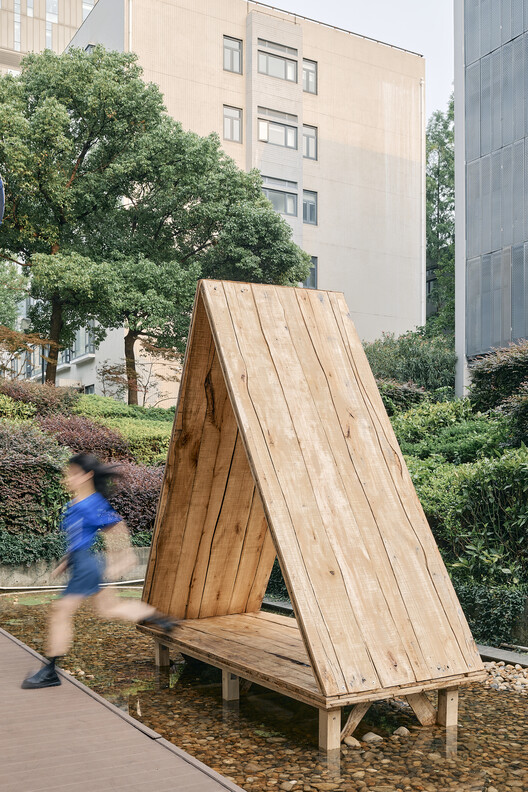
Mass timber has emerged as a sustainable alternative to replace concrete components in construction, as the latter alone contributes to 8% of global CO2 emissions. With various examples across different scales and applications, the material has shown promise in revolutionizing the industry by enhancing efficiency, strength, and comfort. Even when dealing with highly standardized and efficient processes in the manufacturing of structural elements, there is always room for improvement and waste reduction. This is mainly because the traditional industrial process of cutting logs into parts can generate substantial waste.
In this context, A.I. Timber emerges as an innovative construction material designed to minimize waste by preserving the natural contours of trees. Instead of employing conventional methods that involve cutting individual logs into standardized boards, A.I. Timber ingeniously utilizes Artificial Intelligence to fit these logs together like pieces of a perfectly assembled puzzle. To gain further insight into this initiative and the future of this material, we spoke with Carlo Ratti and Mykola Murashko, who coordinated the project.
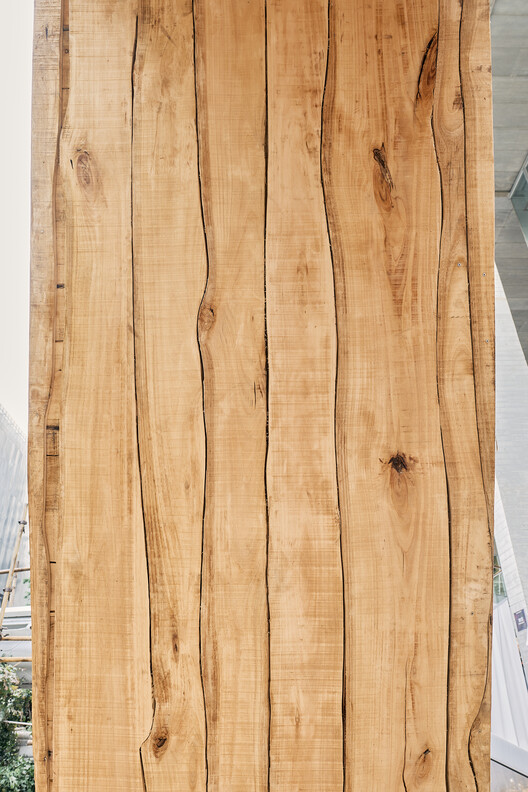
Being a natural material, wood always reflects the conditions of the tree's growth, including factors like climate, prevailing winds, or even its position in the forest. When examining a cross-section of a log, one can identify different parts, such as sapwood and heartwood, each with its unique strength and distinct characteristics. The way the log is cut and divided into boards or structural pieces plays a crucial role in defining the functionality and features of the resulting sections. The innovation behind A.I. Timber lies in using the pieces' natural contour to reduce waste without disrupting the wood fibers. AI algorithms and digital machining tools were employed to scan a set of raw logs, convert them into boards, and determine the optimal arrangement for their assembly. This results in wooden panels with interlocking boards that align perfectly, minimizing the removal of natural material from the tree. The method was developed by Maestro, a recently established construction technology startup, born from the creative minds of CRA-Carlo Ratti Associati and developed in collaboration with students and researchers from MIT and Tongji University.
A.I. timber is inspired by nature itself. With the right technology, we can work with natural forms instead of against them. – Carlo Ratti
The architect continues to explain that “Modern industrial production is about standardization, but every tree grows in different directions. When you saw down unique trees into uniform panels, you waste all of the wood that doesn't conform. For a typical CLT panel, up to 60% of the wood you cut down goes to mulch or the incinerator. Our method is different. We use LiDAR technology to scan a set of raw logs, and deploy AI to fit them together like pieces of a puzzle –making the minimum number of cuts and using all available wood.”
Regarding the technology itself, Mykola Murashko, CEO and co-founder of Maestro Technologies says, “Without A.I., making this material wouldn't be possible. The technology allows us to compute the optimal means of sawmilling a set of logs in order to reduce wood waste. Specifically, our algorithm minimizes the loss function associated with the volume of timber that needs to be cut in order to tesselate a set of lamellas into a CLT layer. Maestro built an integrated pipeline to deploy this technology to production –connecting imaging technology with AI in order to generate custom machine instructions for the sawmill and CNC. Our AI-powered pipeline allows us to deliver bespoke craftsmanship at industrial speeds.”
When you respect the original contour of the tree, you don't only save a tremendous amount of wood –you get a beautiful, unique shape as a result. – Mykola Murashko
Mykola adds that “Beyond aesthetics, the intermeshed lamellas within the CLT panel improve its structural performance by acting against shear forces within the panel. In other words, the material holds itself together. This could, in the future, allow us to use less glue in CLT production.
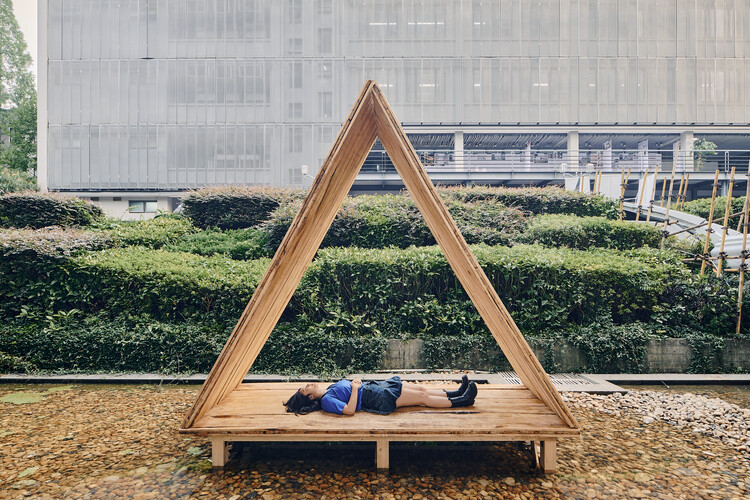
The main aim of the project is to harness technology to bridge the gap between design and manufacturing, enabling a network of suppliers to produce customized components on an unprecedented scale and hence resulting in transportable and tailor-made buildings. This methodology holds the promise of making construction more efficient, faster, and more environmentally friendly than ever before. Carlo Ratti adds, "Maestro, our construction startup, is based on a wholesale plan to revolutionize how we build: A.I. timber is just the first piece. We create custom designs in a digital environment, then send them to a network of European factories that manufacture all of the customized parts. Similar to conducting a symphony, Maestro guides the factories in creating the building in sections, which are then shipped to the destination in the Maestro Flatpack."
Prefabrication eliminates all the time and cost of a traditional construction site – final assembly is as easy as snapping the pieces together. Lightweight, customizable materials like A.I. timber make this method possible. It will make construction cheaper, greener, and of higher-quality than anything we've done before.” – Carlo Ratti
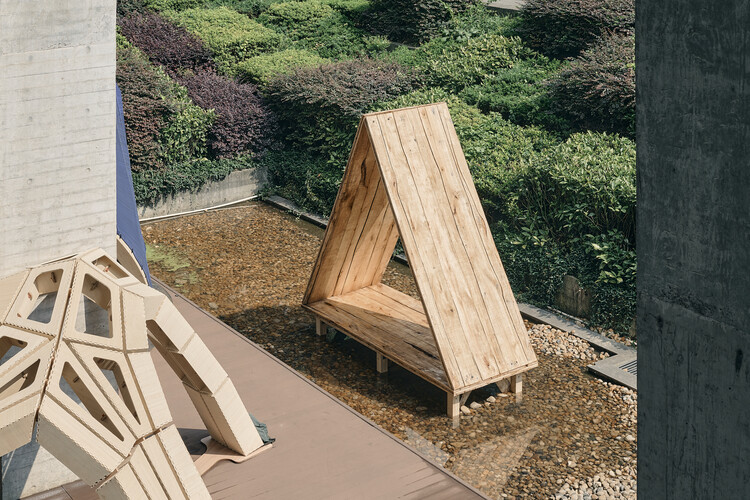
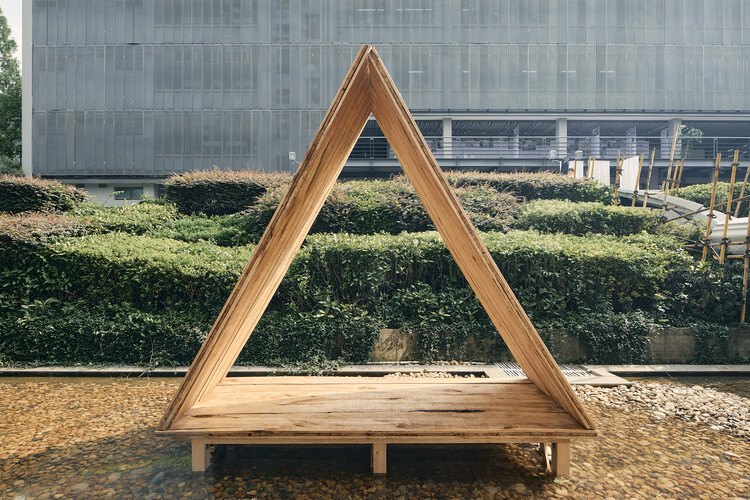
The debut prototype of A.I. Timber was manufactured in Shanghai earlier this summer during the DigitalFUTURES conference, organized by Professor Philip Yuan of Tongji University. Over the course of a one-week workshop, Murashko and Nikita Klimenko from MIT guided an international team of researchers in using AI and wood to construct a proof-of-concept structure –a small interactive triangular pavilion employing the system.
Maestro Team: Carlo Ratti, Mykola Murashko, Nikita Klimenko, Ginevra Nazzarri
Tongji University and DigitalFUTURES Team: Adelaide Tremori, Dan Luo, Filippo Innocenti, Hongsheng Jiang, Hanlin Dong, Jin Gao, Jinghan Wu, Lijun Xiao, Maria Francesca Toti, Guglielmo Sobrini, Qiming Sun, Ruipeng Wang, Wenlei Yang, Wenzhuo Zhao, Xu Cheng, Yantong Xie, Yuqing Huang, Ziying Qi, Toto Tan, Zhihao Zhou, Zhiyi Lin
This article is part of the ArchDaily Topics: The Future of Wood in Architecture presented by Tantimber ThermoWood.
Tantimber ThermoWood brings the timeless warmth of wood to modern design. Natural, renewable, and non-toxic, they transform sustainably sourced wood species into dimensionally stable and durable wood products for use in residential and commercial building and design projects. Find out more about how the enduring beauty of ThermoWood brings warmth to the built environment.
Every month we explore a topic in-depth through articles, interviews, news, and architecture projects. We invite you to learn more about our ArchDaily Topics. And, as always, at ArchDaily we welcome the contributions of our readers; if you want to submit an article or project, contact us.