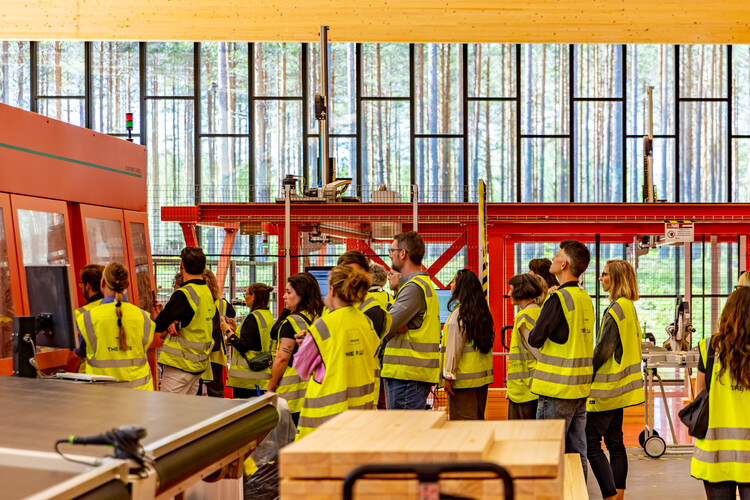
It’s now clear that approximately 80% of emissions from landscape architecture projects come from materials. This includes the extraction of natural resources, and their manufacturing, transportation, and construction in parks, plazas, streets, campuses, and neighborhoods. A significant portion of emissions in the built environment can be traced back to two materials: concrete and metal, which includes steel and aluminum.
The challenge lies in the fact that we use a large amount of both materials, they are difficult to replace due to their strength and utility, and improving their environmental impact is a complex process. But progress is being made.
Low-Tech Solutions for Concrete
At a concrete decarbonization convening earlier this spring, I was overwhelmed by high-tech strategies that seemed inaccessible, expensive, and impractical. Then, Dr. Alice Titus Bakera, a civil and structural engineer from Tanzania at EPFL, presented a refreshingly common-sense approach to reducing construction emissions in her country:
Use Less
In Tanzania, solid concrete blocks are commonly used for buildings and walls due to their strength and ease of construction, accounting for 80 percent of the country’s cement production.
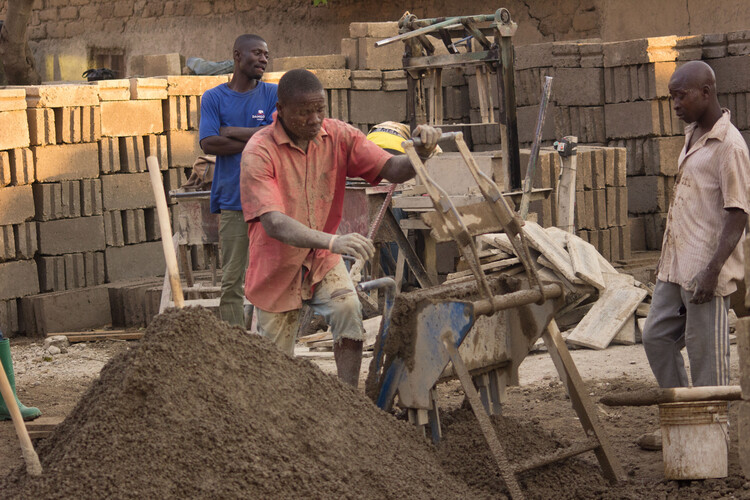
However, if these blocks were hollow and interlocking, they would have significantly less mass and require no mortar. These interlocking blocks also allow for easy assembly, re-assembly, and reuse, with air gaps aiding in temperature regulation. These blocks, similar to concrete masonry units used in North America, are not available in all parts of the world.
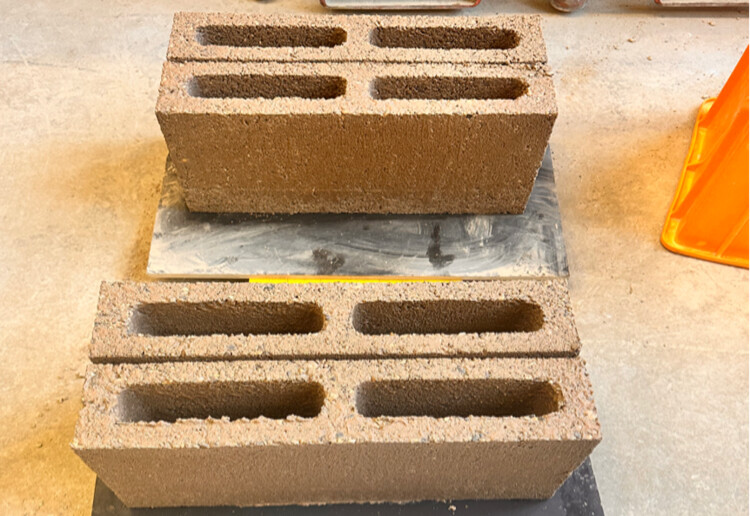
Use Better Materials
Minimizing overdesign and reducing cement in non-load-bearing mixes can also decrease carbon dioxide emissions. While using supplementary cementitious materials (SCMs) like slag, fly ash, and pozzolans can help, these are not always available, especially in developing communities.
Dr. Titus Bakera emphasized the need to work with locally available materials. Ordinary Portland Cement typically consists of 95% clinker and 5% gypsum. Instead of searching for SCMs, we can use materials with naturally lower carbon content, like calcined clay and limestone.

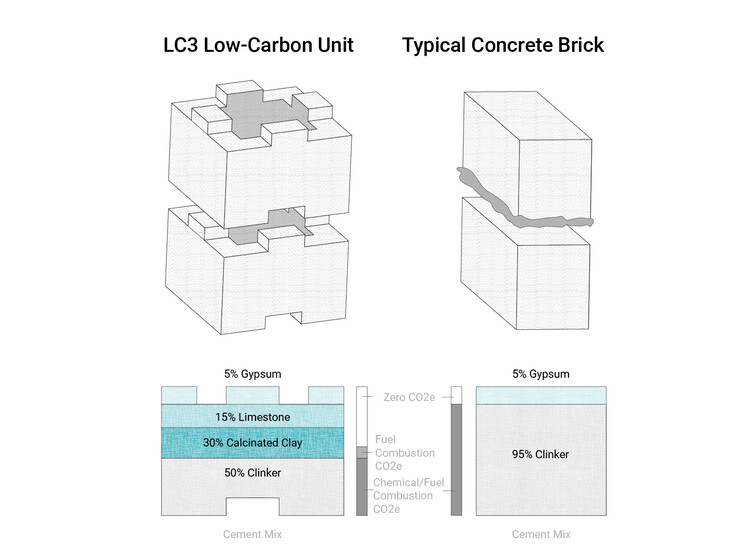
Limestone Calcined Clay Cement (LC3), developed by EPFL professor Karen Scrivener, uses nearly half the amount of clinker, cutting emissions by over 40 percent.
These materials are abundant, cost effective, don’t require modifications to existing manufacturing facilities, and are already in use.
While this approach may seem simple, working smarter, not harder in this decade of decisive action is crucial.
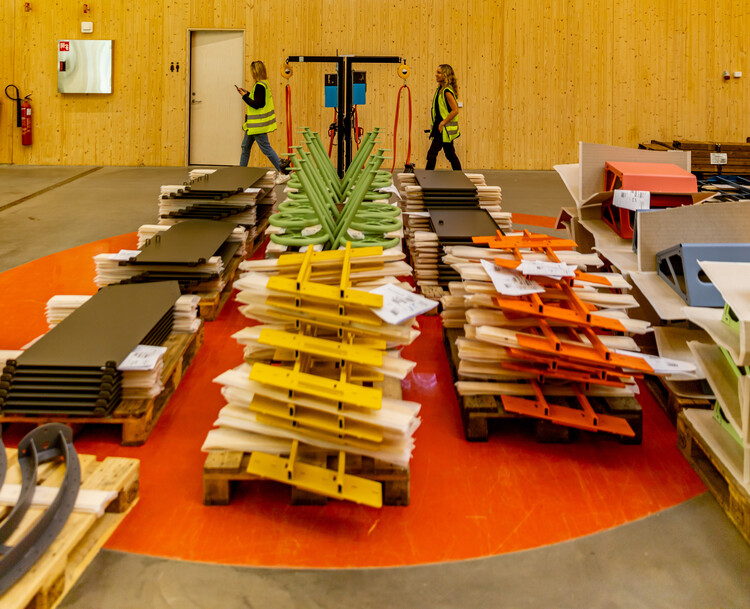
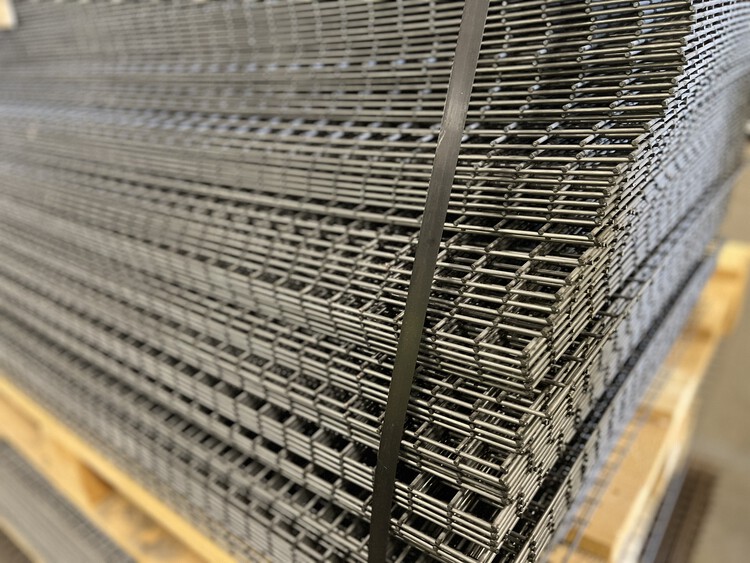
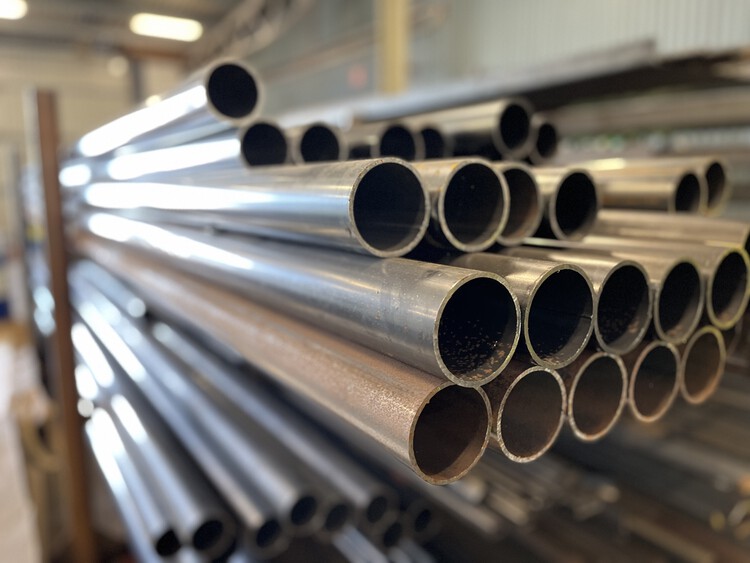
High-Tech Innovations for Steel
Fossil-free steel—can it be real? I recently delved into this topic to understand the energy-intensive steel manufacturing process and possible improvements.
Current Process
Steel is typically made by extracting iron ore using fossil-fuel-powered equipment, trucking it, mixing it with coke derived from burning coal, and heating it to high temperatures in a blast furnace to create crude steel, which is then refined.
Only 25-30 percent of current demand can be met with recycled steel. Even with 90 percent of steel being recycled, a smarter process is needed.
HYBRIT Technology
Swedish steelmaker SSAB has developed the Hydrogen Breakthrough Ironmaking Technology (HYBRIT). Instead of using fossil fuels, hydrogen is split from water via electrolysis to heat the steel in a blast furnace, creating “sponge iron” with no greenhouse gas emissions. This is mixed with scrap metal before forming slabs for use.
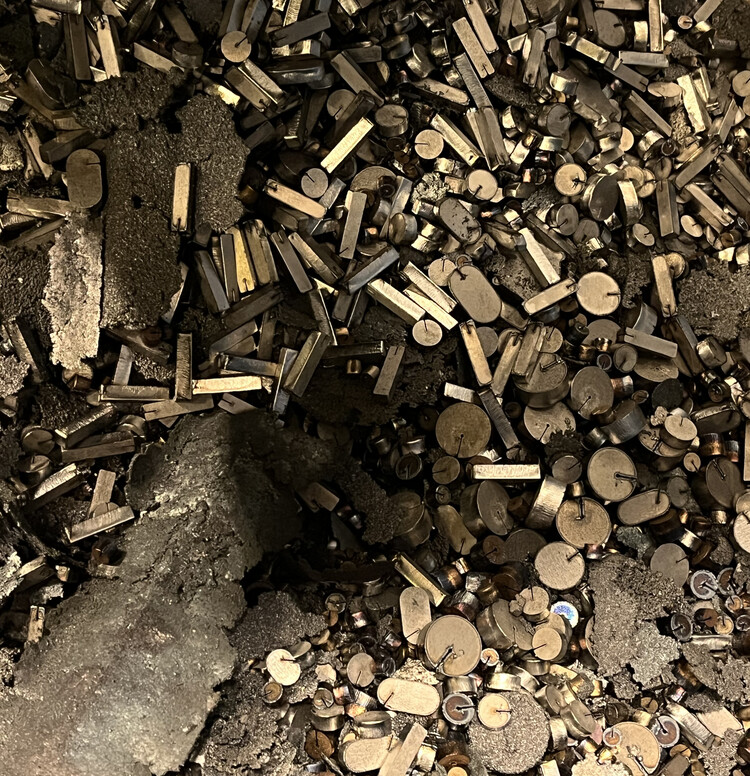
To get the entire process fossil fuel-free, SSAB and its suppliers intend to use 100 percent non-fossil fuel equipment for extraction and transport, including battery-operated machinery and bio-fuel-powered ships.
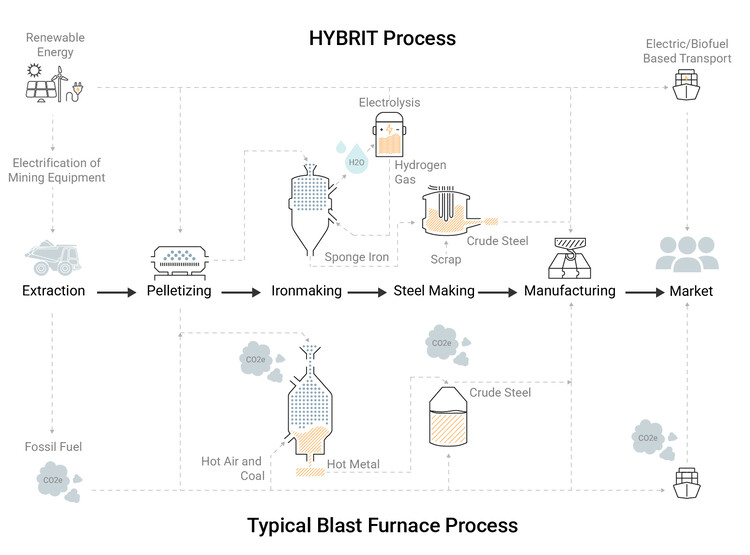
While Volvo currently claims most of SSAB’s fossil-free steel, landscape architects will soon have the chance to specify the remainder in site furnishings.
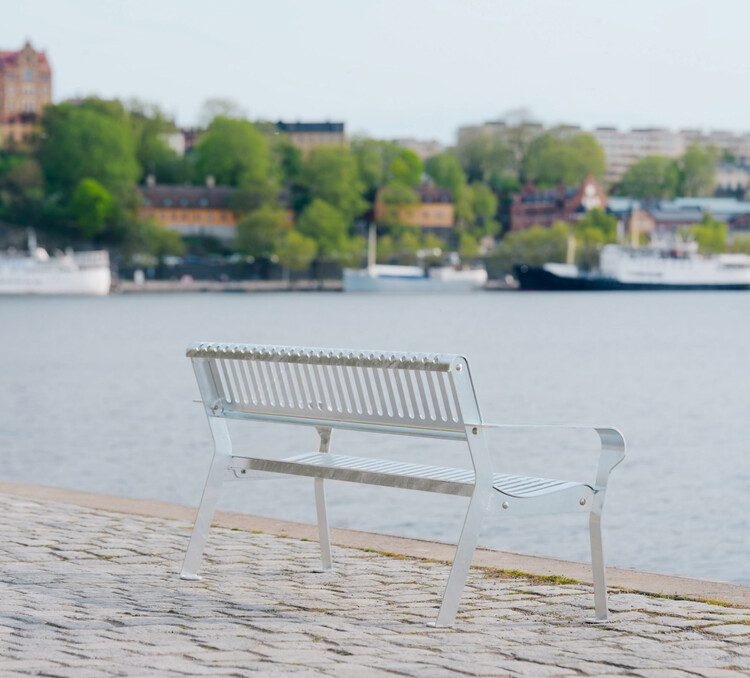
The Bottom Line
While designing out these materials would be ideal, hybrid approaches will likely be necessary even with Nature-Based Solutions. For example, to meet the strength requirements of a living shoreline, some concrete and steel reinforcement may still be needed.
Step one is to minimize use. Step two is to design for efficiency with strategies like hollow LC3 blocks or fossil-free steel to move closer to zero emissions.
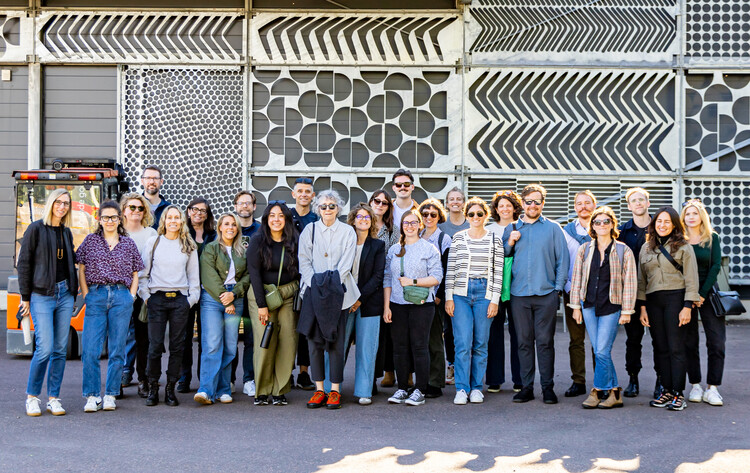
There are no silver bullets – concrete, steel, or otherwise – to solve the climate crisis. It will take different perspectives and innovative thinking to make progress, and all contributions are welcome.