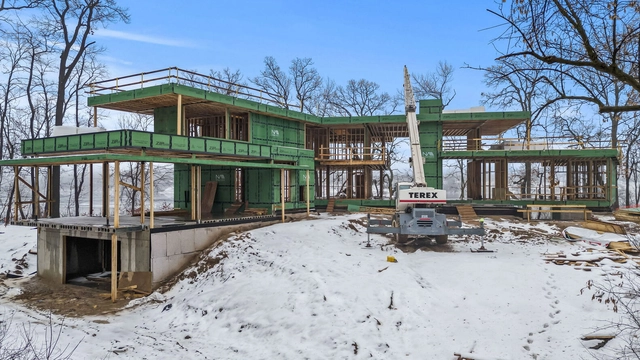
In the construction industry, light wood-frame offsite construction has emerged as a game-changing approach, promising faster build times, higher quality, and reduced environmental impact. Member companies of the Quebec Wood Export Bureau (QWEB) have launched a digital tool that harnesses the benefits and potential of prefabricated light wood-frame products for projects.

It all starts with the BIM environment. QWEB and its members have built a digital tool called Offsite Wood for professionals seeking to delve deeper into offsite wood construction. It offers a wealth of downloadable content, technical specifications, and case studies. It highlights the extensive use of BIM technology among QWEB members, showcasing how digital tools can streamline the prefabrication process and improve project outcomes. By leveraging these resources, industry professionals can stay informed about best practices and innovations in offsite construction.
In addition, prefabricated light wood-frame products from QWEB members are diverse and adaptable to various building types, including single-family homes, apartment units, luxury homes, and commercial buildings. Among the key products are prefabricated wall panels, which are factory-made and often include wood framing, insulation, and barrier membranes, sometimes even incorporating windows and exterior siding. These panels are transported to the construction site and quickly assembled to form building walls.
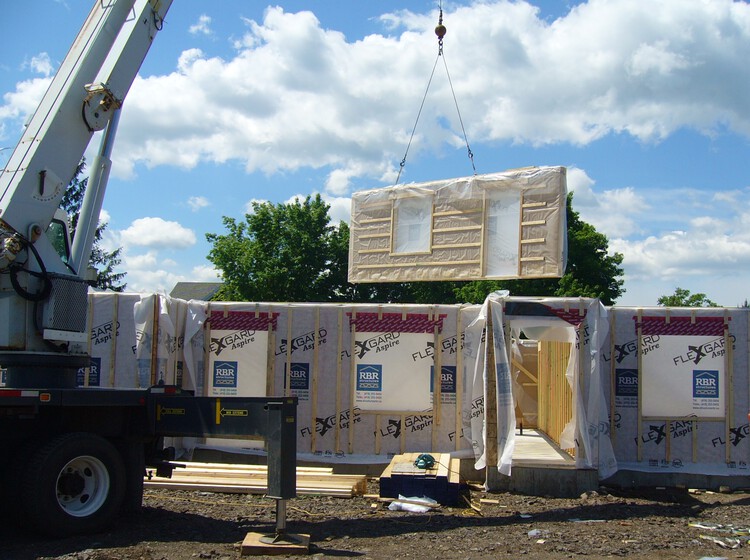
They also take into account on-site construction, which minimizes disruption to local ecosystems, preserves biodiversity, and aids CO2 absorption. Durable and recyclable prefabricated components reduce the demand for new materials, further lowering emissions. By integrating these factors, prefabricated construction plays a significant role in the construction sector’s efforts to combat climate change, enhancing sustainability and environmental responsibility.
'Construction projects these days are about saving time. Not only to stick to a tighter budget but to simply build faster with better quality. This is what we bring to the table as a trade association. Our members adapted their way of working to answer this very need for offsite construction.' – Alain Boulet, Wood Construction Group Director at QWEB.
While housing prices and shortages are making the headlines, Quebec light wood-frame companies like AmeriCan Structures and NA Structures have stepped up to the plate to give solutions to the industry. From the early-phase conception to the complex logistics that an offsite construction project requires, they have the know-how to produce and deliver high-quality products to meet the budget and schedule of the clients.
To do that, they focus on the flexibility and modularity of prefabricated components to provide exceptional design flexibility and an easier adaptation to site-specific constraints. Despite higher initial costs, the savings on labor, construction time, and delays result in a better overall return on investment. These advantages make factory-prefabricated components a compelling solution to labor shortages, providing superior quality, safety, and cost efficiency.
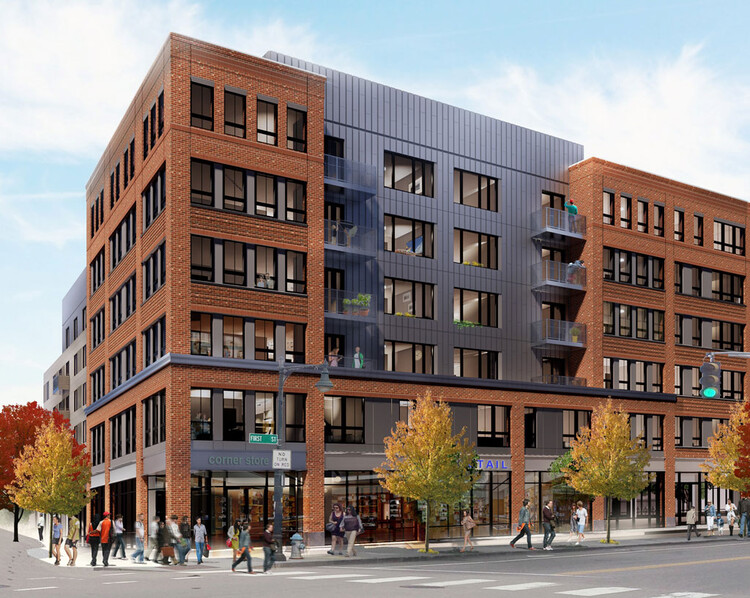
Custom-made luxury homes, designed in the BIM environment and built 'on-screen first' to solve all possible defects before the work on site begins, serve "to lighten the burden on the shoulders of the architect and the general contractor,” added Mr. Boulet. “Multihousing projects using wall panels, floor and roof trusses, also designed in the BIM environment, reduces the on-site schedule so the investor gets a faster return on their investment while obtaining a higher quality product.”
The Offsite Wood initiative that combines BIM tools is helping architects to unlock the full circularity benefit of their buildings. It offers hope by influencing design studios and architects to prioritize materials and design for circular economies with long-term reusability goals.
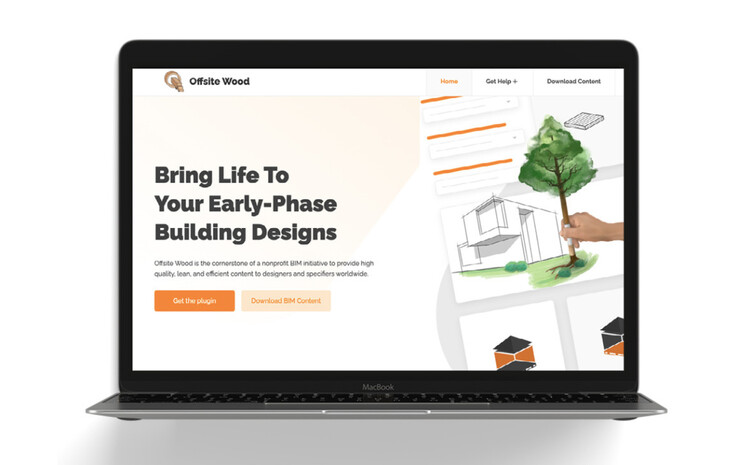
For inquiries, meeting scheduling or more information about Offsite Wood, write directly to info@quebecwoodexport.com.