine the winner by a consensus. The decision to award the prize for further funding for development and prototyping for 3xLP was initiated by Mic Patterson, an expert in the façade technology by saying that “what’s been done so far is substantially thought out. It is well positioned to be taken to the next step.”
James Carpenter added “it is impressive due to both the depth of their engagement with the primary concepts and to the way they have engaged with the manufacturer to test and investigate those ideas.” Bill Zahner weighed in with “aesthetically its quite lovely the way it reflects light.”
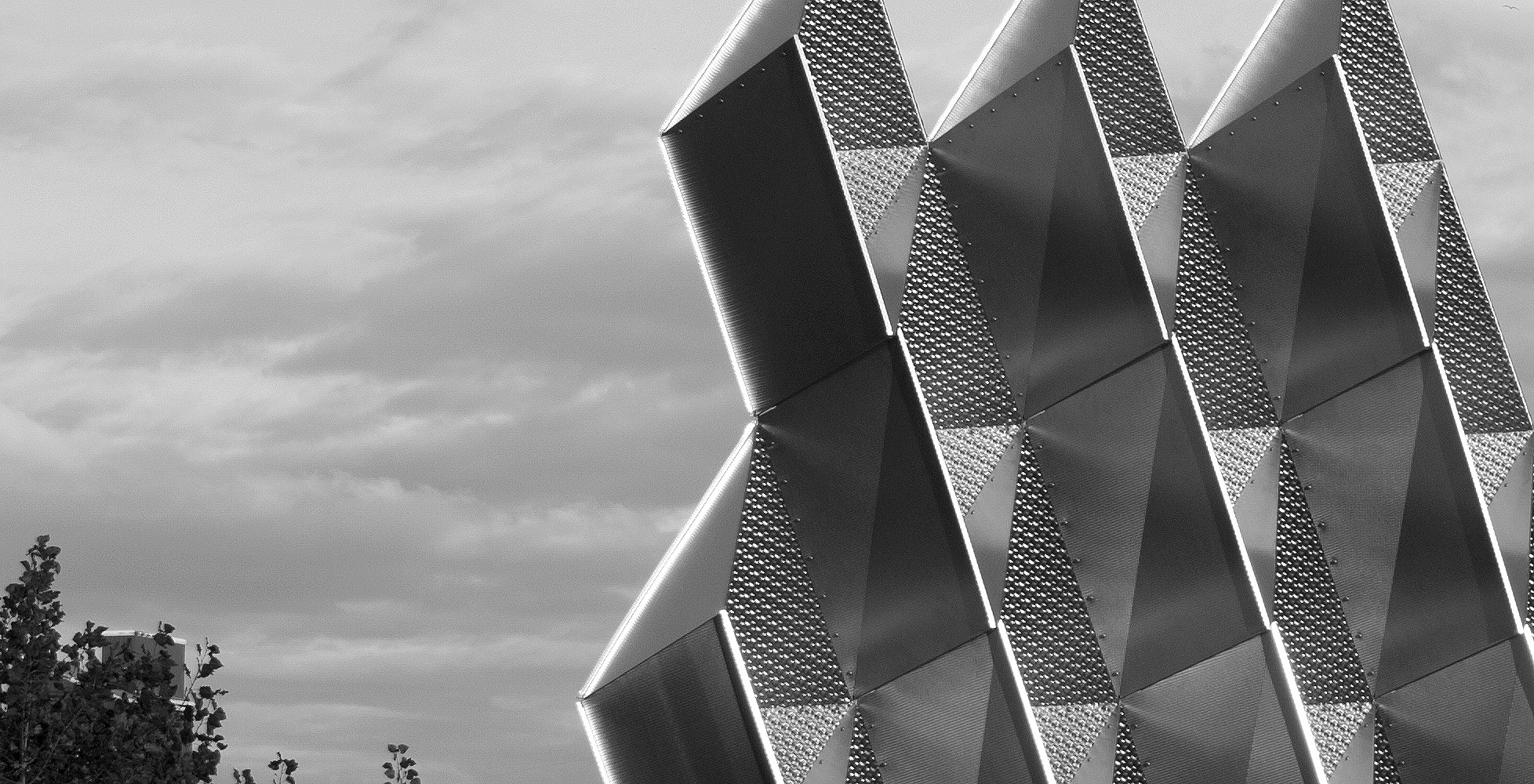
Neil Denari concluded with “for young designers the criteria is about how much shock value can you put into a project that has intensified the level of research toward plausibility. The more possible it becomes the more shocking it becomes. If 3xLP becomes the one that can achieve the greatest level of plausibility it yields the highest potential shock value.”
Design
From the architect. Design schemes are attempting to utilize un-backed, unframed (self-supported), thin-gauge rigidized stainless steel within vertical, free-standing architectural screens. These systems are mono-material, consisting entirely of stainless steel (including the hardware) and consider this to be critical to the clarity of the research and necessary to accurately analyze material behavior. Through texturing and purposefully aggressive folded geometries, loads are transferred through seemingly paper-thin surfaces, a unique approach to using sheet materials vertically and without the assistance of linear frameworks.
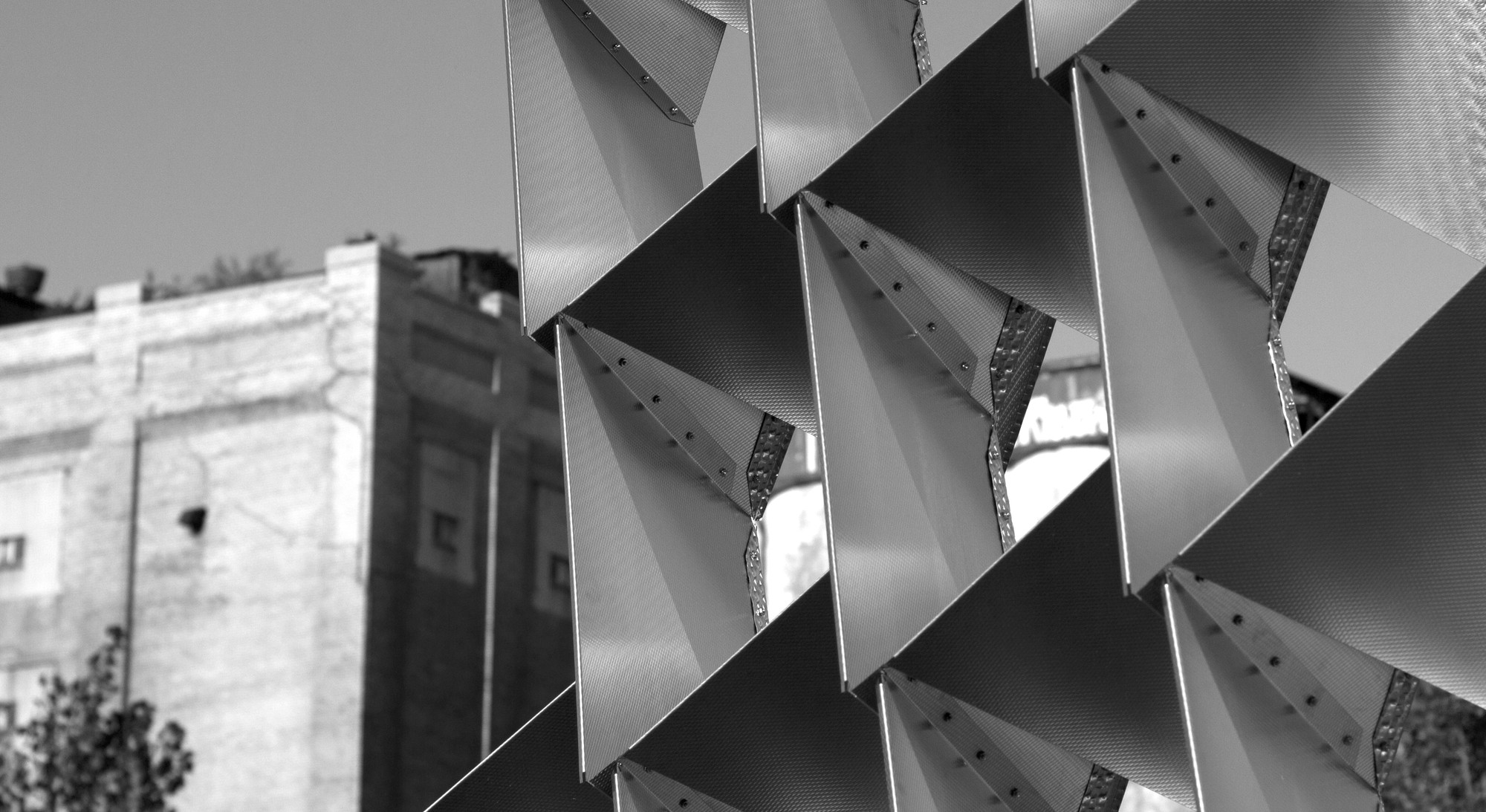
In this scheme, a base geometric scaffold of octahedrons is designed to accept parametric variations before the actual geometry of the system is applied. This allows for mathematic coordination of the panel orientation that when viewed perpendicular to the surface, creates an illusory orthographic projection of the surface depth, since the degree of rotation is related to the panel dimensions.
In addition, the system becomes gradually thinner toward the top to reduce the overall dead-load and material quantities. The gradual widening of the base scaffold throws the interconnected diamond shaped panels out of plane. When relieved of their parabolic curvature, the flat panels conform to a subtle diagonal twist, and reveal much deeper pockets and potential openings when viewed tangentially.
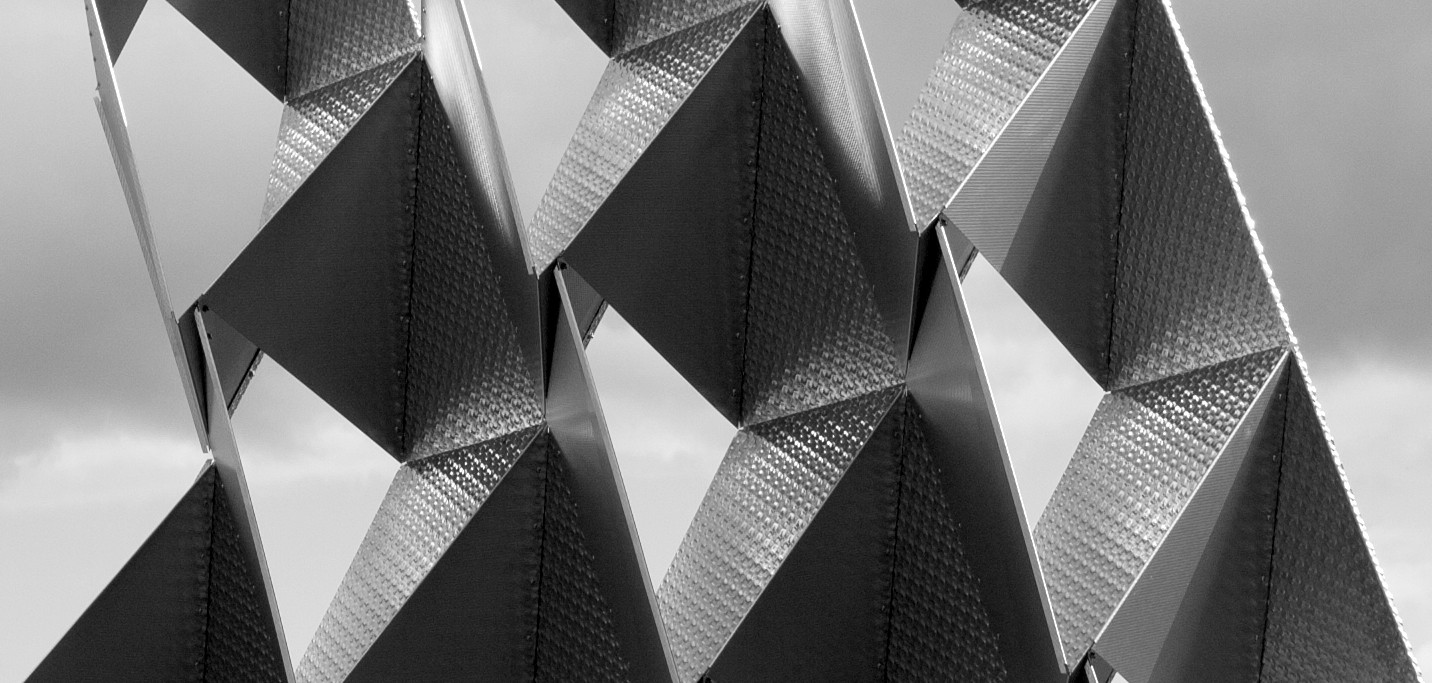
Here, the logic is that the amount of specular quality helps determine where the structural responsibility should be located – thicker gauges and deeper textures are placed in areas where the load is considered highest. This highlights the performance of the metal in compression and animates the surfaces by developing nuanced variations in light reflectance by mixing in complimentary textures.
The scheme is further developed along these lines where unit family types are determined by way of gauge thickness, structural role, and texture. The more deeply pocketed areas within the folds are placed between continuous (shingled) diagonal surfaces that perform as an exterior cross bracing. These units are stitched together from front to back, as are the more aggressively textured panels that connect the coursing of diagonal surfaces.
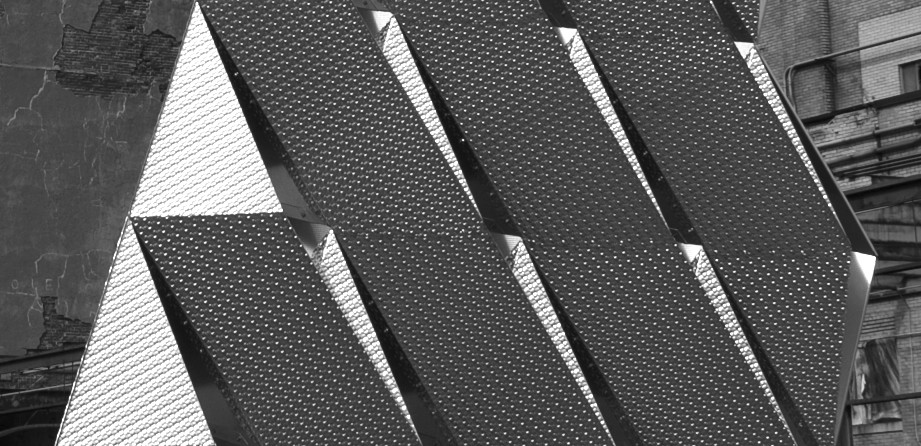
The diagonal elements are the most visually dominate while taking on the responsibility of handling the majority of the load transfer. Here, the structural capacity of the material is put to the test, and has been noted in the load tests of our mock-ups to be the areas of possible buckling.
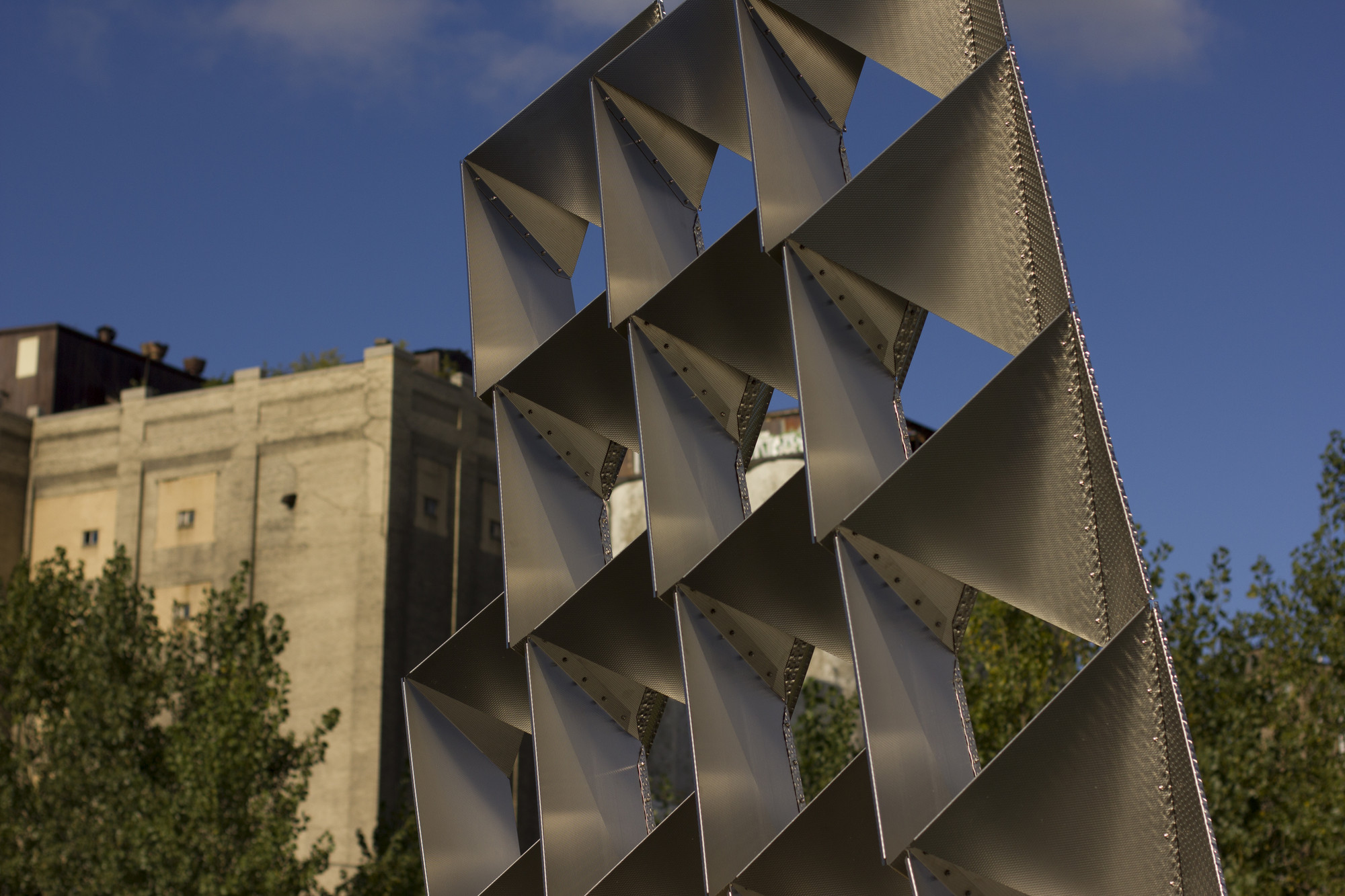