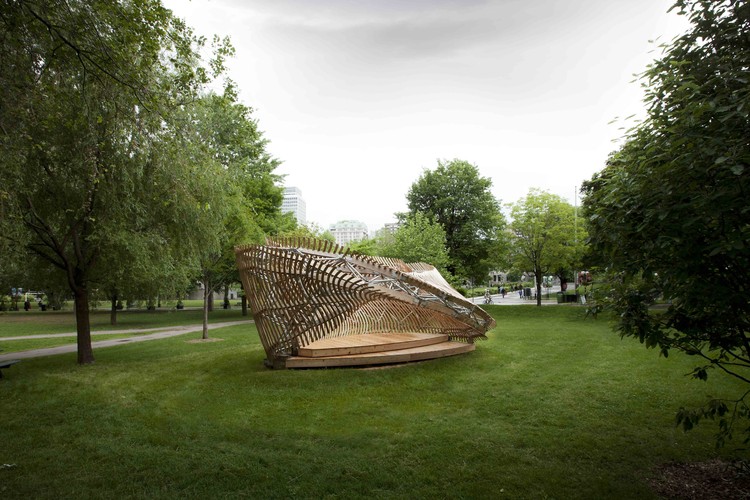
The ContemPLAY pavilion project is a student-led initiative by the Directed Research Studio (DRS) of the McGill School of Architecture, in coordination with the Facility for Architectural Research in Media and Mediation (FARMM), investigating new methods of practice. The project presented a unique opportunity for the students to learn through hands-on experience in an academic context. The pavilion occupies an 8.8m x 6.7m footprint with a total height of 3.7m in front of the Macdonald-Harrington building on the McGill University campus in Montreal, Quebec. More images and architects’ description after the break.
The structure itself is comprised of 140 planar plywood ribs joined together with another 140 sheet metal node assemblies which are triangulated into a space frame by 266 metal tubes. The entire structure is clad with 302 moiré strips fixed to the ribs by 1208 trapezoidal plywood joints. In total, there are 2056 discrete assemblies that comprise the pavilion and more than 3000 individually unique pieces of plywood, sheet metal and tubing.
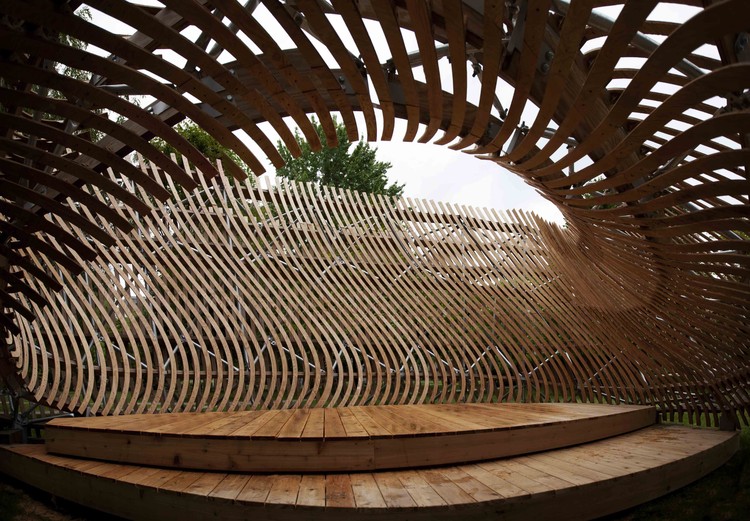
The pavilion’s hybrid lightweight space frame is formed by laminated plywood ribs and steel tubes clad with sinuous plywood strips. The complex structural system, in essence a space frame twisted around and attached to itself, provides a strong but flexible configuration that is capable of resolving the pavilion’s complex geometry without intruding upon the intended optical moiré effect. The effect is created by two apparent layers of cladding that define the volumetric envelope of the möbius strip. The laminated plywood ribs run along the möbius strip’s longitudinal isocurves, providing support for the moiré cladding elements, and are the main chords of the space frame.
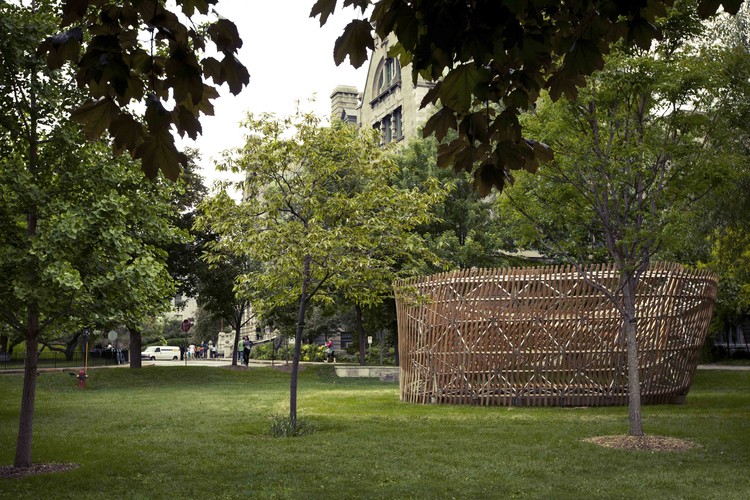
As primary structural members, these ribs experience both axial and bending forces. They are made of two layers of exterior grade BC fir plywood, laminated to a final thickness of 50mm. Transverse to the two surfaces of the möbius volume, a series of galvanized steel tubes with flattened ends form the bulk of the space frame structure. The ribs and tubes are connected to each other by two different types of steel plate joints. The first provides a pinned connection for the steel tubes. Pinned connection at all tube joints constrain them to work only under axial forces. The second connects the steel tubes to the plywood ribs, and the ribs to each other. Despite the compound angles of the incoming geometry, this joint also dealt with primarily axial forces.
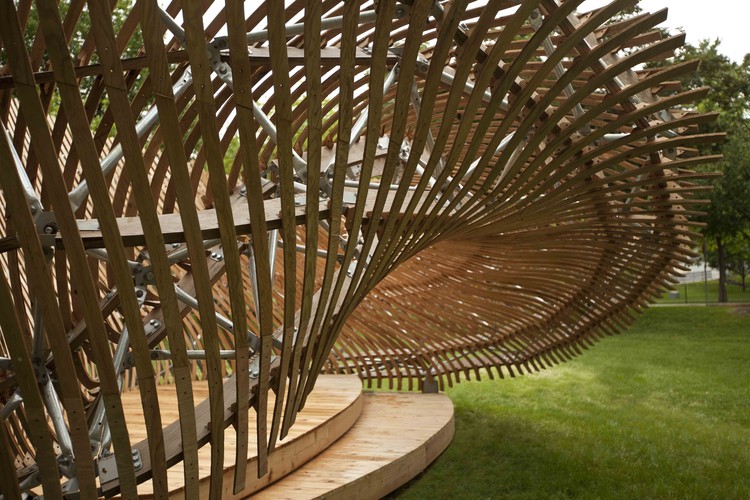
The complexity of the pavilion’s geometry creates a unique opportunity to undertake research through parametric modeling and digital fabrication. Parametric modeling consists of establishing a set of dynamic geometrical relationships to ultimately produce an entity with fixed dimensions. Its main advantage lies in rapid and flexible design exploration: designers can develop virtual prototypes, and simultaneously test the implications of changes on each of the multidisciplinary constraints shaping the project.

The selection of the möbius strip as a formal generator for the project necessitated a design, which would eventually require large numbers of similar yet unique components to resolve its continuously changing curvature. To deal with the formal complexity of the project, the team wrote a customized program in Grasshopper and vb.net to generate design iterations, create concept proofs, and mock-ups. For example, this type of parametric modeling played a decisive role in the evaluation of the perceptual influence of the space frame structure on the intended optical effect of the cladding.
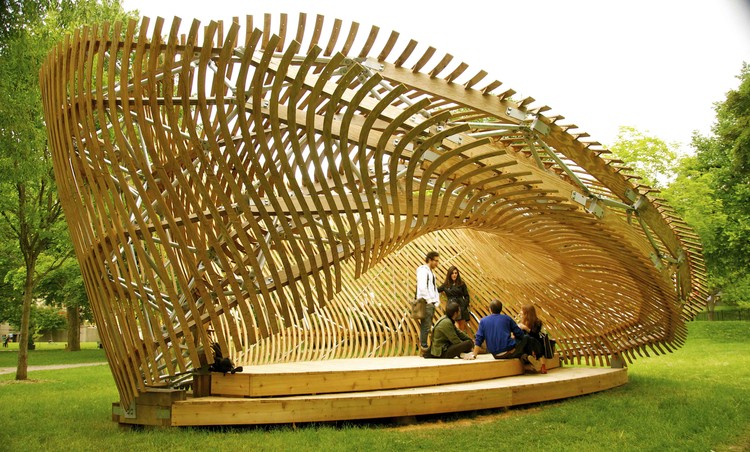
A driving principle in the design of the pavilion program was minimum static input and maximum dynamic derivation. Other than some numerical constants related to the real-world dimensions of construction materials, the program only required two simple geometric inputs: a digitally modeled möbius strip surface (representing the general shape and proportions) and a simple curve (used to derive the profiles of the cladding).
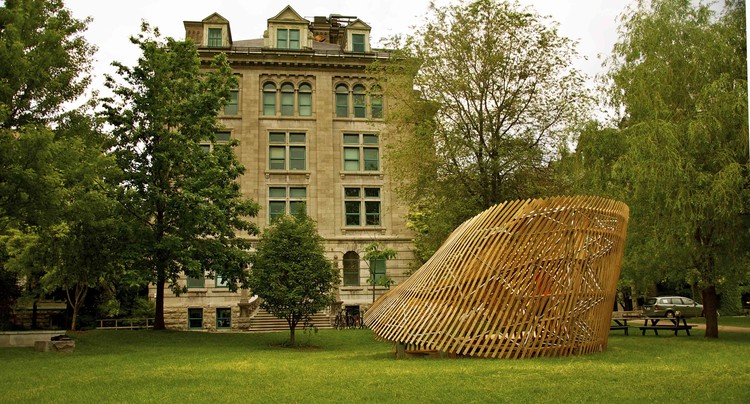
The mechanics of the program are complex but were conceived of as blocks of ideas, as in most commercial software. The first step is to define, from the input surface, a volume to contain structure. The second step is to design the structural system, which will support the pavilion and provide a skeleton for the constantly curving surface of the cladding. The third step is to derive the profiles of the cladding elements and map them onto the curving surface. The final step is to resolve each connection point of structural and cladding elements into a geometry that can be fabricated.
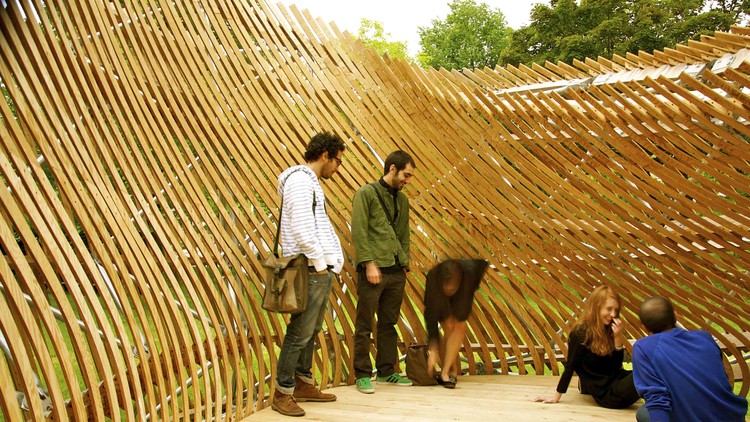
The transfer of the design information from the parametric model to the fabricators was facilitated by programs such as Rhinoceros 3D, RhinoNest, RhinoCAM, and Solidworks. The variability in length of the steel bars, the size and shape of the moiré strips and other wooden elements of the structure, and the specific bending angles in the steel joints are all factors requiring the use of automated processes and computational fabrication. The adaptability of the model and the digital fabrication tools employed permitted the fine-tuning of all architectural details, bringing the virtual model closer to the final built artifact, despite its geometrical complexity. The plywood ribs and moiré strips were cut using a 3-axis CNC router, shared by School of Architecture and Faculty of Engineering. Nearly one hundred sheets of plywood were consumed to produce all of the components fabricated in-house.
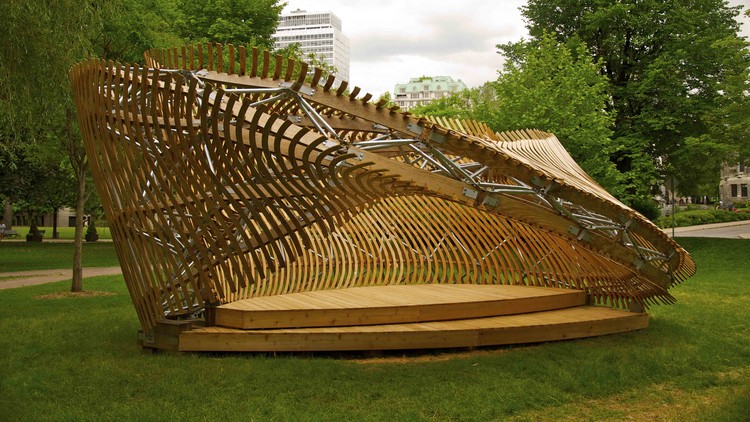
The steel joints were manufactured by a local prototype fabricator with CNC bending capabilities. The precision of this process was necessary to bridge between the continuous doubly-curved geometry of the overall möbius shape and the planar components. Digital fabrication of the ribs, moiré and the steel joints permitted the assembly of an irregular space frame that could adapt to the variable curvature of the surface. This shape would not allow for the mass production of similar parts but required 2175 unique components to generate its structure and cladding. Despite each piece being fabricable by more conventional technology, it was the variability and precision of the digital fabrication process that allowed us to produce so many components which, despite some minor deviation from the digital model during assembly, still fit together within their tolerances to yield the form.
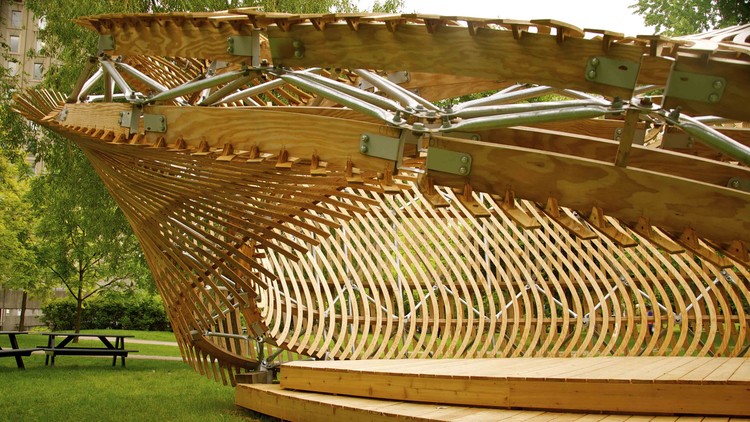
The pavilion sits, in a number of uneasy ways, between states. Its overall form is that of a möbius strip, a continuous, non-orientable surface, which confounds interiority and exteriority. The cladding and structure reinforce the state of uncertainty induced by the möbius geometry. As the object is approached, the visual field is interrupted by movement-induced interference and the viewer becomes aware of an optical fluctuation of the surface of the pavilion via the moiré effect. Perception oscillates between the form of the continuous möbius surface to the shifting pattern of the cladding. Light filters through the cladding, reinforcing the ambiguity of the place. The möbius itself vacillates between an appearance of relative volumetric solidity and a doubled set of surfaces. It is within this unstable appearance that a new place to sit, relax and think is provided literally outside of the otherwise more stressful academic environment of the contemporary classroom.
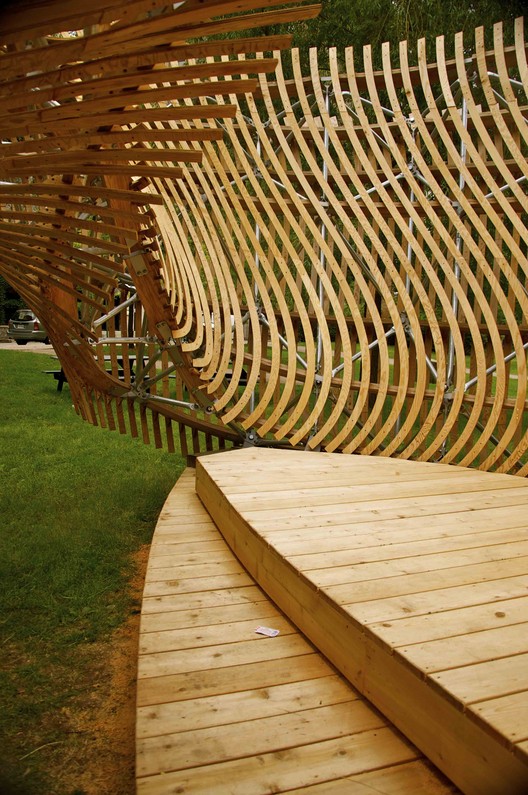
A revolution in digital modeling tools has enabled a new generation of designers to model anything that they are capable of imagining. A typical problem with many of the resulting designs is that it is very difficult to move past the formal superficiality of the digital model into confronting the physical limitations and complications of construction. The production of the ContemPLAY pavilion engaged the question of learning not through the representation of potential project but in questioning through making. In this way, formal possibility and technical complexity were interrogated by fabrication. As a designbuild effort, the project team confronted research into cutting-edge processes within the many challenges of bringing any design to reality.
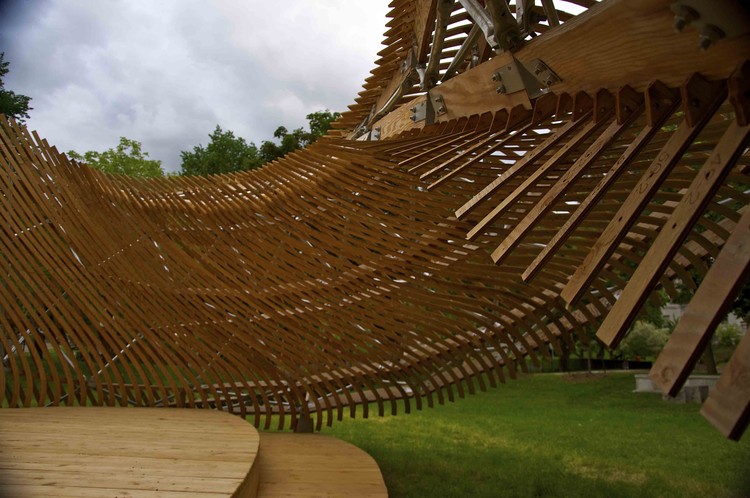
The ContemPLAY pavilion project began as an exercise in parametric design and digital fabrication, and the built form now exists as an architectural statement about resolving complexity. The pavilion is a device for provoking inquiry, thoughtfulness, and even wonder about spaces and objects in one’s environment. It manipulates viewers’ perceptions through its overall form and carefully arrayed details, inviting the user to discern the boundaries between public furniture, shelter, and art. DRS masters students in coordination with the Facility for Architectural Research in Media and Mediation (FARMM) are responsible for the design, fabrication and assembly of the parametric pavilion.
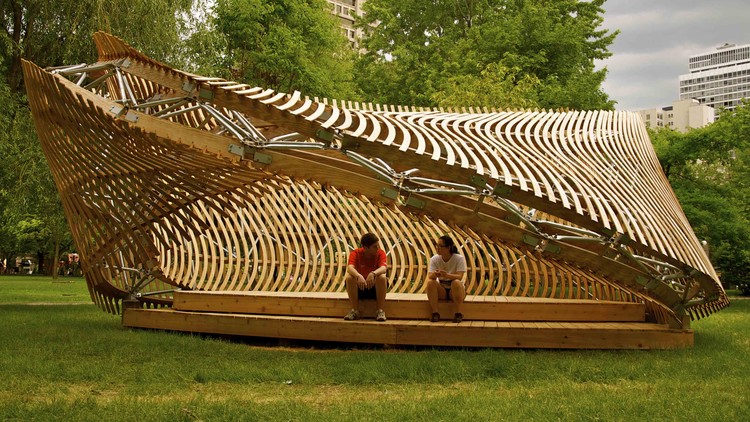
Architects: Directed Research Studio (DRS) of the McGill School of Architecture in coordination with the Facility for Architectural Research in Media and Mediation (FARMM) Location: Montreal, Quebec, Canada Project Team: Hamza Alhbian, Simon Bastien, Justin Boulanger, Evguenia Chevtchenko, Elisa Costa, Nicolas Demers-Stoddart, Andrew Hruby, Olga Karpova, Shelley Ludman, Diandra Maselli, Courtney Posel, Dina Safonova, Dieter Toews, Sophie Wilkin (McGill DRS students) Instructed by: Maria Mingallon and Jason Crow Sponsors: Acier Altitube, Corbec, Desmarais Cousineau Yaghjian St-Jean Architects, Groupe Canam, Institut canadien de la construction en acier, Jodoin Lamarre Pratte Architects, McGill University, Menkès Shooner Dagenais Letourneux Architects, Parametric Structures + Design, PGSS (Post-Graduate Students’ Society of McGill University), Proto Plus Precision, Rubiks, Saia Barbarese Toupanov Architects, Simpson Strong-Tie, Natali Films Year: 2010 – 2012