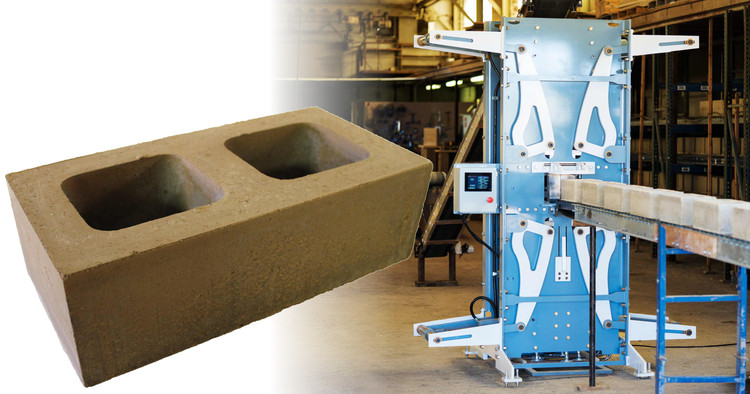
Excavation is usually a bane for real estate developers. To make way for new buildings, truckloads of excavated waste are removed from site in a noisy, time-consuming and gas-guzzling process. Exploring a more sustainable solution, the California-based company Watershed Materials have developed an onsite pop-up plant which repurposes excavated material right at the job site to create concrete masonry units (CMUs) used in the development. By eliminating truck traffic, reusing waste and reducing imported materials, the result is a win for the environment.
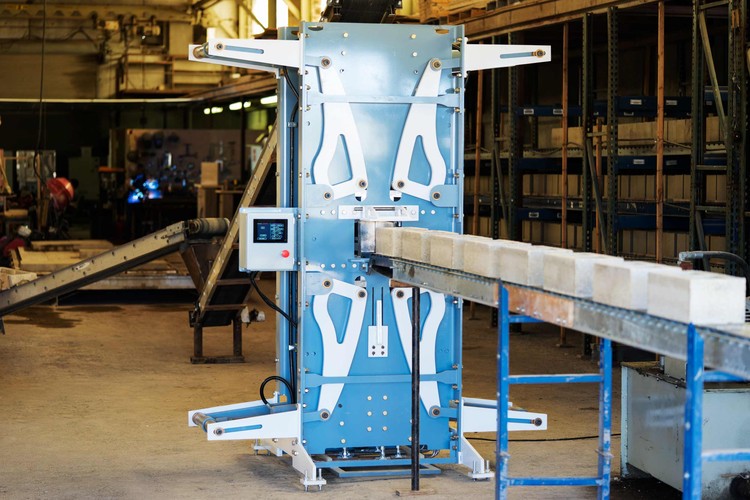
The pop-up plant itself works by applying ultra-high compression to loose excavation spoils, transforming it into a sustainable CMU. The pressure turns the mineral grains into a sort of sedimentary rock, mimicking the natural geological process of lithification. This unique manufacturing technology is the brainchild of Watershed Materials, who previously developed the compression technique in order to reduce the amount of cement used in concrete blocks by 50%.
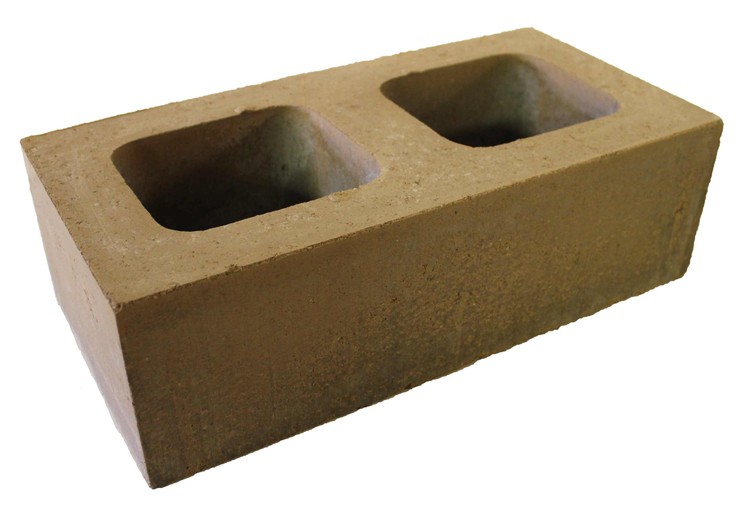
As the founder of the sustainable building materials startup David Easton points out: “There’s absolutely nothing new about building masonry structures from local materials. Some of the oldest and best-known architecture in the world has been constructed from stone and clay sourced directly on site." But according to Easton, "what is new and absolutely groundbreaking is that with upgraded technology and improved material science, a construction waste product the developer had to pay to dispose of can now become an asset and provides environmental benefits as well.”
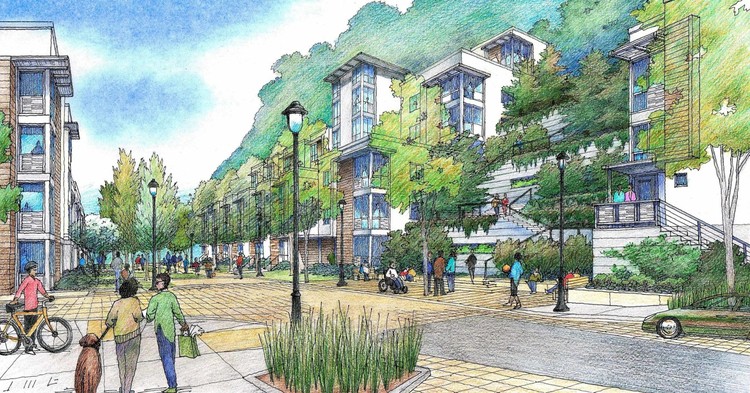
The pop-up plant was born when Naomi Porat, development manager of Alpha Group and part of the team working on the Kirkham Project, approached the startup to bring their technology straight to the construction site. The Kirkham Project is an urban infill redevelopment in San Francisco spanning across 445 new housing units, community plazas and gardens. While addressing the city’s need for additional housing, neighbors expressed concern over construction traffic, making it the perfect place to explore this onsite approach.
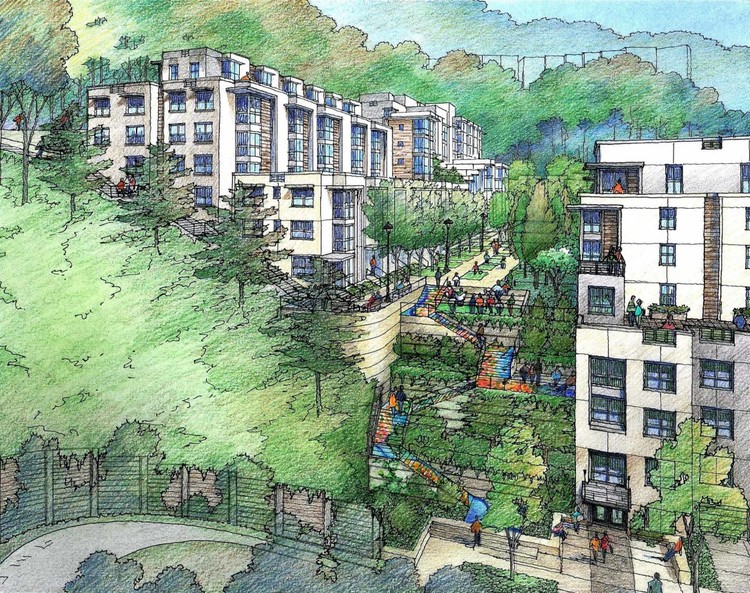
In their feasibility study, the Kirkham Project team identified compelling advantages of the onsite process and product. Reduced truck traffic meant reduced cost, diesel emissions and impact on neighbors. Also beneficial to neighbors is the pop-up plant itself, which is no louder than typical construction equipment and only onsite for a limited period of time.
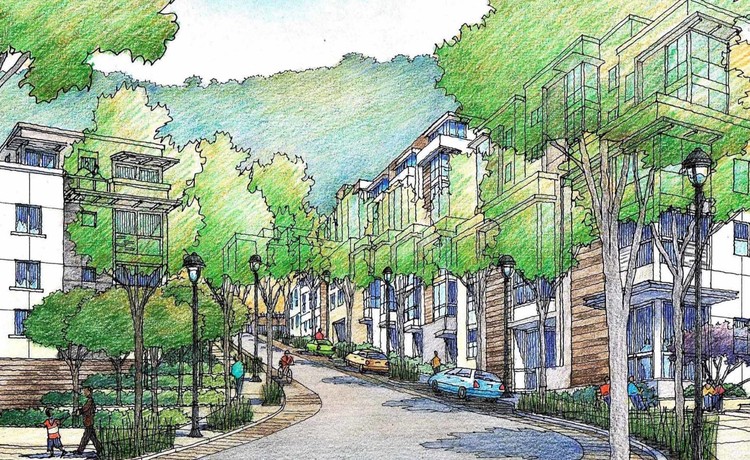