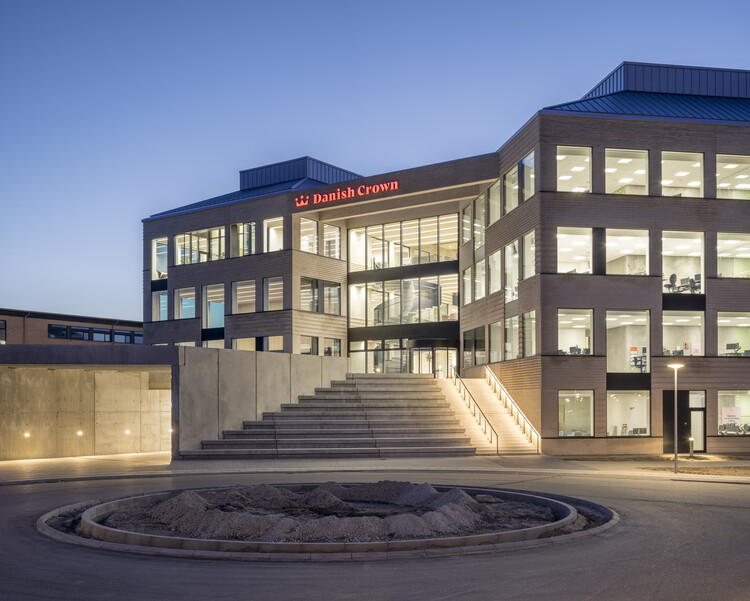
Brick beams have been widely used in construction due to their strength, durability, and aesthetic appeal. By embedding steel reinforcing bars into a series of bricks arranged in a specific pattern, these elements form horizontal load-bearing structures that distribute the weight and forces that act on a building. However, it is difficult to find brick beams with excessively large spans, in order to avoid long-term structural problems. Instead, they mostly come in the form of simple lintels, which can be easier to handle.
With a length of 16.2 meters and an impressive clear span of 15.8 meters, CEBRA architects have collaborated with the Randers Tegl group, the largest brick supplier in Scandinavia, to complete the construction of probably the longest brick beam to date. This exterior beam is accompanied by a 13-meter-span interior "sister" beam and is located above the main entrance to the Danish Crown's new headquarters in Randers, Denmark, extending freely between two of the building's wings. The longest beam is made up of almost 4,200 bricks – its height is made up of 25 rows of bricks, equivalent to 1.6 meters, and its edge consists of 4 bricks.
Construction challenges
Prefabricated in the Carlsberg Bjælker factory, the two beams are made of prestressed brick, without a concrete core or integrated steel profile. According to studies conducted by Randers Tegl, prestressed brick beams experience almost no tensile stresses, which typically lead to stretching at the beam's ends, and as a result, should not exhibit cracks. Due to their special length, they were designed to withstand both horizontal and vertical loads, especially those from wind.
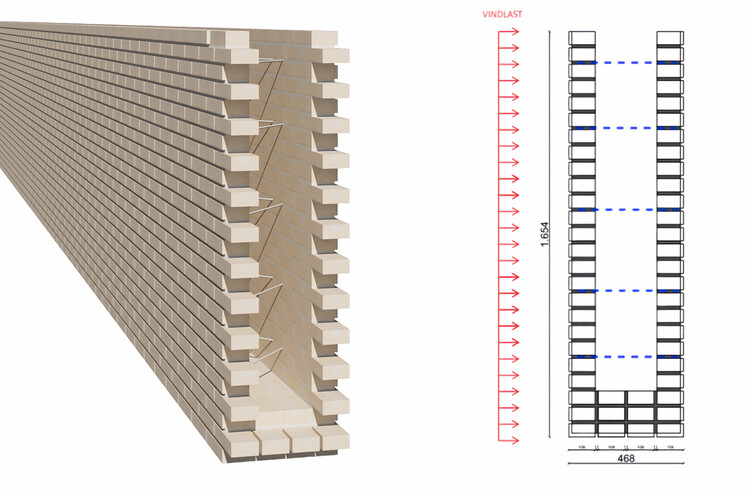
Off-site manufacturing presented a number of challenges that were successfully addressed. At the outset, the casting table had to be reinforced to bear the weight of the beams, and scaffolding was utilized to facilitate the pouring and placement of the top bricks. Its weight required demolding and manipulation with cranes, and then both sides of the beams were finished with the same mortar that is used for the rest of the masonry. After completing the curing process, they were ready to be transported by truck to the site.
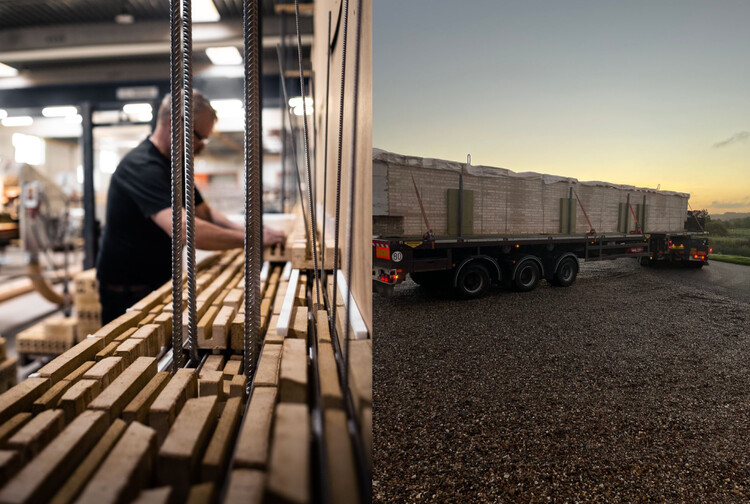
Upon arrival in Randers, the general contractor, Raundahl & Moesby, took charge of positioning the brick beams using a large crane and mounting them on special supports that had been previously affixed to the concrete elements.
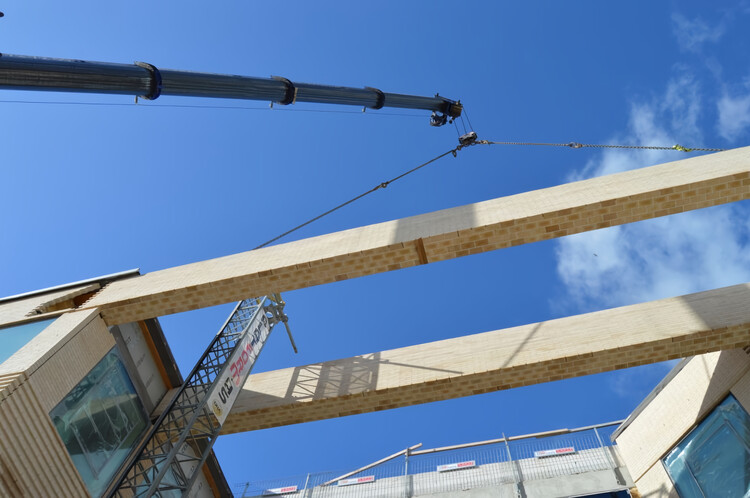
Why is this constructive feat important?
In Denmark, bricks are integral to most buildings. In the new Danish Crown headquarters, they were selected not only for their efficiency and exceptional lifespan but also for their symbolic and visual connection to the inhabitants of the area, enhancing the sense of belonging. The construction of these innovative beams demonstrates the potential of this material for the future.
Most buildings in Denmark are made of bricks. It is something that all Danes associate with quality. I think because everyone has had a brick in their hands and knows its weight and durability. – Mikkel Frost, architect and founding partner, CEBRA.
Situated on a sprawling 12-hectare plot, the building draws inspiration from the architecture of traditional Danish farms and rural communities, featuring solid masonry and gabled roofs. The three wings intertwine, creating a welcoming main entrance that seamlessly blends with the surrounding landscape. This design evokes the communal essence of Danish villages, with a central square serving as the heart of the building. It encompasses common spaces such as a dining room, a kitchen, and an employee store, connecting work areas on all four floors through interconnected bridges and stairs.
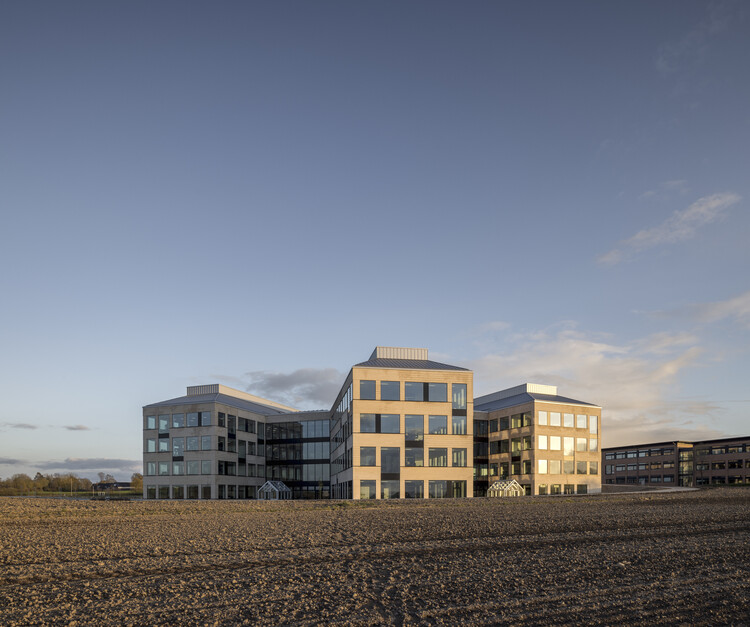
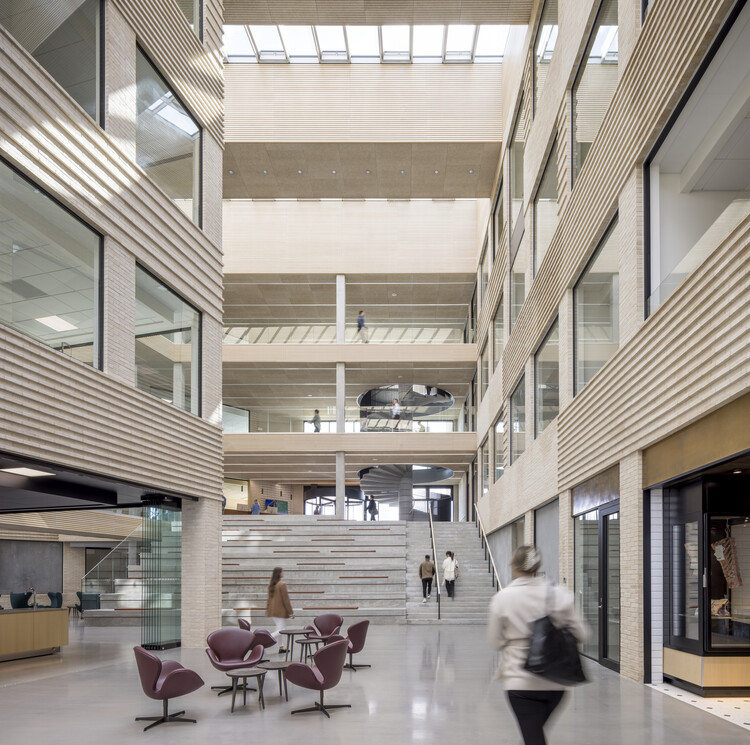
This pioneering project in Denmark adheres to the central standards of the DGNB, promoting a healthy and comfortable work environment. It places special emphasis on air quality, indoor thermal climate, acoustics, and the visual and architectural environment. The choice of materials was guided by strict sustainability criteria in alignment with the Danish Crown's sustainability agenda.
Efficient Brick Production
A total of 250,000 bricks were supplied for the project, including the GREENER variant from the special batch RT103. By choosing these bricks for the façade, produced exclusively with electricity generated by wind energy and biogas, an estimated 50 tons of CO2 emissions are saved, according to calculations by Søren Jensen Rådgivende Ingeniørfirma A/S.
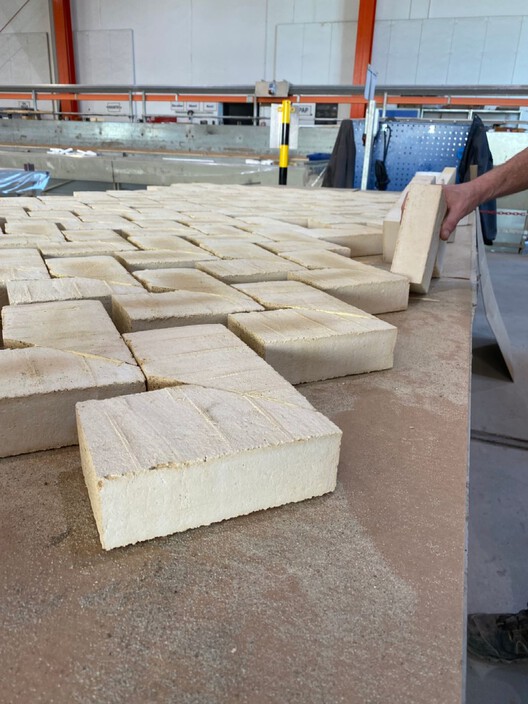
Specifically, compared to generic bricks, the CO2 savings are substantial, amounting to an impressive total of 110,000 kilograms. With GREENER, the total emissions are 58,500 kilograms of CO2-eq, while the use of generic bricks would have resulted in a much higher emission of 168,750 kilograms of CO2-eq. This underscores the positive and significant impact of employing these efficiently produced bricks in construction projects, demonstrating a notable reduction in the carbon footprint.
As a result of all these efforts, the construction has received DGNB Gold and DGNB Heart certifications. Learn more about GREENER features here.