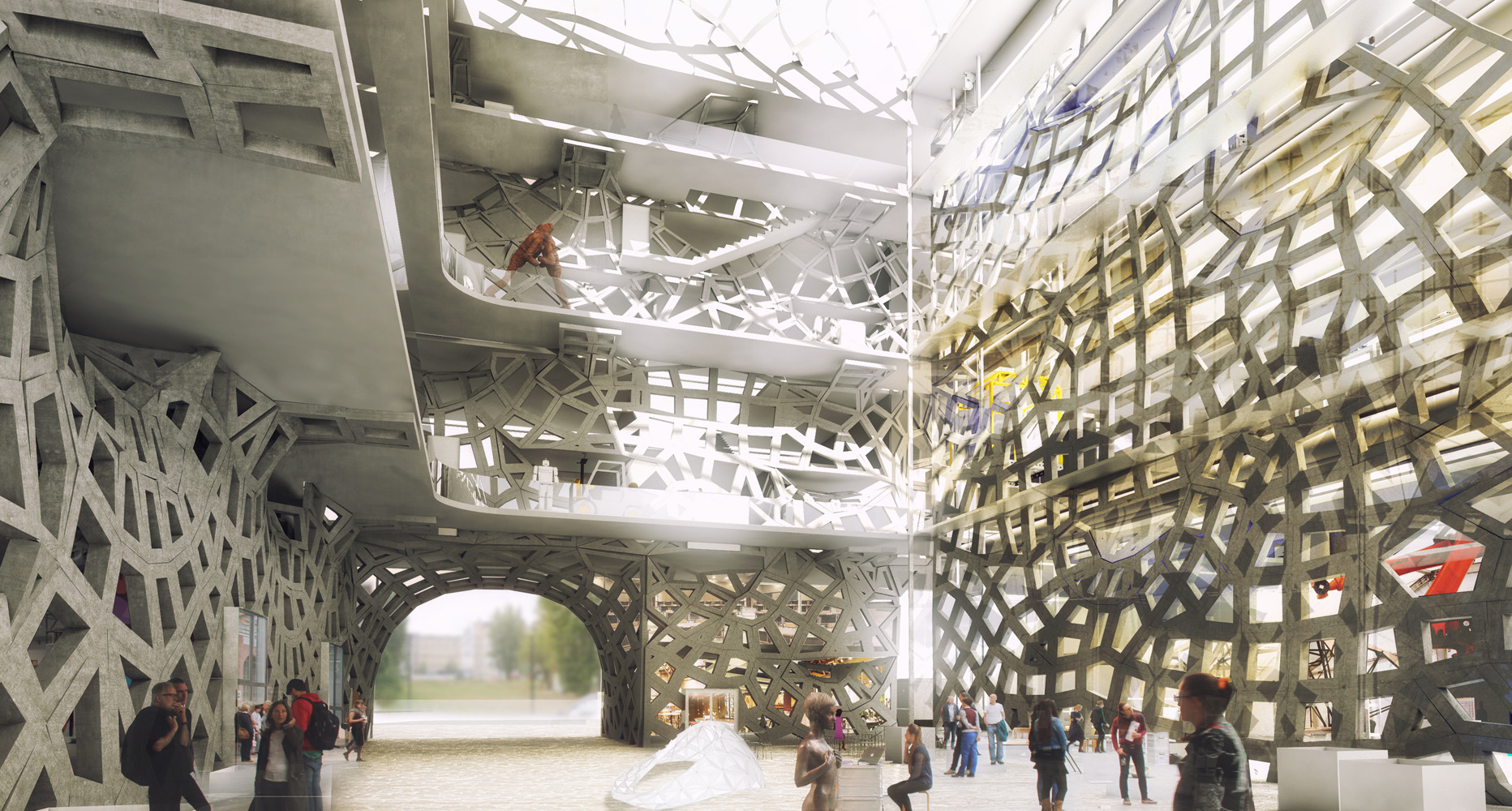
When one hears the term masonry architecture, digital fabrication and automated construction processes are probably not the first ideas to come to mind. By its very nature, the architecture produced with stone masonry is often heavy, massive, and incorporates less natural light than alternative methods. However, with their research proposal for "Smart Masonry," ZAarchitects are proposing to change masonry buildings as we know them and open opportunities for digital fabrication techniques in stone and other previously antiquated materials. Read on after the break to get a glimpse of what these new masonry buildings could look like and learn more about the process behind their construction.
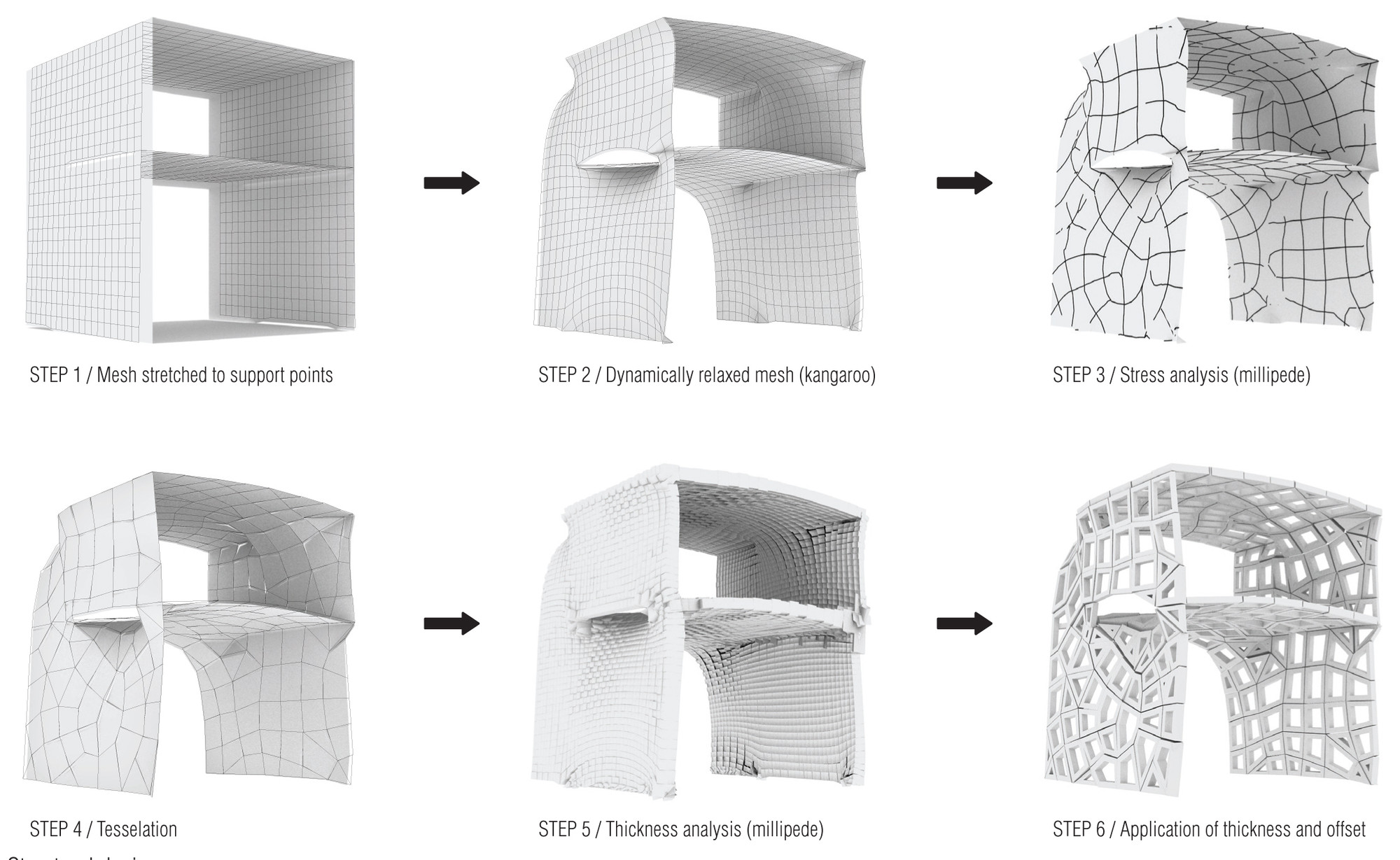
Designers Dmytro Zhuikov and Arina Agieieva derived the foundations and construction methods of their new structural system from the techniques used in traditional masonry buildings. As a construction method that has its roots in ancient history, the vast array of masonry building precedents offer contemporary architects a wealth of information to draw upon. One of the most significant challenges in designing masonry structures throughout history has been ensuring structural loading requirements and minimizing building mass wherever possible to encourage the flow of light and air. Because modern technologies allow us to optimize and minimize dead-weight, the structural skeleton of Smart Masonry is incredibly light. Additionally, complex geometries can be achieved through the use of robotic construction techniques, ensuring that each element can be replicated with the same precision each time.
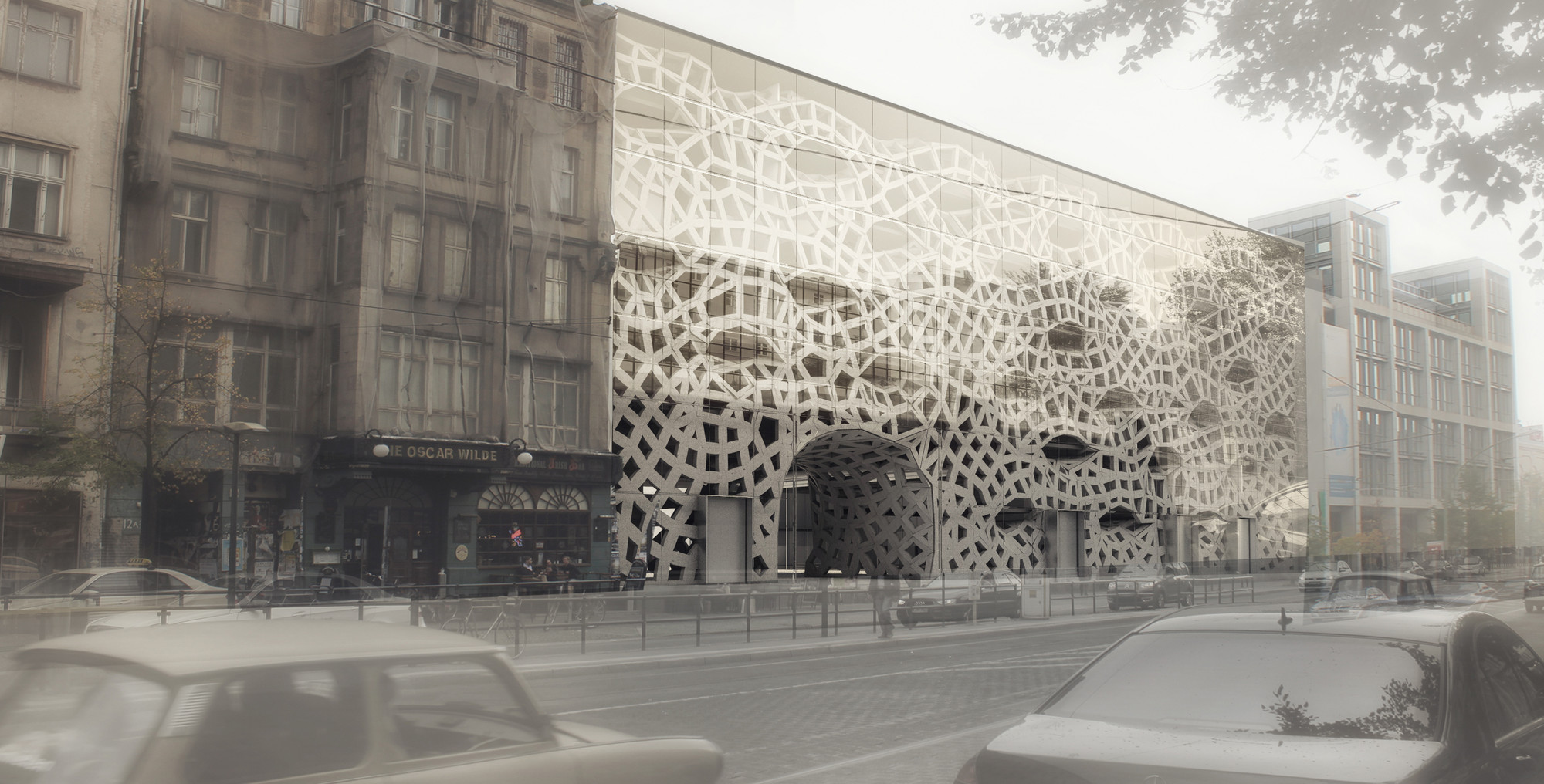
This proposed method is linked to the program and location of the building-makers center in Berlin. The machinery which will be used to construct the building will later be preserved at its core, serving as a reminder of the building’s origin and addressing its present functions.
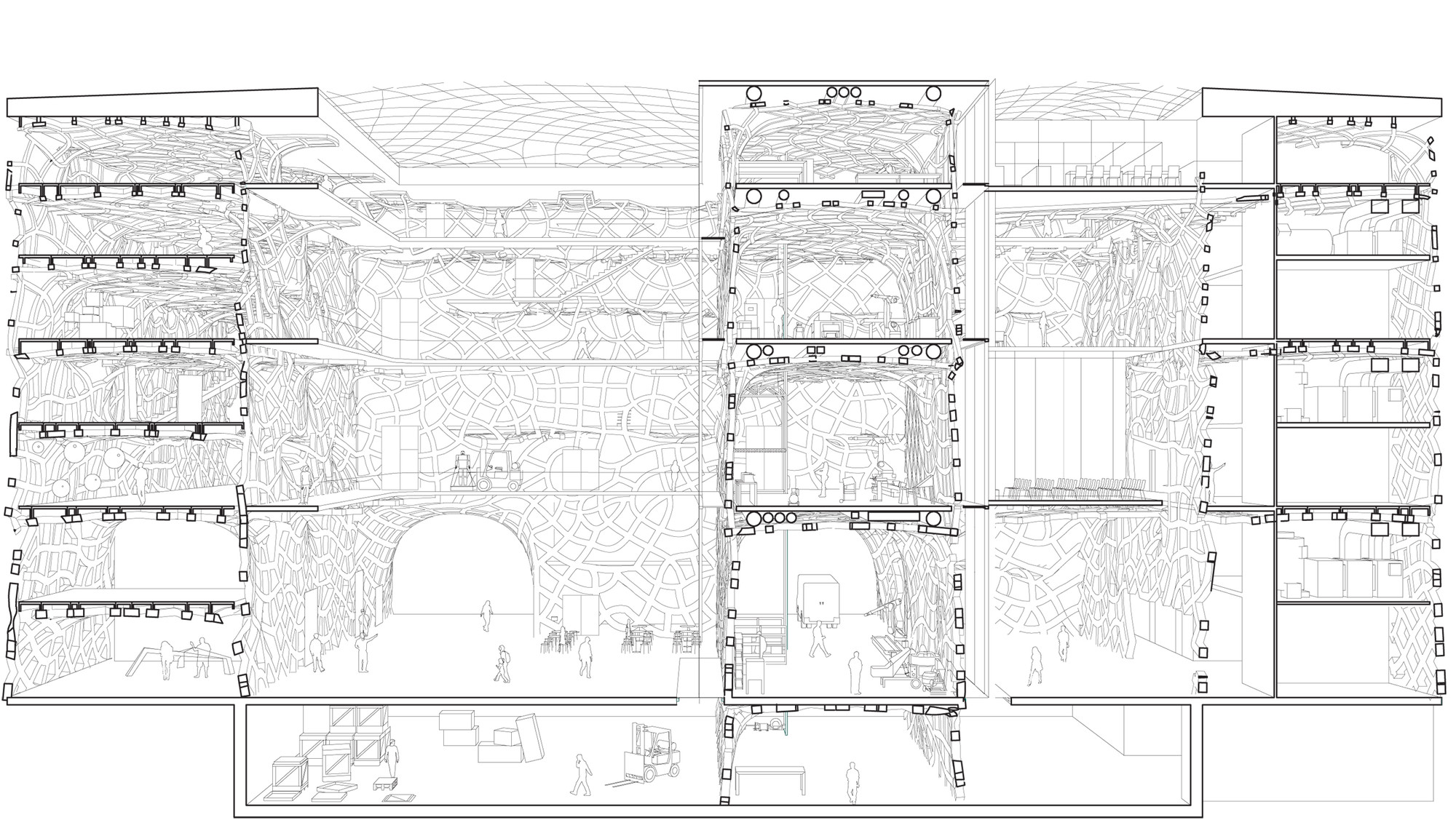
Conceptualized as a seamless mesh, overlapping and wrapping elements replace walls, columns, and beams. Saving on material and costs, the entire area of the building is designed as a “minimal surface” whose stress-pattern is optimized and materialized as a load-bearing pattern.
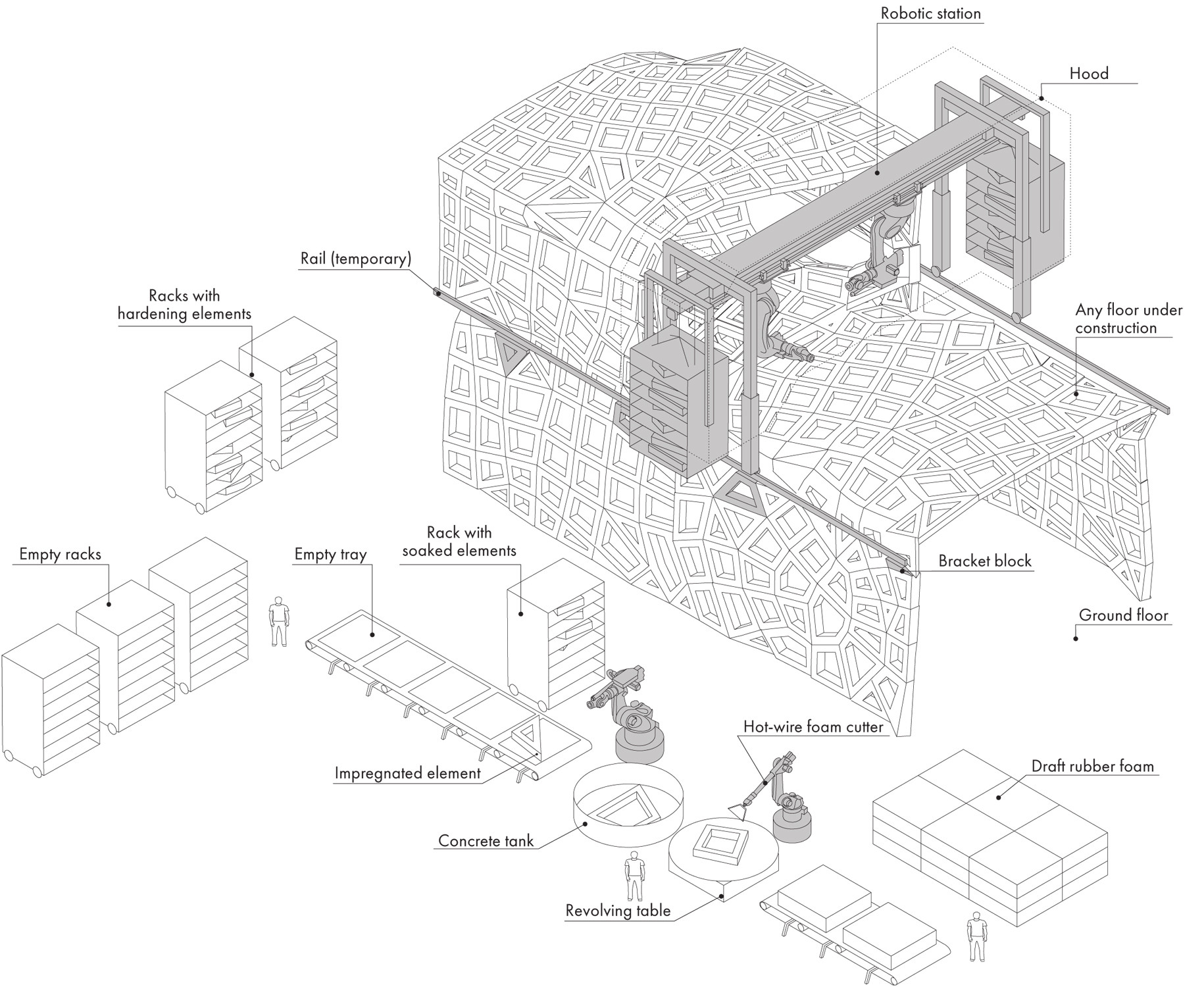
Mixing advantages of 3D printing and large prefabricated elements, the concept seeks to maximize construction efficiency, further reducing costs and enhancing precision. A robotic arm construction station enables the production of complex geometries on each floor. Compared to traditional methods, this robotic arm method is more compact and reduces labor costs throughout the entirety of the construction process. Additionally, it is much faster than 3D printing and can produce complex digital forms in a fraction of the time.
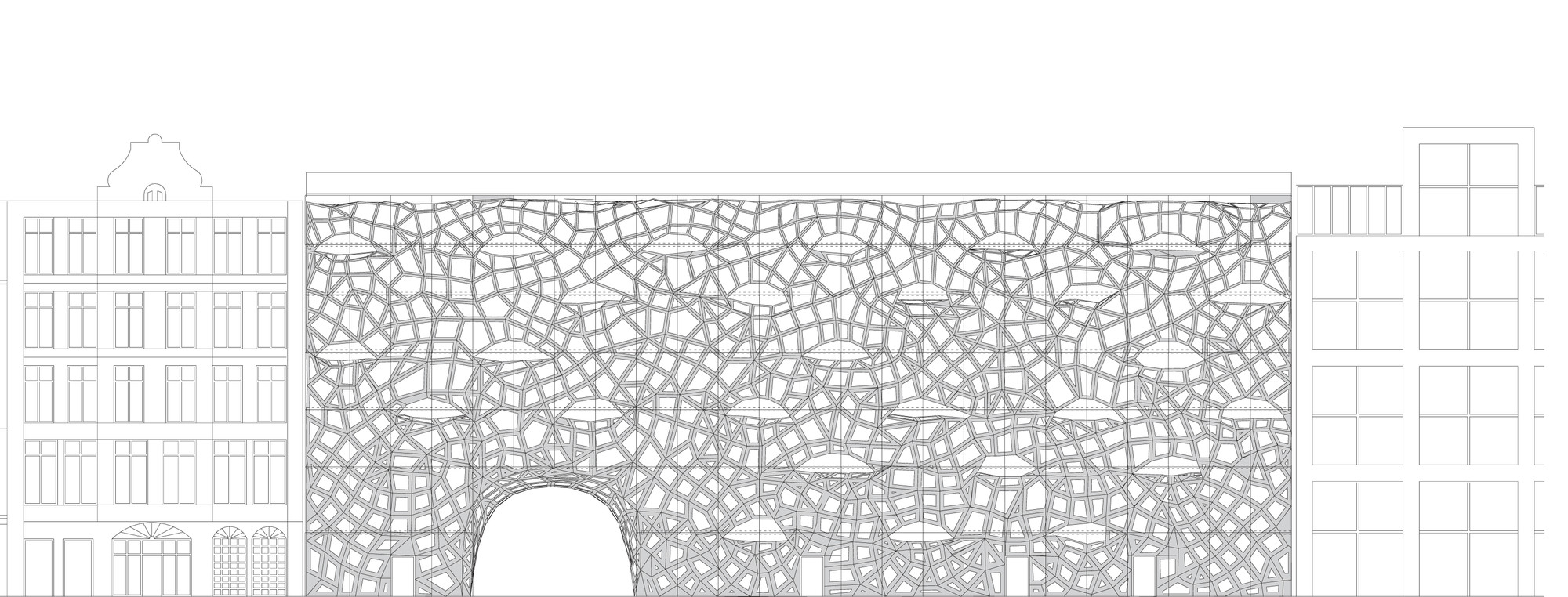
The overall form of the structure is derived by beginning with basic geometries and manipulating them according to structural efficiency, with a technique known as “positive casting” used to conserve resources and to produce the design's unique elements and geometries.