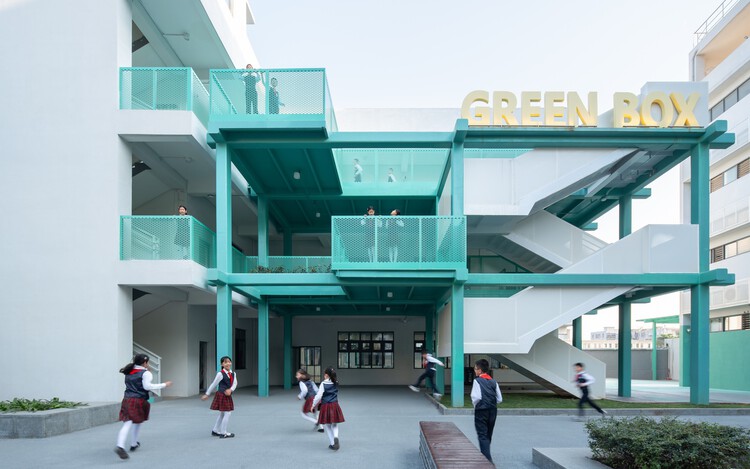
Evolving urban conditions call for an evolving builtscape, and retrofits have been a key mechanism to allow buildings to adapt and respond to new needs. Amidst global environmental concerns, climate retrofits have become a popular strategy to upgrade buildings based on improved operational efficiency. Global decarbonization plans have even called for city-wide retrofits, such as in the case of London, to meet civic goals. While such upgrades significantly reduce energy consumption, they often come with a hidden cost - embodied carbon in retrofit materials and the potential for future waste.
Building retrofits typically focus on two main areas: the building fabric and building services. For example, buildings in temperate climates may prioritize reduced heat loss through improved insulation, double or triple glazing, and insulated doors. Such measures can dramatically decrease a building's energy demand, leading to lower operational carbon emissions and reduced heating costs for occupants.
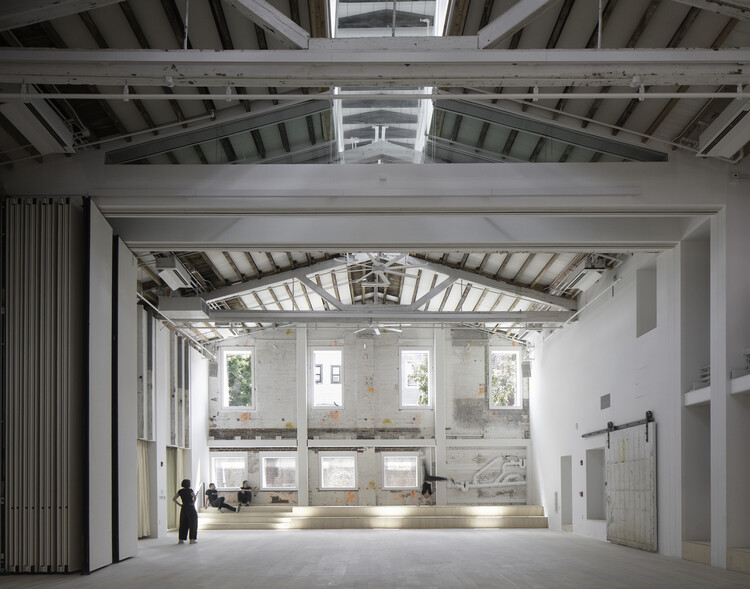
Materials used in climate retrofits, such as insulation and glazing, are often overlooked for their own carbon footprint. Embodied carbon from emissions associated with the production, transportation, and installation of these materials lose emphasis in the push for immediate energy efficiency gains. Many common retrofit materials have limited lifespans, and the longevity of these retrofit solutions is rarely considered. In the pursuit of maintaining optimal energy efficiency, buildings may require frequent upgrades or replacements of retrofit components. This leads to a legacy of waste and recurring embodied carbon as components degrade and require replacement.
Towards a Circular Approach
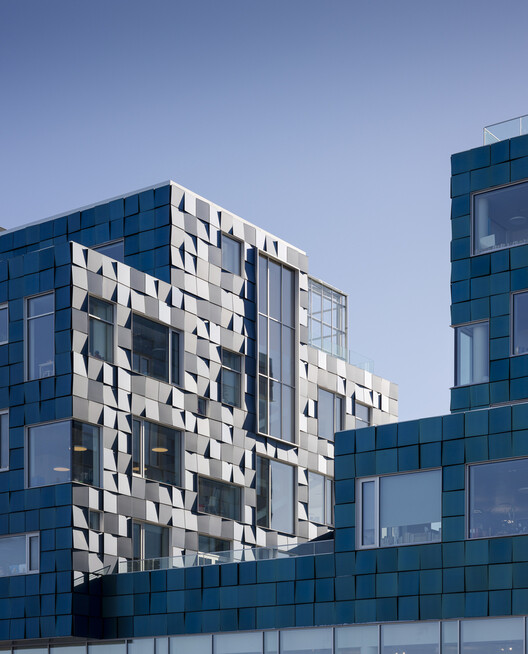
To address this challenge, experts are calling for the integration of circular economy principles into climate retrofit practices. The circular economy aims to keep materials at their highest value for as long as possible, prioritizing reuse and remanufacturing over recycling or disposal. In the context of building retrofits, this could result in design solutions that allow for easy replacement of insulation without damaging surrounding materials, or developing systems that can be remanufactured in situ rather than fully replaced. Such procedures would help reduce waste while minimizing the regular embodied carbon associated with repeated retrofits.
The consideration of the total lifecycle of the building lies at the heart of a circular approach to building retrofits. Architects should lean towards solutions that are easily dismantled and reassembled, and the use of durable or readily recyclable materials. Standardizing components through modular systems allows for future upgrades and replacements without major renovations. Similarly, ongoing performance monitoring becomes essential to identify areas for improvement. This data can then inform decisions about component replacements, ensuring optimal efficiency throughout the building's extended lifespan.
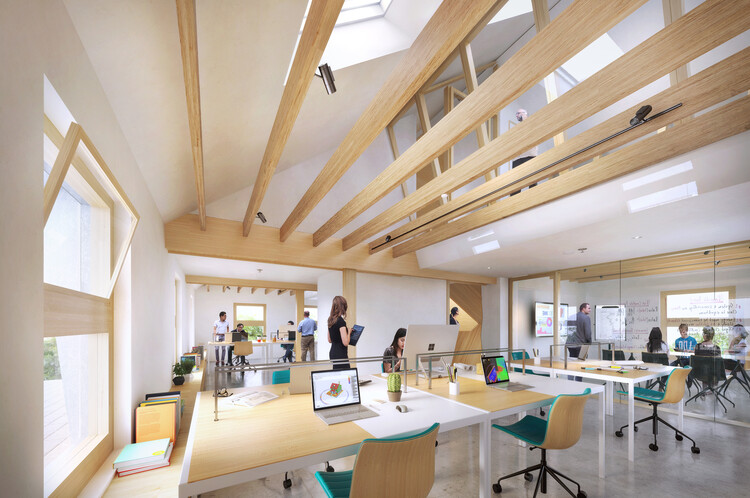
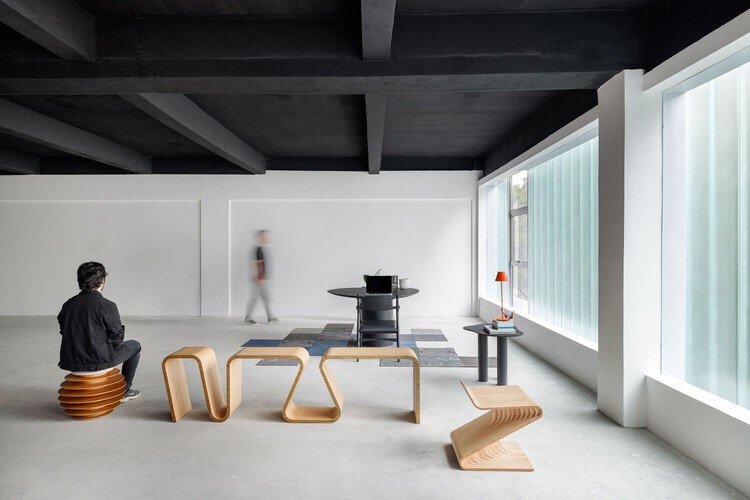
While circular retrofits hold immense promise for a more sustainable built environment, certain roadblocks stand in the way of their widespread adoption. A crucial factor is the need for an upskilled workforce with training in new installation techniques, deconstruction, and material recovery. The industry as a whole need to be instilled with a mindset of disassembly rather than demolition.
The transformation needs to extend beyond construction sites. The development of performative supply chains is important to support the remanufacturing and recycling of retrofit components. This may involve the creation of entirely new specialist roles within the construction sector, fostering a more circular approach throughout the entire building lifecycle.
Educating homeowners and building managers will help operationalize any policies and regulations from governments to uphold circular retrofit principles. While circular retrofits may have higher upfront costs, they offer superior long-term value. Supportive incentives, regulations, and updated building standards that prioritize circularity can help address these challenges collaboratively.
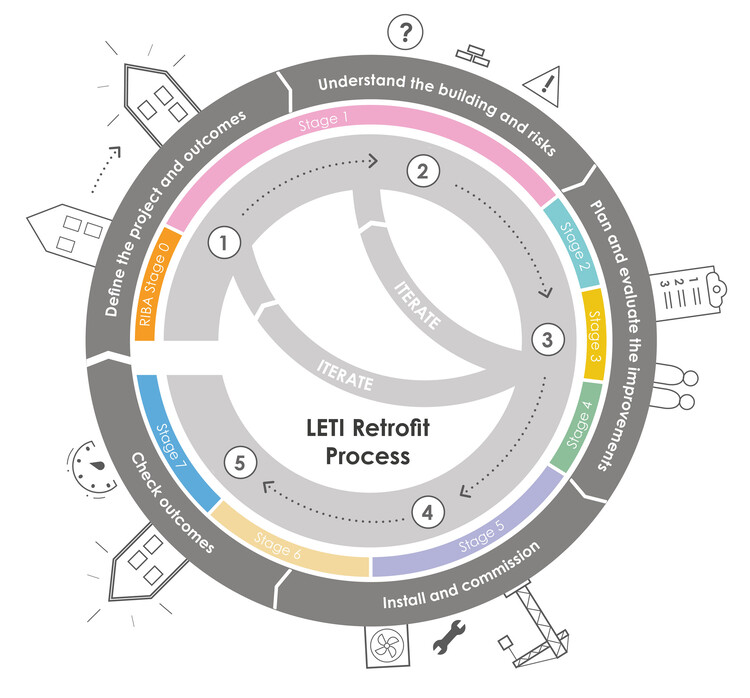
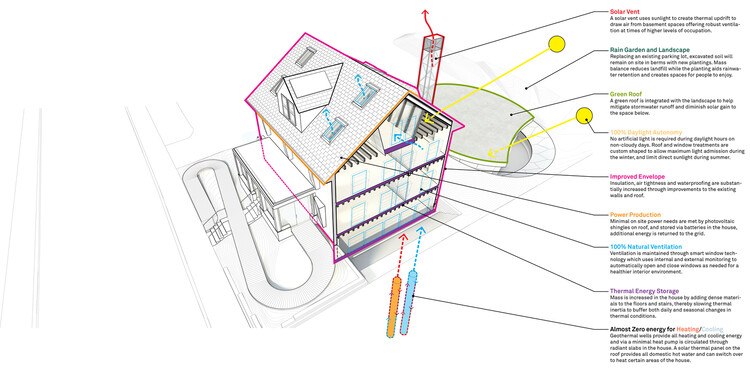
The urgency of implementing circular retrofits cannot be overstated. In England alone, it's estimated that a wall area of approximately 3 billion square meters requires insulation. If this is done using traditional methods, it could result in 300 million cubic meters of insulation material that will eventually require end-of-life processing. Without circular approaches, this massive volume of material is likely to end up in landfills or incinerators, representing a significant waste of resources and a major source of future emissions.
The transition to circular retrofits will require collaboration across the entire construction industry, from architects and engineers to manufacturers and installers. It will also necessitate supportive policy frameworks and innovative financing models. Circular retrofits offer a path to reduced operational carbon emissions and hidden carbon costs, enabling future-proofed buildings for decades to come.
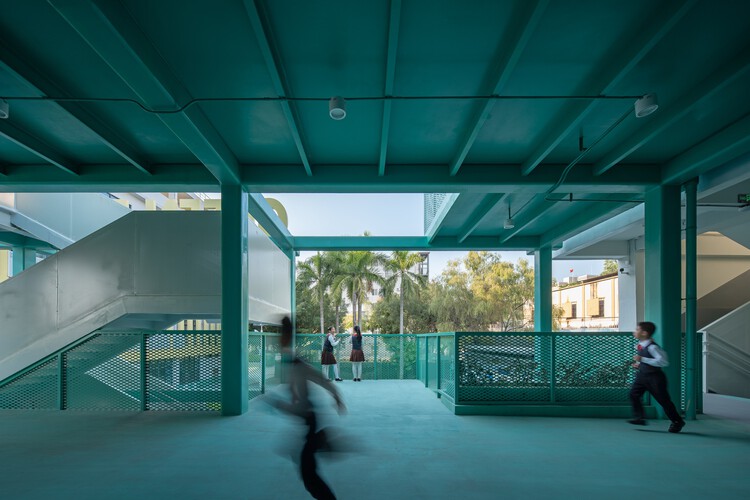
This article is part of the ArchDaily Topics: Refurbishment, proudly presented by Sto.
Extending the lifespan of buildings reduces cost and environmental impact, avoiding demolition or more substantial interventions in the future. Sto's products for facades, facade refurbishment, crack repair, waterproofing, and concrete restoration systems are used on heritage buildings, adaptive reuse projects, renovations, and maintenance of new buildings all over the world. Every month we explore a topic in-depth through articles, interviews, news, and architecture projects. We invite you to learn more about our ArchDaily Topics. And, as always, at ArchDaily we welcome the contributions of our readers; if you want to submit an article or project, contact us.