Architecture, understood as a cultural product, is strongly influenced by diverse stimuli that include historical, geographical, and cultural aspects, among others. Together, these elements form a heritage that may (or may not) endure through time. Although architecture tends to adapt to each culture, modeling its traditional techniques according to its context and shaping the surrounding environment, there is no guarantee that the traditional elements in it will endure or remain unchanged over time. This is largely due to the constant evolution of society and technology, which sometimes tends towards universality and the adoption of a common language, rather than one of their own.
Given this scenario, it is essential to explore an approach where innovation and technology do not replace tradition and artisanal production; instead, they arise as a means of exploration towards emerging routes. Adopting novel techniques and innovative materials that are adapted to specific local needs makes it possible to maintain an authentic expression that responds to the demands of the environment. This approach, which could be termed neo-craft, allows for the preservation of a distinct voice that reflects the authenticity of the local context. At the same time, it contributes to a universal perspective, merging the local with the global.
In this exploration of the dichotomy between tradition and innovation, we can find outstanding examples, such as the Talavera Project, a research initiative carried out by MANUFACTURA in collaboration with Uriarte Talavera. This workshop, founded in 1824, boasts recognition as the first producer of Talavera —a glazed ceramic distinctive of Puebla— in Mexico. The Talavera process was introduced in the region in the 16th century with a strong influence of Muslim and Chinese ceramics and is now recognized as an Intangible Cultural Heritage of Humanity.
The research addresses fundamental problems in the production of Talavera: the lack of innovation and the high level of waste, given that it is a material and process with a designation of origin, protected by local regulations. Hence, the main purpose of this project focuses on a piece whose objective is to make visible the synergy between tradition and technology, creating a new dialogue between handmade craftsmanship and innovation.
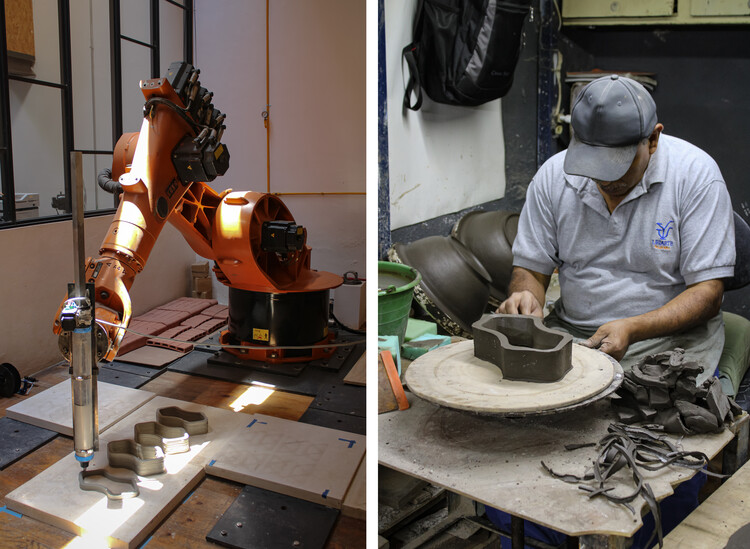
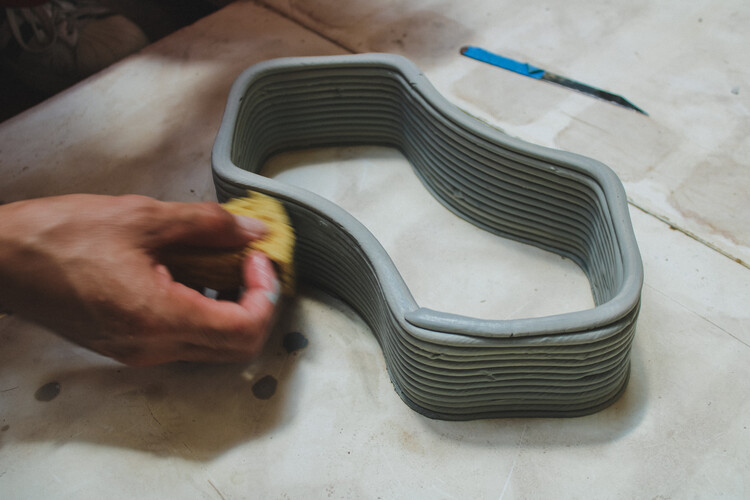
As part of this project, we spoke with Dinorah Schulte to delve deeper into the process. During our discussion, we explored the potential contributions that digital fabrication could offer, drawing insights from research like this.
Enrique Tovar (ArchDaily): By working with local ceramics in this project, what challenges did you face in printing with the robotic arm, and what role did the high-temperature furnace play in the process?
Dinorah Schulte: One of the biggest challenges is that being a protected material, this clay cannot come from another region because it ceases to be Talavera and becomes ceramic. Also, it cannot be intervened by anyone; only certified artisans can work on it following the ordinances dictated since the arrival of this material to our country (Mexico). So it could not be part of any innovation process, such as printing it directly with the robotic arm. We first worked with ceramic, by printing a piece. Using that piece, we created replicas with five molds, enabling us to produce 80 replicas using the Talavera technique.
The high-temperature furnace that we initially used allowed us to make a "fossil" piece. With this, we could enable the replication of numerous pieces in the artisanal technique of Talavera, originating from an industrial process such as 3D printing. These pieces exhibit much more complex geometry than those modeled by hand and take advantage of the precision of the machine.
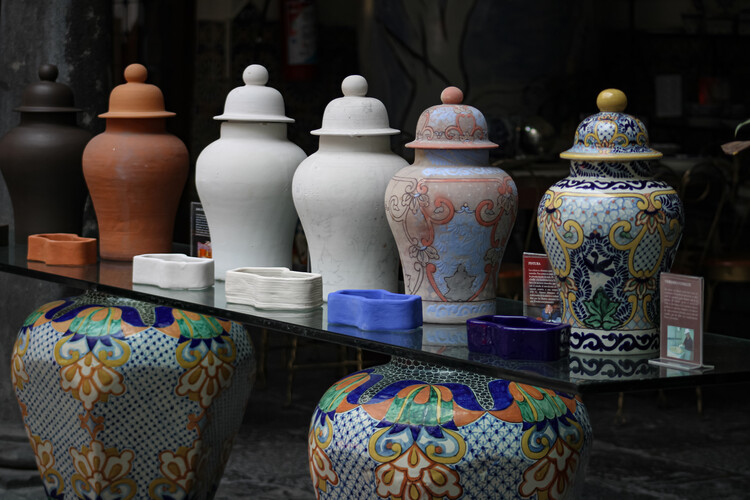
The project illustrates the interconnectedness of water in creating the distinctive cobalt blue color palette. This iconic hue originates from a mineral amalgam of aluminates and cobalt silicates, capturing the very essence of Talavera
ET (AD): In the realm of digital fabrication, we frequently come across pieces with diverse shapes, a result of the interplay between the form and the technical capabilities of the materials employed in the manufacturing process. In this instance, what considerations prompted the selection of this particular shape?
DS: The shape comes from an abstraction of the original drawing of a baroque cross formed by 4 petals, that we extracted from the catalog of tiles from the Uriarte Talavera workshop, which are part of a very old collection made up of baroque and organic strokes, part of the architectural culture of Puebla. Replicating each piece took about four weeks because the process of modeling and drying was done entirely by hand, without the use of electricity. To optimize time, we decided to only manufacture a single piece, instead of several different ones, and be able to arrive on time for delivery.
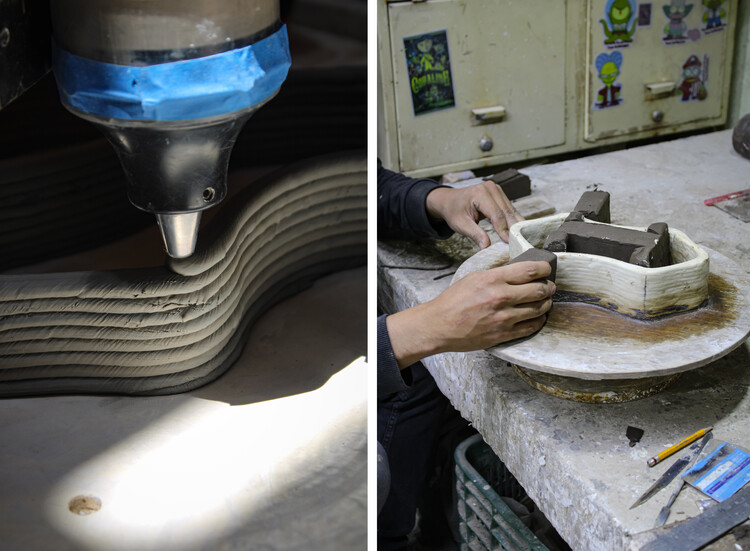
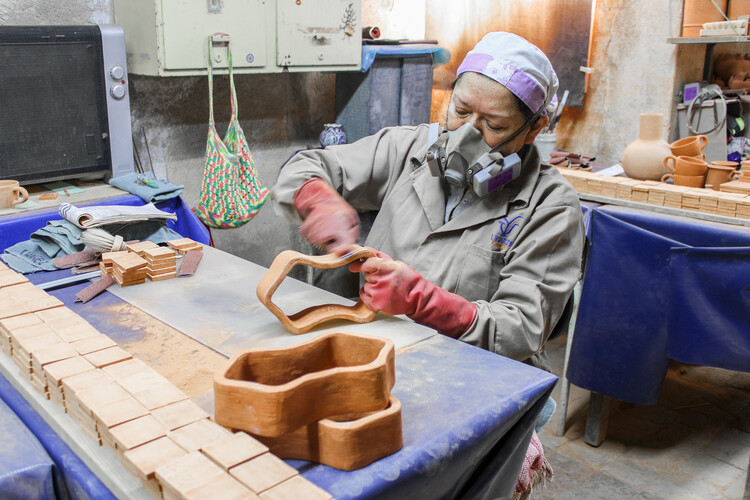
ET (AD): When merging traditional and digital production processes, were there moments when the dimensions or curvatures of the pieces posed challenges for the artisan-piece interaction?
DS: Yes, there were differences between the pieces all the time because they come from an artisanal process; each piece is different and we had to take that into account to generate greater tolerances with the structure that supported it. Additionally, we implemented a mechanism where, when stacking each piece on top of another, it would not significantly impact the height or stability of the pieces. The pieces are different because they are molded, sanded, enameled, and painted completely with manual processes by a group of more than 10 certified artisans who made the manufacturing of these pieces possible.
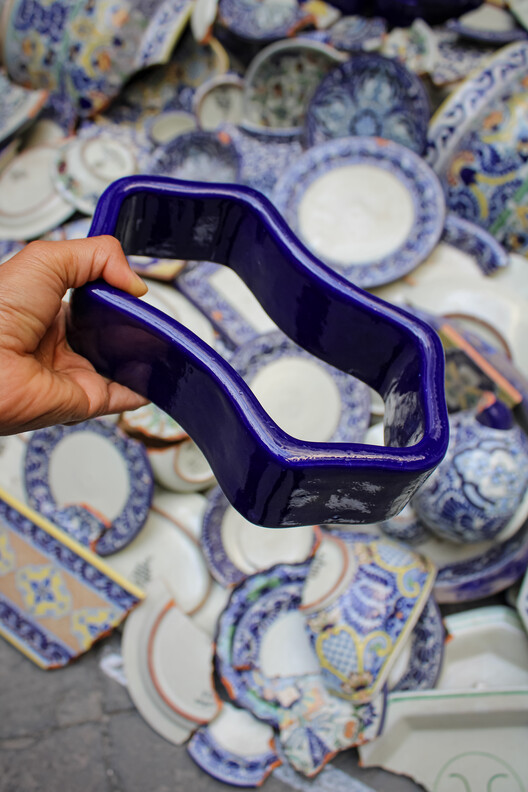
ET (AD): Challenges such as cost, fabrication time, and high waste production are typical during the manufacturing of traditional Talavera. Was there a notable reduction in waste achieved during the combined process (digital-traditional) for Talavera fabrication?
DS: It is very common to see an artisanal process move towards an industrial process, seeking the greatest optimization of waste, time, and precision, but this is the first time we have tested what happens if we do the process in reverse and what the exchanges are between both manufacturing processes. That was one of the great achievements of our collaboration, because since it was such an accurate and precise piece –the result of robotic and automated 3D printing– the artisans excelled.
It was quite easy to make the molds for the replicas of the pieces and they did not contain any dimensional errors. The only true aspect is that, in the traditional Talavera process, small residues are obtained due to the manual process. We cannot be part of or modify it, as it is a protected process and part of the cultural heritage.
We aim not to replace anyone but rather to complement existing jobs with the rich heritage wealth that enriches our culture, making it more solid and ensuring its permanence in our society. This, in turn, strengthens our identity and creates new labor opportunities in our context.
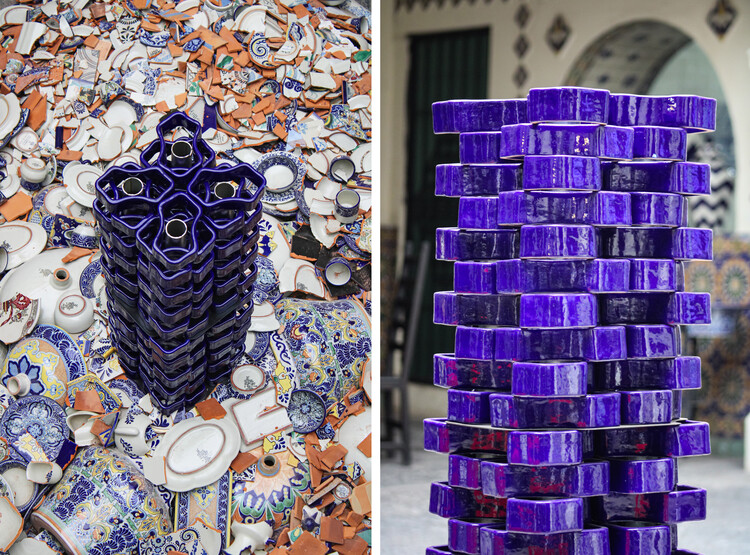
ET (AD): Given the rich diversity of craft processes in Latin America, many architects and designers focus their attention on the identity elements of their region. Do you think that, as a result of this experience, artisans, who already know craft elements, could integrate technology into their processes in the future?
DS: Of course, that is the greatest objective of this process: to open up the regulations of artisanal processes so that innovation can be allowed, reducing costs, time, precision, and, above all, greater quality but without losing traditions. We strive to support new generations of local artisans who face the risk of extinction due to various factors such as the globalization of processes and materials, industrial or mass production, climate change, demanding learning processes, trade secrets, lack of economic support and access to information, undervaluation of crafts, limited participation of artisans, inadequate training and growth opportunities, commercialization challenges, and most importantly, the failure to transfer innovation and knowledge to artisans.
We need to respond to our context and try to reconnect and generate new opportunities for our future labor generations through technology and innovation. Innovation serves as a potent source of evolution, fostering new opportunities in the conscious and sustainable preservation and manufacturing of our heritage.
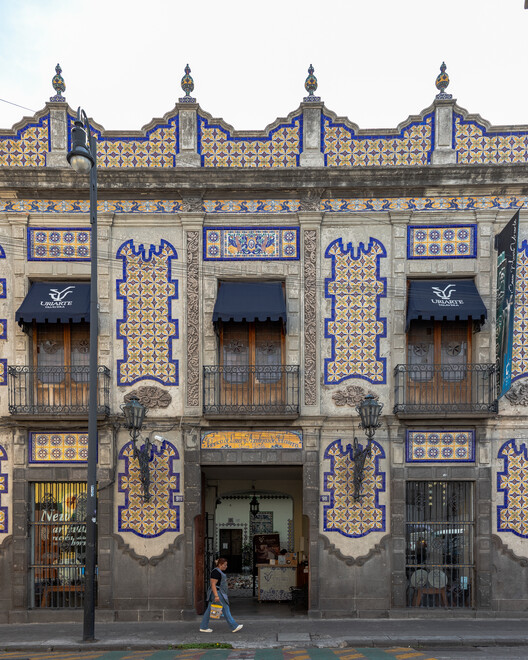
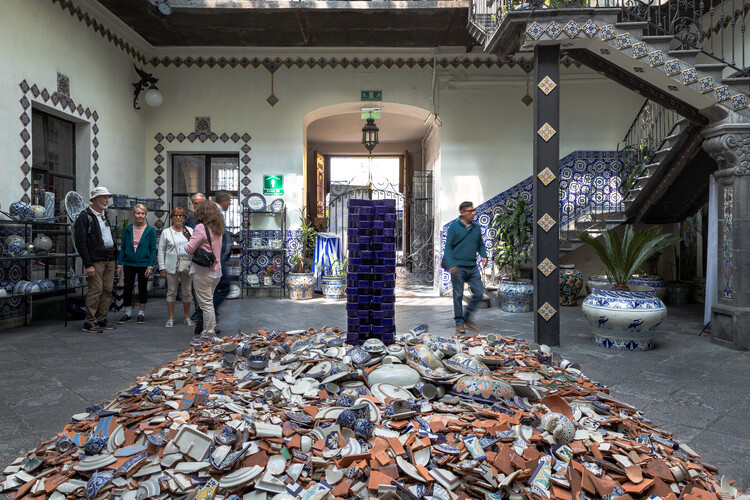
This project reflects the result of cultural miscegenation by combining the local ceramic tradition with the glazing technique, perfected by the Spanish potters who introduced it to America. Beyond being a symbol of this cultural fusion, it also serves as a reminder that today we can employ computational design, robotics, and technology to support ancestral aspects of traditional techniques. In conjunction these efforts seek to recover part of the circular sustainability inherent in these practices, aiming to reduce the environmental, social, and costs, derived from the hyper-production and mass transportation of construction materials.